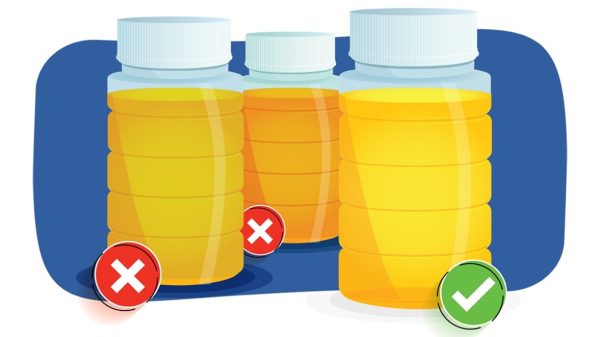
La consolidación de lubricantes es la práctica de seleccionar lubricantes, quedándose solo con lo necesario para un desempeño óptimo de la maquinaria en la instalación. A menudo visitamos diferentes instalaciones para efectuar un diagnóstico o ingeniería del diseño del proceso de lubricación (LPD, por sus siglas en inglés), y cuando lo hacemos, una de las principales áreas de enfoque es el cuarto de lubricación. En general, en cualquier almacén de lubricantes o cuarto de lubricación veremos algunos de los lubricantes actuales y una docena de otros lubricantes olvidados en un rincón que no se han visto ni se ha escuchado hablar de ellos en años. Sin embargo, esos lubricantes antiguos aún forman parte de la lista de lubricantes que recibimos antes de la recopilación de datos para nuestro servicio LPD fase 2 (fase de ingeniería). Esto puede ser confuso para cualquier técnico nuevo y estamos allí para ayudar a resolver esa confusión. Antes de hacerlo, hay algunos pasos que debemos seguir para determinar cuáles lubricantes se quedan y cuáles se van.
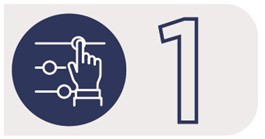
Se inspecciona cada máquina y componente lubricado en toda la instalación e identifique los lubricantes que están en uso. También recopilamos datos pertinentes de cada máquina; para motores eléctricos, podemos recopilar HP, velocidad, tamaño de armazón y otros datos operativos y ambientales.
Esto puede ser muy difícil en algunas plantas, dependiendo de su antigüedad y si han intentado una consolidación de lubricantes en el pasado.
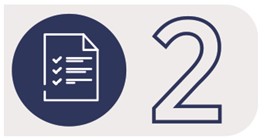
Luego, recopilamos el nombre, la marca y el tipo de cada lubricante, tanto los que se encuentran en el almacén como los que están distribuidos por toda la planta. Después, combinamos este listado con la lista de lubricantes creada en el PASO 1 para formar una lista completa de los lubricantes en la instalación.
Una vez que hayamos descubierto todos los lubricantes actuales en cada máquina y componente, habremos recopilado los datos necesarios para hacer nuestras propias recomendaciones sobre qué lubricantes se deben utilizar en cada máquina.
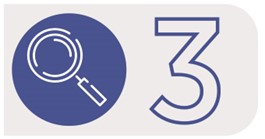
Luego, llevamos todos esos datos a nuestra base de operaciones y estudiamos cada máquina y componente para definir si es necesario equiparla con algún dispositivo para la aplicación de lubricante, control de contaminación, inspecciones, muestreo, lubricante recomendado, etc.
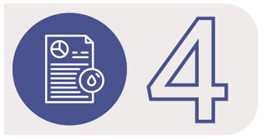
Luego, consideramos toda la información recopilada y llegamos a una recomendación para todos los componentes lubricados con aceite y grasa.
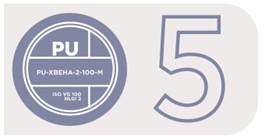
Alineamos los lubricantes recomendados con los lubricantes actualmente en uso y todos los lubricantes en la instalación. Recomendamos lubricantes basados en un enfoque genérico, en el que se incluyen las propiedades físicas, químicas y de desempeño del lubricante en cuestión.
Esto nos permite recomendar la viscosidad, el paquete de aditivos, el tipo de aceite base y la aplicación, sin que sean específicos de la marca: Noria es una empresa neutral a vendedores. Esto lo documentamos en una “especificación técnica genérica” para futuras referencias. En este paso, debemos tener en cuenta la compatibilidad del lubricante actual y el lubricante recomendado. Por ejemplo, no desea purgar un rodamiento con una grasa que tiene espesante de complejo de aluminio si hay actualmente una con espesante de calcio. Incluimos en la especificación técnica el código y la etiqueta de identificación de cada lubricante de acuerdo con el Sistema de Identificación de Lubricantes (LIS, por sus siglas en inglés).
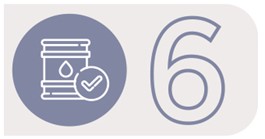
Una vez que se formulan las recomendaciones, se envían a la instalación para su aprobación por parte de las partes interesadas involucradas. Se proporcionan explicaciones y se realiza una revisión para este proceso de aprobación. Una vez que se aprueban los lubricantes, también nos queda una lista de lubricantes que ya no se utilizan pero que aún permanecen en la planta.
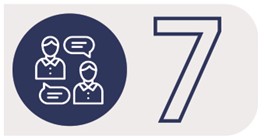
Aconsejamos a la empresa que se deshaga adecuadamente de todos los lubricantes que no estén en uso. Esto tiene dos beneficios: abre espacio en el almacén de lubricantes para los lubricantes actuales y recomendados y garantiza que los lubricantes incorrectos que se encuentran al azar en toda la planta no se usen accidentalmente.
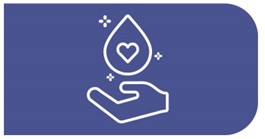
El paso final: Optimización
Ahora que hemos eliminado los lubricantes obsoletos y sin uso en la instalación, es hora de optimizar los lubricantes que se mantienen. A menudo les decimos a los usuarios finales que «consolidación» no es necesariamente la palabra adecuada.
En cambio, la «optimización» es mucho más precisa. Esto significa que “a veces” no basta tener menos lubricantes en el sitio, sino tener los lubricantes correctos para cada aplicación. Pongo «a veces» entre comillas porque en ocasiones el proceso de consolidación del lubricante terminará con la misma cantidad de lubricantes o casi la misma que antes. Es posible que se hayan eliminado algunos y que se hayan agregado otros, pero el resultado es una selección optimizada de lubricantes, lo que garantiza que se seleccione el lubricante correcto para cada máquina.
Optimizamos una lista de lubricantes asignando grasas y aceites específicos en función de los datos de la máquina y los parámetros operativos y ambientales. Esto podría significar que ahora la instalación solo utiliza cuatro grasas en lugar de ocho; una para rodamientos de alta velocidad, una para los de baja velocidad, una para acoplamientos y otra para motores eléctricos, por ejemplo. Sin embargo, ese no es siempre el caso. Algunos lubricantes se ajustan a los parámetros de viscosidad y aditivos para múltiples tipos de máquinas, pero algunos lubricantes solo cumplirán con los parámetros de una máquina específica. Consolidamos y optimizamos lubricantes para llegar a extender la vida útil de las máquinas y optimizar su desempeño. Ese es el objetivo final de la confiabilidad de la maquinaria.
Noria Corporation. Traducido por Roberto Trujillo Corona, Noria Latín América.