A medida que la práctica del análisis y muestreo de aceite evoluciona desde una actitud de “lo que funcione” hacia una habilidad comercial más definida, las técnicas y procedimientos también deben evolucionar. Los principios detrás del análisis de aceite como herramienta de mantenimiento proactivo permiten a las empresas utilizar la información recopilada para realizar análisis de causa raíz y convertir un programa de análisis de aceite en algo más que un simple indicador de cambio de aceite. Con la capacitación e información adecuadas, los empleados pueden utilizar un programa de análisis de aceite como una herramienta eficaz de monitoreo basada en la condición.
Al actualizar un programa de análisis de aceite obsoleto o mal concebido a una herramienta eficaz de monitoreo basada en la condición, es posible que sea necesario actualizar y mejorar algunas cosas; como ubicaciones de muestreo, el tipo de válvulas de muestra utilizadas y el procedimiento empleado para extraer la muestra de forma segura y precisa del equipo. Después de todo, el análisis realizado por el laboratorio es tan bueno como la muestra de aceite que recibe.
Esto es particularmente cierto para las aplicaciones hidráulicas industriales, que normalmente incluyen una multitud de componentes diferentes, como válvulas, bombas, motores, filtros, etc.
Históricamente, las muestras de aceite de los sistemas hidráulicos se tomaban directamente del reservorio o tanque. Si bien esta ubicación es aceptable si la información deseada se refiere a la condición de las propiedades físicas y químicas del aceite, un programa de análisis de aceite verdaderamente eficaz también debe incluir pruebas de desgaste y contaminación como conteo de partículas, concentración de agua y detección y análisis de partículas de desgaste. Todas estas pruebas son extremadamente sensibles a la ubicación del puerto de muestreo, por lo que a medida que evoluciona un programa, también debería hacerlo la estrategia de muestreo.
Muestreo en sistemas hidráulicos
Los sistemas hidráulicos de alta presión utilizan reservorios para mantener el lubricante a presión atmosférica. Aquí es donde comienzan la mayoría de los programas de análisis de aceite y donde la mayoría de los analistas toman muestras. Los reservorios son un buen lugar para comprobar la salud del lubricante. Sin embargo, los datos recopilados en esta ubicación son muy poco específicos en términos de indicar la condición del sistema hidráulico (desgaste) o el ingreso de contaminación.
Si el análisis de aceite va a convertirse en una herramienta verdaderamente efectiva de monitoreo basado en condición, entonces la ubicación de muestreo debe reasignarse para aislar los componentes del sistema y proporcionar muestras más representativas de toda la máquina. Esto puede requerir tomar más de una muestra por sistema. Sin embargo, una vez identificados y aislados los componentes, se pueden tomar mejores decisiones con respecto a la confiabilidad y el mantenimiento del sistema en función de los datos recopilados.
Por ejemplo, considere el sistema hidráulico simple que se muestra en la Figura 1. La falla de la placa de empuje en la bomba puede generar una cierta cantidad de partículas de desgaste, equivalente a una concentración de 250 ppm medida por espectrometría de elementos, directamente después de la bomba.
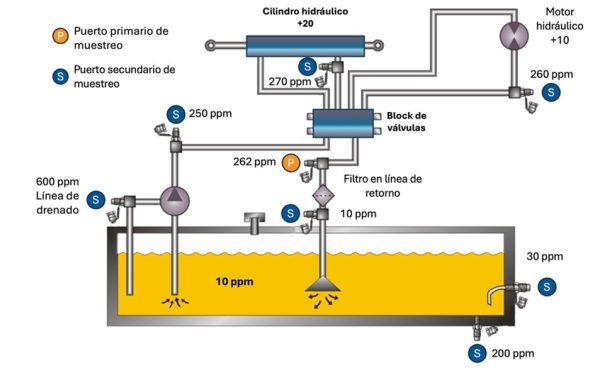
Sin embargo, una vez que el aceite pasa por el sistema y regresa al reservorio, la concentración de partículas de desgaste será significativamente menor, debido a una combinación del filtro de la línea de retorno, pero más significativamente al factor de dilución, causado por suspender la misma cantidad de partículas de desgaste en el gran volumen de aceite en el reservorio. De hecho, las fallas de la bomba hidráulica a menudo pasan desapercibidas debido al muestreo en el reservorio. Para el usuario de análisis de aceite sin educación, la percepción es que el análisis de aceite no es una herramienta efectiva de monitoreo de condición, cuando en realidad es el procedimiento de muestreo el que falla.
Para monitorear de manera más efectiva sistemas complejos, se debe emplear una estrategia de muestreo de aislamiento de componentes. El aislamiento de componentes significa exactamente eso; el componente se aísla y se toma una muestra por separado del resto de la máquina. Al hacerlo, el análisis de aceite proporciona una instantánea del estado de esa parte del equipo en un momento específico, separado de otras ubicaciones. Para hacer esto, se deben recolectar muestras después de todos los componentes críticos y comparar los resultados con los datos recopilados antes del mismo componente.
Todos los elementos del sistema hidráulico de la Figura 1 se consideran críticos. Si alguno de estos componentes falla, el sistema no puede funcionar dentro de las especificaciones de diseño. Por lo tanto, es esencial que se observe la tendencia del estado de estos componentes para mantener la confiabilidad.
Cuando se emplea una estrategia de aislamiento de componentes, los puertos de muestra deben instalarse en zonas turbulentas donde se logra la máxima densidad de datos con una mínima alteración de los datos.
Si bien el muestreo después de cada componente en el sistema simple (como el que se muestra en la Figura 1) se logra fácilmente, una vez que se han instalado las válvulas de muestreo, en sistemas más complejos, el aislamiento de los componentes puede requerir alrededor de 10 a 15 puntos de muestreo. Dado que el muestreo de cada punto de forma rutinaria suele tener un costo prohibitivo, una buena estrategia es localizar un punto de muestreo primario para el monitoreo de rutina.
Luego, el primario está respaldado por puntos de muestreo secundarios ubicados apropiadamente y que se utilizarán en caso de una excepción para fines de solución de problemas. Para la mayoría de los sistemas hidráulicos, una buena ubicación para un único puerto de muestreo primario es en la línea de retorno, antes del filtro en la línea de retorno, como se muestra en la Figura 1. Para sistemas con múltiples líneas de retorno, es posible que se requieran múltiples ubicaciones de muestreo primario.
Dependiendo de los componentes específicos del sistema, es posible que sea necesario instalar más de un puerto de muestreo en un solo componente. Por ejemplo, considere un motor de pistones radiales de velocidad variable. Este tipo de motor tiene dos cámaras internas separadas que son independientes entre sí. Una cámara es la carcasa del motor, que alberga todos los componentes mecánicos del motor, incluidos cojinetes, anillos de retención, casquillos y sellos. La otra cámara es el lado de presión del motor, que alberga los pistones para la entrada y salida de fluido. El drenaje de la carcasa y la salida del motor pueden proporcionar muestras independientes y ricas en datos que indican la condición del motor y ambos deben considerarse puntos de muestreo. En este caso, debido a que los principales componentes de trabajo del motor están alojados y lubricados en la carcasa de la bomba, la mayoría de las partículas de desgaste volverán al tanque sin pasar primero por el sistema.
En este caso, una muestra de la línea de retorno tendrá pocas posibilidades de diagnosticar una falla en el lado de la caja del motor de este componente, mientras que una muestra de la línea de drenaje de la caja no proporcionará una advertencia de problemas en el pistón. Para monitorear efectivamente este componente, se deben tomar dos muestras.
El mercado actual ofrece varias opciones para puertos de muestreo de aceite a alta presión. El tipo de válvula más confiable para usar en aplicaciones de alta presión es una válvula de retención que utiliza una bola de retención normalmente cerrada sobre un asiento de metal (Figura 2). Estas válvulas se pueden utilizar en sistemas con presiones de hasta 9,000 psig, lo que permite un muestreo con sonda de hasta 5,000 psig. Para extraer una muestra, se utiliza un adaptador para mover la bola de control y permitir que el líquido fluya hacia la botella de muestreo.
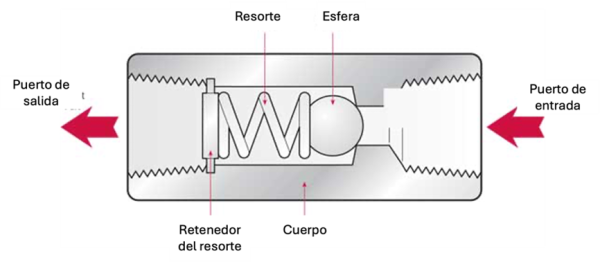
Muestreo hidráulico de forma segura
Cuando se manejan mal, los sistemas hidráulicos de alta presión pueden causar lesiones graves o hasta la muerte. Incluso un pequeño orificio en una línea hidráulica de alta presión puede causar lesiones graves. Siempre que se extrae una muestra, se deben tomar todas las precauciones necesarias para garantizar la seguridad no solo del recolector de muestras, sino también de quienes trabajan alrededor del sistema.
Debido a estas preocupaciones de seguridad, a menudo existen restricciones para acceder al equipo mientras está en funcionamiento. Las mangueras microbore se utilizan ampliamente junto con puertos de muestreo estándar y tubing para llevar la ubicación de la válvula de muestreo a un panel u otra ubicación considerada segura. Debido al orificio nominal de 2 mm dentro de la manguera microbore, solo es necesario enjuagar una cantidad relativamente pequeña de fluido, lo que permite tomar una muestra representativa. Incluso para una manguera de 3 metros de longitud, sólo es necesario purgar 120 ml de líquido.
Tomar una muestra de un sistema hidráulico de alta presión requiere el uso de herramientas que garanticen la seguridad del técnico que toma la muestra. Las válvulas reductoras de presión se utilizan ampliamente para reducir la presión del sistema a un nivel seguro para extraer una muestra de aceite. Estas válvulas se utilizan junto con accesorios de muestreo estándar. Normalmente, una manguera microbore corta (diámetro nominal de 2 mm) conecta el puerto de muestreo a la válvula portátil reductora de presión.
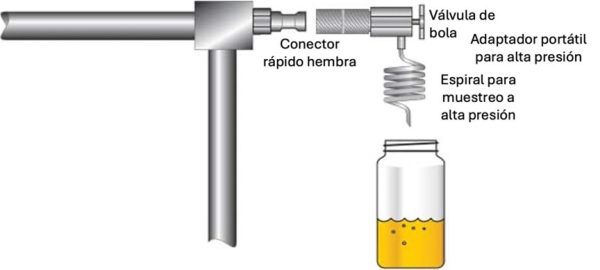
Luego, la válvula reductora de presión reduce la presión de 5000 psig a una presión de salida aceptable tan baja como 50 psig. Luego se conectan un adaptador de puerto de muestreo y un tubo de muestreo limpio a la salida de la válvula reductora de presión. Se puede lograr un efecto similar usando una pequeña bobina helicoidal de tubería como se muestra en la Figura 3.
Cualquiera que sea el método utilizado, es importante lavar la manguera microbore y cualquier válvula o tubería adicional utilizada al menos cinco a diez veces su volumen total.
En muchas industrias, los sistemas hidráulicos son fundamentales para la producción y el control de procesos. Cuando se utiliza correctamente, el análisis de aceite es una herramienta eficaz para resaltar no sólo la condición del fluido, sino también el de todos los componentes críticos de estos sistemas. Si se siguen algunas reglas simples y se instalan puertos de muestreo primarios y secundarios en ubicaciones apropiadas, las señales tempranas de advertencia de ingreso de contaminación y desgaste de componentes pueden usarse como herramientas vitales en la lucha contra el tiempo de inactividad no programado.
Referencia: Noria Corporation. Traducción por Roberto Trujillo Corona, Noria Latín América