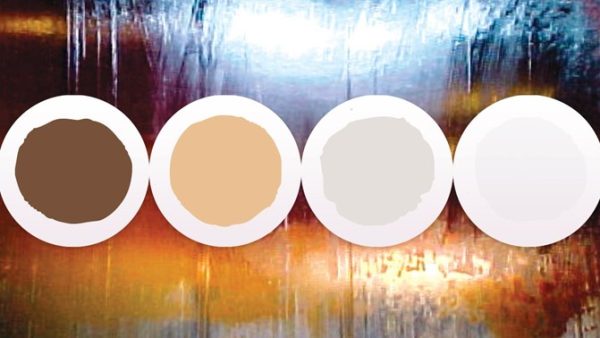
Resumen
El barniz es un residuo orgánico producido por la degradación química irreversible de los lubricantes y provoca numerosos problemas en la maquinaria, entre ellos:
- Taponamiento del filtro
- Flujo de aceite restringido
- Mala transferencia de calor
- Válvulas pegadas
- Condiciones de falla inicial
- Costosas paradas inesperadas
El barniz se ha definido tradicionalmente como un depósito insoluble, pero también existe en estado soluble, y la conversión entre soluble e insoluble es un proceso de equilibrio físico que depende de la temperatura. El barniz soluble se vuelve insoluble al reducir la temperatura del aceite lubricante; por lo tanto, es fundamental eliminar el barniz soluble del aceite lubricante para resolver permanentemente los problemas relacionados con el barniz.
Debido a la prevalencia y la naturaleza costosa de las fallas relacionadas con el barniz, se han desarrollado estrategias para mitigar los efectos del barnizado. El aspecto más importante es medir el barniz de forma rutinaria, desarrollar una tendencia y utilizar tecnologías adecuadas para eliminarlo del sistema de aceite lubricante.
Este artículo describe una evaluación técnica de la efectividad de las tecnologías de enlace de carga iónica para eliminar el barniz soluble y los efectos potencialmente negativos de la tecnología sobre los aditivos del aceite lubricante.
La evaluación realizó pruebas de campo en sitio en una turbina de gas y fue seguida por una evaluación de laboratorio. Para medir la efectividad de la tecnología, se analizaron muestras de aceite lubricante para detectar:
- MPC
- RULER
- AN
- Conteo de partículas
- Otros parámetros primarios del aceite.
Introducción
El barniz es ampliamente aceptado como uno de los principales desafíos de la industria en materia de lubricación. Durante el funcionamiento de la maquinaria rotatoria, la fricción genera calor que degrada el aceite y produce subproductos: barniz. A medida que se acumula el barniz, el desempeño de la maquinaria rotatoria se ve enormemente afectado. Además, con el tiempo suficiente, los depósitos de barniz pueden curarse térmicamente en las superficies, creando una capa sólida que es difícil de eliminar y aumenta el riesgo de falla.
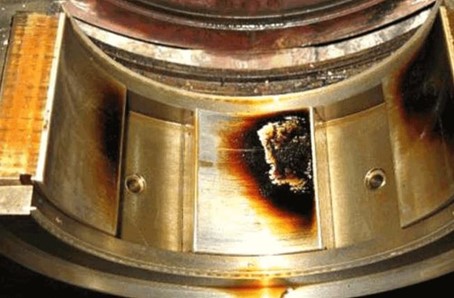
En Saudi Aramco, la degradación del aceite lubricante y el barniz son las principales causas de fallas de lubricación en nuestras máquinas rotativas críticas, lo que puede tener consecuencias devastadoras. En las empresas de petróleo y gas, las paradas de turbinas de gas debido a formaciones de barniz pueden costar hasta US $150,000 por incidente.
Por lo tanto, eliminar el barniz de los aceites lubricantes es esencial para prevenir fallas catastróficas, pérdidas operativas importantes y reparaciones costosas de la maquinaria. En respuesta a esta necesidad, se han desarrollado diversas tecnologías de eliminación de barniz que ahora están disponibles. Muchos de estos sistemas no sólo son expertos en eliminar barniz soluble e insoluble, sino también en mejorar las tasas de disipación de calor y reducir las temperaturas del sistema, evitando la formación futura de barniz.
Formación de barniz
En condiciones normales de funcionamiento, los aceites lubricantes están sujetos a oxidación, pero a medida que los equipos modernos siguen exigiendo más de sus aceites lubricantes, el estrés térmico aumenta. Este tipo de máquina está sometido a microdieseling y descargas de electricidad estática, que aceleran el proceso de oxidación del aceite lubricante. Esta degradación por oxidación produce moléculas polares a partir de aceites minerales no polares. Estas especies polares representan el punto de partida del ciclo de vida del barniz.
Actualmente, la industria tiende a utilizar aceites lubricantes altamente refinados, que tienen mayor estabilidad térmica y de oxidación, pero características de baja solvencia en comparación con los aceites lubricantes convencionales. Los subproductos oxidativos polares aumentan de tamaño debido a la polimerización. A medida que el subproducto oxidativo polar sale de la solución, se aglomeran y se acumulan en superficies metálicas polares, que atraen moléculas oxidativas polares y forman un depósito pegajoso. El barniz generalmente se forma en zonas relativamente frías con flujo bajo y tolerancias estrechas, como carretes de válvulas y reservorios de aceite, porque tienen una solubilidad relativamente baja.
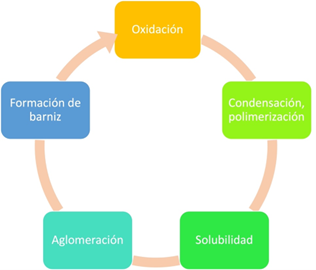
Las principales causas de la formación de barniz son:
- Descarga de electricidad estática
- Depósito compartido para circuito de aceite hidráulico y lubricante
- Puntos calientes en el sistema
- Agotamiento de aditivos
- Implosión de burbujas de aire (microdieseling)
- Circuitos hidráulicos de bajo caudal con diferenciales de temperatura
El barniz puede afectar el funcionamiento de la máquina de varias maneras:
- Acelera el proceso de degradación del aceite
- Reduce la holgura en carretes de válvulas y cojinetes debido a la formación de depósitos. Los depósitos provocan que las válvulas se atasquen y que el equipo funcione mal.
- Atrae contaminantes y aumenta el desgaste de los cojinetes
- Reduce el desempeño de los intercambiadores de calor
- Provoca obstrucción del filtro
- Reduce la disipación de calor y aumenta la temperatura del aceite y de la máqiuna.
Saturación, equilibrio y ciclo de vida del barniz
La solubilidad del barniz en el aceite lubricante depende de la temperatura y el aceite lubricante tiene una capacidad finita para disolver el barniz soluble a cualquier temperatura determinada. El punto de saturación del aceite aumenta con temperaturas elevadas y disminuye con temperaturas más bajas. La saturación de lubricante y las simetrías térmicas desempeñan papeles clave en el ciclo de vida del barniz.
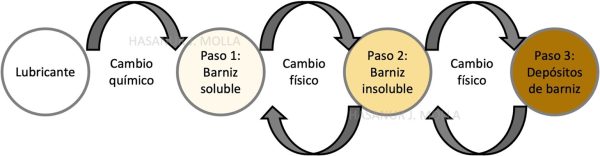
Durante el servicio, los lubricantes se degradan químicamente de manera irreversible, produciendo barniz soluble, que se acumula en el lubricante (Paso 1).
A medida que se acumula el barniz soluble, el lubricante finalmente alcanza su punto de saturación. Más allá de este punto, cualquier barniz adicional que se produzca será insoluble. La degradación continua de un lubricante saturado produce partículas de barniz insolubles (Paso 2). Estas partículas eventualmente se aglomeran y producen depósitos (Paso 3).
Los cambios de fase entre el barniz soluble e insoluble son de naturaleza física, por lo tanto, son reversibles. Debido a que los niveles de barniz dependen de la temperatura, una vez que se deposita el barniz, se pueden alterar las condiciones para cambiar positivamente el equilibrio y devolver los depósitos a un estado soluble disuelto. Esta capacidad de manipular el equilibrio es clave para eliminar completamente el barniz y mitigar los riesgos asociados al mismo.
La mayoría de los eventos de falla del lubricante ocurren en las áreas más calientes de un sistema, conocidas como “puntos calientes”. Las altas temperaturas en estos puntos calientes calientan el lubricante y aumentan su capacidad para disolver el barniz soluble. A medida que la solución de barniz lubricante se enfría en otras áreas, el punto de saturación del aceite disminuye. Aunque el lubricante puede adaptarse a los niveles actuales de barniz soluble cuando está caliente, estos niveles a menudo exceden la capacidad del lubricante en áreas más frías.
Cuando la concentración de barniz soluble de un fluido excede su punto de saturación, el lubricante se sobresatura; el barniz soluble se convertirá en barniz insoluble y se depositará hasta que baje a niveles que puedan adaptarse a esa temperatura específica. Si no se hace nada para abordar los niveles de barniz soluble presentes a las temperaturas de funcionamiento del lubricante, el barniz continuará precipitando y depositándose en regiones más frías.
Tecnologías de eliminación de barniz
Los contaminantes blandos dentro del estado de equilibrio del aceite tienden a tener un tamaño submicrón y, a menudo, son tanto solubles como insolubles. Pueden ser difíciles de extraer debido a la alta temperatura de funcionamiento de muchos lubricantes en servicio, lo que puede hacer que pasen a un estado soluble.
Actualmente existen en el mercado varias tecnologías de filtración y separación que pueden intervenir en la formación de barniz. Al eliminar continuamente los subproductos dañinos de la degradación, se reduce la concentración de precursores de barniz, lo que proporciona un aceite más limpio.
Aglomeración por cargas balanceadas
La tecnología por aglomeración de cargas balanceadas (BCA, por sus siglas en inglés) divide el fluido en dos corrientes y carga las partículas contaminantes con cargas opuestas: positiva (+) y negativa (-). Estas partículas cargadas se recombinan y mezclan bajo un flujo turbulento para formar partículas neutras más grandes, que pueden eliminarse con dispositivos de filtración mecánica tradicionales.
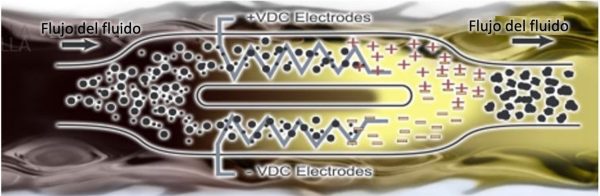
Limpiador líquido electrostático
El limpiador líquido electrostático (ELC, por sus siglas en inglés) funciona según el principio básico de que las cargas opuestas se atraen. Con la ayuda de un campo eléctrico constante, una partícula cargada positivamente es atraída hacia un electrodo negativo dentro del sistema, y las partículas con una carga negativa inherente son atraídas hacia una placa conectada a tierra. Los contaminantes polares (moléculas que tienen una distribución de carga no uniforme, un componente principal del barniz) son atraídos hacia el área de mayor intensidad de campo del medio colector.
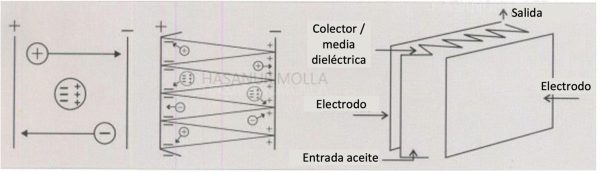
Proceso de separación electrostática
El proceso de separación electrostática (ESP, por sus siglas en inglés) es la unión física y/o química de átomos, moléculas o partículas a una superficie. El proceso de filtración se compone de adsorción y quimisorción. El medio filtrante está diseñado para eliminar ciertas sustancias químicas del fluido sin afectar los componentes de aditivos saludables.
Esta tecnología es ventajosa porque elimina productos de degradación seleccionados independientemente de si están en suspensión o en solución. Debido a su estructura química, se cree que las moléculas del barniz son atraídas por el adsorbente a través de fuerzas moleculares débiles como las de Van der Waals (o dispersión) y los enlaces de hidrógeno.
Eliminación de barniz por adsorción
La adsorción es la unión física y/o química selectiva de átomos, moléculas y partículas a una superficie (o adsorbente) como el carbón activado o sílica gel. No es lo mismo que absorción; la absorción no es selectiva y absorbe el material en el absorbente como lo hace una esponja con el agua.
Una distinción importante entre los sistemas clásicos de adsorción y filtración como elemento de procesamiento es que el desempeño del adsorbedor generalmente depende de la temperatura, el caudal, la concentración y otras condiciones operativas, mientras que los filtros son menos sensibles a tales condiciones.
Algunos filtros de aceite de alta calidad utilizan celulosa, que puede usarse como adsorbente. Tiene una gran superficie y, debido a su naturaleza química, las fibras son muy adecuadas para captar moléculas orgánicas oxigenadas, como el barniz.
Limpieza química
La limpieza química implica el uso de productos químicos para limpiar internamente el sistema de lubricación. Se apaga el equipo y se drena el aceite lubricante del sistema. Luego se utilizan ciertos productos químicos para lavar el sistema y eliminar los depósitos de barniz de las superficies internas. Este se considera un método eficaz para eliminar los depósitos internos de barniz; sin embargo, debido a que el equipo debe estar fuera de línea durante la limpieza, generalmente solo se puede realizar durante la fase de prueba e inspección o en paradas planificadas.
Principio de la tecnología de eliminación de barniz soluble
La tecnología de eliminación de barniz soluble se conecta al tanque de aceite lubricante en forma de “circuito tipo riñón”. El aceite caliente se extrae desde el punto más bajo del tanque del sistema hasta la tecnología de eliminación de barniz soluble a través de una bomba de transferencia en la unidad.
Este medio de filtración es un compuesto que consta de una matriz de fibra de celulosa y otros materiales que le dan un volumen alto de vacíos y una matriz de fibra abierta. La matriz de fibras abiertas unida con resina proporciona una alta permeabilidad, que es necesaria para que el fluido entre en contacto con la gran superficie de la fibra y para que los precursores del barniz sean absorbidos. Estas resinas aglutinantes especialmente formuladas le dan al medio filtrante una alta afinidad por los precursores del barniz polar, lo que resulta en una alta eficiencia de eliminación y retención del material suspendido en la fase fluida.
Las resinas de intercambio iónico selectivo se mezclan y formulan para absorber el barniz dentro de su estructura porosa. Esta naturaleza absorbente se debe a la atracción polar entre la resina de intercambio iónico y el barniz. Hay grandes cantidades de superficie por volumen, lo que hace que este proceso sea muy eficaz.
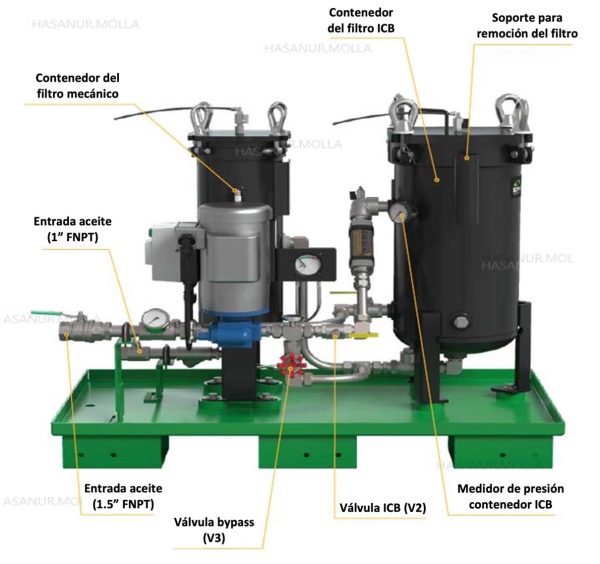
Los sistemas de eliminación de barniz soluble utilizan una media filtrante de enlace de carga iónica (ICB, por sus siglas en inglés) especializada que contiene miles de millones de sitios capaces de adsorber barniz soluble. Esta adsorción se basa en una interacción preferencial entre las moléculas del barniz y los sitios presentes dentro de la media.
Los sistemas de eliminación de barniz soluble interrumpen el ciclo de vida del barniz en su etapa más temprana y evitan que el barniz soluble se acumule en el lubricante y forme partículas y/o depósitos de barniz dañinos. Dado que los contaminantes solubles que eliminan prevalecen a las temperaturas de funcionamiento, estos sistemas también son adecuados para uso continuo durante el funcionamiento de la turbina.
Cuando el barniz soluble se elimina continuamente, los niveles presentes permanecen muy por debajo del punto de saturación del lubricante. Esto significa que se elimina eficazmente el riesgo de que se formen depósitos de barniz en zonas más frías o durante las paradas.
Mientras que otros sistemas de eliminación de partículas no pueden eliminar tanto el barniz soluble como el insoluble, los sistemas de eliminación de barniz soluble aprovechan el equilibrio que existe entre estas dos fases para eliminar todo el barniz. Esto incluye no sólo el barniz presente en el lubricante sino también el barniz que pueda haberse depositado previamente en las superficies del sistema de lubricación.
Metodología piloto
Esta tecnología de eliminación de barniz soluble con un caudal de 7.5 galones por minuto (GPM) se evaluó en colaboración con Saudi Aramco, donde se puso a prueba en un depósito de lubricante de una turbina de gas M58-CGTG-07. La capacidad del depósito era de 1700 galones y la máquina estaba funcionando con aceite de turbina de gas ISO VG 32. La turbina fue seleccionada debido a su alto potencial de barniz medido mediante MPC, con un valor de 35, que fue confirmado por un informe de análisis de aceite, como se ve en la Figura 7.
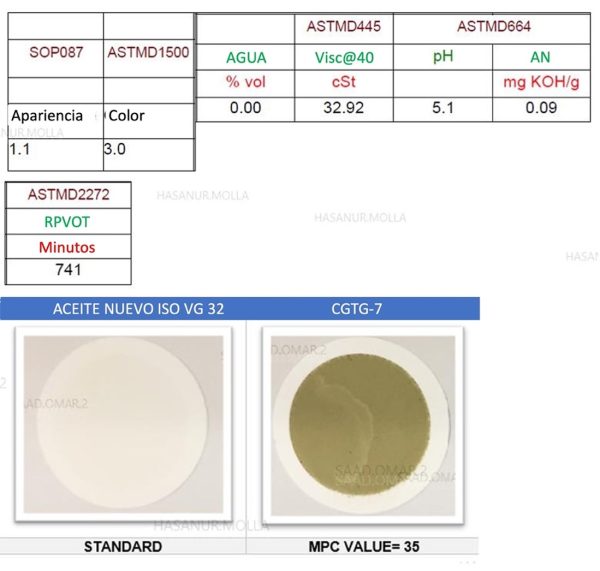
El sistema de eliminación de barniz soluble se instaló en el depósito de aceite lubricante por un período de aproximadamente tres meses. Se tomaron muestras de la salida del dispositivo para probar su eficacia.
Métodos de evaluación
La evaluación de la tecnología de eliminación de barniz soluble se llevó a cabo tanto en el laboratorio como en sitio para evaluar su eficacia en la eliminación del barniz del aceite lubricante en servicio.
Se realizaron los siguientes análisis para evaluar el estado del aceite de la turbina de gas en servicio CGTG-07.
- Potencial de barniz mediante colorimetría de membrana (MPC): ASTM D7843
- Número ácido (AN): ASTM D664
- Oxidación por espectrometría infrarroja por transformada de Fourier (FTIR): ASTM E2412
- Aditivos antioxidantes RULER: ASTM D6971
- Espectrometría de absorción atómica: ASTM D5185
- Conteo de partículas ISO: ISO 11500 e ISO 4406.
Luego se prepararon columnas de eliminación de barniz soluble a escala de laboratorio para evaluar la eficacia del tratamiento del fluido utilizando media filtrante de enlace de carga iónica. Luego se pasó una porción de cada muestra de aceite proporcionada a través de columnas separadas durante 24 horas a una velocidad de 20 ml/minuto y una temperatura de 40 °C. Después del tratamiento de eliminación del barniz soluble, se repitieron los análisis enumerados anteriormente y sus resultados se utilizaron para evaluar la eficacia de la eliminación del barniz soluble en laboratorio.
Resultado de la evaluación en laboratorio
En total, Saudi Aramco envió al laboratorio una muestra de aceite nuevo de turbina de gas ISO VG 32 y otra de aceite usado recolectada de la turbina de gas CGTG-07 para determinar la condición del aceite lubricante en servicio y evaluar la efectividad de la tecnología de eliminación de barniz soluble.
Los resultados de la evaluación de laboratorio se muestran a continuación:
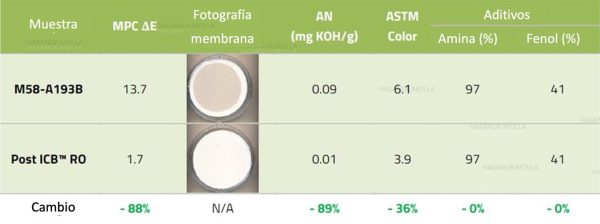
El MPC del aceite usado sugirió que el barniz se convertiría en un problema grave en un futuro próximo. Afortunadamente, la tecnología ICB eliminó eficientemente el barniz acumulado y el MPC ΔE del aceite disminuyó en un 88 % después del tratamiento de eliminación de barniz soluble a escala de laboratorio.
Con estos valores de MPC drásticamente reducidos, se mitigaron los riesgos asociados con el barnizado. Además, dado que los barnices solubles e insolubles depositados dentro de un sistema existen en equilibrio entre sí, la eliminación del barniz soluble provocaría que el barniz previamente depositado se volviera a disolver. Una vez redisuelto, la tecnología de eliminación de barniz soluble también eliminaría este barniz.
Estos hallazgos fueron corroborados por análisis de color y número ácido, que mostraron una disminución del 36% y del 89% respectivamente en los niveles de precursores de barniz, respectivamente, y el número ácido del fluido se redujo a niveles mejores que los del aceite nuevo. Estos resultados resaltan que la media filtrante no solo retiene el barniz ya presente, sino también materias primas clave para el barniz.
Dado que la filtración para eliminar el barniz se produce de forma continua, estos precursores del barniz se pueden eliminar a medida que se forman, evitando por completo los problemas del barniz.
Finalmente, debido a que la media filtrante está diseñada para dejar intactos los aditivos deseables, no se observó pérdida de aditivos en el aceite en servicio.
Evaluación de campo
La muestra final tomada antes de completar la prueba reveló que:
- El número ácido, el contenido de humedad y la viscosidad estaban todos dentro del rango objetivo deseado
- El conteo de partículas del fluido de acuerdo con ISO 4406 había disminuido del 18/20/12 a 12/15/9
- El MPC ΔE ahora era <15, lo que indica un bajo nivel de subproductos de degradación dentro del fluido
- Si bien los niveles de silicio estaban por encima del objetivo y los niveles de fósforo estaban por debajo, todos los demás metales disueltos estaban dentro del rango objetivo
- El color del fluido estaba por encima del objetivo
- El 100 % de las aminas del aceite y el 100 % de los antioxidantes fenólicos del aceite permanecieron similares a las muestras analizadas durante la puesta en marcha del sistema, lo que indica que no hubo impacto en el contenido de aditivos en el aceite lubricante.
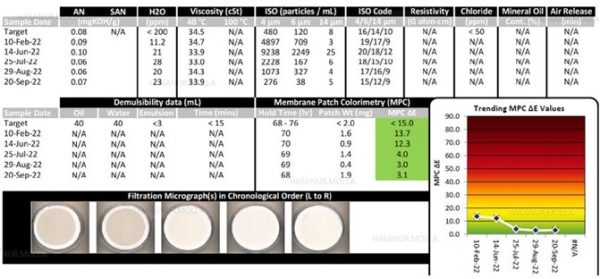
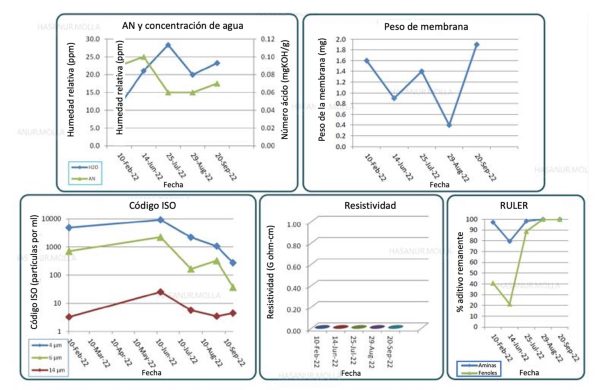
Nota: Esta prueba se llevó a cabo en condiciones controladas. Los resultados pueden variar según la condición y el desempeño de la unidad y la calidad del aceite lubricante.
Conclusión
La aplicación de una tecnología de eliminación de barniz soluble facilitó la limpieza del aceite al eliminar eficazmente el barniz soluble e insoluble del sistema de aceite lubricante. Además de mejorar la confiabilidad de la turbina, eliminó la necesidad de cambio prematuro inmediato del aceite lubricante, lavado del sistema y limpieza química.
Referencias
- “Lubricant Varnishing and Varnish Mitigation” de MG Hobbs y PT Dufresne Jr. de EPT, publicado en LUBMAT 2014, Manchester, Reino Unido.
- “The Root Cause of Varnish Formation” por Buddy Atherton, gerente de ventas técnicas, United Air Specialists, Inc./Kleentek
- “Sludge and Varnish in Turbine Systems” de Jim Fitch de Noria Corporation, publicado en Machinery Lubrication, USA.
Autores
Hasanur Jamal Molla es ingeniero de lubricación que trabaja con Saudi Aramco en Central Engineering y es responsable de gestionar el programa de lubricación en toda la empresa. Tiene alrededor de 20 años de experiencia en el campo de la lubricación y trabajó con muchas empresas de lubricantes de renombre antes de unirse a Saudi Aramco. Se ha ocupado de la resolución de problemas de equipos rotativos, fallas de lubricación, programas de monitoreo de la condición del aceite lubricante y también ha brindado consultas a instalaciones y proyectos operativos. Tiene BE y ME en Ingeniería Mecánica del Instituto Indio de Ciencia y Tecnología de Ingeniería (IIEST), India. Es autor de numerosos artículos y artículos sobre lubricación y tiene pocas patentes a su nombre. También está certificado con Vibration Analyst CAT-II por Vibration Institute y Machinery Lubricant Analyst II (MLA-II) por ICML.
Abdullah B. Samman es ingeniero de lubricación y trabaja en Saudi Aramco Central Engineering. Tiene una licenciatura en Ingeniería Mecánica de la Universidad de Leeds. Desde que se unió a Aramco en 2015, ha trabajado en varios temas en el campo de los equipos rotativos y la lubricación. Se ha ocupado de la resolución de problemas de equipos rotativos, fallas de lubricación, programas corporativos de monitoreo de la condición de lubricantes y ha brindado consultas a instalaciones y proyectos operativos. También está certificado como Machinery Lubricant Analyst II (MLA-II) por ICML.
Saad H. Al-Dossary es un distinguido consultor de ingeniería con amplia experiencia en análisis dinámico y vibración. Con más de 25 años de experiencia en el campo, ha adquirido un vasto conocimiento y experiencia en la resolución de problemas complejos de ingeniería relacionados con el análisis y la gestión de vibraciones de maquinaria. Actualmente, Saad es el líder del grupo de Saudi Aramco en Dynamic Analysis Group (DAG), que se ocupa de todos los temas relacionados con el análisis de vibraciones y la lubricación en Saudi Aramco. Es responsable de supervisar un equipo de expertos, garantizar que se aborden todos los problemas de vibración y lubricación relacionados con los equipos de la empresa y brindar recomendaciones sobre cómo mejorar su desempeño. Saad tiene una Licenciatura en Ingeniería Mecánica de la Universidad de Nebraska Lincoln, EE. UU. También obtuvo una Maestría en diseño de máquinas rotativas de la Universidad de Cranfield en el Reino Unido. Es autor de varios artículos y artículos sobre vibración y lubricación y miembro de varias organizaciones profesionales. La experiencia de Saad como consultor de ingeniería y su amplio conocimiento en análisis de vibraciones de maquinaria lo convierten en un activo invaluable para cualquier proyecto de ingeniería que requiera experiencia en vibración y lubricación. Está comprometido a brindar servicios de calidad a los clientes y brindar soluciones que garanticen el funcionamiento eficiente y seguro de su maquinaria.
Meshaal S. Al-Uthman trabaja como ingeniero de confiabilidad en las plantas de Saudi Aramco Abqaiq con más de 6 años de experiencia. Comenzó su carrera en Saudi Aramco como ingeniero de soporte técnico para diferentes campos de petróleo y gas. Luego se unió a los proyectos de expansión del campo petrolero de Khurais y actualmente apoya las actividades de puesta en marcha de los proyectos de desarrollo de almacenamiento de gas de Hawiyah. Su área de especialización se centra en la gestión de activos, mejoras de confiabilidad y gestión de proyectos. Tiene una maestría en gestión de ingeniería de la Universidad de Petróleo y Minerales Rey Fahd (KFUPM). También es un profesional certificado en mantenimiento y confiabilidad (CMRP) por SMRP y posee una calificación en gestión de activos del Instituto de Gestión de Activos (The IAM) en el Reino Unido.
Nadheer L. Al-Qudsi es jefe del grupo de confiabilidad de Saudi Aramco y trabaja en las plantas de Abqaiq, la instalación de estabilización de petróleo más grande del mundo, con más de 15 años de experiencia en los campos de confiabilidad y turbomaquinaria. Dirigió muchos estudios de confiabilidad, proyectos e investigaciones de fallas de equipos que contribuyeron a mejorar la confiabilidad de las plantas Abqaiq. Tiene una licenciatura en Ingeniería Mecánica de la Universidad de Petróleo y Minerales Rey Fahad (KFUPM) y una maestría de la Universidad de Ottawa. También es Profesional Certificado en Mantenimiento y Confiabilidad (CMRP) por SMRP, Ingeniero de Confiabilidad Certificado (CRE) por ASQ, Líder de Confiabilidad Certificado (CRL) por AMP, Analista de Vibraciones Certificado CAT-III por Mobius Institute y Machinery Lubricant Analyst I (MLA-I) por ICML.