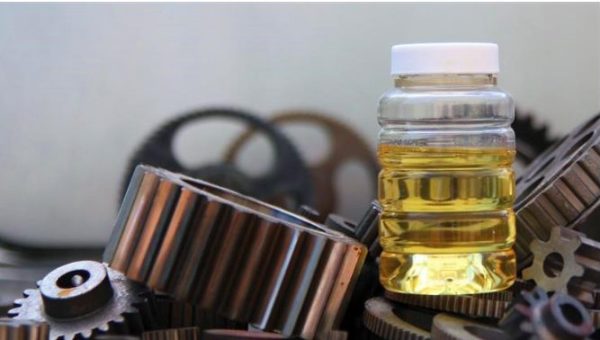
No hay duda de que un programa efectivo de análisis de lubricante reduce los costos de mantenimiento en equipos rotativos. El truco es saber cómo ejecutar un programa efectivo de análisis de lubricante. Las organizaciones deben ser proactivas para que la solución de un problema relacionado con el lubricante no sea siempre un cambio de aceite. El beneficio real del análisis de aceite es utilizar los datos para guiarlo hacia soluciones que eliminen los problemas. Este artículo describirá las mejores prácticas para usar el análisis de lubricante y monitorear su programa de lubricación.
Primeros pasos
¿Está esperando implementar estrategias básicas de manejo de lubricantes antes de tomar las primeras muestras de aceite porque sabe que los resultados serán malos? No dude en iniciar su programa. Probablemente verá muchas muestras de aceite con problemas, pero eso no es un motivo para retrasar la toma de muestras. Los problemas relacionados con el aceite son oportunidades para su programa de lubricación. Cuanto más grave sea el problema, mayor será la oportunidad de obtener una solución rentable que se traduzca en grandes ahorros para su presupuesto de mantenimiento.
Comience por tomar muestras de aceite nuevo para establecer líneas base (limites) antes de realizar mejoras en las condiciones de sus lubricantes y maquinaria dentro de la planta. Además, los resultados iniciales del análisis de aceite le brindarán orientación en cuanto a las soluciones que deben implementarse y en qué maquinaria.
Qué buscar
Cuando reciba sus primeros resultados de las muestras de aceite, lo más probable es que vea una serie de reportes anormales o críticos. Los principales problemas para tomar en cuenta son: la contaminación con agua, alto nivel de partículas sólidas en el aceite y rellenos de aceite incorrectos.
También es posible que obtenga resultados que muestren un desgaste anormal o grave en alguna maquinaria. El propósito de establecer un programa de lubricación es mantener una adecuada lubricación y evitar el desgaste innecesario, por lo que supongamos que su personal de confiabilidad está evaluando estos reportes y tiene la situación en cuestión. En su lugar, nos centraremos en los problemas relacionados con el lubricante, comenzando con la contaminación por suciedad y el agua.
El agua aparecerá en su reporte de muestra como «agua» o «H2O». ¿Son estos resultados anormales o graves? En este punto, no se ha establecido ningún nivel de alarma para la contaminación por agua, por lo que es aceptable utilizar los valores predeterminados del laboratorio para su industria y tipo de maquinaria. Con la mayoría de los equipos rotativos, el límite de contaminación para el agua será de 0.1 por ciento. Los límites oscilarán desde 0.03 por ciento para turbinas y hasta 0.5 por ciento para cajas de engranajes. Algunos compresores que usan aceites sintéticos pueden llegar a tener un alto porcentaje de agua.
La contaminación aparecerá en el reporte de muestra como silicio (Si, como símbolo del elemento químico) junto con los demás datos de elementos de desgaste y aditivos. Si está muestreando maquinaria con filtración de aceite el laboratorio debería hacer conteo de partículas. Asegúrese de haber solicitado el conjunto de pruebas adecuado para este tipo de maquinaria.
Ponga atención al código de limpieza ISO, así como a los conteos de partículas por tamaño en micrones. Los niveles anormales o graves de silicio y/o los resultados del conteo de partículas indican un problema con la contaminación. Nuevamente, el laboratorio utilizará los límites típicos de la industria para la limpieza del aceite y del silicio, lo cual está bien cuando esté comenzando su programa de análisis de lubricante. El nivel estándar de alarma de silicio para la mayoría de los equipos es de aproximadamente 25 partes por millón (ppm). Los códigos de limpieza ISO para sistemas filtrados están generalmente alrededor de 19/17/14.
Los rellenos de aceite inadecuados son un poco más difíciles de detectar, pero busque comentarios sobre los cambios en los niveles de elementos de los aditivos (fósforo, zinc, magnesio, boro, bario, azufre, etc.) y monitoree cualquier cambio en la viscosidad del aceite que tenga una variación de más o menos 10 por ciento con respecto a la línea de base del aceite nuevo. Los niveles de elementos de los aditivos pueden fluctuar hasta en un 25 por ciento, por lo que un laboratorio buscará otros elementos que no deberían estar presentes o la falta de un elemento que debería estar presente en el aceite.
Algunos laboratorios tienen algoritmos muy sofisticados que no solo comparan el aceite usado con la línea base, sino que también pueden determinar el tipo de fluido y compararlo con el tipo de fluido genérico para el aceite que ha especificado. Luego pueden avisarle cuando se está utilizando un tipo diferente de fluido. Es posible que desee consultar si su laboratorio tiene la capacidad de realizar este nivel de comparación.
Los rellenos incorrectos o el uso incorrecto de aceites son cuando la viscosidad varía considerablemente con relación a la línea de base del aceite nuevo. Esto incluiría cuando cree que está usando un aceite para engranajes ISO VG 320, pero la viscosidad es en realidad de 100 centistokes, lo que indica un posible relleno con aceite hidráulico, de compresor o de circulación.
Para la mayoría de la máquinas lubricadas de la planta, la condición del aceite se controla utilizando el número de ácido del aceite (AN). Cuando el aceite se oxida, forma productos ácidos de degradación. Un incremento en el AN significa degradación del aceite. Una vez que el AN supera el límite establecido para el lubricante, es hora de programar su cambio. Los sistemas grandes, como las turbinas, requieren pruebas más avanzadas, como las pruebas de oxidación en recipiente rotarotio presurizado (RPVOT, por sus siglas en ingles), la demulsibilidad, las propiedades antiherrumbre, las características de formación de espuma y la liberación de aire, para determinar si el aceite está en capacidad de continuar en uso.
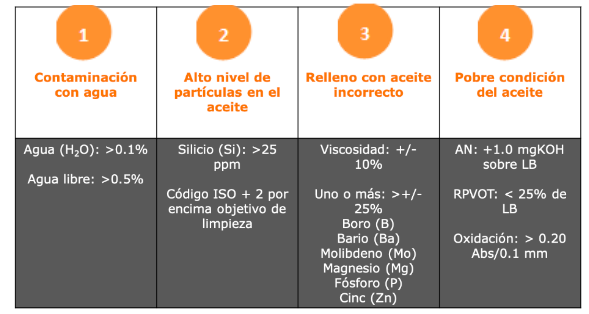
Los problemas más comunes relacionados con el lubricante descubiertos por el análisis de lubricantes y sus limites de advertencia
Cómo corregir problemas
Así que el análisis del aceite encontró algunos problemas. ¿Ahora qué? Tenga en cuenta que estos problemas relacionados con el aceite son oportunidades para mejorar su programa de lubricación. La mayoría de las sugerencias son de bajo costo y proporcionan una tasa alta de retorno de la inversión. Muchas de estas recomendaciones se pueden implementar en un corto tiempo y no requieren de una gran inversión de capital. Cuanto más rápido inicie, más mejorará el balance final de su presupuesto de mantenimiento.
Los respiradores de partículas con desecantes de buena calidad son la primero opción para comenzar. Los respiradores de partículas con desecante son una solución fácil de implementar y de bajo costo para evitar que el agua y las partículas entren en la maquinaria. Los respiradores de partículas con desecante pueden reducir los niveles de humedad en los aceites, incluso cuando los resultados del análisis del lubricante muestran un 0,2 por ciento o menos de contaminación por agua. Los respiradores de partículas con desecante secan el aire que ingresa a la maquinaria durante la operación y también el espacio de superior en los depósitos, eliminando la humedad del aceite. El resultado es un aceite más seco. Además, estos respiradores de partículas con desecante tienen un filtro especificado en micrones que limpia el aire, lo que también conduce a un aceite más limpio.
Para sistemas muy grandes, el uso de gas seco comprimido en el espacio superior del depósito puede ser una opción efectiva, especialmente cuando hay una fuente de gas seco comprimido fácilmente disponible (como en las refinerías). Por ejemplo, el uso de nitrógeno seco en un depósito de aceite de turbina puede crear una presión positiva para evitar el ingreso de contaminantes. El gas seco hace que la humedad salga del aceite y entre en el espacio superior, de donde es liberado hacia el exterior.
Para sistemas con problemas importantes de contaminación con agua (0.5 por ciento o más de agua en el aceite), se requiere una solución más complicada. Comience por asegurarse de que todas las compuertas de la maquinaria y los puertos de inspección estén debidamente selladas. La mejora de los sellos puede ser necesaria. Para eliminar la contaminación con agua entre 0,3 y 2,0 por ciento en sistemas más pequeños (menos de 56 litros de aceite), considere usar un carro de filtración fuera de línea equipado con filtro de adsorción de agua. Si hay demasiada agua, corre el riesgo de incrementar su gasto en elementos para filtros. Consultar con su proveedor de cartuchos para filtro puede ayudarlo a evaluar la situación. Si los problemas de contaminación del agua son crónicos (por ejemplo, fugas en el enfriador) y tiene sistemas grandes (más de 378 litros), necesitará un equipo como un deshidratador de vacío o un sistema de centrifugación por bypass. En este caso, estará invirtiendo de $25,000 a $100,000 USD.
La contaminación por partículas se puede manejar fácilmente con una lubricación correcta, puertos de drenado y filtración fuera de línea. Compre un carro de filtración fuera de línea que mejor se adapte a su aplicación y necesidad. Los carros para filtrar aceite hidráulico son bastante sencillos y económicos. Las aplicaciones para las cajas de engranajes requieren equipo de trabajo pesado y tiempo para garantizar que el carro de filtración tenga las especificaciones adecuadas para la aplicación.
Es fundamental colocar puertos de llenado y drenado a la maquinaria que formará parte de su programa de filtración fuera de línea, ya que estos puertos cuentan con conexiones rápidas que permiten a los técnicos de lubricación conectar fácilmente un carro de filtración y realizar rellenos y cambios de aceite sin tener que quitar los puertos de llenado y drenado. Además, se puede colocar un respirador de partículas con desecante, lo que reduce aún más la entrada de partículas.
El control de los rellenos de aceite se puede administrar fácilmente. Comience por instalar el conector rápido en el equipo para facilitar los rellenos y proporcionar el equipo correcto a los técnicos para el despacho del lubricante y así puedan realizar el trabajo correctamente. Si le da a su personal de lubricación las herramientas adecuadas, harán el trabajo de la manera correcta.
Las etiquetas de identificación de aceite se deben colocar en los puntos de lubricación. Use colores y/o símbolos para identificar el lubricante que se utiliza. Los contenedores de despacho están disponibles en una variedad de colores para combinar. Con algo de entrenamiento básico en lubricación, su personal de lubricación estará equipado con las herramientas y el conocimiento necesario para hacer el trabajo correctamente.
Si el reporte de la muestra indica una condición deficiente del aceite (donde no hay contaminación), debe programar un cambio de aceite cuando sea conveniente. Si se trata de un cambio de aceite costoso (más de $ 5,000 USD), puede ser aconsejable invertir en pruebas de laboratorio más avanzadas para determinar si se requiere o no realizar el cambio inmediatamente o si la tarea puede posponerse por tres meses o más. A diferencia de la contaminación, en el 99 por ciento de los casos en que la condición del aceite es un problema, es necesario cambiar el aceite. Para una mejor indicación de lo que está pasando con el aceite, solicite pruebas de colorimetría de membrana (MPC, por sus siglas en ingles) para el potencial de barniz y pruebas de voltametría de barrido lineal (LSV, por sus siglas en ingles – RULER) para determinar las cantidades exactas de antioxidantes que quedan en el aceite.
Monitoreo de su programa de lubricación
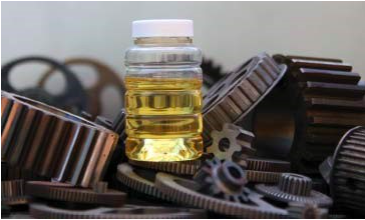
Después de implementar estas soluciones, ¿qué debe observar en sus reportes de análisis de lubricante? La humedad y los niveles de partículas deberían comenzar a bajar una vez que haya sellado sus depósitos de aceite adecuadamente.
Durante unos seis meses, estos niveles alcanzarán su mínimo. Vale la pena señalar algún cambio de las líneas de base de los aceites y establecer objetivos razonables para el futuro.
Por ejemplo, digamos que el nivel de agua en su caja de engranajes fue inicialmente de 0.15 por ciento y el código de limpieza ISO fue 22/20/18. Seis meses después de colocar respiradores de partículas con desecante y utilizar un carro de filtración fuera de línea, sus niveles de humedad son ahora 0.03 por ciento y el código de limpieza ISO es 20/18/16. Debe informar a su laboratorio que desea establecer nuevos límites de alarma en estas cajas de engranajes. Establezca la alarma anormal de limpieza ISO en 22/20/18 (dos códigos por encima del nuevo promedio), y la alarma crítica en 23/21/19 (tres códigos por encima del nuevo objetivo). Para la humedad, establezca la alarma anormal en 0.05 por ciento y la alarma crítica en 0.10 por ciento. Ahora, cuando reciba reportes de muestras anormales o críticas en función del nivel de agua o partículas, sabrá qué medidas correctivas debe tomar: cambiar el filtro respirador de partículas con desecante y/o poner en operación el carro de filtración fuera de línea durante varios días y volver a tomar otra muestra.
Si implementa procedimientos de identificación de aceite e invirtió en dispositivos apropiados de despacho, ya no debería ver cambios significativos en los aditivos (más del 25 por ciento más o menos) o cambios en la viscosidad (más del 10 por ciento o más) a menos que la condición del aceite también sea sospechosa. Cuando vea un cambio dramático, asegúrese de que todo el personal nuevo de lubricación esté informado sobre cómo evitar la mezcla de aceite y que haya recibido capacitación sobre el uso del equipo de despacho. Si el problema no es la capacitación, es posible que tenga una entrega de aceite identificada incorrectamente y debe tomar muestras de los contenedores o tambores sospechosos.
Éxito en la medición
Si ha estado utilizando los datos del reporte de análisis para encontrar problemas en su planta relacionados con el aceite, los reportes de gestión posteriores deben mostrar una tendencia decreciente en las estadísticas de agua, partículas y aceite incorrecto.
Si ha reducido la humedad y los niveles de partículas, entonces ha aumentado el tiempo medio entre fallas (MTBF, por sus siglas en ingles) para esa maquinaria. En el ejemplo anterior, la caja de engranajes debería ver un aumento de aproximadamente 1.25 veces, basado en la reducción de humedad, y 1.25 veces para la reducción de partículas, lo que significa un aumento de más del 50 por ciento del tiempo medio entre fallas (MTBF). Eso es significativo.
Con respecto a la mezcla de lubricante, no todos los rellenos de aceite incorrectos causan problemas de lubricación. Sin embargo, en varios casos, pueden ocurrir daños graves. Agregar menos del 1 por ciento de un aceite emulsionante, que está diseñado para mantener el agua en suspensión, destruirá la demulsibilidad de un aceite formulado para separarse del agua, es decir, aceite para circulación de rodamientos, aceite de turbina, etc. Las máquinas con componentes de bronce no deben usar aditivos comunes de extrema presión (EP). Colocar dentro de una máquina de este tipo un aceite con aditivos EP para engranajes no solo aumentará la viscosidad, sino que también provocará la corrosión de los componentes de bronce mucho después de que se haya detectado el problema y se haya cambiado el aceite.
Una inversión en la identificación de fluidos, en los equipos de aplicación adecuado y, lo que es más importante, en la capacitación y la educación, reducirá drásticamente la incidencia de rellenos de aceite incorrectos. Es muy difícil estimar los ahorros, pero evitar cualquier daño catastrófico justifica la mejora.
Siguientes pasos
Con estas modificaciones, sin duda habrán mejorado considerablemente su programa de lubricación. La tasa interna de retorno y el valor presente neto durante cinco años de un programa para una planta de tamaño mediano son, aproximadamente, 150 por ciento y $ 500,000 USD, respectivamente.
Los siguientes pasos requerirán de poner en un plan para gastos de capital. Invierta en una sala de lubricación de clase mundial con un avanzado sistema de almacenamiento de aceite, gabinetes y carros de filtración. Reemplace el programa de carros de filtración fuera de línea por sistemas de filtración montados permanentemente en equipos críticos. Aumente su programa de análisis de lubricantes estándar con un programa avanzado de monitoreo de aceite para máquinas críticas y aquellas con grandes depósitos de aceite (más de 1,000 litros).
Conforme continúe mejorando la condición de sus lubricantes, vuelva a revisar los niveles de alarma de desgaste, condición del aceite, contaminación y ajústelos en consecuencia. Su inversión inicial en la gestión de la lubricación probablemente ha eliminado el 80 por ciento de sus problemas relacionados con el lubricante. El próximo 20 por ciento tomará esfuerzos más continuos.
Los siguientes pasos incluyen la búsqueda de mejoras en toda la planta. Será esencial que continúe preparándose sobre las mejores prácticas de lubricación y también busque oportunidades para mejorar su programa. Recuerde, la clase mundial es un objetivo en movimiento, por lo que el consejo es comenzar ahora.
Noria Corporation. Traducido por Roberto Trujillo Corona, Noria Latín América.