Los acoplamientos de engranajes están entre los métodos más utilizados para conectar equipos de proceso. Cuando se seleccionan, instalan y mantienen apropiadamente, pueden proveer larga vida y buena confiabilidad. Los acoplamientos de engranajes brindan varias ventajas con respecto a otros tipos de acoplamientos, entre las cuales están una capacidad moderada de desalineamiento, excepcional rigidez torsional y muy alta densidad de torque.
Sin embargo, cuando se trata de lograr su confiabilidad, hay muchas áreas por donde pueden iniciar las fallas. Con frecuencia esas fallas comienzan por una falta de entendimiento o por una deficiente ejecución de ciertos principios, que son necesarios para que dichos acoplamientos operen confiablemente.
Diseño, selección y dimensionamiento
La correcta selección del acoplamiento de acuerdo a su aplicación es un aspecto crítico para su confiabilidad. Para facilitarlo, siga los siguientes pasos:
- Elija el tipo de acoplamiento y su diseño (Fast´s, serie H o Waldron; rígido o flexible; eje flotante o acoplado; especificaciones de los dientes de engranes y requerimientos de desalineamiento).
- Seleccione el factor de servicio (SF) de acuerdo con las tablas del fabricante original (OEM) del acoplamiento de engranajes. Las cargas de choque o cargas variables pueden causar falla prematura si no se utiliza el SF adecuado. Los factores típicos de servicio están en un rango de entre 1.5 y 2.0. Algunos fabricantes pueden especificar un factor de desalineamiento al dimensionar el acoplamiento cuando se espera que exista este.
- Calcule los requerimientos de torque de la aplicación con base en el diseño de potencia de freno (BHP), SF y velocidad.
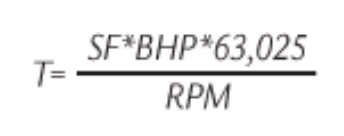
4. Seleccione un acoplamiento con una capacidad de torque mayor que la requerida. Puesto que el factor de servicio ya ha sido tomado en cuenta, no hay razón para añadir capacidad adicional.
5. Confirme que el acoplamiento seleccionado tenga un diámetro interno mayor que el diámetro de la aplicación (diámetro del eje). Frecuentemente la dimensión del diámetro máximo definirá el proceso de dimensionamiento del acoplamiento e incluso incrementar su capacidad de torque dos o tres veces la calculada previamente.
6. Verifique la profundidad disponible del núcleo del acoplamiento y compárelo con la profundidad real. Si el núcleo es muy profundo, debe maquinarse o dejarse en cantiléver. Dado que la conexión entre el núcleo y el eje es la misma en cualquiera de los métodos, es preferible maquinar el núcleo debido a los efectos de torsión que se presentan si se tiene el eje en cantiléver. De cualquier manera, se requiere efectuar una inspección adicional para determinar si hay suficiente capacidad de transmisión de torque disponible. La regla general es una relación de 1 a 1 entre la longitud del núcleo y el diámetro.
7. Revise la gráfica de equilibrio dinámico para ver si el acoplamiento necesita ser balanceado. Los acoplamientos de engranajes de alta velocidad requieren balanceo.
8. Asegúrese de que el acoplamiento y la guarda de protección sean de fácil acceso. Por lo general esto puede ser un problema cuando se requiere efectuar alguna modificación en el diseño de los equipos existentes. Las guardas de protección que permiten la mantenibilidad fomentarán el mantenimiento adecuado a largo plazo.
Instalación
Algunos acoplamientos no tienen oportunidad de tener una vida decente debido a su instalación. De la misma forma en que otros componentes sufren de mortalidad infantil, estas partes no mueren, sino que son asesinadas. Deben tomarse en cuenta ciertos elementos en la instalación de acoplamientos de engranajes si se quiere obtener una confiabilidad óptima, entre los cuales están:
- Ajuste del eje y cubo – Determine el tipo de ajuste del cubo (holgura, conicidad e interferencia). Aplicaciones de alta velocidad deben tener un ajuste de interferencia adecuado para compensar los efectos de las fuerzas centrífugas en las presiones de contacto entre el eje y el cubo. Un exceso de ajuste en la interferencia del cubo puede provocar agrietamiento y falla del cubo.
- Ajuste de la cuña y cuñero – El cuñero debe tener un radio adecuado para reducir el riesgo de ruptura por fatiga. Debe medirse la longitud de la cuña para minimizar el desbalanceo del acoplamiento.
- Espesor del cubo – Verifique que el ajuste del cubo sea concéntrico para asegurar un buen patrón de contacto.
- Instalación del núcleo – Seleccione métodos adecuados de calentamiento para que las propiedades del material del núcleo no se vean comprometidas y elija la temperatura correcta para el ajuste de la interferencia de manera que el núcleo se deslice fácilmente en el eje. Nunca emplee martillos para instalar o remover los núcleos, ya que esto puede dañarlos.
- Espaciador correcto – Si los ejes flotantes del acoplamiento tienen un pequeño espaciador, los ejes pueden impactar entre sí cuando existe desalineamiento conforme el eje oscila durante la operación.
- Sellado apropiado – Utilice siempre juntas y O-rings para que el lubricante permanezca dentro del acoplamiento.
- Alineación – Instale el acoplamiento de manera que el dealineamiento se mantenga dentro de los límites establecidos por el fabricante respecto al desalineamiento angular, axial y lineal.
- Ensamble del sujetador – Seleccione el tipo correcto de sujetador (fino o burdo, longitud, expuesto, envuelto, etc.) y el arreglo apropiado. Aunque los birlos estándar pueden funcionar, las cuerdas de estos pueden introducirse en el plano de corte. Los birlos del acoplamiento necesitan contar con la precarga correcta, lo cual puede lograrse empleando métodos de torque apropiados.
- Lubricación – Coloque el producto correcto en la cantidad correcta con la frecuencia correcta para una óptima confiabilidad del acoplamiento.
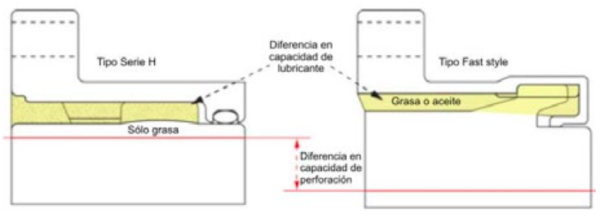
Diferentes tipos de acoplamientos tienen diferentes espesores y capacidades de lubricante. (Ref. Kop ex)
Lubricación
Quizás el factor de operación más importante en un acoplamiento de engranes para que éste sea confiable es su lubricación. El primer paso es la selección del lubricante correcto. Muchos fabricantes de acoplamientos proveen sus propios lubricantes. Los acoplamientos de engranes, dependiendo de su diseño, pueden ser lubricados por grasa o aceite. Los que son lubricados por aceite no tienden a resecarse como los acoplamientos lubricados por grasa. Los acoplamientos Fast-style tienen menor capacidad interna.
Se puede decir que la mayoría de los acoplamientos son lubricados por grasa. Las grasas para estos acoplamientos tienen propiedades especiales, por lo que las grasas de propósitos generales (multi- propósitos) nunca deben emplearse en acoplamientos de engranes. Estos acoplamientos pueden estar sujetos a muy altas fuerzas centrífugas y la separación del aceite es un elemento crítico de las grasas para acoplamientos. Como las grasa están compuestas principalmente de aceite y un espesante, la selección y aplicación de las grasas deben hacerse tomando consideraciones especiales.
Los espesantes de base jabonosa son más pesados que los aceites, por lo que las fuerzas centrifugas tienden a depositar el espesante en los dientes de los engranes. Por lo general, se pre ere emplear una grasa que contenga un alto contenido de aceite de alta viscosidad y consistencia grado 1 de acuerdo con el Instituto Nacional de Grasas Lubricantes de los Estados Unidos (NLGI, por sus siglas en inglés). Para aplicaciones de alta velocidad, debe considerarse el uso de una grasa de alta consistencia, pero debe evitarse esta en aplicaciones de baja velocidad.
Las especificaciones de grasas deben incluir los límites de velocidad o ciertos ensayos como el factor de separación K36. Cualquier grasa separará el aceite dependiendo del tiempo, temperatura y fuerza centrífuga. El factor K36 determina la máxima separación del aceite de la grasa mientras opera a 36,000 G’s. UN factor K36 de 8/24 significa que la separación del aceite fue de 8% en 24 horas. En comparación, una grasa con un factor K36 de 3/24 significaría que esta no separó tanta grasa como aquella con un factor K36 de 8/24.
En bajas velocidades es deseable tener una alta separación de aceite (menores fuerzas G), mientras que se prefiere una baja separación de aceite en altas velocidades y altas temperaturas. Una alta vibración en la máquina también puede fomentar la separación del aceite e inducir a la falla. Algunos estudios han demostrado que las tasas de desgaste de los acoplamientos disminuyen cuando se reduce su velocidad de operación.
La principal función de un lubricante en un acoplamiento de engranes es reducir la fricción entre los dientes de los engranes conforme se deslizan entre sí. El movimiento relativo entre la superficie de los dientes se presenta en dirección axial debido a un ligero desalineamiento del eje. Este movimiento es oscilatorio, de baja amplitud, de relativamente alta frecuencia y está en función de la magnitud del desalineamiento angular.
El movimiento deslizante axial entre los dientes de los engranes puede generar gran cantidad de desgaste si la lubricación es insuficiente. Esta es la razón por la que los lubricantes de acoplamientos juegan un rol muy crítico en la confiabilidad y vida de un acoplamiento de engranes. Una pobre lubricación entre los dientes de los engranes genera alta fricción entre ellos, dando como resultado el desgaste de los acoplamientos, generación de calor y altas cargas axiales que actúan sobre los rodamientos. Mientras mayor es la carga axial sobre los rodamientos más disminuirá la vida de la máquina.
La bomba en la imagen muestra un acoplamiento sin nada de lubricante y estaba en operación bajo una condición de bajo torque y creando altas fuerzas axiales en la máquina. El acoplamiento se sustituyó sin hacer ajuste alguno a la bomba o al motor. El único cambio fue la instalación de un acoplamiento con buena lubricación, el cual redujo la fricción del diente y disminuyó las fuerzas axiales desde el acoplamiento hacia la bomba y motor. El resultado fue una notable disminución de la temperatura en el rodamiento de la bomba.
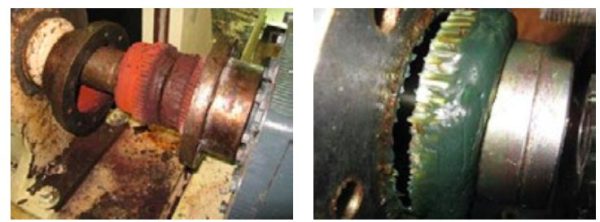
Mantenimiento
El mantenimiento es el factor final para asegurar la confiabilidad del acoplamiento de engranes para una larga vida de la máquina. Mientras que los primeros tres factores tienen que ver más bien con la falta de conocimiento, el mantenimiento con frecuencia tiene que ver con falta de ejecución. Desafortunadamente, este requiere disciplina por parte de los grupos de mantenimiento y operaciones, así como el compromiso de la dirección para dedicar los recursos necesarios para asegurar que esto pueda darse.
Las recomendaciones típicas de parte de los fabricantes de acoplamientos indican que se debe re-engrasar al menos cada 12 meses. Un procedimiento típico debería incluir el desarmado, limpieza, inspección y empacado manual del acoplamiento con grasa nueva. Por lo general no se recomienda el empleo de una pistola manual de engrasar cuando el acoplamiento se ha desarmado y está listo para recibir la grasa nueva. Cuando se engrasa a través de una grasera en lugar del empacado manual, puede presentarse sobre-engrasado, y podría ocurrir una condición de bloqueo hidráulico, lo que causaría generación de elevadas fuerzas axiales en el equipo. Una condición de bloqueo hidráulico puede incluso dificultar el alineamiento, ya que el eje podría volverse difícil de mover.
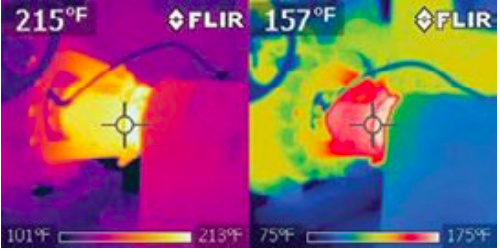
Algunas aplicaciones requieren ser engrasadas cada seis meces para asegurar buena confiabilidad. Entre ellas están aplicaciones de alta velocidad (elevadas fuerzas G), altas temperaturas, desalineamiento y vibración. Otro factor a considerar para ajustar los intervalos de re-engrase es el tamaño del alojamiento para contener lubricante. Sin embargo, la decisión de exceder de 12 meses sin rellenar con grasa nueva un acoplamiento de engranes es una condición de alto riesgo que no se recomienda.
El mantenimiento regular de acoplamientos de engranes debe involucrar cuidados especiales para todos los factores discutidos previamente. Al inspeccionar juntas y O-rings, asegúrese de que el lubricante permanezca dentro del acoplamiento hasta la siguiente actividad programada de mantenimiento. Deben removerse las graseras al concluir las labores de mantenimiento. Se ha sabido de casos en que el lubricante se fuga por ellas y además pueden golpear las guardas de protección causando pérdida del lubricante. Bajo elevadas fuerzas centrífugas, debe asegurarse que la grasa quede sellada completamente dentro del acoplamiento. Las guardas deben permitir suficiente acceso de forma que no tengan que removerse por completo para el mantenimiento normal del acoplamiento.
Recuerde que la confiabilidad no es apta para cardiacos. La mayoría de esos factores deben ejecutarse correctamente para alcanzar una buena confiabilidad de acoplamientos. Esta es la razón por la que el trabajo de los profesionales del mantenimiento y confiabilidad rara vez se acaba.
Noria Corporation. Traducido por Roberto Trujillo Corona, Noria Latín América.