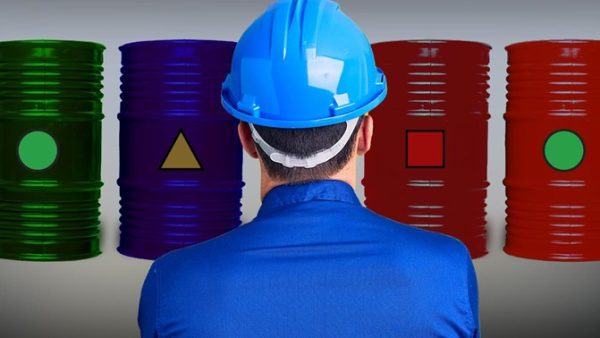
Bajo la presión de ser más competitivas, las empresas toman decisiones estratégicas para cambiar de proveedor de lubricantes. Menores costos, mejores productos y servicios son los incentivos para el cambio.
Sin embargo, la idea de cambiar de proveedor de lubricantes, especialmente después de permanecer con el proveedor actual durante mucho tiempo, puede resultar problemática. Además de los altos costos por el cambio, la incertidumbre sobre su impacto en el corto plazo puede retrasar muchas oportunidades que se pueden obtener de un nuevo proveedor.
Comprender los riesgos y los posibles problemas al cambiar los lubricantes puede aliviar estas preocupaciones. Los riesgos se pueden clasificar como de desempeño, compatibilidad y aplicación. Mitigar estos riesgos garantizará un proceso de cambio exitoso y ágil.
Riesgos de desempeño
Uno de los riesgos clave al cambiar los lubricantes es la calidad y el desempeño del aceite nuevo. El nuevo lubricante podría ser inferior y tener debilidades en comparación con el lubricante actual, lo que puede provocar problemas de confiabilidad. Debe buscar que el aceite nuevo tenga al menos el mismo o mejor desempeño que el aceite actual.
El primer paso para gestionar este riesgo es revisar los requisitos de lubricación de su máquina y establecer una línea base o desempeño mínimo. La primera referencia siempre deben ser las especificaciones del fabricante de equipo original (OEM, por sus siglas en inglés). También debe considerar las condiciones operativas como la carga, la temperatura, la velocidad, los materiales y el ciclo de trabajo de los componentes lubricados de sus máquinas. Luego podrá hacer coincidir esos requisitos con las propiedades de los lubricantes que le ofrecen los proveedores.
La mayoría de las empresas eligen el camino más fácil: obtener equivalentes de los lubricantes actuales en lugar de revisar los requisitos de la máquina. Aunque es más rápido, no es aconsejable. Esta práctica supone que el producto actual es el lubricante adecuado para la máquina. A veces este no es el caso.
Además, es posible que el lubricante correspondiente no sea necesariamente un equivalente directo en términos de especificación y formulación. Revisar los requisitos de lubricación de la máquina puede evitar posibles errores o el uso de un lubricante inferior al óptimo.
Además de la facilidad, las empresas prefieren seguir la ruta de la equivalencia de productos porque no tienen buenos registros de las especificaciones de lubricación de sus máquinas y el contexto operacional. Lo único que tienen es un registro histórico de compras. Realizar una revisión de los requisitos de lubricación es una oportunidad para establecer una referencia maestra de lo que necesitan sus activos.
Los proveedores de lubricantes pueden afirmar que su aceite está aprobado según ciertos organismos industriales o estándares del OEM. Como usuario final, debe verificar esto directamente con la organización emisora del estándar o el propio OEM.
Hay ocasiones en las que los lubricantes del nuevo proveedor no se pueden verificar según los estándares que afirman. Esto se debe a que algunos organismos industriales y fabricantes de equipos originales no otorgan aprobaciones para marcas específicas. Los fabricantes de lubricantes deben cumplir sus estándares, y ellos tienen la responsabilidad de demostrar que sus productos cumplen con los estándares.
Cuando no se pueden verificar los estándares, es posible que deba confiar en la credibilidad del proveedor de lubricantes. ¿Existe alguna justificación para confiar en ellos? ¿Qué información y trayectoria conoce sobre ellos y sus productos? ¿Existe algún cliente de referencia del que pueda obtener la información? ¿Existen datos de desempeño sobre el uso exitoso de lubricante nuevo en máquinas y condiciones similares?
En ausencia de lo anterior, deberá evaluar la calidad y el desempeño del lubricante mediante pruebas del producto. Los laboratorios comerciales pueden realizar pruebas estándar como viscosidad, elementos metálicos, AN/BN y conteo de partículas. Estos resultados pueden darle una idea básica de las propiedades típicas y la composición del nuevo lubricante. Sin embargo, para conocer verdaderamente su desempeño se requieren pruebas avanzadas. Esto significa que necesita acceso a laboratorios de pruebas especializadas. A menudo, los costos y el tiempo impiden que la mayoría de las empresas hagan esto.
Alternativamente, puede efectuar una prueba del producto en su planta. Elija las máquinas menos críticas y haga funcionar el nuevo lubricante durante un período predeterminado. Supervise las condiciones de la máquina y del aceite mediante análisis de lubricante.
Vale la pena acortar los intervalos de muestreo para la detección temprana de anomalías. Si la prueba en las máquinas menos críticas muestra resultados prometedores, se puede aumentar a más máquinas y a las más críticas.
Riesgo de compatibilidad
Los nuevos lubricantes podrían ser incompatibles con los anteriores cuando se mezclan en un tanque de almacenamiento, lo que podría provocar un desempeño deficiente del lubricante y otros problemas de confiabilidad asociados. Mitigar este riesgo requiere una evaluación de compatibilidad entre los aceites nuevos y actuales basada en la comprensión de su tipo de aceite, aceite base, aditivo y composición de espesante (para grasa).
Existen reglas generales para determinar la compatibilidad entre productos. Empezando por el aceite base, los sintéticos como los polialfaolefinas (PAO) y los diésteres suelen ser compatibles con los aceites minerales. El polialquilén glicol (PAG), sin embargo, no lo es.
Para los aceites de motor, la capacidad de mezcla entre la misma clasificación de desempeño API y el grado de viscosidad SAE no debería ser un problema. Para otros aceites, la incompatibilidad a menudo se debe a la combinación de tecnologías de aditivos ácidos y alcalinos. Mezclar estos dos tipos se anularán entre sí. Como resultado, se formarán sustancias sólidas que cambiarán las propiedades físicas y químicas del aceite. Es probable que esto ocurra si se mezclan diferentes tipos de aceite, por ejemplo, aceite de motor y aceite de turbina.
Aunque no es común mezclar intencionalmente diferentes tipos de aceite, aún puede ocurrir incompatibilidad con tipos similares, como al mezclar aceites hidráulicos con aditivos de zinc y sin zinc. Consulte con su proveedor de aceite para identificar si sus productos incluyen tecnologías de aditivos ácidos y alcalinos.
En cuanto a la grasa, la compatibilidad entre los espesantes es la más crucial. La consistencia de la grasa NLGI se verá afectada cuando entren en contacto espesantes incompatibles.
Dado que existen muchos espesantes diferentes, se debe consultar una tabla de compatibilidad de grasas. Esto se presenta en la Tabla 1 :
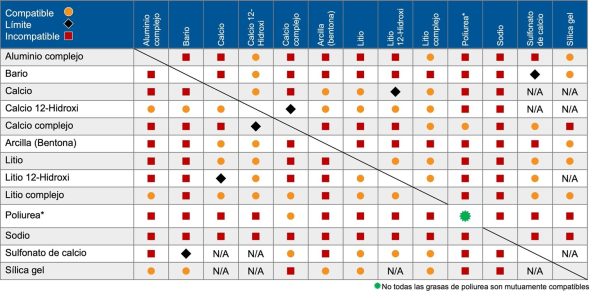
También puede determinar la compatibilidad basándose en las especificaciones del OEM y de la industria. Ciertas especificaciones estipulan que los aceites deben pasar pruebas de compatibilidad con diferentes tipos de aditivos de las mismas especificaciones o relacionadas. API y Caterpillar TO-4 son ejemplos de especificaciones que permiten la mezclabilidad entre aceites dentro de la misma especificación.
Si su proveedor de aceite no está seguro o no puede proporcionarle información suficiente, es mejor asumir que son incompatibles. Esto justifica efectuar pruebas de compatibilidad para determinar que los dos aceites, al ser combinados, no sufrirán cambios en sus propiedades y el desempeño, lo que los llevará a ser inferiores a los aceites de forma individual.
Mezcle los aceites vírgenes nuevos y actuales en tres proporciones, 90:10, 50:50 y 10:90, para simular diferentes condiciones de mezcla. Caliente las mezclas a 65 ⁰C continuamente durante siete días mientras se observa cualquier cambio en la apariencia y la precipitación de sedimentos. Un claro indicador de incompatibilidad es la formación de depósitos que obstruirán los filtros y dificultarán el flujo de aceite.
La ausencia de cambios en la apariencia no significa que los aceites sean 100% compatibles. Las máquinas críticas, como las turbinas, requerirán pruebas adicionales para garantizar que no se produzca ninguna degradación del desempeño durante el servicio.
Algunas de las pruebas de seguimiento recomendadas son viscosidad cinemática a 40 ºC (ASTM D445), número ácido (ASTM D664 o D974), propiedades de formación de espuma (ASTM D892), propiedades de liberación de aire (ASTM D3427), separabilidad del agua (ASTM D1401) y prueba de oxidación de recipiente rotativo a presión (ASTM D2272).
Si se descubre que alguno de los lubricantes nuevos es incompatible, se deben tomar medidas para minimizar el contacto con los lubricantes actuales durante la transición. Se deben implementar procedimientos de cambio total de lubricantes para eliminar cualquier posibilidad de mezclar fluidos incompatibles, siempre que sea práctico. Por ejemplo, los tanques de almacenamiento y los compartimentos de las máquinas deben lavarse y limpiarse antes de llenarlos con los nuevos lubricantes.
Riesgo de aplicación
El riesgo de aplicación implica que el personal de mantenimiento aplique el aceite incorrecto debido a la falta de familiaridad con el nombre y el empaque del nuevo lubricante. Este error puede ser catastrófico.
Una gestión adecuada del proceso de cambio es clave para gestionar la transición. Se debe asignar a una persona como líder general o gerente de proyecto para manejar el proceso de cambio de principio a fin. Involucre al proveedor de lubricante y a todas las partes interesadas dentro de su planta para obtener sus opiniones. No queremos tener problemas de cambio por un descuido. La comunicación es primordial. Todos los usuarios, especialmente el personal que recibe, almacena, transfiere y aplica lubricantes en las máquinas, deben estar al tanto de los cambios. Los procedimientos e instrucciones fáciles de entender ayudarán enormemente a que el cambio sea perfecto.
Una herramienta importante es un cuadro de referencias cruzadas. Muestra los lubricantes nuevos y actuales uno al lado del otro y el compartimiento de la máquina en el que deben colocarse. Para evitar confusiones, es preferible que el director del proyecto revise el cuadro con el personal correspondiente para asegurarse de que todos lo comprendan.
Esto permite formular y abordar preguntas más temprano que tarde. La tabla de referencias cruzadas también debe ser accesible y exhibirse claramente en las áreas donde se llenan los lubricantes, siempre que sea práctico.
El área de almacenamiento de lubricante y todos los puntos de dosificación y llenado deben estar claramente etiquetados con el nombre del nuevo lubricante junto con los lubricantes viejos que se están reemplazando. Una vez finalizada la transición, la antigua etiqueta de lubricante deberá retirarse totalmente de la planta. Los documentos de mantenimiento, como la hoja de servicio, deberán actualizarse con aceites nuevos a medida que se desechen los viejos.
Durante el período de transición, tendrá que almacenar lubricantes nuevos y viejos al mismo tiempo. Todos los envases y contenedores de lubricantes viejos deben marcarse para saber si están agotados y detener el pedido una vez terminado. En este caso, el principio «primero en entrar, primero en salir (PEPS/FIFO)» debe estar estrictamente establecido. No queremos encontrar envases de aceite viejo sin abrir o sin usar en la planta a mitad de la transición, cuando todas las máquinas ya están llenas con aceite nuevo.
Peor aún, alguien, sin querer, vuelve a pedir el lubricante viejo cuando se está realizando el cambio, pensando que tiene pocas existencias. Este es un error común y puede ocurrir fácilmente en su planta sin la capacitación adecuada sobre el reemplazo adecuado del lubricante.
Si tiene un programa de análisis de aceite implementado, el laboratorio debe ser informado del cambio. Las propiedades del aceite, la composición de los aditivos y la concentración pueden ser ligeramente diferentes. Esto podría causar una falsa alarma cuando las lecturas resulten diferentes a la referencia del aceite viejo.
Por ejemplo, algunos aceites de motor contienen más concentración de magnesio como detergente que otros. Esto se puede mitigar suministrando una muestra del aceite nuevo al laboratorio para analizarla y registrar las lecturas como una nueva línea de base para referencia.
Cuando estos tres riesgos se gestionan adecuadamente, las empresas tienen una interrupción mínima en sus operaciones durante un cambio de lubricante. Aunque puede haber problemas iniciales, los beneficios a largo plazo de tener una mejor calidad, desempeño y servicio del lubricante superan con creces todos los obstáculos potenciales.
Referencia: Aaron Said, International Lubricant Distributors (ILD). Traducción por Roberto Trujillo Corona, Noria Latín América