Un componente de maquinaria está funcionando según lo diseñado sin indicación de un problema; está realizando su función prevista. Sin el conocimiento del operador o del departamento de mantenimiento, la máquina comienza a desarrollar un desgaste anormal y el inicio del daño ha comenzado a ocurrir. Se toma una muestra de aceite y una lectura de vibración en el intervalo mensual de rutina regular; el problema no es detectable, pero la máquina ha entrado en un estado de falla. El desgaste continúa empeorando y alcanza un nivel detectable, pero estamos entre muestras mensuales, por lo que el departamento de mantenimiento aún no conoce la falla.
El momento en que la falla es detectable por primera vez (no detectada) se define como “P”. Cuando se alcanza el siguiente intervalo de muestreo mensual, se toma una muestra y se analiza, y el departamento de mantenimiento obtiene la primera indicación (detección) del problema.
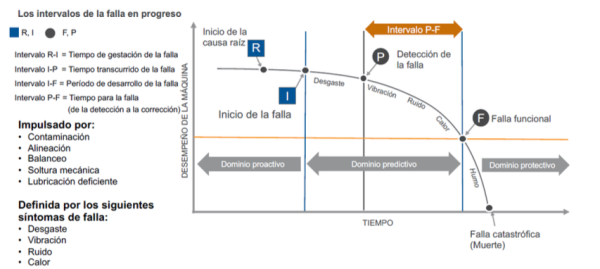
Figura 1. Dominio del monitoreo de condición en el intervalo de la curva P-F
El desgaste continúa aumentando, y el departamento de mantenimiento continúa detectando y monitoreando la situación de empeoramiento. Finalmente, algún tiempo después, el componente de la máquina se ha desgastado tanto que ya no puede realizar su trabajo previsto en el diseño (función). Todavía puede estar girando, pero no puede hacer su trabajo lo suficientemente bien (por ejemplo, bombear suficiente líquido).
Ahora hemos alcanzado una falla funcional (“F”), y el equipo debe estar fuera de servicio para reparación o reemplazo. El tiempo entre “P” y “F” se conoce como el intervalo P-F.
Se prefiere que el intervalo P-F sea lo más largo posible para permitir la planificación de la reparación y su programación para minimizar el impacto en la producción, de ahí la necesidad de un monitoreo frecuente de la máquina para detectar la falla lo antes posible.
Las causas raíz de las fallas son la razón fundamental de inicio de la falla. En la lubricación, generalmente se trata de contaminación con partículas, contaminación con agua, uso de un lubricante con viscosidad incorrecta, desalineación, desbalanceo, contaminación del sistema de lubricación con productos químicos y calor.
La máquina puede hacer ruido, calentarse o vibrar excesivamente, o el aceite puede parecer oscuro, pero todas estas observaciones o síntomas son causados por una causa más profunda. No realice una tarea como cambiar el aceite o verter agua sobre una bomba para enfriarla e ignorar la raíz del problema. Estas acciones no corrigen el problema, sino que lo enmascaran u ocultan. Corrija la causa raíz una vez y esperemos que nunca más tenga que tratarla nuevamente.
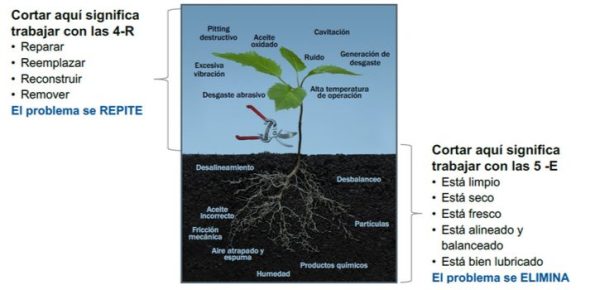
Figura 2. Ataque las causas raíz de falla, no los síntomas
Principio de Pareto
El Principio de Pareto o la Regla 80/20 establece que los eventos rara vez se distribuyen de manera uniforme en la vida. Los números 80 y 20 son aproximaciones redondeadas que no siempre se aplican, pero se puede decir que el 20 por ciento de las máquinas causan el 80 por ciento de las fallas y el tiempo de inactividad. El mensaje es concentrarse en equipos críticos que impactan directamente en la producción. Se puede a firmar que el 20 por ciento de las causas de falla son responsables del 80 por ciento de los casos de falla. El punto es enfocarse en las pocas causas raíz de fallas que ocurren en su planta. El concepto general es dedicar tiempo de mantenimiento a las pocas tareas que realmente marcan la diferencia. Trabaje en las cosas que más importan. Trate de lograr el mayor retorno de su inversión.
Mantenimiento centrado en confiabilidad
El mantenimiento centrado en confiabilidad (RCM, por sus siglas en inglés) es un proceso que intenta seleccionar tareas de mantenimiento que mejoren la confiabilidad al reducir el riesgo de fallas anticipadas en maquinaria crítica.
Es un ejercicio útil si no hay un historial de mantenimiento disponible para ayudar a seleccionar las tareas de mantenimiento más beneficiosas. RCM también aborda el hecho de que ocurren muchas fallas durante la infancia de la maquinaria (durante el arranque inicial o inmediatamente después de una reparación o reconstrucción). Intenta determinar si se debe realizar una tarea de mantenimiento observando las consecuencias de la falla (severidad) y la probabilidad de que ocurra una falla. Por lo tanto, la máquina solo debe abrirse o desmontarse para realizar el mantenimiento si existe una necesidad absoluta de hacerlo. Al abrir una máquina, se expone a contaminantes externos y es posible que no se vuelva a ensamblar correctamente. Hay algo de mérito en la antigua expresión, “Si no está descompuesto, no lo repares”. Sin embargo, solo porque una máquina esté funcionando no significa que no esté descompuesta. Las tecnologías de monitoreo de condición tales como vibración, análisis de aceite y termografía pueden detectar fallas incipientes (etapas iniciales) y condiciones de falla inminentes. Al igual que con la patología humana, la detección temprana de fallas y desgaste de la máquina es esencial para reducir los costos de reparación y establecer la confiabilidad de la máquina.
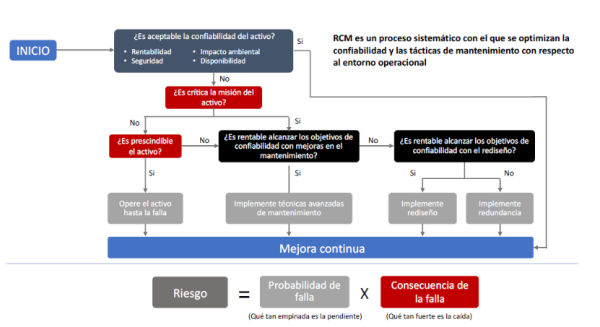
Figura 3. Enfoque del mantenimiento centrado en confiabilidad
Estrategias de mantenimiento
El mantenimiento reactivo o la operación a la falla es el enfoque de operar un equipo hasta que deja de rotar y se detiene por completo. Para equipos pequeños, económicos y no críticos, esta es una forma viable de operarlo. Pero para equipos grandes y costosos que son críticos para la producción, este es un enfoque costoso (en general) para operar una planta por varias razones. Cuando se permite que un rodamiento funcione hasta la falla completa, no solo se daña el rodamiento, sino que a menudo la carcasa y el eje también están dañados. Hay mucho daño colateral. Además, cuando se permite que un rodamiento funcione hasta la falla, se pierde una cantidad significativa de tiempo para decidir qué hacer a continuación, como reunir piezas, personas, herramientas, etc. La cantidad de tiempo de inactividad aumenta y también las pérdidas de producción.
El mantenimiento preventivo (PM, por sus siglas en inglés) es el mantenimiento que se realiza a intervalos o tiempo, independientemente de la condición del equipo o de sus componentes, como el aceite. No se realiza monitoreo para determinar qué mantenimiento se requiere. Los MP se realizan de forma rutinaria en toda la maquinaria de una planta, excepto en máquinas muy pequeñas, económicas e insignificantes. Esto incluirá engrase de rutina, controles de nivel de aceite e incluso cambios de aceite que se realizan en un tiempo de ejecución específico (horas) sin tener en cuenta la condición del aceite. Esto generalmente implica algunas conjeturas, y el aceite puede cambiarse con más frecuencia de lo necesario o no con la suficiente frecuencia. La misma situación puede ocurrir con el engrase de rutina de los rodamientos. Hay situaciones en las que los cambios de aceite basados en el tiempo son una necesidad, como cuando un equipo solo está disponible para un cambio de aceite una vez al año durante el cierre de la planta.
El mantenimiento predictivo implica el uso de cinco tecnologías principales de monitoreo: análisis de aceite, análisis de vibración, termografía, ultrasonido y análisis de corriente del motor, para monitorear la condición operativa de la maquinaria (y el aceite). Estas cinco tecnologías son como “herramientas en la caja de herramientas”. Ninguna tecnología es significativamente mejor que las demás. Cada uno busca una falla de una manera ligeramente diferente. Deben usarse como una colección de herramientas. Una puede ser mejor en el monitoreo que otra, dependiendo del equipo específico y las circunstancias.
Las tareas de mantenimiento predictivo intentan detectar las etapas iniciales de una falla y estimar la vida útil restante. Recuerde la curva P-F. El mantenimiento predictivo no evita que ocurran fallas. La falla debe haber comenzado a ocurrir antes de que la tecnología predictiva pueda detectarla. Sin embargo, el mantenimiento predictivo ayuda a reducir el impacto (severidad) que esas fallas tendrán (en la producción).
El mantenimiento proactivo está destinado a reducir realmente la cantidad de fallas en la maquinaria. Algunos ejemplos de actividades de mantenimiento proactivo incluyen establecer objetivos de limpieza del aceite y límites de contenido de agua, y luego monitorear los aceites nuevos y en servicio para asegurar que se cumplan estos objetivos. El prefiltrado de aceites que ingresan a los equipos para lograr niveles de limpieza más limpios y lograr una alineación y balanceo precisos son otros ejemplos de mantenimiento proactivo.
El término mantenimiento “programado” también se usa a veces. Simplemente se re ere al mantenimiento que se ha planificado en el que las herramientas y los procedimientos se reúnen y están listos para utilizarlos. Incluye todas las actividades preventivas, predictivas y proactivas.
Diferencia entre el mantenimiento reactivo y el mantenimiento proactivo
En un sistema reactivo típico, la mayor parte del esfuerzo del equipo de mantenimiento se dedica a atender a fallas. Hay poca o ninguna actividad planificada de mantenimiento y el trabajo se prioriza de manera aleatoria (en respuesta a averías) sin tener en cuenta los objetivos del negocio. Con este sistema se mantiene a la empresa operativa, pero a un costo muy alto ya que los paros imprevistos ocasionan mucho tiempo perdido para la obtención de repuestos y otros recursos para efectuar la reparación. Además, es difícil cumplir con los trabajos de mantenimiento preventivo ya que el personal de mantenimiento está la mayor parte del tiempo respondiendo a las fallas.
Un sistema de mantenimiento proactivo no está exento de fallas, pero la falla puede relacionarse con los objetivos de la organización a través de la criticidad de los activos y la prioridad asignada a cada trabajo.
Un trabajo de baja prioridad puede programarse para las actividades planificadas de las próximas semanas. También permite que el personal de mantenimiento controle la actividad de mantenimiento, en lugar de que la actividad “urgente” controle al personal.
Costo de la confiabilidad
La confiabilidad necesita equilibrar el costo de mejorar la confiabilidad con el costo de la producción perdida y el tiempo de inactividad. Si se gasta muy poco dinero en confiabilidad, el resultado puede ser que el tiempo de inactividad y los costos de producción perdidos sean altos. El objetivo es gastar suficiente dinero en mejorar la confiabilidad para reducir las pérdidas por tiempo de inactividad a n de lograr el menor costo general y el mayor beneficio para la empresa. Esto se ilustra en la figura 4.
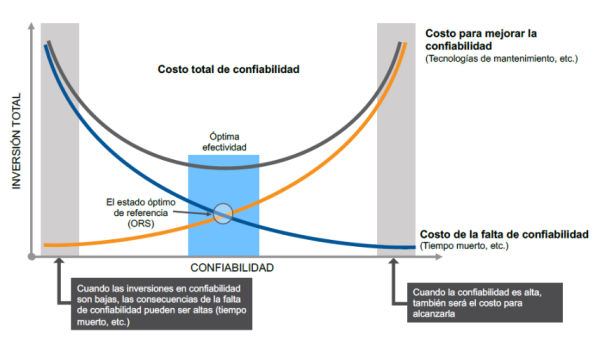
Figura 4. Balance de las inversiones para confiabilidad
Noria Corporation. Traducido por Roberto Trujillo Corona, Noria Latín América.