La apropiada selección de la maquinaria puede considerarse uno de los elementos básicos para obtener un firme retorno de inversión (ROI) de un programa de análisis de aceite. Raramente es costo-eficiente incluir todos los componentes lubricados o sistemas hidráulicos en un programa de análisis de aceite. Al intentar incluir en su programa todas las máquinas o la mayoría de ellas, corre el riesgo de llegar al punto en que disminuyen los retornos sobre el costo y aumenta el esfuerzo requerido para lograr esta meta.
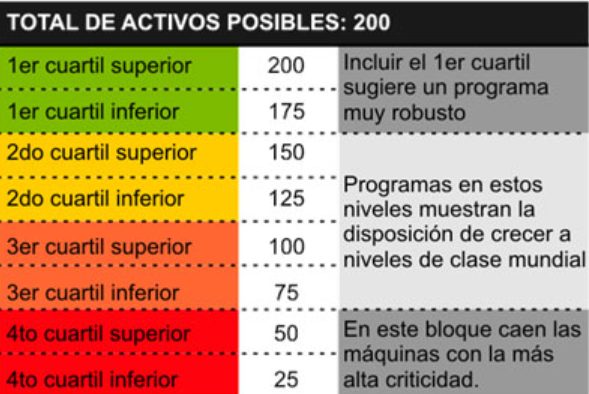
Figura 1. Ejemplo de un programa basado en cuartiles con 200 activos posibles
Existen varias metodologías para seleccionar la maquinaria para análisis de aceite. Una de ellas utiliza la cobertura cuartil. Como su nombre lo indica, la lista de activos, con sus valores asociados de criticidad, se divide en cuartiles. Este método divide posteriormente los cuartiles en la porción superior e inferior, lo que finalmente termina dividiendo la lista de máquinas en ocho secciones. Haciendo esto, usted puede asignar las máquinas en un área específica, lo que le da una guía para seleccionarlas.
Al utilizar este método, usted debe entender que mientras más bajo se encuentre su programa en la tabla de cobertura, más enfocado está en cubrir sólo las máquinas que son muy críticas. Por ejemplo, si usted está comenzando a establecer su programa de análisis de lubricante, o si está rediseñándolo, y se toma la decisión de incluir sólo el cuarto cuartil superior, entonces deberá tomar muestras primero de las máquinas más críticas. Una vez tomada la decisión, usted deberá revisar la lista de equipos críticos para determinar las siguientes máquinas a incluir.
79%
De los profesionales de la lubricación consideran que la criticidad de las maquinas es el factor más importante al seleccionar los equipos a incluir en el programa de análisis de lubricantes, de acuerdo con una reciente encuesta efectuada en machinerylubrication.com
Otro método sencillo es utilizar simplemente el principio de Pareto para seleccionar las máquinas. El principio de Pareto, o la regla 80:20, sugiere que el 20 por ciento superior de sus máquinas críticas tiene el potencial para provocar el 80 por ciento de sus problemas. Idealmente, esas máquinas caerán en el 20 por ciento superior de su escala de criticidad. Empleando esta simple regla, se vuelve muy fácil tomar una decisión sobre las máquinas a seleccionar.

Figura 2. Desglose de los valores de criticidad según el principio de Pareto para la selección de las máquinas
Si usted se enfocó en el 20 por ciento superior de los valores de criticidad para la selección de las máquinas, el principio de Pareto se desglosaría como se muestra en la Figura 2. Sin embargo, si usted quiere considerar el 20 por ciento actual de las máquinas, lo que se recomienda es que dé el siguiente paso. Al calcular el porcentaje actual de máquinas, haga una lista de todas las máquinas y el valor de criticidad asociado a cada una. A continuación, aplique matemáticas simples para determinar el valor límite real de criticidad para el 20 por ciento superior de las máquinas.
Aplicar este proceso no implica que usted ignore el restante 80 por ciento de los equipos de la planta. Más bien, ofrece un punto de partida para enfocar sus esfuerzos iniciales y un punto de continuación para cuando desee expandir el programa.
Cualquiera que sea el método que utilice para la selección de las máquinas, todavía tiene que tomar en cuenta algunos factores más. Generalmente el primer factor después de la criticidad es el volumen del depósito. Cuando usted considera una bomba centrífuga pequeña de aproximadamente un litro de aceite, es fácil darse cuenta de cómo el aplicar el análisis de aceite puede frustrar el propósito de hacer tareas que añadan valor.
Al muestrear un sistema con muy poco volumen de aceite, prácticamente está efectuando un cambio de aceite cada vez que extrae una muestra. Esto se debe al proceso de purga de los accesorios de muestreo, de acuerdo a como lo indican las mejores prácticas de muestreo. Los componentes que caen en este universo incluyen pequeñas cajas de engranajes, bombas y rodamientos lubricados por aceite.
Entendiendo el Principio de Pareto
El principio de Pareto, también conocido como la regla del 80:20, proporciona una estrategia para el trabajo inteligente en la organización de mantenimiento. Se afirma que el 20 por ciento de las causas de falla son responsables del 80 por ciento de las ocurrencias de las fallas. Es esencial entender estas importantes causas, que son conocidas como las pocas críticas. Estas son las causas dentro de su ámbito de control en las que debe centrarse. Entre ellas están la contaminación por partículas, contaminación por humedad, lubricante equivocado, lubricante degradado o incluso causas mecánicas como desalineación y desbalanceo. El principio de Pareto le permite enfocar sus recursos, establecer prioridades e identificar objetivos para obtener el mayor beneficio sobre su inversión y ayudar a reducir el riesgo para su organización. Otra regla del 80:20 se refiere a las máquinas en sí, ya que no todas las máquinas presentan el mismo nivel de riesgo. De acuerdo con esta regla, 20 por ciento de las máquinas de la planta pueden ser responsables del 80 por ciento del tiempo de inactividad. Estas máquinas son los malos actores que son más propensas a la falla. Pueden estar funcionando a la carga de diseño o incluso por arriba de la carga recomendada, a diferencia de las máquinas que están operando a sólo 5, 10 o 20 por ciento de la carga nominal. Si usted entiende cuáles son las máquinas más riesgosas y que han sido más propensas a las fallas en el pasado, puede enfocar sus recursos tecnológicos de mantenimiento y confiabilidad en ellas.
En el actual ambiente centrado en la tecnología, el tamaño del depósito es un problema menor, siempre y cuando se tomen las medidas necesarias para que se pueda regresar la máquina a su volumen total de aceite.
También debe tomarse en consideración la severidad del ambiente del fluido. Por ejemplo, si usted tiene dos máquinas parecidas cuyos niveles de criticidad son similares o incluso iguales en el valor calculado, con sólo tomar en cuenta la criticidad podría sugerir la misma estrategia para cada máquina o componente. Sin embargo, si observa todo el ambiente en el que el fluido debe operar, un componente puede requerir una estrategia ligeramente diferente al del otro.
El desarrollo de un programa integral de análisis de aceite requiere esfuerzo. Es fácil tomar el camino de menor resistencia y simplemente crear un programa “al vuelo”, lo cual nos retornará resultados muy pobres. Para alcanzar el mejor retorno de inversión (ROI), deben tomarse en consideración la criticidad y severidad de operación del fluido. Sólo entonces podrá decir que tiene un verdadero programa de análisis de aceite de clase mundial.
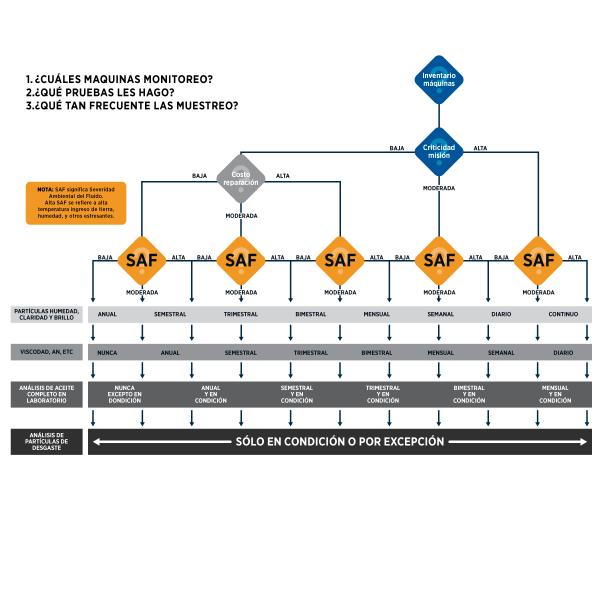
Noria Corporation. Traducido por Roberto Trujillo Corona, Noria Latín América
Publicado en la revista Machinery Lubrication (4/2012)