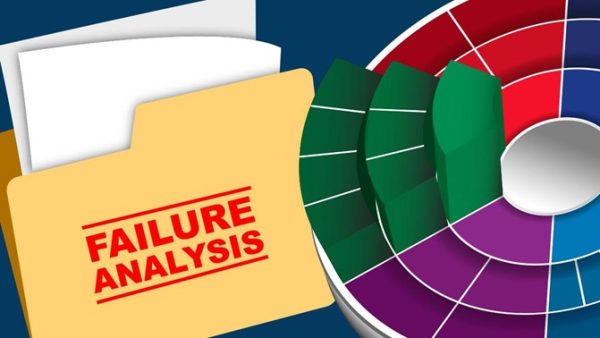
Es un escenario con el que la mayoría de la gente está muy familiarizada. A pesar de nuestros mejores esfuerzos, un componente falló en la planta y paralizó la producción. Estas fallas son la ruina de la confiabilidad y, a menudo, se analizan para determinar los modos de falla, aprender lecciones para evitar fallas futuras y, en algunos casos, rediseñar la máquina o el entorno para maximizar el tiempo de actividad del equipo.
Se utilizan términos como Análisis de Causa Raíz (RCA, por sus siglas en inglés) y Sistema de Informe, Análisis y Acción Correctiva de Fallas (FRACAS, por sus siglas en inglés), y se reúnen equipos de personas para analizar la falla desde varios aspectos de operaciones, mantenimiento, medio ambiente y la lista continúa. En última instancia, el objetivo es determinar qué sucedió específicamente que provocó la falla de la máquina, para que no ocurra lo mismo una y otra vez.
Pero la pregunta sigue siendo: ¿qué rol debería jugar la lubricación en todo esto?
El análisis de lubricantes existe de muchas formas dentro de una instalación: desde el personal de primera línea que realiza inspecciones hasta sensores en tiempo real que proporcionan datos sobre los diversos parámetros del componente. Todos estos datos son significativos y deben integrarse. Cada tipo de tecnología de monitoreo de condición tiene sus propias fortalezas y debilidades, pero combinar métodos puede proporcionar una mejor instantánea de lo que realmente puede estar fallando en esa máquina.
Cuando se trata de análisis de lubricantes, las principales fuentes de datos deberían incluir:
- Resultados de la inspección: Los técnicos u operadores que participan en las rondas diarias en una instalación poseen una enorme cantidad de información y experiencia. Revisar las notas sobre las inspecciones de las mirillas (nivel, espuma, emulsiones, depósitos, etc.) puede ayudar a señalar una falla del lubricante, o tal vez incluso una falta de lubricante. Lo mismo ocurre con las inspecciones audibles, observando cualquier ruido anormal que pueda haber ocurrido.
- Datos de muestreo de aceite: Esto representa una de las áreas más grandes de datos de rutina recopilados para generar tendencias y analizarlos en busca de advertencias tempranas o síntomas de falla de la máquina. Una mirada retrospectiva a los resultados de estas pruebas sobre la condición de los fluidos, la contaminación y las partículas de desgaste de las máquinas a menudo puede indicar un probable mecanismo de falla.
- Datos del análisis de grasa: Al igual que con el análisis del aceite, la grasa también contiene información valiosa. Si bien no es tan común como el análisis de aceite, el análisis de grasa puede proporcionar información sobre qué tan bien la grasa mantiene sus propiedades y si hay cantidades significativas de contaminación y partículas de desgaste presentes.
- Análisis de filtros: A menudo pasado por alto, el filtro es una bóveda de información, especialmente en lo que se refiere a fallas de maquinaria lubricada. Las partículas de desgaste a menudo aumentan en tamaño y concentración a medida que avanza la falla. Analizar la forma y la metalurgia de las partículas en el filtro puede proporcionar información útil sobre componentes específicos que pueden estar desgastados y, al mismo tiempo, arrojar algo de luz sobre el mecanismo de desgaste.
- Datos de sensores: Los sensores vienen en una variedad de formas, cada una de las cuales revela diferentes aspectos del lubricante o de la máquina. Dado que muchos sensores proporcionan datos a alta frecuencia, la información se puede analizar para determinar si hubo tendencias anormales que condujeron al evento de falla. Si no se encuentra ninguno, puede ser un motivo para volver a examinar dónde están instalados los sensores y los parámetros específicos que están monitoreando.
Existen muchas estrategias diferentes para realizar un análisis de causa raíz, pero todas comparten algunas similitudes. Con el mismo objetivo final de determinar qué sucedió y cómo evitar que vuelva a suceder, se han utilizado muchos métodos, incluidos los cinco porqués, diagramas de espina de pescado, análisis de árbol de fallas y análisis de diagramas de dispersión, por nombrar algunos.
Las fases del análisis de fallas adecuado
Todas estas herramientas son valiosas para ayudar a utilizar el método de análisis de fallas que tenga más sentido para su instalación u organización. Para simplificar, aquí hay cinco fases principales que recomiendo seguir:
- Recopilación de datos: Incluye la investigación de hechos, entrevistar a testigos del evento y determinar si hubo otros eventos secuenciales que puedan haber ocurrido con la falla. Durante la fase de recopilación de datos, es importante preservar la evidencia tanto como sea posible. Esto incluye documentar las condiciones finales de funcionamiento, tomar fotografías dela máquina y los componentes y obtener muestras de datos muy similares a los mencionados anteriormente. La diligencia es la clave para evitar incurrir en ningún impacto en la integridad de los datos recopilados durante este paso.
- Evaluación: Durante la fase de evaluación, se pueden emplear métodos analíticos como los cinco porqués. El objetivo general de este paso es analizar los datos y determinar si revelan la causa raíz de la falla. A menudo, las causas raíz se agrupan en una de las muchas de las siguientes categorías, que incluyen:
- Problemas con maquinaria/materiales
- Problemas de diseño
- Problemas de proceso
- Error humano
- Deficiencia de entrenamiento
- Problemas de gestión
Si bien esta no es una lista exhaustiva, una sola falla puede tener múltiples razones que la llevaron a un caso catastrófico. Por ejemplo, el rodamiento no se lubricó adecuadamente porque la frecuencia de PM programada era demasiado larga. Es posible que algunos técnicos simplemente atribuyan esto a un problema de lubricación y no observen los otros aspectos de lo que estaba ocurriendo.
- Acción correctiva: Representa el plan de reparación para solucionar el problema y evitar que vuelva a ocurrir. A menudo, este plan involucrará a varios departamentos, como mantenimiento, confiabilidad, ingeniería y operaciones. Dependiendo de la complejidad de la acción correctiva, lo más prudente puede ser un rediseño/reconstrucción completa de la máquina o del entorno en donde está alojada. Estos casos son raros pero ocurren.
- Informe: Las acciones para evitar que se repitan deben ser informadas a las partes que serán responsables de implementarlas. También es una buena práctica compartir la información con los departamentos que tienen impacto en la operación futura del activo. A veces, esto puede involucrar a los planificadores cuando es necesario actualizar una tarea de MP o una lista de materiales para reflejar los cambios derivados de este proceso.
- Seguimiento: Como ocurre con cualquier proceso, a menudo se emplea un paso de verificación para garantizar que se implementó el plan de acción correctiva. Esto también puede incluir análisis más detallados en el futuro, como aumentar la tasa de muestreo de lubricante, inspecciones y pruebas de la máquina.
Existen diferentes tipos de fallas que pueden requerir un análisis más significativo. Por ejemplo, una falla de un solo punto que ocurre cuando falla un solo componente podría resolverse en cuestión de minutos y no requerir un proceso RCA reglamentado. Las fallas multipunto o secuenciales pueden ser más difíciles de determinar la verdadera causa raíz y, como tales, requieren más atención e investigación para llegar al verdadero culpable.
Comprender cuándo y dónde implementar su proceso RCA puede basarse en muchos criterios. Por lo general, los RCA se reservan para aquellas fallas que son graves, complejas y repetitivas. Si este no es el caso, se puede utilizar eficazmente un modelo simplificado de RCA sin un gran riesgo para la organización.
No se desanime si el proceso es difícil o si la causa raíz es difícil de localizar. Sea diligente y apéguese a ello. Con el tiempo, descubrirá que se ha vuelto experto en resolver el complicado caso de falla de una máquina.
Referencia: Wes Cash, Noria Corporation. Traducción por Roberto Trujillo Corona, Noria Latín América