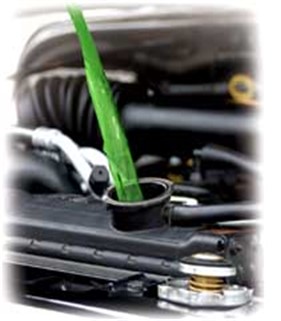
La introducción de glicol en los aceites lubricantes expone sus máquinas a una mezcla poderosa y venenosa de químicos. A diferencia de otros contaminantes dañinos como el agua y la tierra, el potencial destructivo del glicol puede provocar fallas masivas de los componentes de la máquina en un corto período de tiempo.
Difícilmente podría haber un papel más importante para el analista de lubricante que el análisis rutinario del aceite para detectar la presencia de glicol.
Un gran laboratorio de análisis de aceite que se especializa en equipos de flotas de servicio pesado desplegados en minería y construcción informó que se encontró glicol en el 8.6 por ciento de las muestras de aceite de motor durante un período de años, aproximadamente una de cada 12 muestras.
De hecho, los laboratorios de análisis de aceite han estado realizando pruebas para detectar fugas de refrigerante en aceites usados de motor y otros lubricantes para trenes de transmisión de potencia durante casi el mismo tiempo que existen las pruebas de aceite usado. Las técnicas varían considerablemente de un laboratorio a otro, al igual que los límites de alarma. Este artículo destaca el tema de las pruebas de glicol en el laboratorio de análisis de aceite al describir las últimas técnicas de laboratorio para detectar y medir su concentración, además de consejos para la resolución de problemas.
Cómo se formula y utiliza el glicol
El glicol, el ingrediente principal del anticongelante, generalmente se mezcla con agua 50/50 para formar un “refrigerante” líquido para transferir calor, elevar la temperatura del punto de ebullición (por encima de 107 °C o 225 °F) y reducir la temperatura de congelación (por debajo de -35 °C o -32 °F). Cuando se incorporan aditivos a la formulación, el refrigerante puede proteger eficazmente contra la corrosión y la cavitación.
Tanto el propilenglicol como el etilenglicol se utilizan en formulaciones de refrigerantes. El propilenglicol es la elección de algunos usuarios porque, a diferencia del etilenglicol, no es tóxico ni se considera un material peligroso. Sin embargo, el etilenglicol se usa mucho más ampliamente, principalmente debido a sus mejores propiedades de transferencia de calor. Este artículo se centrará exclusivamente en el etilenglicol.
Las formulaciones de anticongelantes utilizadas como refrigerantes utilizan una variedad de aditivos organometálicos y orgánicos. Se utilizan para proteger los metales en el sistema de enfriamiento de la corrosión y cavitación, para controlar las incrustaciones, evitar la formación de espuma y mantener el pH. Los ejemplos comunes de aditivos incluyen varios fosfatos, borato de sodio, molibdato, silicato de sodio, sebacato de potasio y nitrato de sodio.
Al igual que los aditivos en un aceite lubricante, estos aditivos contribuirán a variar las concentraciones elementales de sodio, boro, potasio, silicio y fósforo en el refrigerante. Como se analizará con mayor detalle más adelante, las familias de elementos del sistema de aditivos refrigerantes ayudan a servir como marcadores, como el ADN, para identificar la contaminación por glicol en los aceites lubricantes.
Los tratamientos aditivos utilizados en las formulaciones de anticongelantes varían considerablemente entre los proveedores del mercado de repuestos y los OEM que proporcionan el llenado original de fábrica y ofrecen aditivos refrigerantes suplementarios (SCA). También existen marcadas diferencias geográficas en la química de los aditivos para refrigerantes, influenciadas por las regulaciones ambientales y la calidad del agua. Por ejemplo, los japoneses no utilizan silicatos, sino grandes cantidades de fosfatos.
Por el contrario, los europeos utilizan tratamientos aditivos de silicatos, benzoatos, boratos, nitritos y nitratos. Las formulaciones estadounidenses emplean silicatos, fosfatos y numerosos inhibidores orgánicos.
Cómo llega el glicol a los aceites de motor y otros lubricantes
El glicol puede filtrarse a los aceites de motor y otros aceites lubricantes de diversas formas. Estas incluyen:
- Sellos defectuosos o deteriorados
- Juntas de culata dañadas
- Pernos de cabeza mal apretados
- Culatas de cilindros térmicamente deformadas o agrietadas (desde baja carga de refrigerante hasta termostato atascado)
- Bloque o culata agrietados por refrigerante congelado
- Superficies de cabeza y bloque mal maquinadas
- Daños por corrosión en las camisas de los cilindros.
- Erosión por cavitación o corrosión de camisas de cilindros.
- Erosión electroquímica
- Núcleos del enfriador dañados o corroídos
- Fallo en el sello de la bomba de agua y bloqueo del orificio de drenado
Un importante fabricante de equipos originales de motores diésel ha estimado que el 53 por ciento de todas las fallas catastróficas del motor se deben a fugas de refrigerante. Para muchos motores diésel y de gas natural, el mayor riesgo de contaminación ocurre durante el tiempo que el motor no está funcionando. En tales casos, el enfriamiento del motor debido al uso intermitente puede provocar fugas internas asociadas con la fluencia térmica, como en las culatas, donde existe riesgo de recesión o movimiento de los sellos de las juntas.
Las presiones hidrostáticas más altas del refrigerante en relación con el sistema de aceite lubricante agravan el riesgo cuando el motor está en reposo. Esto puede provocar que el refrigerante entre en el lubricante.
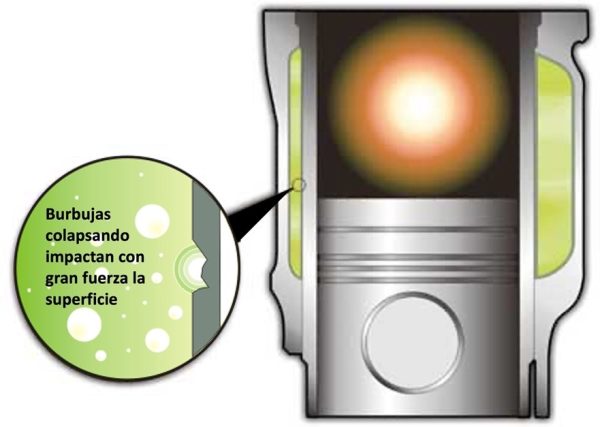
Otra fuente común de fugas en motores con camisas de cilindros húmedas está asociada con una perforación químico-mecánica de las camisas, promovida por la cavitación vaporosa. Esto ocurre cuando las camisas vibran violentamente (del lado de la carga) al ritmo del movimiento del pistón, la compresión y la combustión. Este movimiento hace que la porción de rarefacción de las ondas de presión forme regiones de presión negativa que nuclean burbujas de vapor (cavidades).
A medida que se enciende la cámara de combustión, las burbujas de vapor implosionan a la velocidad del sonido, provocando chorros de fluido y presiones en la superficie de hasta 60,000 psi. Esta energía localizada puede literalmente provocar pequeños agujeros en la película protectora de óxido de la pared del revestimiento, similar a la cavitación vaporosa en las bombas hidráulicas.
El daño puede verse impulsado aún más por el ataque químico del metal naciente expuesto durante este evento de cavitación. Con el tiempo, esto puede provocar la perforación del revestimiento y fugas (Figuras 1 y 2). Tenga en cuenta que muchos investigadores han postulado sobre el mecanismo exacto del daño. Si bien existen variaciones en la teoría, existe un consenso general en que el modo de falla se propaga mediante una combinación de ataque mecánico (cavitación localizada) y químico (corrosión del metal base expuesto).
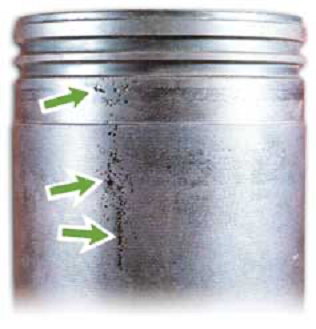
Se ha descubierto que ciertos aditivos utilizados en los aditivos suplementarios para refrigerante (SCA, por sus siglas en inglés), como el molibdato y el nitrito de sodio, inhiben drásticamente el progreso de la corrosión por cavitación. Si la película protectora de óxido del revestimiento se decapa debido a la energía de cavitación, el aditivo reforma una película de barrera para detener el progreso.
Sin embargo, la concentración de estos SCA introducidos en la mezcla de refrigerante es importante. Una carga insuficiente puede provocar picaduras aceleradas, mientras que una sobrecarga puede provocar gelificación del refrigerante, corrosión de la soldadura a base de plomo y otros problemas.
Daño causado por el aceite lubricante contaminado con glicol
El glicol es un villano en todos los aspectos cuando se mezcla con el aceite. El problema se intensifica por el agua en el refrigerante que ingresa al sistema de lubricación al mismo tiempo que el glicol. Los mecánicos encargados de reparar el daño que causa a menudo ven evidencia de contaminación por glicol.
Por ejemplo, los cojinetes principales y de biela pueden oscurecerse, con una apariencia casi de carbón, cuando el glicol ha contaminado el lubricante del cárter del motor diésel.
Debido al hecho de que el glicol no es soluble en aceite mineral y que las condiciones térmicas dentro de los motores conducen a la transformación del glicol y los aditivos del refrigerante en una variedad de otras sustancias químicas, no sorprende que haya tantas consecuencias degenerativas.
A continuación se analizan varios síntomas o efectos nocivos comunes y algunos no tan comunes de la fuga y contaminación con glicol.
Bloqueo hidráulico
Anteriormente se mencionó que los refrigerantes podrían corroer y erosionar las paredes de las camisas de los cilindros. Esto puede provocar perforaciones estenopeicas. Cuando un motor está en reposo, la cámara de combustión dentro del cilindro puede literalmente inundarse con refrigerante que pasa a través de estos orificios. Más tarde, al arrancar el motor, la falta de compresibilidad del refrigerante puede provocar un bloqueo hidráulico, como el bloqueo de una bomba. Dado que el refrigerante no tiene adónde ir, pueden ocurrir fallas en los cojinetes, anillos o el vástago del pistón.
Formación de ácido y daños en los cojinetes
En condiciones normales de funcionamiento, el etilenglicol se oxida para formar ácidos orgánicos como el ácido glicólico, el ácido oxálico, el ácido fórmico y el ácido carbónico. Normalmente, la velocidad de reacción se duplica por cada 10 ºC (18 °F) de temperatura. Estos ácidos contribuyen a los efectos secundarios y terciarios como se describe más adelante. Sin embargo, su sola presencia en el aceite lubricante puede poner en peligro los cojinetes y otras superficies de fricción.
Las condiciones corrosivas pueden picar las superficies revestidas de plomo/estaño de los cojinetes, promover la oxidación en las superficies de acero y hierro y manchar los metales con aleaciones de cobre, como el bronce y latón. Un estudio encontró que incluso una pequeña fuga de refrigerante en un motor o compresor de gas integral grande era suficiente para corroer gravemente las superficies de acero y cobre del motor.
Bolas de aceite y precipitación de aditivos
Chevron y otros investigadores han informado que cuando los refrigerantes a base de glicol envejecen térmicamente en los lubricantes del motor, se forman bolas de aceite, en gran parte debido a la reacción del glicol con los aditivos del aceite. Los aditivos involucrados incluyen sulfonatos, fenatos y ZDDP (Figura 3). Esto se evidencia aún más en un estudio realizado por la división de filtros Fleetguard de Cummins Engine que informó que se forman hasta 77 gramos de sólidos filtrables cuando el aceite se contamina con refrigerante que contiene etilenglicol en una concentración de solo dos por ciento (Figura 4).
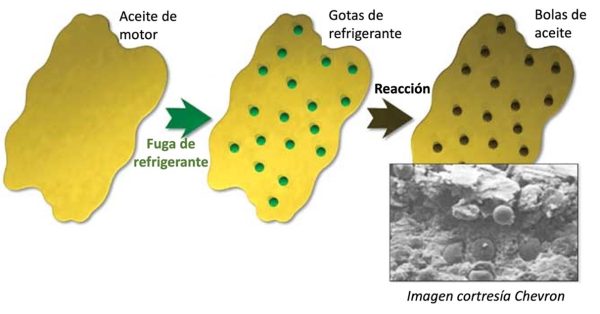
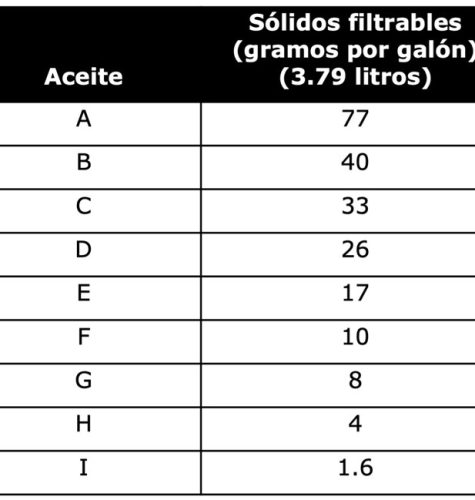
Pérdida de dispersancia y obstrucción del filtro
Los ácidos y el agua que se forman en el aceite en el motor como resultado de la contaminación con refrigerante a menudo alteran la dispersancia de hollín, incluso con una carga baja de hollín. Fleetguard informa que “el 75 por ciento de las quejas de los clientes sobre obstrucciones de filtros se relacionan con refrigerante o humedad en el cárter”. Una vez que el hollín comienza a aglomerarse y separarse del aceite, puede producirse una reacción en cadena de fallas asociadas, incluida la pérdida de protección antidesgaste, lodos pegajosos en las superficies del asiento de válvulas y depósitos carbonosos en las ranuras de los anillos, las superficies de las coronas de los pistones, los componentes del tren de válvulas y los conductos de aceite hacia los cojinetes, etc.
Si no se identifica el problema, el aceite se cambia a menudo sin lavar el sistema (descrito más adelante en la sección “Procedimiento para limpiar el glicol de los motores”). La reacción en cadena cobra entonces nueva vida a medida que los detergentes y dispersantes que llegan con el nuevo aceite de motor pueden movilizar los lodos y los depósitos. Luego, unos minutos después de un cambio de aceite y filtro, el filtro nuevo puede volver a obstruirse. A continuación se muestra el resumen de esta reacción en cadena:
- El refrigerante contamina al aceite del motor.
- Se forman ácidos y precipitantes a medida que reaccionan el glicol, los aditivos del refrigerante y del lubricante.
- Estos insolubles comienzan a obstruir el filtro de aceite.
- Al mismo tiempo, los ácidos y el agua interrumpen la dispersancia de hollín provocando una condición de aglomeración y separación. Se forman más lodos e insolubles.
- En este momento el filtro está obstruido con los subproductos de la transformación del glicol y el hollín aglomerado.
- Se cambian el aceite y el filtro (normalmente queda alrededor del 15 por ciento del aceite viejo, ya sea en el cárter de aceite o en las superficies del motor). El aceite nuevo (con detergentes y dispersantes) moviliza el hollín y los lodos, llevándolos al filtro.
- Una vez más, el filtro se obstruye (incluso con la fuga de refrigerante reparada).
Oxidación y cambio de viscosidad
Cuando el glicol contamina los aceites lubricantes, la viscosidad del aceite puede aumentar dramáticamente. Este problema es especialmente grave en los aceites de motor con alto contenido de aditivos. La alta viscosidad puede provocar un flujo inadecuado del lubricante hacia las superficies de fricción críticas. De la misma manera, el glicol y sus productos de reacción pueden promover agresivamente la oxidación del aceite base. Caterpillar informa que “la contaminación con refrigerante en las transmisiones y los fluidos hidráulicos generalmente se manifiesta como un aumento de la oxidación”.
Cómo se detecta el glicol en sitio
Los mecánicos, técnicos de lubricación y operadores calificados siempre están atentos a los signos reveladores de un lubricante contaminado con refrigerante. En flotas de camiones, autobuses y equipos móviles, la primera señal puede ser el humo blanco que sale de los tubos de escape de los motores diésel. O podría aparecer como un lodo brillante y adherente con la consistencia de mayonesa en un filtro usado durante un cambio de rutina. Quizás, como se mencionó anteriormente, la presión del aceite en un motor diésel aumenta inusualmente solo unos minutos después de un cambio de aceite y filtro.
Prueba de la gota en papel secante
Una prueba que ha ganado una atención especial es la prueba de la gota en papel secante. Apareció por primera vez en la escena de la lubricación como una prueba de campo que data aproximadamente de 1880. Resurgió en estudios realizados por Shell Oil en la década de 1950 y ahora nuevamente está captando la atención incluso de los laboratorios petroleros más sofisticados. Debido a su simplicidad, la prueba se realiza fácilmente en campo, aunque se requiere tiempo para que los resultados se desarrollen por completo.
La prueba se basa en el procedimiento establecido de cromatografía en papel e implica colocar un par de gotas de aceite usado en papel secante común (disponible en catálogos de suministros de laboratorio). Deje que las gotas penetren en el papel durante un par de horas. Si queda una mancha oscura o marrón en el centro después de que el aceite se absorbe hacia afuera, esto podría deberse a una alteración de la dispersancia y la aglomeración del hollín, una consecuencia común de la contaminación por glicol.
Una pasta negra y pegajosa con una periferia bien definida (borde afilado) es motivo de gran preocupación. Muy a menudo se desarrolla un anillo de hollín alrededor de un centro amarillo/marrón cuando hay glicol presente. La Figura 5 muestra este patrón único en pruebas de gota desarrolladas a partir de aceite de motor diésel usado envejecido térmicamente en presencia de concentraciones variables de glicol y agua.

Prueba de membrana
Al pasar una pequeña cantidad de aceite diluido en solvente a través de una membrana de un micrón, a menudo verá lodos, aditivos precipitados y otros contaminantes insolubles presentes en la superficie de la membrana. El uso de un microscopio portátil de 30 aumentos puede ayudar en el examen del material presente. Varios proveedores ofrecen kits de prueba de membrana de campo.
Tenga en cuenta que si el tamaño de los poros de la membrana es demasiado grande (>3 micrones), gran parte del lodo y los insolubles pasarán a través de ella. Se recomienda el uso de una membrana de 0.45 micrones. También evite el uso de solventes que corren el riesgo de disolver los óxidos condensados y otros materiales objetivo del aceite contaminado con glicol.
Método del reactivo de Schiff
El método del reactivo de Schiff (ASTM D2982) es un método colorimétrico para detectar trazas de glicol en aceites lubricantes. En este método, se introduce en el aceite una solución de ácidos clorhídrico (HCl) y ácido iódico (HIO3) para oxidar cualquier glicol que pueda estar presente. La reacción produce un aldehído, que a su vez reacciona con el reactivo de Schiff, produciendo un cambio de color positivo de incoloro a rosa/púrpura: cuanto más oscuro es el color, más glicol está presente. Hay varios proveedores de kits de prueba de reactivos de Schiff.
Tenga en cuenta que con frecuencia se han reportado falsos positivos debido a la presencia de trazas de impurezas en aceites nuevos. Chevron ha documentado que este efecto se debe a trazas de residuos de glicol en el aceite nuevo procedente de la fabricación de aditivos del lubricante. Sin embargo, otros han informado que también podría deberse a los aldehídos y cetonas de la refinación del aceite base, a pesar de los datos publicados por Chevron. Esto tiene sentido porque el aceite nuevo puede mostrar un resultado positivo con el reactivo de Schiff antes de oxidarse con HIO3.
En otro caso, el laboratorio de análisis de aceite de Cummins informó que realizó pruebas sucesivas en una sola muestra de aceite usado que arrojaron resultados positivos, negativos e indeterminados. Debido a la inestabilidad del etilenglicol en los aceites lubricantes a altas temperaturas del cárter, se convierte rápidamente en ácidos y otros compuestos. Debido a que este y otros métodos de prueba que se analizan a continuación dependen de la presencia de glicol molecular, cualquier descomposición química o térmica del refrigerante puede hacer que la prueba del reactivo de Schiff no sea confiable. Las pruebas de laboratorio realizadas por Cummins muestran que “un aceite que contiene cuatro por ciento de refrigerante retendrá sólo el 10 por ciento del glicol originalmente presente al calentarlo a 93 °C (200 °F) durante ocho horas”. Sin embargo, otros signos reveladores de contaminación por glicol permanecen en el aceite.
Cómo se detecta el glicol en el laboratorio
Los laboratorios comerciales de análisis de aceite implementan varios métodos e instrumentos de prueba diferentes para detectar y medir las concentraciones de glicol en lubricantes usados. La efectividad de estas técnicas varía considerablemente y por esta razón se justifica una discusión que las compare y contraste. Con este fin, a continuación se analizan los tres métodos más comunes utilizados por los laboratorios de análisis de aceite:
Espectrometría infrarroja por transformada de Fourier (FTIR)
Muchos laboratorios de análisis de aceite utilizan este procedimiento para analizar las propiedades moleculares del aceite usado de forma rutinaria. La revista Machinery Lubrication ha cubierto la espectrometría infrarroja en varios artículos. Las propiedades objetivo comunes detectadas y medidas con FTIR incluyen concentración de hollín, contaminación con agua, dilución por combustible, oxidación, nitración y sulfatación. Muchos laboratorios también informan sobre bandas de absorción comúnmente asociadas con el etilenglicol.
Si bien tiene mucho mérito incluir el glicol entre las diversas propiedades reportadas por el infrarrojo, también existen interferencias y límites de sensibilidad más bajos que los laboratorios y los usuarios deben tenerlos en cuenta. Las interferencias se relacionan con otras propiedades y contaminantes que comparten regiones de absorción espectral comunes con el glicol.
Por ejemplo, la banda más fuerte del glicol, una región amplia de alrededor de 3450 cm-1 correspondiente al grupo funcional OH, también está cohabitada por agua y otros alcoholes que tienen un grupo funcional similar. Debido a que el agua se mezcla con anticongelante (etilenglicol) para formar el refrigerante, a menudo es imposible hacer la distinción.
Sin embargo, existe una banda más exclusiva para el etilenglicol en 1070-1030 cm-1 correspondiente al grupo funcional CO, que se usa comúnmente porque hay menos bandas superpuestas de otros contaminantes del aceite y subproductos de degradación (Figura 6). El principal riesgo en esta región está asociado con ciertos aditivos (como el sulfonato de bario) y compuestos oxigenados (éteres, lactonas y alcoholes) provenientes del aceite base y la degradación de aditivos.
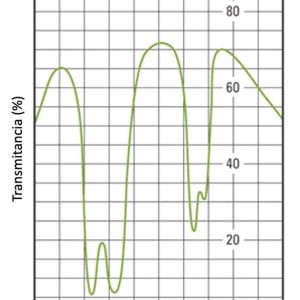
Al igual que con la contaminación con agua, la capacidad del FTIR para detectar concentraciones de glicol por debajo de 1000 ppm es muy limitada. Al igual que la prueba del reactivo de Schiff, FTIR también se basa en la presencia de glicol molecular. Sin embargo, debido a que el glicol puede degradarse química y térmicamente con rapidez como se mencionó anteriormente, su presencia en el aceite usado puede quedar completamente disimulada. En este caso, para que FTIR tenga éxito, un analista calificado necesitaría reconocer las bandas de absorción de los distintos productos de transformación del glicol.
Cromatografía de gases
Quizás no haya existido ningún método analítico que haya tenido mayor impacto en el análisis del aceite que la cromatografía de gases (GC, por sus siglas en inglés). En el ámbito del análisis de aceite usado, se considera ampliamente que es el método más preciso para detectar y medir el glicol y el combustible, aunque es más costoso y requiere más tiempo que las alternativas. El procedimiento de GC más comúnmente utilizado para el análisis de glicol es ASTM 4291, “Método de prueba estándar para trazas de etilenglicol en aceite de motor usado” (Figura 7).
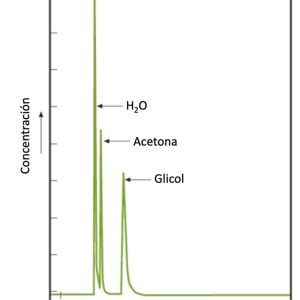
El procedimiento implica primero extraer el glicol del aceite utilizando agua y luego centrifugar. Luego se retira el extracto y se inyecta en el GC, donde los compuestos polares se separan y se detectan en un cromatograma.
Tenga en cuenta que Chevron ha informado que este procedimiento es tan sensible que puede dar indicaciones falsas de paso de refrigerante. Esto se debe a la presencia de subproductos de la fabricación de aditivos y a la contaminación con combustible que pueden dejar trazas de glicol en aceites nuevos y usados. Es útil realizar una referencia de lubricantes nuevos utilizando GC antes de implementar el método con aceites usados.
El principal inconveniente de la detección de glicol por GC es que el glicol puede descomponerse rápidamente en ácidos, aldehídos y ésteres, lo que puede dar como resultado un falso negativo o una subestimación de la concentración real de glicol y derivados de glicol. Esto también es válido para el reactivo de Schiff y las pruebas por FTIR.
Análisis de elementos en filtros y aceites usados
El análisis de elementos mediante espectrometría de emisión por plasma inductivamente acoplada (ICP, por sus siglas en inglés) o mediante espectrometría de emisión por electrodo y disco giratorio (RDE, por sus siglas en inglés) de chispa de arco ha sido el pilar del laboratorio de análisis de aceite durante años.
El uso del análisis de elementos es quizás el método más confiable para verificar que el glicol o sus derivados hayan contaminado un lubricante. El procedimiento es clave para detectar la presencia de aditivos organometálicos del anticongelante que se mezclan con un lubricante al contaminarse. Estos aditivos son señales reveladoras de que el aceite ha sido contaminado con una dosis de anticongelante.
Por ejemplo, el sodio, el boro, el potasio y el silicio se encuentran comúnmente en las formulaciones de anticongelantes (Figura 8). Para saber específicamente qué elementos de aditivos y sus concentraciones se encuentran en el anticongelante nuevo o usado (incluidas las mezclas que contienen SCA), se podría analizar fácilmente una muestra de anticongelante nuevo de la misma manera que se hace con los aceites usados.
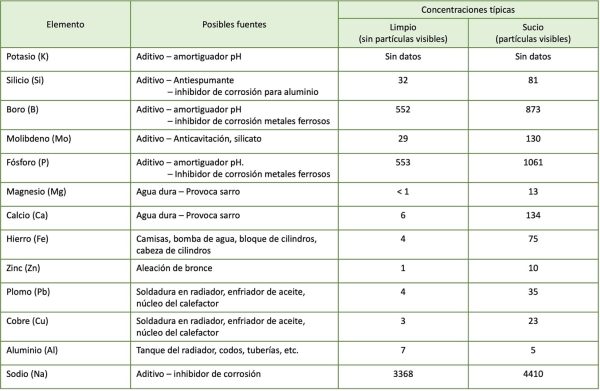
De los diferentes compuestos que componen los aditivos del anticongelante, los de sodio y potasio son los más estables, aunque existe el riesgo de que precipiten y sean eliminados por el filtro. El boro presenta un riesgo de evaporarse a temperaturas típicas del cárter del motor, mientras que el silicio de una fuga de refrigerante puede confundirse con la entrada de suciedad o un aditivo antiespumante del aceite.
Citando nuevamente el informe de la división Fleetguard de Cummins Engine, “las muestras de aceite a veces tendrán varios cientos de partes por millón de sodio, pero no habrá humedad ni glicol presente. La cantidad de sodio indica que se ha filtrado al menos un galón de refrigerante en el cárter, pero no hay señales de ello (aparte del sodio)”. Cummins resume diciendo: “Nuestra experiencia es que el indicador más confiable de fuga de refrigerante es el nivel de sodio de las cenizas del papel del filtro seguido del nivel de sodio en el aceite”.
Debido a la pérdida de sodio por el consumo de aceite o por el sodio insoluble capturado por el filtro de aceite (80 a 90 por ciento del sodio total que se ha filtrado al cárter en algunos casos), un aumento de sodio en el aceite de tan sólo 50 ppm puede significar que se ha filtrado hasta un galón de refrigerante en un sistema de aceite lubricante de 10 galones (38 litros).
Si se sospecha que el residuo en un filtro usado son aditivos del refrigerante, se podría realizar un análisis para determinar el sodio de la siguiente manera:
- Usando un baño ultrasónico, transfiera las partículas de un trozo del medio filtrante a un solvente como queroseno o alcohol isopropílico.
- Use un método de digestión ácida para determinar los elementos de aditivos (sodio, etc.) en el residuo del filtro, o
- Transfiera el residuo a una membrana filtrante y analice los materiales mediante espectrometría de fluorescencia de rayos X (o SEM/EDX, PIXE), o
- Transfiera el residuo a un portaobjetos de vidrio y analice las partículas mediante microscopía química.
Cuando se observa un aumento repentino del sodio, el analista debe conocer otras fuentes comunes. Estos incluyen: sal y agua salada, grasa, suciedad, cenizas en el aire, hidróxido de sodio, etc. Por esta razón, es posible que se necesiten otros miembros de la familia de aditivos para refrigerantes para confirmar que el contaminante es anticongelante, como boro, potasio, silicio y fósforo, teniendo en cuenta que algunos de estos elementos también pueden ser aditivos del aceite.
Límites y alarmas
Establecer alarmas y límites para el glicol es difícil debido a los diferentes instrumentos de análisis de aceite que se utilizan y los estados transitorios del glicol en el lubricante. En la medida en que el analista pueda confirmar una fuga de refrigerante, por pequeña que sea, el asunto es motivo de grave preocupación. Sin embargo, pueden producirse falsos positivos si los límites de alarma se establecen demasiado bajos por los motivos comentados anteriormente. Del mismo modo, si las alarmas se configuran demasiado altas, los niveles reales de fuga de refrigerante podrían ser varias veces superiores a las cantidades medidas y el motor podría estar peligrosamente cerca de una falla catastrófica.
En el caso de que se produzcan falsos positivos como resultado de la nueva química del aceite asociada con la fabricación de aditivos y la refinación del aceite base, las interferencias que causan estos falsos positivos a menudo se queman durante el servicio. Por lo tanto, un aceite de referencia nuevo o un aceite puesto en servicio por un corto período de tiempo puede dar positivo en glicol y luego dar negativo.
Cuando se produce un falso positivo debido a la química del aceite en laboratorios que informan el resultado de una prueba de glicol (reactivo de Schiff, FTIR y GC), normalmente colocan una indicación positiva en el informe. Sin embargo, basándose en la revisión de otros indicadores (incluidos los elementos de aditivos del refrigerante), como se analizó anteriormente, el analista que comenta los datos del análisis de aceite debe enfatizar que el resultado positivo de glicol no es motivo de preocupación.
Algunos laboratorios utilizan el enfoque de informar la contaminación con refrigerante o anticongelante en lugar de glicol para eliminar esta posible causa de preocupación injustificada. El mismo principio se aplica en el caso de una prueba de glicol negativa, donde su presencia queda disfrazada por el hecho de que se ha convertido en subproductos.
Al observar otros indicadores, como el sodio y el potasio, el analista debería informar un resultado positivo de contaminación con refrigerante a pesar de que no se detectó glicol real. En tales casos, el analista de laboratorio determina la entrada de contaminación basándose en la revisión de múltiples factores.
En general, el glicol por encima de 200 ppm en la mayoría de los casos se considera reportable. Los niveles superiores a 400 ppm deben considerarse significativos y los niveles de hasta 1000 ppm deben considerarse críticos.
Procedimiento para limpiar el glicol de los motores
Un procedimiento de lavado propuesto por una importante compañía petrolera para eliminar el glicol de las superficies internas del motor implica el uso de butoxietanol (nombre comercial Butyl Cellosolve, Union Carbide). El procedimiento de lavado para condiciones de menos del cinco por ciento de contaminación con glicol se resume a continuación:
- Drene el aceite del compartimiento y de todas las líneas y componentes.
- Instale elementos filtrantes nuevos.
- Mezcle un aceite mineral ISO VG 32 R&O 50/50 con Butyl Cellosolve.
- Utilice la mezcla para lavar turbulentamente (utilizando una bomba externa instalada en la línea de suministro del turbocompresor u otro método de bombeo adecuado) las superficies internas con un flujo y volumen amplios durante una hora a una temperatura no inferior a 21 °C (70 °F).
- Drene el sistema por completo, limpie el cárter y sustituya los filtros.
- Repita los pasos 2 a 5, utilizando una mezcla de 60 por ciento de R&O 32 y 40 por ciento de queroseno.
- Retire e inspeccione todos los cojinetes principales, muñones y otras superficies del motor.
- Retire la bomba externa y rellene con el lubricante correcto. Sustituya el filtro.
- Monitoree el motor cuidadosamente hasta que todas las condiciones se estabilicen.
Referencias:
Anderson, Daniel P., Lucas, Malte, and Lynch, Brian K. – Spectro Incorporated. “Diesel Engine Coolant Analysis.”
Anonymous (Phillips 66). Cleaning Procedures to be Used When Lube Oil Systems are Contaminated with Ethylene Glycol.
Annual Book of ASTM Standards, 2000, Section Five, Petroleum Products, Lubricants, and Fossil Fuels.
Beal, Roy E. (1993). Engine Coolant Testing, Third Volume, ASTM.
Birke, Mike – Southwest Research Institute (1999). “New Challenges in Detecting Glycol Contamination with New Anti-Freeze Additive Formulations,” Practicing Oil Analysis ‘99 Conference Proceedings.
Booser, Richard E. (1997). Tribology Data Handbook, CRC Press.
Caterpillar, various S·O·SSM Services publications.
Chevron Technical Bulletin LTB-03 (1993). “Avoiding False Coolant Leak Indications with Lubricating Oil Analysis.”
Coates, J.P., and Setti, L.C. (1985). Oils, Lubricants, and Petroleum Products, Characterization and Infrared Spectra. DEKKER.
Hudgens, R. D., and Feldhaus, L. B. – Fleetguard, Inc., (1978). “Diesel Engine Lube Filter Life Related to Oil Chemistry,” International Fuels & Lubricants Meeting, Society of Automotive Engineers, Toronto.
Mathys, Mark – Butler Machinery, Caterpillar (1999). “Coolant and Coolant Analysis,” Seminar Course Materials.
Peterson, F.S. (1979). Lubrication – Chromatography. Texaco, Vol. 65.
Staff editor. (1999). “Schiff’s Reagent Glycol Test – Controlling False Positives,” Practicing Oil Analysis magazine, November-December.