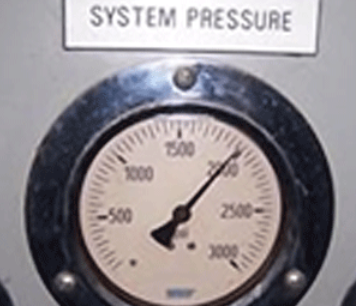
Cuando la mayoría de la gente piensa en los procedimientos de mantenimiento preventivo y confiabilidad para un sistema hidráulico, por lo regular solo se toma en consideración el cambio de los filtros y el control del nivel de aceite. Cuando la máquina falla, a menudo hay muy poca información relacionada con el sistema, cuando se busca solucionar el problema. Sin embargo, deben efectuarse inspecciones de confiabilidad con el sistema funcionando en condiciones normales de operación. Estas inspecciones son vitales para prevenir las fallas y el tiempo de inactividad del sistema.
Inspección de la válvula de derivación del filtro
La mayoría de los conjuntos de filtros hidráulicos tienen una válvula de derivación para evitar daños en caso de que el elemento filtrante se obstruya con contaminación. Esta válvula se abrirá siempre que la presión diferencial a través del filtro alcance la calibración del resorte de la válvula que, dependiendo del diseño del filtro, generalmente es de 25 a 90 libras por pulgada cuadrada(psi). Cuando estas válvulas fallan, normalmente lo hacen debido a contaminación o mal funcionamiento mecánico, lo que hace que el aceite pase en derivación por el elemento y no sea filtrado. Esto causará una falla prematura de los componentes ubicados después del filtro.
En muchos casos, esta válvula puede ser retirada del alojamiento del filtro e inspeccionada para detectar desgaste y contaminación. Consulte la documentación del fabricante del filtro para conocer la ubicación específica de esta válvula y los procedimientos adecuados de extracción e inspección. Debe ser inspeccionada periódicamente cuando se esté dando mantenimiento al conjunto del filtro.
Condición de las mangueras
La fuga de fluido es uno de los mayores problemas en un sistema hidráulico. El montaje adecuado de las mangueras y la sustitución de las que estén defectuosas es una de las mejores maneras de reducir las fugas y evitar tiempos de inactividad innecesarios, por lo que deben inspeccionarse regularmente para detectar fugas y deterioro; las que muestren desgaste en los conectores exteriores o fugas en los extremos deben ser sustituidas tan pronto como sea posible. Una manguera que tiene «ampollas» indica una falla del revestimiento interior, permitiendo que el aceite se escape a través del trenzado metálico y se acumule bajo la cubierta exterior.
Longitud de las mangueras
Siempre que sea posible, la longitud de la manguera no debe exceder de 1.2 a 1.8 metros. La longitud excesiva aumentará la posibilidad de que roce contra otras mangueras, un conducto o un bastidor, causando su falla prematura. Además, cuando se produce un pico de presión en el sistema, la manguera puede absorber parte del choque, cambiando ligeramente la longitud. La manguera debe hacerse lo suficientemente larga para que tenga una ligera curva donde se absorban estos picos de presión.
Ubicación de la manguera
Siempre que sea posible, las mangueras deben posicionarse de manera que se evite el rozamiento entre ellas. Esto evitará la falla prematura de la cubierta exterior. En caso de que no sea posible acomodarlas para evitar el roce, se deben usar cubiertas o mangas protectoras. Existen varios tipos de mangas para este propósito; también pueden hacerse utilizando una manguera vieja del largo apropiado, cortándola longitudinalmente para colocarla en los puntos de rozamiento de la manguera que desea proteger. También se deben utilizar abrazaderas o amarres de plástico para sujetar las mangueras y evitar el movimiento relativo de estas en los puntos de roce.
Compruebe que la abrazadera sea la correcta
Se deben usar abrazaderas adecuadas para tubería hidráulica. Las abrazaderas para tubo conduit generalmente no son aceptables para las líneas hidráulicas debido a los picos de vibración y presión inherentes a un sistema hidráulico. Deben inspeccionarse regularmente para detectar pernos de montaje sueltos, las que estén rotas deben sustituirse; además, deben estar bien espaciadas. Una regla de oro es separar las abrazaderas aproximadamente entre 1.5 a 2.5metros una de otra y dentro de 0.15 metros del extremo donde termina el tubo.
Mantenimiento e inspección del respirador
Los respiradores son algunos de los elementos más olvidados en un sistema hidráulico, tenga presente que el respirador es en realidad un filtro. El nivel de aceite del depósito cambia constantemente a medida que los cilindros se extienden y se retraen, y el respirador (filtro) es la primera línea de defensa contra la contaminación. Para evitar que la contaminación entre en el depósito desde el exterior, debe usarse un filtro respirador adecuado, con la capacidad de filtración apropiada. Varios fabricantes ofrecen respiradores en el rango de 3 micrones y que además eliminan la humedad (agua) del aire por medio de materiales desecantes. El desecante cambia de color cuando se satura con humedad. Estos respiradores se pagan por sí solos muchas veces cuando se cambian regularmente porque evitan la degradación del lubricante y el desgaste de los componentes.
Medición del consumo de corriente del motor de accionamiento
La cantidad de potencia necesaria para accionar una bomba hidráulica depende de la presión y el flujo del sistema. A medida que la bomba se desgasta, el bypass interno aumenta debido al incremento de las holguras internas. Esto da como resultado una reducción en el flujo de la bomba, disminuyendo proporcionalmente la potencia necesaria para accionarla. Por lo tanto, disminuirá el consumo de corriente del motor de accionamiento. Debe hacerse un registro del consumo de corriente cuando el sistema es relativamente nuevo para establecer una línea de base de referencia.
Inspección de temperatura
A medida que los componentes del sistema se desgastan, las holguras internas aumentan. Esto conduce a un aumento de la derivación, lo cual genera calor. Este calor no hace ningún trabajo útil en el sistema; por lo tanto, se desperdicia energía. Empleando una cámara infrarroja o algún otro tipo de dispositivo de detección de calor, puede identificarse esta derivación. Tenga en cuenta que cada vez que ocurre una caída de presión se genera calor, por lo que siempre existirá calor localizado en cualquier dispositivo medidor de flujo, como un control de flujo o válvula proporcional. La comprobación regular de la temperatura del aceite a la entrada y salida de los intercambiadores de calor dará una indicación general de su eficiencia.
Inspección de sonido
Debe efectuarse una revisión regular de sonidos en el sistema, especialmente en las bombas hidráulicas. La cavitación se produce cuando la bomba no puede obtener todo el volumen de aceite que está pidiendo en el puerto de succión. Esto produce un sonido constante y agudo. Si no se corrige, la bomba generará un flujo reducido a la salida hasta que se destruya a sí misma. La causa más común de cavitación es un cedazo de succión obstruido. También puede deberse a una excesiva viscosidad del aceite (baja temperatura) o a un número excesivo de revoluciones por minuto (rpm) del motor de accionamiento. La aireación se produce cuando el aire del exterior ingresa por alguna conexión en la línea de succión de la bomba, lo que producirá un sonido más errático. Entre las causas de la aireación están una fuga de aire en la línea de succión, un bajo nivel de fluido o un sello de eje defectuoso en una bomba de desplazamiento fijo.
Inspección de presión
Regularmente deben efectuarse inspecciones de la presión. Esto dará una indicación de la condición de varios componentes en el sistema, tales como acumuladores y varias válvulas de control de presión. Si la presión cae más de 200 psi mientras los actuadores se mueven, puede indicarnos un problema. Debe hacerse un registro de las presiones cuando el sistema está funcionando normalmente para establecer una línea de base de referencia.
Noria Corporation. Traducido por Roberto Trujillo Corona, Noria Latín América.