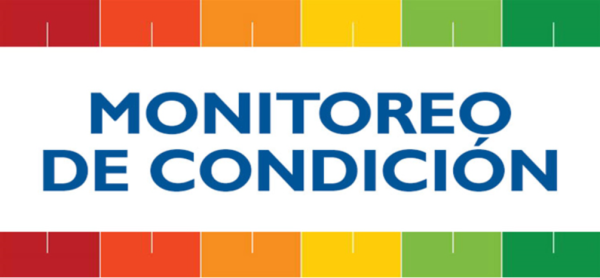
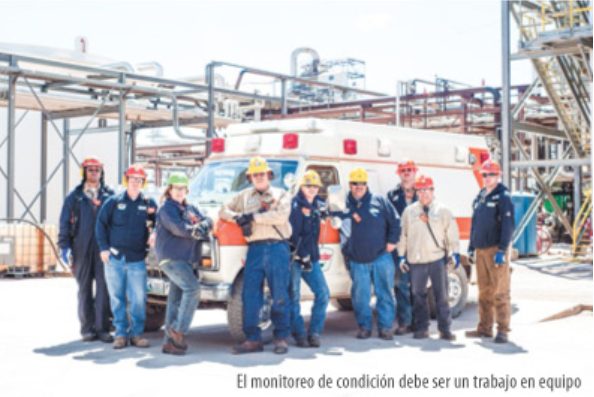
El monitoreo de condición nunca debe limitarse a un solo método o tecnología. En su lugar, debe combinar e integrar una buena selección de herramientas y tareas útiles. El monitoreo de condición puede basarse en gran medida en tecnología, pero también puede basarse en la observación o inspección.
La mayoría de la maquinaria comparte las necesidades de monitoreo de condición e inspección con muchos otros tipos de maquinaria. Esto se debe a que tienen en común componentes y condiciones de operación, es decir, motores, rodamientos, sellos, lubricantes, acoplamientos, etc. Al mismo tiempo, sus condiciones de operación y aplicaciones pueden exigir requisitos únicos de inspección. Estos influyen en los modos de falla y criticidad de la maquinaria.
Como se comentó en artículos anteriores, la inspección debe verse con la misma seriedad con que se ven otras prácticas de monitoreo de condición. En mi opinión, un programa de inspección de clase mundial debería producir más «ahorros» que todas las demás actividades de monitoreo de condición combinadas. No es una alternativa al monitoreo de condición basado en la tecnología, sino un compañero poderoso y estratégico.
Las tecnologías de termografía infrarroja, ferrografía analítica, vibración, corriente del motor y acústica se utilizan generalmente para detectar fallas activas y desgaste anormal. A la inversa, un programa de inspección bien realizado debería centrarse en gran medida en las causas fundamentales y en las condiciones iniciales (etapa temprana). La detección de desgaste avanzado y falla inminente es secundaria.
Solución a la ceguera del monitoreo de condición
Considere esto: ¿Cómo podría detectar alguna de las tecnologías de monitoreo de condición mencionadas el inicio repentino de lo siguiente?
- Sello dañados y fugas de aceite.
- Filtración en derivación (bypass)
- Fuga de refrigerante
- Aceite con aire atrapado
- Oxidación del aceite
- Barniz
- Deficiente suministro de lubricante (desabasto)
- Agua y sedimentos en el fondo (BS&W, por sus siglas en inglés)
- Incorrecta respiración o condición de ventilación
Incluso si las tecnologías pudieran detectar estas condiciones, la capacidad está limitada por el programa de monitoreo de condiciones. Por ejemplo, considere un programa de monitoreo de condición que se realiza mensualmente y en el primer día de cada mes. Si el inicio de una condición anormal ocurre al día siguiente, no se detecta mediante el monitoreo de condición basada en tecnología sino hasta el mes siguiente (30 días después).
Podría decir que la inspección proporciona los ojos y oídos para todo lo que el monitoreo de condición no puede detectar y es una forma predeterminada de detección durante los días intermedios del mes cuando no se realiza un monitoreo de condición basado en tecnología. En otras palabras, la inspección llena los vacíos críticos donde existe ceguera de las tecnologías y ceguera en la programación a causa de las frecuencias de uso. Las inspecciones frecuentes y las habilidades de revisión (por parte del técnico) aumentan significativamente la capacidad del monitoreo de condición para detectar causas y síntomas de diversos estados de falla.
Términos y definiciones
- Condición reportable: Esta es una condición anormal que requiere corrección. Una condición reportable podría ser una causa raíz, un evento de falla o una falla activa.
- Dominio proactivo: Este es el período de tiempo en el cual hay una condición de causa raíz reportable pero aún no se ha producido una pérdida significativa de la vida útil de la maquinaria. A menos que se detecte y se corrija, la condición avanzará al dominio predictivo.
- Dominio predictivo: Este sigue al dominio proactivo, también se le conoce como el período de desarrollo de falla. El dominio predictivo comienza al inicio de una condición de falla reportable (por ejemplo, desalineación grave) y termina cuando se aproxima el final de la vida útil en operación.
- Vida útil remanente (RUL, por sus siglas en inglés): Es una estimación de la vida que le resta a una máquina cuando se detecta y se repara una condición de desgaste o falla activa. Las máquinas comienzan con una RUL del 100 por ciento. A medida que envejecen y se produce el desgaste, la RUL se aproxima a cero.
- Ahorros por causa raíz (RC, por sus siglas en inglés): El ahorro por causa raíz es el porcentaje de condiciones reportables que se detectaron y resolvieron en el dominio proactivo. Cuanto mayor sea este número, mejor. Todos los ahorros por RC dejan a la RUL sin cambios.
- Ahorros predictivos: Se refiere a las condiciones detectables que han avanzado al dominio predictivo y se corrigen antes de la falla operativa. La RUL de la máquina se redujo durante el tiempo en que la condición reportable permaneció sin ser detectada y sin corregir en el periodo predictivo.
- X: Este es un punto de la línea de tiempo cuando se detecta y remedia una condición reportable (por ejemplo, la causa raíz de una falla). También representa una falla operativa cuando no se detectó en los dominios proactivo o predictivo.
- Omisiones: Las omisiones se refieren al porcentaje de condiciones reportables que avanzan a una falla operativa no detectada. Cuanto menor sea este número, mejor.
- Efectividad general del monitoreo de condición (OCME, por sus siglas en inglés): Esta métrica define la efectividad general del monitoreo de condición (inspección combinada con el monitoreo de condición basado en tecnología). Esto se cuantifica como el cambio promedio en el porcentaje de vida útil remanente (RUL) en todas las máquinas y condiciones reportables durante el período del reporte. Cuanto mayor sea este número, más efectivo será el monitoreo de condición para detectar y corregir las condiciones reportables en una etapa temprana.
- Intervalo de monitoreo de condición: Se refiere al periodo de tiempo entre eventos de monitoreo de condición basado en tecnología (vibración, muestreo de aceite, termografía, etc.).
- Intensidad del monitoreo de condición: Se refiere al número de tecnologías de monitoreo de condición utilizadas y la intensidad de su uso. Por ejemplo, un conjunto de pruebas de análisis de aceite que involucra numerosas pruebas con una interpretación de datos especializada, se referiría como intensa.
- Intervalo de inspección: Se refiere al periodo de tiempo entre las inspecciones de la maquinaria por parte de operadores y técnicos.
- Intensidad de inspección: Se refiere al número de puntos de inspección y las habilidades del personal para examinar.
Construya un equipo de monitoreo de condición
El monitoreo de condición debe ser un esfuerzo de equipo. Como con la mayoría de los equipos, cada integrante contribuye con habilidades únicas y necesarias para mejorar las capacidades colectivas del equipo. Un integrante no puede o no debe hacer las tareas de otros. En el fútbol americano, no puedes convertir a un apoyador en un mariscal de campo. Si bien los integrantes del equipo son diferentes, todos están trabajando hacia un objetivo en común.
La gestión de un programa de monitoreo de condición es una actividad de formación de equipos. Tiene sus jugadores «A» y sus jugadores «B». Algunos son generalistas, y otros son especialistas. Tiene líderes, y tiene seguidores. Todos los elementos clásicos están ahí. El equipo de monitoreo de condición incluye personas (inspectores, analistas, etc.), tecnologías (vibración, contadores portátiles de partículas, cámaras infrarrojas, etc.) y proveedores de servicios externos (un laboratorio de análisis de aceite, por ejemplo).
Efectividad general del monitoreo de condición (OCME, por sus siglas en inglés)
El desempeño del equipo requiere una o más métricas alineadas a objetivos bien definidos. Algunas métricas son micro (por ejemplo, el total de vibraciones o conteos de partículas en el lubricante), mientras que otras son macro para capturar el desempeño general del equipo. En confiabilidad, las métricas macro podrían considerar el costo de confiabilidad (gasto del equipo) y el nivel general de confiabilidad alcanzado (por monitoreo de condición y otras actividades).
Para ilustrar el concepto de una métrica macro, estoy introduciendo la Efectividad General de Monitoreo de Condición (OCME). Esta métrica un tanto teórica maneja varios puntos importantes. OCME se define por la efectividad general del monitoreo de condición (inspección combinada con el monitoreo de condición basado en tecnología) en la detección de causas raíz y la detección temprana de síntomas de falla.
Esto se cuantifica como el porcentaje promedio de vida útil remanente (RUL) en todos las máquinas y condiciones reportables durante el período del informe (por ejemplo, un año). Cuanto mayor sea este número, más efectivo será el monitoreo de la condición para detectar y corregir las condiciones reportables en una etapa temprana. Las máquinas que no tienen fallas o condiciones reportables no se incluyen en esta métrica. La puntuación OCME perfecta es de 100, lo que significa que la RUL en todas las máquinas desde el comienzo hasta el final del período del informe no cambió. Esto se puede normalizar a las horas totales de funcionamiento de la maquinaria (para todo el grupo de máquinas incluidas en la métrica OCME).
Para mostrar cómo funciona la OCME, veamos tres ejemplos. Consulte las definiciones previamente listadas de los términos utilizados. Cada uno de los tres casos considera diferentes intervalos (frecuencia) e intensidad de inspección y monitoreo de condición. Nuevamente, la intensidad se refiere a la habilidad y efectividad de las tareas de monitoreo de condición e inspección.
En cada caso se utilizan hipotéticamente diez condiciones reportables. Estas pueden ser desalineación, desbalanceo, rodamientos trabajando a elevada temperatura, partículas de alto desgaste, lubricante incorrecto, falta de lubricante, contaminación con agua, etc. Se considera que las condiciones reportables detectadas en el dominio proactivo tienen un 100 por ciento de RUL. Falla operacional significa cero por ciento de RUL. Las condiciones detectadas en una etapa temprana en el dominio predictivo tienen un RUL más alto que las que se aproximan a la falla operativa. El punto de inicio del dominio predictivo es el inicio de la falla.
Caso #1: Intervalos comunes a baja intensidad
En este escenario, muy pocas de las condiciones reportables se detectan en el dominio proactivo (en la etapa de causa raíz). La mayoría de las condiciones avanzan a la etapa predictiva o falla operacional. Las causas de esto son la poca habilidad y efectividad de las tareas de monitoreo de condición e inspecciones. La RUL de cada condición reportable se estima y se calcula para obtener la puntuación de la OCME, que es de 35.5 en este caso. Alrededor del 40 por ciento de las condiciones reportables fueron omisiones, y solo el 10 por ciento fueron ahorros por causa raíz.
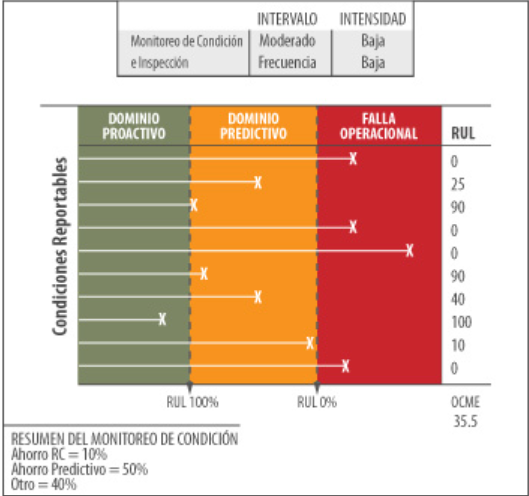
Caso #1
Caso #2: Intervalos comunes a alta intensidad de inspección
Este caso es el mismo que el primero, con la excepción de la habilidad de inspección y competencia (alta intensidad). Esto afecta drásticamente a la OCME (puntaje de 72). En lugar del 10% de ahorro por causa raíz ahora tenemos 50% y solo 10% de omisiones.
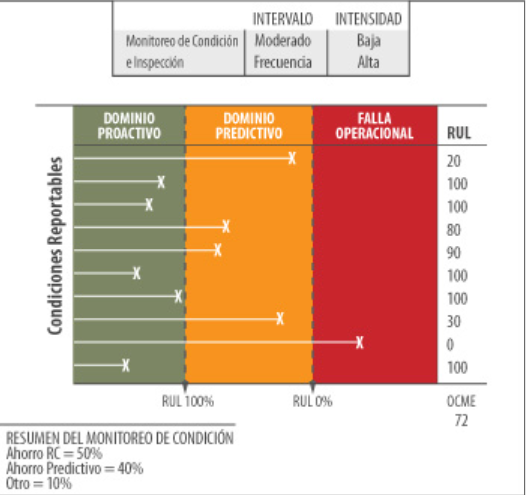
Caso #2
Caso #3: Monitoreo de condición e inspección de clase mundial
En este caso aplica una alta frecuencia e intensidad de inspección tanto para el monitoreo de condición basado en tecnología como para las tareas de inspección. En este alto nivel de supervisión, la mayoría de las condiciones reportables se detectan y reparan en el dominio proactivo (70 por ciento de ahorros por causa raíz). Todas las demás se detectan tempranamente en el dominio predictivo. Esto se traduce en una extraordinaria puntuación de 93 de la OCME para todos las máquinas y eventos reportables.
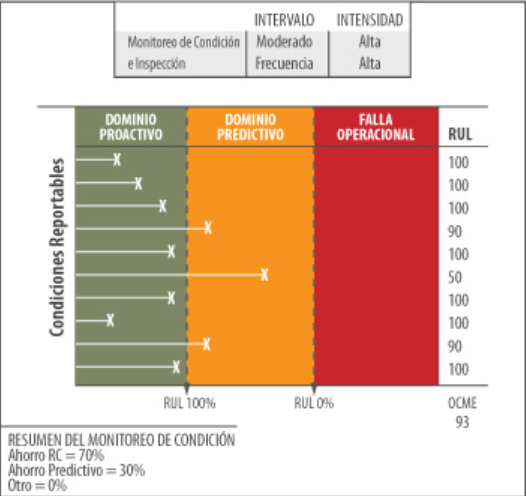
Caso #3
Optimización
Sería imprudente terminar esta columna sin hacer un pequeño recordatorio sobre la optimización. Como todos sabemos, el monitoreo de condición tiene un costo. Este costo está influenciado por la frecuencia y la intensidad. Se debe establecer el estado óptimo de referencia (ORS, por sus siglas en inglés) para el monitoreo de condición e inspección. Nuestro objetivo es optimizar la OCME en el contexto de la criticidad de la máquina y la clasificación del modo de falla. He tocado este tema ampliamente en artículos anteriores. Consulte mis artículos en Machinery Lubrication acerca del ORS, la criticidad global de la maquinaria (OMC, por sus siglas en inglés) y el análisis de modos y efectos de falla (FMEA, por sus siglas en inglés).
Como nota final, mi referencia a la intensidad no debe pasarse por alto como si no tuviese importancia. Es un factor determinante para mejorar la puntuación de la OCME. Lograr la intensidad en el monitoreo de condición e inspección tiene que ver tanto con la cultura como con el presupuesto disponible o el acceso a la tecnología. El entrenamiento y el apoyo de la gerencia definen la cultura del mantenimiento. Los factores humanos, tan delicados, requieren de un alto nivel de atención para lograr la excelencia en lubricación, confiabilidad y gestión de activos.
Jim Fitch, Noria Corporation. Traducido por Pilar Esquivel, Noria Latín América