
El choque hidráulico ocurre cuando el aceite comienza o deja de fluir rápidamente en un sistema hidráulico. El caudal de aceite es generalmente de 4.5 a 6.0 metros por segundo (15 a 20 pies por segundo) en la línea de presión de sistemas por debajo de 3,000 psi. En sistemas por arriba de 3,000 psi, el caudal puede ser tan alto como 9.4 metros por segundo (30 pies por segundo). El choque también puede ocurrir cuando una fuerza externa actúa sobre un cilindro o motor hidráulico.
A diferencia del aire, el aceite hidráulico generalmente se considera no compresible. El aceite solo comprimirá la mitad del porcentaje cuando se presurice a 1,000 psi. Cuando se produce un pico de presión en el sistema, la presión puede aumentar cuatro o cinco veces por encima de la presión de operación normal. Dado que la duración promedio de un pico de choque es de 25 milisegundos, el medidor de presión no puede responder lo suficientemente rápido como para dar una indicación precisa. Los transductores de presión se utilizan normalmente para registrar picos de presión.
Los picos de choque que no son apropiadamente disminuidos o absorbidos pueden provocar fugas y daños en las tuberías y componentes del sistema. Este artículo analizará tres cosas que pueden hacerse para reducir el choque hidráulico.
Instale un acumulador
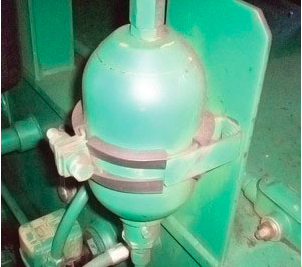
Figura 1. Acumulador de cámara de aire (hule)
Un acumulador hidráulico está precargado con nitrógeno seco. Se usa algún tipo de dispositivo de separación, como un pistón, cámara de aire (hule) o diafragma, para separar el nitrógeno del aceite hidráulico dentro del acumulador. Se recomienda una cámara de aire (hule) (Figura 1) o un tipo de diafragma para absorber los choques. Los dos acumuladores contienen elementos de hule que se comprimen cuando la presión hidráulica rebasa la presión de precarga con nitrógeno seco. Dependiendo del sistema, el acumulador se debe precargar de 100 psi por debajo a 200 psi por encima de la presión máxima de operación del sistema. Los acumuladores que se usan para absorber choques pueden ser de tamaño pequeño, generalmente de un litro a 4 litros.
El acumulador debe instalarse lo más cerca posible al lugar donde se produce el pico de choque. Por ejemplo, si el pico de presión se presenta cuando el cilindro se extiende completamente, el acumulador debe instalarse cerca del puerto conectado al lado del pistón lleno del cilindro.
Los acumuladores se utilizan para absorber grandes cantidades de flujo en las líneas de retorno. En este caso, la precarga debe ser inferior a la presión nominal máxima de cualquier filtro de retorno o intercambiador de calor ubicado aguas abajo. Cada vez que se usa un acumulador en la línea de presión, se debe instalar una válvula de descarga manual y/o automática para purgar la presión hidráulica hasta cero una vez que se apaga el sistema.
Agregue una válvula estranguladora direccional piloto
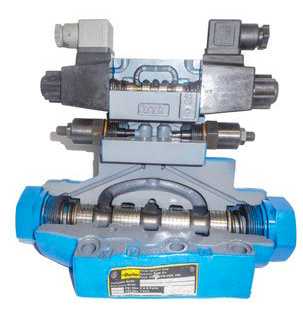
Figura 2. Una válvula direccional de dos etapas.
En la Figura 2 se muestra una válvula direccional, de dos etapas controlada por solenoide y pilotada hidráulicamente. La válvula contiene estranguladores piloto, que se encuentran en el bloque entre la válvula piloto en la parte superior y el carrete principal en la parte inferior. El bloque incluye dos controladores de flujo conectados al medidor y dos válvulas check de bypass. Cuando cualquiera de los solenoides de la válvula piloto está activado, la presión se transporta a través de una de las válvulas de retención internas y hacia un lado del carrete principal.
A medida que el carrete se desplaza, el aceite en la cavidad del piloto en el lado opuesto fluye a través del control de flujo y regresa la tanque por la válvula piloto. La configuración del control de flujo determina la velocidad a la que se desplaza el carrete principal. Al permitir que el carrete se desplace lentamente, el volumen de la bomba se transporta gradualmente a través de la válvula y al sistema.
Hace varios años, me pidieron que consultara con una planta de tableros de fibra en Minnesota sobre cómo reducir el choque en su prensa caliente. Las tuberías se habían soldado varias veces debido a la fuga que se produjo debido a los picos de presión. La prensa utilizaba ocho bombas de paletas de 400 lpm (109 gpm) para suministrar un alto volumen de aceite para cerrar la prensa. Se utilizaban válvulas direccionales, como la que se muestra en la Figura 2, para transportar el volumen de las bombas de regreso al tanque cuando estaba en modo inactivo y cuando ya no se necesitan en los cilindros.
Cuando se ordenó cerrar la prensa, sonó como si ocho martillos golpearan el depósito. Después que se cerró la prensa y se desenergizaron los solenoides, se produjo una tremenda cantidad de vibración y choque en las tuberías. Esto se debió al cambio rápido de la dirección del flujo en las bombas. En lugar de ir a la prensa, el volumen de las bombas cambió rápidamente de dirección y regresó al tanque a través de las válvulas de descarga. Tomó un día entero ajustar los estranguladores piloto en las ocho bombas. Al final del día, las bombas entraban y se descargaban sin problemas.
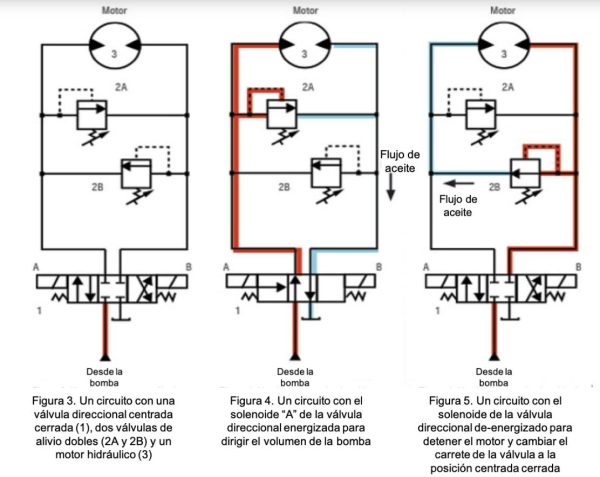
Los estranguladores piloto se consideran equipos opcionales en válvulas direccionales. En las válvulas que no las tienen, una vez que el solenoide de la válvula piloto esté activado, la presión del piloto se adaptará para desplazar el carrete principal a una velocidad muy rápida. Esto permite que el volumen de la bomba fluya inmediatamente a través de la válvula, lo que genera un pico de choque. Los estranguladores piloto se pueden agregar fácilmente a las válvulas existentes al usar pernos más largos para montar la válvula piloto y bloquear al alojamiento del carrete principal.
Utilice válvulas de alivio dobles
Las válvulas de alivio dobles se usan comúnmente con motores hidráulicos cuando es necesario detener una carga muy rápido. Los problemas principales con las válvulas de alivio dobles es que generalmente se omiten del sistema, se ajustan demasiado alto o se montan demasiado lejos del motor. En la Figura 3, se muestra un típico circuito con una válvula direccional de centro cerrado, dos válvulas de alivio dobles y un motor hidráulico.
Las válvulas de alivio dobles realizan dos funciones en el sistema hidráulico: primero, absorben el pico de choque inicial que se produce cuando el aceite se transporta por primera vez para impulsar el motor y segundo, detiene el motor cuando se desactiva la válvula direccional.
Las válvulas de alivio dobles deben ajustarse a 200-400 psi por encima de la presión máxima requerida para impulsar el motor. En la Figura 4, el solenoide “A” de la válvula direccional se ha energizado para dirigir el volumen de la bomba al motor. Una vez que la presión aumenta momentáneamente a la configuración de la válvula “2A”, el carrete se abrirá y transportará el fluido presurizado a través de la válvula direccional y regresará al tanque. Cuando la presión cae por debajo del ajuste “2A”, el carrete de la válvula se cerrará y el motor comenzará a girar.
Cuando se desenergiza el solenoide de la válvula direccional para detener el motor, el carrete de la válvula cambiará a la posición central cerrada (Figura 5). El motor tenderá a continuar girando debido a la inercia de la carga en movimiento y se convertirá momentáneamente en una bomba hidráulica, entregando aceite a su puerto de salida. La presión aumentará hasta que se alcance el ajuste de la válvula de alivio doble “2B”. La válvula “2B” luego se abrirá y dirigirá el flujo de aceite de regreso al puerto de entrada del motor. El ajuste del resorte “2B” determinará qué tan rápido se detendrá el motor.
Si tiene problemas de choque y fugas en los circuitos del motor hidráulico, primero verifique que el sistema cuente con las válvulas de alivio doble. He visto algunos sistemas en los que se han omitido, permitiendo que el choque se dé en las tuberías, mangueras y accesorios, lo que produce fugas. En segundo lugar, asegúrese de que las válvulas de alivio dobles estén ajustadas correctamente. Cuando hay un problema en un sistema hidráulico, generalmente la primera acción es aumentar la presión. En tercer lugar, las válvulas de alivio dobles deben ubicarse lo más cerca posible del motor hidráulico.
Una planta de madera contrachapada en Carolina del Norte estaba teniendo un problema para arrancar el eje rotatorio del motor hidráulico del lanzador de troncos. A medida que los troncos bajaban por el transportador, el motor giraba y empujaba el tronco para sacarlo de la banda transportadora y colocarlo en la banda transportadora de alimentación hacia el torno. Tras la inspección, se encontraron válvulas de alivio doble debajo de la válvula direccional, instalada a 9 metros (30 pies) de distancia del motor. Se instaló un conjunto adicional de válvulas de alivio doble cerca del motor, lo que eliminó el problema de arranque de los ejes del motor.
Del mismo modo, al utilizar estas tres recomendaciones, puede disminuir considerablemente el impacto hidráulico en sus sistemas y ayudar a eliminar las fugas de aceite en su planta.
Noria Corporation. Traducido por Roberto Trujillo Corona, Noria Latín América.