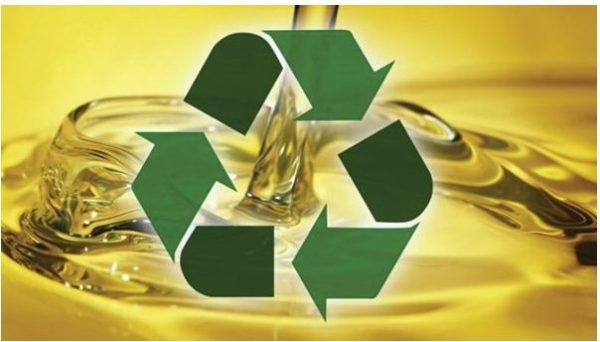
En la mayoría de las plantas, el reacondicionamiento de aceite no cuenta con el apoyo total debido a la falta de conocimiento técnico y disponibilidad de tecnologías, procesos y aplicaciones. ¿Por qué se debe considerar el reacondicionamiento? El proceso ha evolucionado a lo largo de los años a través de rigurosas pruebas de aceite y análisis de compatibilidad de ensayos en campo. Los avances y el apoyo científico ahora disponibles han llevado a tecnologías y procesos de reacondicionamiento robustos. Sin embargo, es importante entender los límites y fronteras.
Las experiencias y prácticas pasadas a menudo conducen a que el aceite se cambie en un intervalo de tiempo o en función de los resultados del análisis de aceite. Pocos gerentes quieren ser responsables del riesgo de usar métodos nuevos y emergentes. Por lo tanto, el cambio de aceite y el lavado del sistema suelen ser el enfoque elegido.
Los aceites lubricantes en sistemas de gran volumen pueden tener una larga vida útil. Algunos pueden estar en servicio durante 15 a 20 años. Muchos de estos aceites están hechos de bases lubricantes del Grupo I o II, a diferencia de las bases lubricantes más robustas del Grupo III o sintéticas a base de polialfaolefina (PAO). ¿Qué hace que estos lubricantes duren tanto? Una revisión histórica de los datos de estos sistemas revela que los aceites operaron dentro de los parámetros establecidos, específicamente temperatura y contaminación. El contenido de aditivos se mantuvo saludable y la base lubricante se mantuvo protegida. Los aceites tampoco se estresaron significativamente.
También se revisaron otros sistemas que experimentaron problemas significativos. Estos incluyeron problemas con el sello de laberinto, temperaturas más altas, degradación y falla del filtro, ingreso de gas y vapor de proceso y prácticas de mantenimiento deficientes. En estos casos, los aceites operaron en ambientes altamente estresados y estuvieron expuestos al calor, agua, contaminantes sólidos y químicos. También se emplearon costosas estrategias, como sistemas de filtración, deshidratadores por vacío y “endulzamiento” de los aceites.
Para las organizaciones que desean mitigar más problemas, hay buenas noticias. Algunas soluciones tienen una duración mucho mayor que otras, dependiendo de las operaciones, disponibilidad de repuestos, planes de mantenimiento y el establecimiento de objetivos a largo plazo. Para el aceite lubricante, se requiere un análisis detallado para determinar su vida útil. Algunos aceites serán aptos para continuar en uso, mientras que otros deberán cambiarse.
Desafortunadamente, pocas empresas se enfocan en recuperar sus aceites cuando la base lubricante no está comprometida, lo que solo puede verificarse a través de pruebas de laboratorio. El reacondicionamiento normalmente implicará la eliminación de precursores junto con la adición de aditivos, típicamente antioxidantes para aceites de turbinas. La adición de estos antioxidantes debe validarse mediante pruebas de compatibilidad. A continuación se detallan tres ejemplos de casos de estudio.
Caso de estudio #1: Planta petroquímica Turbina A
El tamaño del depósito de esta turbina en particular era de 11,000 litros. El sistema de aceite lubricante estaba bien mantenido y tenía una purga de nitrógeno en el espacio superior. El sistema de filtración utilizaba filtros absolutos de 5 micrones. El cambio de aceite estaba basado en un intervalo cronometrado y apoyado con un análisis de aceite de rutina. Dos veces al año se realiza la prueba de oxidación en recipiente rotativo a presión (RPVOT, por sus siglas en inglés), la prueba de voltametría de escaneo lineal para evaluación de la vida útil restante (conocida como RULER) y la prueba de colorimetría de micro membrana (MPC, por sus siglas en inglés). El sistema ha estado en servicio durante 12 años sin cambios de aceite. Los resultados típicos incluirían un valor RPVOT superior a 1100, más del 55 % de vida útil restante en la prueba RULER y un valor MPC inferior a 10.
Caso de estudio #2: Planta petroquímica Turbina B
El tamaño del depósito de este depósito era de 8,300 litros. El sistema de aceite lubricante tenía más de 30 años. El sistema de filtración v utilizaba cartuchos de algodón enrollado de 25 micrones nominales. El espacio superior del depósito tenía un deshumidificador, que había sido problemático. Debido a un problema con el sello de laberinto, había una fuga de vapor constante. El sistema experimentó importantes desafíos relacionados con el aceite lubricante. Los resultados típicos incluyeron un valor RPVOT de 700, 30 % de vida útil restante, un valor MPC de 35 y un cambio de viscosidad de más del 3 % cada seis meses.
El “endulzamiento” del aceite lubricante era frecuente. El barniz prevalecía. El sistema contaba con un deshidratador por vacío y una unidad de remoción de barnices por aglomeración de cargas balanceadas. El deshidratador reduce significativamente la humedad por debajo de 300 partes por millón (ppm) y el barniz por debajo de 20. Sin el deshidratador por vacío, la humedad aumentaría significativamente y superaría las 10,000 ppm. Los operadores han notado diariamente un fuerte olor a amoníaco proveniente del escape de la bomba de vacío del deshidratador.
Caso de estudio #3: Compresor centrífugo
El aceite en servicio de este compresor no cumplió con las especificaciones requeridas por el fabricante del equipo original (OEM, por sus siglas en inglés). Los resultados del análisis de aceite mostraron un valor RPVOT de 900, un 50 % de vida útil restante y un valor MPC de 15. La empresa realizó pruebas exhaustivas sobre la compatibilidad del aceite con la adición de un antioxidante. Los resultados de laboratorio fueron muy favorables. El antioxidante se añadió bajo la supervisión del proveedor. Se realizaron pruebas al aceite por un período de un año con resultados favorables.
Análisis
El caso de estudio #1 es un claro ejemplo de un sistema bien mantenido. El sistema está bien diseñado con metodologías de mejores prácticas. Se han eliminado las oportunidades de ingreso de contaminantes. Pero lo que es más importante, el sistema está bien mantenido. Las anomalías se abordaron oportunamente. No se requiere efectuar un reacondicionamiento. La descontaminación se ha mantenido por la filtración del sistema. La empresa ha invertido en capacitación, certificación y se ha asociado con el OEM de la turbina para el mantenimiento.
El caso de estudio #2 identifica una situación que es crónica. Otros factores desconocidos son la disponibilidad de repuestos o la disponibilidad de recursos para abordar los problemas. La situación de “extinción de incendios” es común, sin objetivos claros. Los cambios de viscosidad obligan a ejecutar periódicamente la estrategia de “endulzamiento del aceite”. No se puede considerar el reacondicionamiento ya que el aceite base se ha dañado. El equipo es el más antiguo de estos tres escenarios.
El caso de estudio # 3 identifica un problema del sistema al que se le han asignado recursos para identificar la causa raíz, con la intervención de una solución a largo plazo. El costo asociado con este proceso es considerablemente más alto que el escenario dos, pero tiene un costo de propiedad más bajo. Una vez más, es importante tener en cuenta todos los factores, incluido el contexto. La estrategia de reacondicionamiento examinó la adición de antioxidantes bajo estricta supervisión del equipo de gestión en colaboración con el proveedor. Esta estrategia aún es poco común, pero está cobrando impulso a medida que aumentan las referencias en todo el mundo. Es una opción que está disponible para la consideración de grandes usuarios de aceite para turbinas; algo que no se habría considerado hace muchos años.
En resumen, el reacondicionamiento se está volviendo visible para los usuarios de aceites de turbina. A medida que aumentan las referencias, el riesgo se reduce y los usuarios exploran sus opciones. Es obligatorio que los aceites lubricantes se analicen para garantizar que sean aptos para el reacondicionamiento, así como para garantizar que el proceso haya sido exitoso.El caso de estudio #1 es un claro ejemplo de un sistema bien mantenido. El sistema está bien diseñado con metodologías de mejores prácticas. Se han eliminado las oportunidades de ingreso de contaminantes. Pero lo que es más importante, el sistema está bien mantenido. Las anomalías se abordaron oportunamente. No se requiere efectuar un reacondicionamiento. La descontaminación se ha mantenido por la filtración del sistema. La empresa ha invertido en capacitación, certificación y se ha asociado con el OEM de la turbina para el mantenimiento.
El caso de estudio #2 identifica una situación que es crónica. Otros factores desconocidos son la disponibilidad de repuestos o la disponibilidad de recursos para abordar los problemas. La situación de “extinción de incendios” es común, sin objetivos claros. Los cambios de viscosidad obligan a ejecutar periódicamente la estrategia de “endulzamiento del aceite”. No se puede considerar el reacondicionamiento ya que el aceite base se ha dañado. El equipo es el más antiguo de estos tres escenarios.
El caso de estudio # 3 identifica un problema del sistema al que se le han asignado recursos para identificar la causa raíz, con la intervención de una solución a largo plazo. El costo asociado con este proceso es considerablemente más alto que el escenario dos, pero tiene un costo de propiedad más bajo. Una vez más, es importante tener en cuenta todos los factores, incluido el contexto. La estrategia de reacondicionamiento examinó la adición de antioxidantes bajo estricta supervisión del equipo de gestión en colaboración con el proveedor. Esta estrategia aún es poco común, pero está cobrando impulso a medida que aumentan las referencias en todo el mundo. Es una opción que está disponible para la consideración de grandes usuarios de aceite para turbinas; algo que no se habría considerado hace muchos años.
En resumen, el reacondicionamiento se está volviendo visible para los usuarios de aceites de turbina. A medida que aumentan las referencias, el riesgo se reduce y los usuarios exploran sus opciones. Es obligatorio que los aceites lubricantes se analicen para garantizar que sean aptos para el reacondicionamiento, así como para garantizar que el proceso haya sido exitoso.
Descontaminación
La descontaminación ha sido un enfoque para muchos en el pasado con gran énfasis en las tecnologías de filtración de numerosos proveedores en todo el mundo. Algunos se han beneficiado significativamente, mientras que otros se han quedado “atascados” sin objetivos claros. Algunos no comprenden los procesos y tecnologías de descontaminación disponibles.
Algunos de los contaminantes más comunes que se encuentran con frecuencia en los sistemas de aceite lubricante son agua (humedad), partículas sólidas, gases de proceso, altas temperaturas y depósitos de barniz. La presencia de estos contaminantes tiene efectos perjudiciales sobre los lubricantes y los componentes de la máquina. La mayoría de las veces, estos efectos son a largo plazo con un deterioro progresivo que puede conducir potencialmente a la falla. Sin embargo, algunas consecuencias son inmediatas y pueden ser catastróficas.
Usando las mejores prácticas, los sistemas pueden diseñarse o modificarse para excluir el ingreso de contaminantes. Entre los puntos de ingreso de contaminantes a revisar se incluyen juntas, sellos desgastados o dañados, escotillas y tuberías abiertas, mangueras sucias, recipientes de relleno sucios y aceite nuevo sucio.
Es necesario centrarse en los tipos de contaminación que hay en un sistema de aceite lubricante. En primer lugar, examine los reportes de análisis de aceite y revise cualquier anomalía. Busque cambios y tendencias en los datos (tanto crecientes como decrecientes). Si un reporte muestra advertencias de precaución o críticas, debe investigarse más a fondo. Vuelva a muestrear y vuelva a analizar el aceite lubricante. Una nueva prueba confirmará la precisión de los resultados y puede evitar acciones innecesarias.
En ausencia de reportes de análisis de aceite, tome opciones alternativas como usar sus sentidos. Esto no es de ninguna manera la mejor práctica. Use su sentido del tacto para sentir material pegajoso, delgado o sólido. Use su sentido del olfato para detectar combustible, gases de proceso, olor a quemado, desagradable o picante. Use su vista para buscar agua, espuma, burbujas de aire o una apariencia turbia u oscura.
Para contaminantes sólidos, otra alternativa es realizar una prueba de campo de membrana. Esto proporciona una excelente instantánea de los contaminantes sólidos en la muestra de aceite lubricante. Sin embargo, el conteo de partículas es la mejor práctica disponible. El conteo de partículas proporciona conteos de partículas reales por medio de los números de rango del código ISO. Esto es muy útil para seleccionar los filtros adecuados para eliminar partículas sólidas.
Una vez que se identifiquen los contaminantes, es imperativo eliminarlos lo antes posible. Los siguientes son algunos de los métodos más populares para eliminar estos contaminantes.
Agua
El agua y las partículas sólidas pesadas se asentarán naturalmente en el fondo de los depósitos. Si los resultados del análisis de aceite identifican altos niveles de humedad más allá de los límites especificados, debe reducirse. Para aplicaciones con un gran ingreso de agua, una centrífuga será muy eficaz. Sin embargo, no eliminará la humedad por debajo del punto de saturación. Es mejor eliminar la humedad lo más bajo posible. Por lo tanto, en la mayoría de las situaciones, se puede utilizar un deshidratador por vacío para eliminar grandes volúmenes de agua y cumplir con los objetivos de humedad del aceite. En la situación en la que hay una fuga de refrigerante o de vapor, la entrada de humedad puede ser continua. Deberá lograrse un equilibrio con un deshidratador por vacío para garantizar que se mantengan los límites de humedad. El aire seco y el nitrógeno son los más adecuados para mantener los aceites lubricantes con bajos niveles de humedad.
Para los deshidratadores por vacío, la tecnología ha evolucionado significativamente. La mayoría de los sistemas utilizan calentadores de baja densidad de potencia. Esto evita que los aceites lubricantes se quemen al pasar por estos calentadores. Las bombas de vacío han mejorado significativamente dando como resultado operaciones más confiables. También se han incluido sensores de espuma con controles para evitar la formación de espuma. Esto reduce el riesgo de fallas en la bomba de vacío y derrames de aceite. Se han mejorado los diseños de las cámaras de vacío, lo que ha dado como resultado una mayor eficiencia de transferencia de masa. Los deshidratadores por vacío son cada vez más confiables.
Gases
La mayoría de las veces los gases están directamente relacionados con los gases de proceso. Por lo general, se disuelven y se pueden eliminar fácilmente mediante deshidratación por vacío. Tenga en cuenta que algunos gases son peligrosos. En este caso, el escape de la bomba de vacío debe ventilarse a una antorcha.
Partículas sólidas
Las partículas se eliminan a través de medios filtrantes. La elección de los medios puede ser un desafío, ya que varían en rendimiento. Sin embargo, se debe adoptar un proceso lógico en el que se seleccionen filtros según el tipo y la cantidad de partículas que se eliminarán.
No hay un proceso simple para su selección. Sin embargo, obtenga un conteo de partículas actual con distribución de partículas por tamaño. Esto le dará una indicación del tamaño y la cantidad de las partículas.
Si la filtración está fuera de línea con fácil acceso para cambiar filtros, entonces se pueden explorar filtros de menor costo. Comience con el tamaño en micrones de las partículas que hay en más cantidad y elimínelas. Luego sustitúyalo con un filtro más fino (menor tamaño en micrones. Cambie el filtro según la presión diferencial recomendada o por el indicador del filtro. Repita el proceso hasta que el conteo de partículas sea aceptable. Esto evitará el uso de filtros más finos en micrones que normalmente son más costosos.
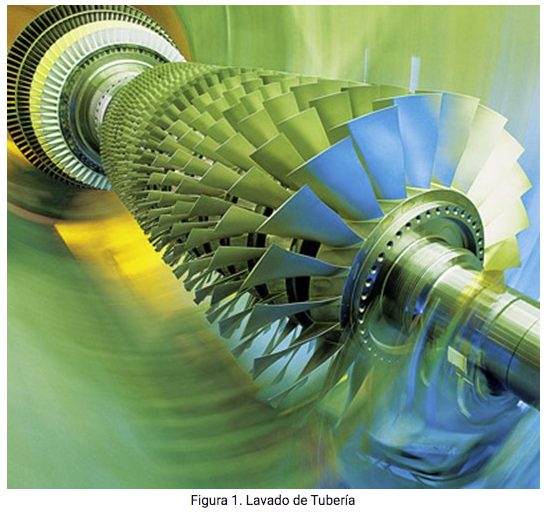
Para el lavado de tuberías, se puede usar inicialmente un cedazo o un medio de filtración de superficie para eliminar los contaminantes más grandes, seguido de una filtración estándar.
La eficiencia o tasa beta a veces no se entiende bien. Algunos fabricantes afirman que sus filtros son de alta eficiencia o de clasificación absoluta. Desafortunadamente, no existe un estándar que identifique un filtro de clasificación absoluta. La recomendación de mejores prácticas es revisar las curvas de desempeño de cada filtro. Un filtro de mayor eficiencia capturará más partículas de un tamaño específico en micrones en una sola pasada. Este tipo de filtro es necesario si los aceites lubricantes se bombearán directamente a los componentes después del filtro. No se recomiendan para sistemas de recirculación.
La capacidad de retención de suciedad se puede usar para determinar el costo de la filtración según la cantidad de filtros que se espera usar.
Alta temperatura
Para sistemas con alta temperatura, se deben revisar muchos factores. Estos incluyen el uso de análisis de vibraciones, termografía infrarroja y ultrasonido aerotransportado. Los síntomas relacionados normalmente van más allá del sistema de aceite lubricante. Sin embargo, el sistema de refrigeración se obstruye periódicamente con minerales. En este caso, se debe lavar el sistema de refrigeración.
Barniz
El barniz se ha vuelto prominente en muchos sistemas de lubricación. Existen muchos precursores para el desarrollo del barniz a partir de altas temperaturas, contaminantes y tipo de base lubricante. En muchos sistemas, los depósitos de barniz en las superficies de las máquinas se pueden identificar por una capa oscura muy delgada en las paredes del tanque, cojinetes/muñones, carretes de válvulas y filtros. Esta capa actúa como un aislante que conduce a altas temperaturas. Los efectos pueden ser devastadores. Para reducir el barniz, muchas empresas se centran en equipos para remoción de barniz. Tenga en cuenta que es posible que muchos sistemas no muestren signos visibles de barniz a menos que se apague el sistema. El barniz se puede disolver a temperaturas más altas. Cuando el sistema se apaga, el aceite lubricante se enfría y se forman depósitos de barniz en las superficies de la máquina. Deben evaluarse los sistemas diseñados para eliminar el barniz y considerarse teniendo en cuenta la temperatura. Se recomienda realizar pruebas y análisis de aceite para determinar el potencial de barniz. El barniz se puede reducir utilizando tecnologías como la aglomeración por cargas balanceadas, medios filtrantes de profundidad con celulosa comprimida y resinas de intercambio iónico. Estas tecnologías están disponibles en unidades similares a los sistemas de filtración fuera de línea.
Hoja de ruta
Se proporciona una hoja de ruta como guía para la toma de decisiones con sistemas de aceite de turbina de reservorio grande. Se proporcionan pasos tanto a corto como a largo plazo.
Corto plazo
Paso 1: Obtenga datos de análisis de aceite y determine los problemas actuales.
Paso 2: En función de los KPI existentes, determine los requisitos para abordar los problemas actuales. Estos pueden incluir el cronograma y presupuesto de operaciones, el cronograma y presupuesto de mantenimiento, los recursos requeridos y los costos asociados.
Paso 3: Obtenga e implemente los recursos relevantes. Analice el aceite y sus resultados. Repita hasta lograr los resultados deseados.
A largo plazo
Paso 4: Vuelva a evaluar los KPI existentes y los objetivos a largo plazo, como pruebas de análisis de aceite, mejores prácticas, mitigación de barniz, reacondicionamiento de aceite, filtración/deshidratación, desempeño del enfriador, reemplazo de piezas y modificaciones de la máquina. Determine los recursos necesarios para implementar las soluciones de mejores prácticas recomendadas, entre las que se pueden incluir capacitación y certificación, procedimientos estandarizados, reemplazo de piezas, modificación e implementación de las máquinas y el despliegue de estrategias de reacondicionamiento de aceite. Finalmente, busque la asignación de fondos para pruebas y análisis de aceite, incluidas pruebas de barniz, salud de aditivos y bases lubricantes.
Paso 5: Obtenga la aprobación del presupuesto.
Paso 6: Implemente los recursos.
Paso 7: Supervise y reevalúe. Revise los reportes actuales de análisis de aceite, los costos de mantenimiento y operaciones y el desempeño del programa.
Resumen
Los aceites de turbinas son fundamentales para las operaciones de las empresas. Si no se monitorean y respaldan de manera efectiva, el aumento de los costos y las fallas potenciales seguirán siendo inminentes. El análisis de aceite es fundamental para comprender la salud de los aceites lubricantes y la maquinaria. En algunos casos, la vida útil del aceite lubricante se ha agotado. En muchas aplicaciones, los aceites lubricantes se pueden recuperar mediante un análisis detallado del aceite junto con las tecnologías y soluciones disponibles en la actualidad. Es obligatorio que los usuarios de la maquinaria consideren opciones para monitorear y mantener la salud del aceite lubricante. La extensión de la vida útil y la confiabilidad de la maquinaria se lograrán y se convertirán en la nueva norma. Las empresas podrán gestionar su negocio principal con la máxima rentabilidad.
Noria Corporation. Traducido por Roberto Trujillo Corona, Noria Latín América.