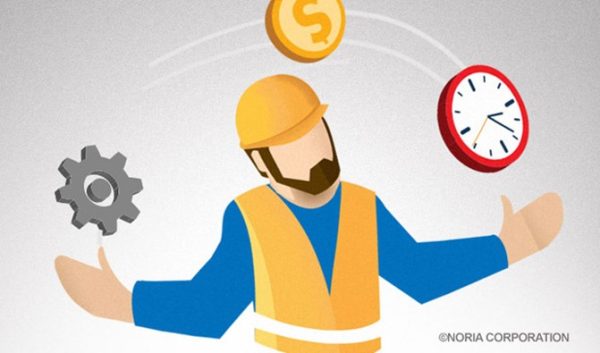
¿Cuáles son los tipos de mantenimiento más utilizados?
Existen varios nombres asignados a las estrategias de mantenimiento, en función de sus objetivos y técnicas utilizadas, como el Mantenimiento Productivo Total (TPM, por sus siglas en inglés), Mantenimiento Basado en Condición (CBM, por sus siglas en inglés) o Mantenimiento Centrado en Confiabilidad (RCM, por sus siglas en inglés), etc., sin embargo en todos ellos podemos hablar de clasificaciones de las tareas de mantenimiento como sigue:
Mantenimiento reactivo
El mantenimiento a la falla, también conocido como mantenimiento reactivo, es un tipo de mantenimiento correctivo que se lleva a cabo ante una falla inesperada de la máquina, la cual debe ser reparada o sustituida para reanudar el funcionamiento de la empresa.
El mantenimiento reactivo generalmente incurre en costos iniciales menores y requiere menos necesidades de personal en comparación con las formas proactivas de mantenimiento. Las actividades se limitan a solucionar problemas identificados y no se requiere de actividades preventivas innecesarias. El mantenimiento reactivo tiene sentido para equipos no críticos.
Sin embargo, a medida que aumenta el riesgo con maquinaria más crítica o compleja, que puede requerir más tiempo de reparación y tener un mayor impacto en la producción y el desempeño, el mantenimiento reactivo puede tener riesgos que superan los beneficios.
Las reparaciones no planificadas pueden causar problemas graves de producción y seguridad, además de altos costos.
Mantenimiento preventivo
Son las actividades programadas de reparación o cambio efectuadas a los componentes de la maquinaria basados en tiempo. Estudios publicados en Forbes Magazine, indican que un 33% de las actividades de mantenimiento preventivo son efectuadas sin que fueran requeridas. Es una de las más empleadas, aunque tiene el inconveniente de ser muy costosa ya que requiere de una programación exacta, controles, mucha mano de obra, partes de repuesto y no garantiza la confiabilidad de su maquinaria.
Mantenimiento predictivo
Es el monitoreo periódico de ciertos parámetros de operación de la maquinaria y equipos considerados críticos, seguimiento de sus tendencias, establecimiento de límites de advertencia y detección de señales del inicio de alguna falla para tomar acciones de corrección o reemplazo. Esta clase de mantenimiento ha tomado un gran impulso receintemente porque proporciona grandes beneficios de confiabilidad y disponibilidad de la maquinaria. Se apoya en tecnologías relevantes como el análsis de vibración, ultrasonido, termografía, emisión acústica, video, análisis de corriente, análisis de lubricante, etc. Debe ser aplicado solo a equipo crítico y requiere personal entrenado, equipos, tecnología y un sistema de administración de la información.
Mantenimiento proactivo
Es una filosofía moderna en la que el objetivo principal es el de identificar las causas de falla de la maquinaria para controlarlas y tratar de eliminarlas de la mejor manera, para evitar que estas se conviertan en desgaste. Utiliza herramientas como el Análisis de Modo de Falla, Efecto y Criticidad (FMECA, por sus siglas en inglés), el Análisis de Causa Raíz de Falla (RCFA, por sus siglas en inglés) y principalmente el análisis de aceite para la localización de las causas de falla, ya que el lubricante durante su operación recoge esas señales, además de la condición de la máquina. El análisis de lubricante es una herramienta ampliamente utilizada desde los años 60 como una herramienta predictiva de las condiciones de la maquinaria (especialmente en ferrocarriles, maquinaria pesada y aviación) y frecuentemente utilizada para determinar la necesidad del cambio de aceite, sin embargo es una de las tecnologías que más importancia tiene actualmente, ya que con la nueva visión del mantenimiento proactivo, además de esos beneficios, se evita el desgaste de la maquinaria al controlar las causas de falla.
Estudios publicados establecen que la implementación de un programa de mantenimiento que incluya las técnicas proactivas puede ampliar la vida de la maquinaria hasta en 10 veces, comparado con sus condiciones actuales.
La combinación de las filosofías de mantenimiento predictivo y proactivo, de acuerdo con la importancia de la maquinaria, resulta en una estrategia conocida como Mantenimiento Basado en Condición.