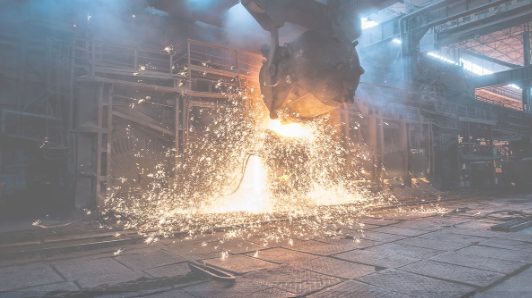
Monitoreo de condiciones, control de contaminación, excelencia en lubricación y confiabilidad de máquinas son palabras clave que a menudo se usan en exceso y se malinterpretan. Estas palabras son mucho más relevantes y amplias en el contexto empresarial actual, pero solo un puñado de organizaciones a nivel mundial pueden implementar estos conceptos de manera simultánea y exitosa, manteniendo al mismo tiempo la sustentabilidad.
Este proceso no siempre es fácil, pero las organizaciones pueden lograrlo mediante un esfuerzo intenso, reflexivo y un trabajo colectivo; los éxitos y beneficios resultantes están ampliamente documentados.
Por ejemplo, examinemos un caso de estudio con JR Simplot, una empresa privada de procesamiento de alimentos y agricultura que posee y opera una de las minas de fosfato de alto grado más grandes del oeste de los Estados Unidos.
Se necesitaba una gran flota, incluidos camiones de transporte, para mantener el exigente programa de operaciones mineras. En promedio, cada motor debía reconstruirse cada 15,000 horas de funcionamiento, con un costo de hasta 160,000 dólares por motor. Esto consumía casi el 70% del presupuesto total de mantenimiento de la empresa. El equipo reconoció que las malas prácticas de lubricación y los errores humanos eran las principales causas de las fallas de sus motores y decidió realizar un cambio.
Al priorizar las prácticas e implementar estándares de gestión de lubricación adecuados, el equipo aumentó las horas de funcionamiento promedio entre reconstrucciones de motores en un 37 % a más de 18,000 horas, lo que generó una reducción de costos anualizada de más de USD $15,000. Actualmente, el equipo está trabajando para aumentar el tiempo promedio entre reconstrucciones a casi 25,000 horas.
Sin embargo, a pesar de que hay muchos casos de estudio exitosos documentados como este, se ha observado que está surgiendo un nuevo patrón de pensamiento. Ahora, parece que muchas organizaciones y líderes están más interesados en hablar y promover la extensión de la vida útil de los componentes y la práctica de la gestión de activos y el mantenimiento proactivo en diferentes plataformas que en implementar los cambios necesarios.
Esta mentalidad de exceso de confianza en los fundamentos, pero sin acciones que los respalden, puede llevarnos a un escenario moderno de “contar los pollos antes de que nazcan”, lo que significa que es más probable que se produzcan errores, poniendo en riesgo el futuro de una planta que se transforma en una instalación de clase mundial.
El estado alarmante de una acería
Hace unos años, tuve la oportunidad de visitar una antigua fábrica de acero y alambrón en la India para explorar posibles oportunidades comerciales.
Mi colega y yo visitamos el lugar en un día normal y nos quedamos allí durante toda la jornada laboral. Debido a la ubicación de la planta en la India, es importante señalar que nos encontramos con un ambiente extremadamente caluroso, húmedo y polvoriento. Recorrimos las instalaciones, interactuamos con gerentes, supervisores y técnicos, y recolectamos algunas muestras de aceite utilizando accesorios y botellas de muestreo adecuados.
Lo que descubrimos fue una situación muy diferente a la que esperábamos. Descubrimos que:
- El almacenamiento de los tambores de aceite era inadecuado
- Había capas gruesas de suciedad en la superficie de los tambores.
- Respiradores desecantes en cantidad insuficiente, tamaño insuficiente y agotados
- Sin etiquetas de identificación
- El almacenamiento, manipulación y aplicación de aceite se realizaba en una atmósfera abierta, utilizando bombas manuales y pequeñas latas.
- Se observaba suciedad en todas partes: pisos, tanques de aceite hidráulico, respiraderos, área de almacenamiento de piezas de repuesto.
- No existía ningún proceso de limpieza establecido
Además, a pesar de nuestras reiteradas solicitudes, la fábrica no nos facilitó ningún dato anterior. Esta renuencia a compartir datos puede deberse a:
- Falta de datos
- Falta de consentimiento para generarlos
- Simplemente, no existía un proceso de recopilación de datos
Estos datos históricos eran fundamentales para analizar y comprender el nivel de limpieza del fluido con el que operaban las máquinas y cómo llegaron a ese estado. Además, serían necesarios para ayudar a orientar las estrategias y los planes de acción futuros para la remediación.
Recolección, prueba y análisis de las muestras
Las muestras de aceite que recogimos se analizaron al día siguiente en nuestro propio laboratorio. Las pruebas que realizamos incluyeron:
- Prueba de membrana con aumento de 50X
- Conteo de partículas con un contador de partículas láser estándar
- Análisis de desgaste de metales mediante espectrometría de plasma inductivamente acoplada (ICP, por sus siglas en inglés)
Las membranas se prepararon con un microscopio manual y las pruebas de conteo de partículas se realizaron con los procedimientos adecuados dentro del laboratorio. Aunque no se consideró crucial en este escenario, se realizó el análisis de metales de desgaste para identificar las partículas de desgaste en las muestras de aceite. La prueba reveló que, si bien había aditivos metálicos, como zinc, calcio y fósforo, no encontramos un contenido excesivo de metales de desgaste.
Una mirada cercana a los sistemas de lubricación
Al observar los sistemas de lubricación, se encontró que las líneas de alimentación de aceite estaban equipadas con filtros absolutos de 25 y 10 micrones y no había filtros en las líneas de retorno. En los sistemas hidráulicos, la línea de alimentación estaba equipada con un filtro absoluto de 5 micrones y la línea de retorno con un filtro absoluto de 10 micrones.
Revisando los tanques de relleno y los sistemas de lubricación, descubrimos que la fábrica todavía utilizaba los estándares del sistema NAS, que en gran medida se han eliminado de todas las industrias en favor de los estándares ISO. A pesar de haberse vuelto obsoleto, el sistema NAS aún debería haber podido promover cierto nivel de limpieza.
Sin embargo, cuando consultamos los datos del conteo de partículas, se confirmaron nuestras sospechas: los aceites estaban extremadamente sucios y contaminados.
Varios de los sistemas hidráulicos operaban con un nivel de limpieza NAS 6 (equivalente a ISO 17/15/12), y otros operaban con NAS 9 (equivalente a ISO 20/18/15) e incluso NAS 12 (equivalente a ISO 23/21/18).
Los aceites lubricantes de la fábrica también contenían un alto contenido de humedad: alrededor de 2,000 partes por millón (ppm), mientras que el máximo estándar de la industria es de 200 ppm.
Esta información nos permitió llegar a la conclusión de que la mayoría de sus problemas de contaminación se producían debido a errores humanos y prácticas inadecuadas durante el almacenamiento y la manipulación del lubricante.
Fin de las conversaciones
Una vez finalizadas las pruebas y los análisis, nos reunimos con el equipo directivo de la planta para revisar los datos y los hallazgos. Durante esta reunión, el equipo directivo reveló cuáles eran sus requisitos de limpieza interna:
- El nivel de limpieza del aceite del sistema hidráulico debe ser menor o igual a NAS 3 (equivalente a ISO 14/12/9)
- El contenido de humedad en el aceite de lubricación debe ser menor o igual a 200 ppm
Esto fue absolutamente impactante. Cuando se presentaron nuestros hallazgos, que mostraban las graves discrepancias entre las expectativas de limpieza de las instalaciones y la realidad, el equipo de gestión de la fábrica se negó a ofrecer ninguna explicación y se reusó a discutir el asunto más a fondo antes de finalizar abruptamente la reunión.
No hace falta decir que todo nuestro entusiasmo y actividades iniciales relacionadas con descubrir una oportunidad de negocio y crear una propuesta comercial fueron rápidamente descartadas.
Si bien no conocemos bien los procesos de cada industria, hay algo que es constante: la contaminación puede afectar a todas las instalaciones si no se toman las precauciones adecuadas y la comprensión de los principios no se correlaciona con una aplicación adecuada. Confiar solo en conocer los principios, pero sin aplicar el esfuerzo y la acción adecuados, conduce a un mayor riesgo de error humano, lo que pone en peligro la capacidad de la planta de transformarse en una instalación de clase mundial.
Reflexión
Después de reflexionar detenidamente sobre mi experiencia, estas fueron varias razones por las que se hace cada vez más difícil mantener una relación comercial con esta acería:
- Desde el principio hubo falta de cooperación y comunicación adecuadas por parte de la dirección de la fábrica.
- No se observó un enfoque agresivo hacia el mantenimiento proactivo.
- El personal y la maquinaria no estaban preparados ni equipados para lograr un nivel de limpieza adecuado.
- Todas las actividades de lubricación se realizaban en un ambiente expuesto y sucio.
- No existía ningún proceso establecido para manipular, almacenar y dispensar adecuadamente los aceites.
- Había un enfoque contradictorio hacia las normas: se establecen requisitos estrictos, pero con prácticas extremadamente deficientes.
- Los directivos de la fábrica estaban conscientes de la necesidad de eliminar los contaminantes de los sistemas, pero ignoraban los diversos procedimientos y técnicas necesarios para evitar que los contaminantes los invadieran.
- Los filtros de aceite no protegían adecuadamente.
- Las mangueras y tuberías que transportan fluidos estaban abiertas.
- No existían procesos para limpiar y proteger adecuadamente las mangueras nuevas.
- No se contaba con suficientes filtros respiradores de la eficiencia adecuada.
- El sistema de filtración actual era insuficiente para reducir el valor de NAS 9 al nivel deseado de NAS 3, incluso si se seguían los procedimientos adecuados.
- El tamaño de partícula y eficiencia del filtro de aceite estaban seleccionados incorrectamente en varias de las ubicaciones.
- No existía ningún proceso para monitorear o recopilar regularmente datos sobre la limpieza de todas las muestras de aceite en las instalaciones.
Si bien estas razones pueden dificultar una mayor participación de la empresa, esta acería, sin saberlo, está ansiosa por encontrar un catalizador de cambio. Podría bastar con que una sola persona con el enfoque de gestión del cambio adecuado desencadene una serie de acontecimientos positivos. Se trata de una cuestión de cultura, y esta comienza con el liderazgo.
Para cambiar la mentalidad colectiva de quienes actualmente no están motivados para reconocer la oportunidad, necesitan descubrir “qué hay en esto para ellos”. Somos criaturas de hábitos y solo cambiamos si hay una razón convincente. Hasta entonces, el “statu quo” persistirá y la fábrica de acero y las personas que trabajan en ella sufrirán tiempos de inactividad no programados y oportunidades perdidas.
Pensando en el futuro
Recuerdo que, a principios de la década de 2000, mi laboratorio recibía, procesaba y analizaba un promedio de 100 muestras por mes. Hoy, este mismo laboratorio procesa casi 5,000 muestras por mes y los miembros del equipo trabajan en dos turnos para completar la carga de trabajo. Este ejemplo es un rayo de esperanza en medio de condiciones deplorables, como las de la acería que visité.
En el futuro, la capacitación debe ser una prioridad, no solo para los miembros del equipo en la planta, sino también para la alta gerencia, que es responsable de diseñar e impulsar la implementación de nuevos programas de mantenimiento y lubricación. Por eso, la capacitación no solo debe incluir prácticas de lubricación adecuadas, sino también transformación cultural y gestión del cambio, que se impulsa desde arriba hacia abajo.
Cuando el esfuerzo intenso y reflexivo se combina con el trabajo colectivo y la acción intencional, se logran los beneficios de un programa de calidad y las historias de éxito comienzan a superar a los fracasos.
Debasish Mukherjee. Traducción por Roberto Trujillo Corona, Noria Latín América