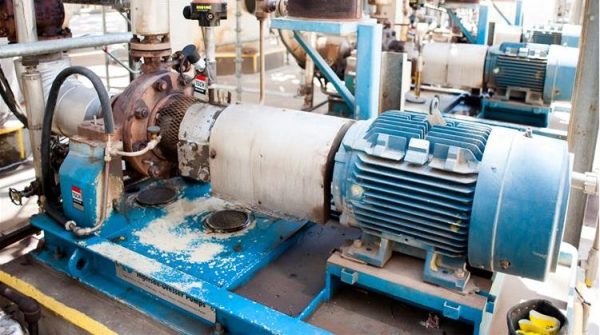
Cuando la mayoría de nosotros se refiere a inspecciones, estamos pensando en inspeccionar en forma rutinaria máquinas en funcionamiento como, por ejemplo, en los recorridos diarios. Indiscutiblemente, este tipo de inspección con la máquina operando es fundamental para el monitoreo de condición de la maquinaria, pero hay otros tipos de inspecciones que también son importantes.
En el mejor de los casos, la inspección busca y encuentra los «precursores» de la falla, también conocidos como causas raíz. Este es el principal objetivo, seguro. A continuación, la inspección debe detectar aquellas condiciones de falla incipiente (detectar la falla lo más temprano posible) que pueden ser tan difíciles de detectar con nuestros sentidos, como lo es el sonido que produce la «caída de un alfiler».
El periodo de tiempo para realizar la inspección debe abarcar desde la cuna hasta la tumba. He resaltado en artículos anteriores que la Inspección 2.0 es un estado continuo de vigilancia.
El momento en que baja la guardia es exactamente el momento en que el eterno Sr. Murphy hace su entrada. Para defenderse de los riesgos y la vulnerabilidad, la organización intensa en confiabilidad realiza inspecciones en varias condiciones.
Inspección de repuestos, almacenamiento y maquinaria de reserva
Mantener las piezas de repuesto y la maquinaria de reserva en una condición excelente y saludable puede ser una tarea abrumadora, por decir lo menos. A menudo, la maquinaria y los repuestos críticos deben almacenarse durante años en una condición de «listo para funcionar».
Se han publicado varios artículos en la revista Machinery Lubrication sobre mantenimiento de maquinaria inactiva y de reserva. Este es un asunto serio para proteger su inversión y, lo que es más importante, para mantener una buena disponibilidad.
Sin lugar a duda, el enemigo principal para este tipo de maquinaria es el agua que se condensa, se asienta, forma charcos y corroe. Por lo tanto, desde el punto de vista de la inspección, ubicar puntos de entrada de agua e identificar su presencia es la mayor prioridad.
La capacidad de los aditivos de un lubricante para eliminar la corrosión se neutraliza en gran medida cuando estos no están circulando. Por varias razones, el agua es principalmente el azote de las máquinas almacenadas e inactivas y de las partes de repuesto.
Muchos tipos de máquinas se llenan completamente con aceite durante el almacenamiento para minimizar el intercambio de aire entre el espacio superior y la atmósfera. Esto también mantiene las superficies internas humedecidas con aceite, que de lo contrario estarían expuestas a la condensación y otros contaminantes atmosféricos.
En las cajas de engranajes, estas superficies incluyen todos los rodamientos, ejes y engranajes. Debido a las fuerzas hidrostáticas, estas máquinas llenas con aceite son propensas a producir fugas con el tiempo, por lo regular a través de los empaques y sellos de labio. Cualquier evidencia de fugas, desde humedad hasta charcos de aceite, debe anotarse y corregirse.
Además, verifique para asegurarse que:
- Todos los ejes y acoplamientos aún tienen recubrimientos protectores en su sitio.
- Las tuberías de lubricación y los componentes están herméticamente sellados (tapas, tapones, etc.), y las escotillas y las tapas bien cerradas.
- Los depósitos y tanques están limpios y libres de agua y lodos.
- Los ejes deben ser rotados con frecuencia.
- La suciedad y otros residuos no se han acumulado en las superficies exteriores.
- Las refacciones y los componentes pequeños están sellados (por ejemplo, con láminas/bolsas de plástico) y están en posición correcta (por ejemplo, vertical vs. horizontal), incluidos los cilindros hidráulicos, rodamientos, cajas de engranajes, bombas, etc.
- Las áreas de almacenamiento no deben exponer las refacciones, los ensamblajes y las máquinas almacenadas a los efectos de las vibraciones.
Inspección de puesta en marcha
Con frecuencia se dice que el momento en que una maquinaria es más propensa a fallar es justo después de la puesta en marcha, reparaciones mayores o el desmontaje. Estos acontecimientos son condiciones críticas de cambio, y el cambio presenta riesgos desde el punto de vista de la confiabilidad de la maquinaria.
También está el factor humano. Cuando los operadores, mecánicos y trabajadores de mantenimiento modifican una máquina, regularmente es difícil devolverla con precisión al estado operativo anterior. Cualquier tipo de evento intrusivo, a pesar de todas las buenas intenciones, presenta peligro. Antes de desarmar cualquier máquina, debe haber una necesidad irremediable. Analice primero todas las opciones no intrusivas.
Una excelente medida para evitar el riesgo de la puesta en marcha es una inspección exhaustiva y continua junto con el monitoreo de condición. Respete todas las áreas potenciales de peligro. Inspeccione tantos de estos peligros como sea posible hasta que se restablezca la estabilidad operativa. Estos incluyen:
- Temperatura (todas las zonas críticas, componentes y superficies)
- Vibración
- Balanceo y alineación
- Lecturas de los medidores (temperatura, presión, vacío, flujo, velocidad, proximidad, etc.)
- Presión diferencial del filtro
- Acumulación de partículas en los tapones magnéticos
- Nivel de aceite, color y claridad en todos los visores o mirillas
- Fugas
No pase por alto la necesidad de tomar muestras con frecuencia y verifique los niveles de limpieza y de partículas de desgaste. Normalmente, no es necesario que un laboratorio realice estas pruebas. Existen diferentes pruebas de campo para hacer un trabajo adecuado, incluidas las pruebas de filtración por membrana, el método Durban y la prueba de la gota de aceite.
Inspección durante la operación
He cubierto este tema en los últimos artículos de Machinery Lubrication. Sí, hay una diferencia entre la Inspección 2.0 y las prácticas convencionales. Un mejor estado de confiabilidad exige un mejor estado de participación del operador. No se trata solo de mirar rápidamente una máquina, sino de examinar la máquina con frecuencia y a fondo con un ojo experto y bien educado.
Para toda la maquinaria considerada como «mal actor» bajo su cuidado, existe una necesidad crítica de vigilancia por la Inspección 2.0. Estas son las máquinas que son trabajadas más allá de sus límites de diseño. Son los principales responsables de la interrupción del proceso y la pérdida de producción, así como del 80 por ciento de los costos de tiempo de inactividad y reparación.
Inspección durante los paros
Las inspecciones durante los paros le permiten acceder a las condiciones de la máquina y las superficies de fricción difíciles de alcanzar. Por supuesto, como se mencionó anteriormente, debe evitar todas las intervenciones innecesarias que puedan ocasionar una causa raíz de falla.
Dicho esto, a menudo se puede acceder de forma segura a los dientes de los engranajes, paredes de los depósitos, acoplamientos, sellos de ejes, visores de sedimentos del fondo y agua (BS&W, por sus siglas en inglés), tapones magnéticos, tolerancias en los rodamientos, etc., para un breve vistazo de la condición. Las cámaras, incluidos los boroscopios, pueden ser muy útiles.
Inspección durante las reparaciones
Las inspecciones durante la reparación y reconstrucción representan una oportunidad valiosa que, con frecuencia, no se explota. Qué maravillosa oportunidad de aprendizaje puede ser una falla. Esto no solo implica lo que falló y por qué falló, sino también lo que puede observar mientras realiza la autopsia. Considere lo siguiente:
¿Qué le enseñan los talleres de reconstrucción sobre las causas de falla de los motores eléctricos, cilindros, cajas de engranajes, bombas, etc.? ¿Recibe reportes de inspección de estas empresas de reconstrucción sobre lo que encuentran cuando abren sus máquinas dañadas? ¿Le orientan sobre la prevención? Si es así, ¿cómo se usa actualmente este conocimiento (retroalimentación) para mejorar sus prácticas actuales de mantenimiento?
¿Pospone cuando es necesario realizar autopsias de fallas? Una vez que la operación ha sido restaurada en su proceso o maquinaria, ¿no investiga la causa de la falla? ¿Se necesitan tres o incluso hasta cuatro fallas similares antes de tomar acciones para buscar la causa?
Además de la búsqueda de las causas de la falla, ¿aprovecha la oportunidad para inspeccionar otras zonas de desgaste y superficies de la máquina? ¿Qué hay de los filtros, cedazos, pisos de los depósitos, condiciones de los sellos, corrosión, cojinetes planos, etc.?
¿Su organización tiene responsabilidades asignadas para las actividades del sistema de reporte de fallas, análisis y acciones correctivas (FRACAS, por sus siglas en inglés)? ¿Qué tal el análisis de la causa raíz?
Uno de los problemas con las inspecciones durante las reparaciones y las investigaciones de fallas es que las personas asignadas para realizar estas tareas son regularmente las mismas personas que directa o indirectamente son el blanco de la culpa. Pedirle a una organización de mantenimiento que encuentre fallas en sí misma tiene desafíos inherentes para los cuales no existe una solución fácil.
Parte de la respuesta es la cultura. Construir una cultura de mejora continua y no una cultura de culpar y señalar con los dedos es muy útil. Todos cometemos errores. ¿Cómo podemos aprender de ellos?
Se han detallado las cinco condiciones de la Inspección 2.0 de las máquinas. ¿Cómo se compara con su organización de confiabilidad?
Jim Fitch, Noria Corporation. Traducido por Pilar Esquivel, Noria Latín América