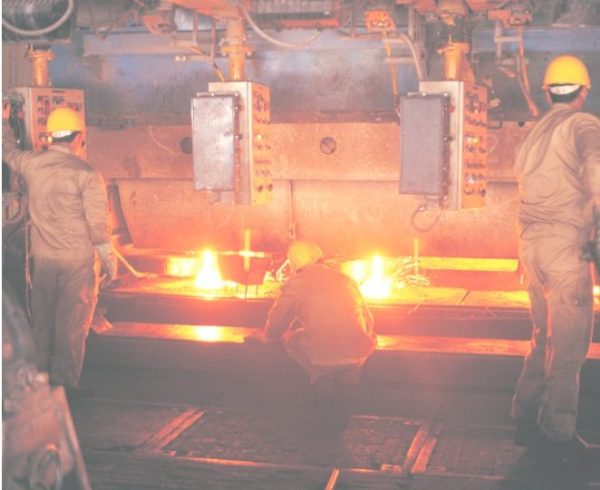
Con frecuencia se habla de los métodos de mantenimiento preventivo, pero rara vez se ponen en práctica. Este artículo intentará alentar un cambio de paradigma en la forma de pensar del mantenimiento, haciendo que la prevención impulse la mayoría de las actividades. El factor principal está en el liderazgo y no simplemente en la administración.
Liderazgo vs. Administración
La definición clásica de administración es hacer las cosas bien. La definición de liderazgo es hacer las cosas correctas. La diferencia puede ser sutil pero muy importante. ¿Cuántas veces ha presenciado que alguien planifica un trabajo de reparación para que se complete dentro de un período de tiempo asignado, pero nadie se pregunta por qué esta reparación se debe realizar con tanta frecuencia?
Un gerente intenta hacer el trabajo a tiempo, mientras que un líder intenta minimizar o eliminar el trabajo requerido. Un gerente continuamente solicita más personas, mientras que un líder intenta maximizar la efectividad de su personal. Un gerente aborda los problemas a medida que llegan, mientras que un líder pregunta por qué se toleran los problemas recurrentes.
La prevención depende del liderazgo
Sin un liderazgo adecuado, es muy difícil lograr la prevención de problemas. Los siguientes casos de estudio ilustran diversas situaciones en las que las técnicas preventivas se usaron de manera efectiva en el entorno típico de una planta.
Sistema hidráulico mal diseñado
En una siderúrgica, las láminas de acero que salen de la máquina de colada comienzan como una larga tira de metal caliente, en forma continua. Un cortador de soplete las cortaba en tramos de 9 metros a medida que la tira se movía a un ritmo lento. Posteriormente, las láminas eran levantadas de la mesa de rodillos y apiladas en un patio de almacenamiento para ser entregadas al transportista. Las tenazas empleadas para esta tarea parecían dos pares de tijeras gigantes de 3 metros operadas por cilindros hidráulicos y alimentadas por un sistema hidráulico montado cerca de la parte superior de las tenazas.
El sistema tenía un tanque vertical con una bomba montada a un costado. Debido a las limitaciones de espacio, las válvulas, los tubos y las mangueras se ubicaron directamente sobre la bomba y el motor, creando un diseño muy congestionado. Todo el ensamble colgaba de una grúa. Cuando un sello tipo O-ring o una válvula necesitaba cambiarse, se requería desarmar bastantes cosas para acceder a la parte defectuosa. También se desperdiciaba mucho tiempo en las reparaciones de este equipo debido a su diseño.
La causa del problema era obvia y solo podría resolverse mediante un rediseño. Se contactó al proveedor de las tenazas y se le dijo que el diseño del sistema era inadecuado. Empleando la tecnología de distribuidores hidráulicos (manifold), podrían eliminarse la mayoría de las tuberías, tubos y mangueras, así como la congestión en los espacios confinados. El proveedor acordó rediseñar esta parte del sistema, lo que resolvió el problema. Este caso ejemplifica un problema único en donde la prevención de problemas futuros era la única opción. Aprender a vivir con el problema no era una alternativa.
Ineficaz compra de lubricantes
En esta misma siderúrgica, los lubricantes y fluidos hidráulicos eran comprados por departamentos independientes, sin una coordinación entre ellos. En consecuencia, la cantidad de marcas proliferó, aumentando las posibilidades de duplicidad. Los productos se adquirían por su nombre, y el departamento de compras no tenía más remedio que comprar lo que se solicitaba. Debido a que los lubricantes eran comprados a una marca que no tenía competencia, se sospechaba que los precios eran excesivos. Cuando surgía algún problema, se culpaba a la calidad del lubricante y se recurría a otro proveedor para resolverlo.
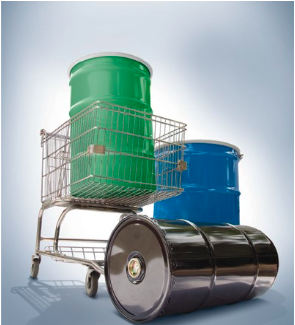
Se sospechaba que la compañía vivía con un problema que podía resolverse. Empleando pruebas ASTM y otros métodos se puede determinar la calidad del lubricante, por lo que se formó un comité para decidir cómo comprar lubricantes con base en estas pruebas. Pronto se desarrolló una estrategia: todos los lubricantes serían analizados en parámetros importantes para identificar duplicados, los productos se separaron por categorías tales como fluidos hidráulicos minerales, fluidos hidráulicos resistentes al fuego, grasas de uso general, grasas para motores eléctricos, aceites minerales para turbinas, aceites para engranajes, aceites para rodamientos, aceites minerales de circulación y aceites sintéticos.
También se escribieron las especificaciones técnicas para cada tipo de lubricante según los resultados de las pruebas de los grados más altos en cada categoría. A cada especificación se le asignó un número único, y todos los puntos de lubricación de la maquinaria de toda la planta se marcaron con el número del producto que le correspondía.
Se enviaron las especificaciones a varios proveedores para que presentaran sus ofertas. El mejor postor se adjudicó el negocio por un año. Los precios eran notoriamente más bajos, comparados contra los de la otra marca.
Después de que se completó la etapa inicial, el sistema comenzó a funcionar bien. El inventario se redujo porque muchas máquinas usaban los mismos tipos de lubricantes. Se hizo posible comprar a granel gracias a la consolidación, que también resultó en una reducción de costos y en el número de tambores. Periódicamente se tomaban muestras de los lubricantes que se recibían para garantizar la calidad. Poco a poco mejoró la calidad en general.
El objetivo del sistema era comprar productos de alta calidad al menor costo posible y eliminar los tambores vacíos tanto como fuera posible. También se redujeron los errores relacionados con la aplicación de lubricante incorrecto. Una vez que el sistema se implementó completamente, mantenerlo fue muy simple.
Este fue un ejemplo de una planta que vivía con un problema que no muchos pensaban que fuera un problema. Fue solo después de hacer un profundo análisis que la mayoría se convenció de que había una mejor manera de hacer las cosas. La forma en que la planta compraba lubricantes costaba mucho más de lo necesario, tanto en dólares como en mano de obra.
Corta vida de los rodamientos del motor
En esta planta siderúrgica, cuando el cordón de acero sale del último módulo de acabado, un largo transportador de rodillos lo mueve a gran velocidad hacia los enrolladores. Cada rollo es accionado individualmente por un motor eléctrico. Los aspersores dejan caer chorros de agua para enfriar el cordón a medida que avanza hacia los enrolladores. A pesar de las elaboradas protecciones contra salpicaduras, es casi imposible mantener el agua fuera de los ejes del motor. Los sellos del eje no eran adecuados para mantener el agua fuera de los motores. Se probaron diferentes diseños de sellos, pero no fue de ayuda. El taller de reparación de motores apenas podía seguir el ritmo de las frecuentes fallas.
Finalmente, una compañía de sellos recomendó añadir deflectores al eje. Estos dispositivos consistían en una goma que se parecía mucho al sello del eje, pero con un agujero en el centro ligeramente más pequeño que el diámetro del eje. Cuando se reparaba un motor y estaba listo para ser enviado a operar, se deslizaba un deflector en el eje hasta hacer contacto con la carcasa. Cuando el motor se instalaba en este ambiente húmedo, cualquier cantidad de agua que pasara hacia el área del sello era expulsada gracias al deflector giratorio. De esta forma, el agua no podía llegar al sello. La vida del rodamiento del motor aumentó considerablemente. En este caso, se evitó un problema grave con un dispositivo simple, pero fue solo después de que alguien preguntó por qué se toleraba esto.
Reparaciones frecuentes de servo-válvulas
A medida que la tecnología de la planta siderúrgica mejoraba, se usaban cada vez más servo-válvulas en los sistemas hidráulicos de la planta para ganar precisión. Debido a su sensibilidad a los contaminantes, el aceite en los sistemas con servo-válvulas se debe filtrar a niveles de limpieza extrema. A pesar de los grandes esfuerzos, las fallas de servo-válvulas se estaban volviendo excesivas. Los costos también eran altos, ya que las reparaciones no podían hacerse dentro de la misma planta.
Para evitar estas fallas, se instaló un filtro dúplex sin derivación separado por una válvula de tres vías con una alarma eléctrica antes de cada válvula. Los filtros tenían un enfoque de tamaño de partícula de 1 a 2 micrones. Cuando sonaba la alarma, el personal de mantenimiento sabía que disponían de solo unos minutos para accionar la válvula de tres vías al lado limpio antes de que el sistema se apagara automáticamente. Siempre estaba un filtro limpio nuevo en reserva para utilizarse. El resultado fue que las fallas de las servo-válvulas prácticamente cesaron.
Una vez más, un simple cambio de diseño evitó un problema grave. Sin embargo, la diferencia con el problema de las servo-válvulas era que tanto la producción como los costos de reparación se afectaban considerablemente.
Pérdidas de aceite excesivas
Las pérdidas de aceite estaban volviéndose excesivas en los sistemas hidráulicos y de lubricación de la planta. Los operadores de los molinos mantenían diligentemente los sistemas llenos y operando, pero no informaban todas las adiciones de aceite que efectuaban. Cuando se informaba que se habían hecho reposiciones de aceite, no había
un buen método para determinar la cantidad. Por lo tanto, era difícil establecer dónde estaban las fugas y programar las reparaciones requeridas. El objetivo era prevenir o reducir estas pérdidas de aceite, pero solo podían ser atacadas cuando ocurrían.
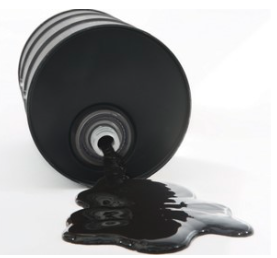
Se tomó la decisión de montar pequeños medidores de agua en las líneas de llenado de cada sistema. Estos medidores generaban un poco de fricción interna, pero dado que el aceite que se bombeaba era para reposición de nivel, la presión requerida era adecuada. En los casos en que el aceite fluía por gravedad desde un piso superior a uno inferior, se requirió de medidores de baja fricción. Cada día, un inspector leía los medidores para determinar si alguna fuga no había sido denunciada. Si era así, se tomaban medidas. Este fue un ejemplo de toma de medidas preventivas (lectura de medidores) para evitar pérdidas de aceite. No se podía efectuar ninguna acción sin la adecuada información que proporcionaban los medidores.
Motores que se quemaban rápidamente
Las puertas del horno de coque de la planta miden aproximadamente 6 metros de alto y 1.20 metros de ancho. Están hechas de acero, forradas con ladrillo refractario y pesan alrededor de 450 kg. Cada una está montada verticalmente en cada extremo del horno y debe ser levantada por una máquina enorme para que pueda ser expulsado el coque candente. Las puertas se mantienen en su lugar por dos brazos de acero que rotan en su sitio, por detrás de las columnas verticales de anclaje.
En el centro de los brazos hay una tuerca hexagonal de 5 pulgadas de diámetro. Los brazos son rotados con un acople grande que se ajusta a la tuerca hexagonal y son accionados por un motor y una caja de engranajes montados en la máquina. Con frecuencia los brazos quedan atrapados detrás de las columnas de anclaje, por lo que un electricista debe accionar los relés de sobrecarga para que el motor gire. Debido a esta práctica, frecuentemente se quemaban los motores.
En lugar de aumentar el tamaño y capacidad de los motores, se tomó la decisión de convertir la operación a motores hidráulicos, por la inherente protección por sobrecarga de estos sistemas. El ajuste de la válvula de alivio sirve para este propósito.
Debido a la gran cantidad de suciedad propia de la planta de coque y la sensibilidad a la suciedad de los motores hidráulicos, se rediseñaron los sistemas hidráulicos. Este rediseño fue tan exitoso que no se produjeron fallas en los motores hidráulicos durante los primeros cinco años. La mejora en el nivel de limpieza del fluido también aumentó la vida útil de la bomba. Este caso es un ejemplo de prevención que involucró un cambio radical de diseño con el que no todos estaban de acuerdo.
Falta de medición de temperatura del aceite
En otra siderúrgica en el área de Pittsburgh, el reto fue determinar la causa de la pérdida de varios rodamientos de los soportes. Parecía ser un caso de sobrecalentamiento del aceite, pero cuando se examinaron los sistemas de enfriamiento, ninguno de los termómetros estaba funcionando. Era evidente que nadie estaba revisando los parámetros clave del sistema, como la temperatura, contenido de agua, flujo, niveles de aceite en el tanque y los niveles de limpieza.
Cuando se cambiaron los termómetros, se observaron temperaturas del aceite de 80 ºC (175 ºF). Evidentemente, los enfriadores no estaban siendo efectivos; una vez que estos se sustituyeron, el problema cesó.
Este fue un caso de falta de atención a las señales que pueden advertir sobre problemas inminentes. La administración implementó inmediatamente un formulario de inspección para que se completara en cada turno, obligando a alguien a observar esos importantes parámetros del sistema.
Demulsibilidad del aceite mal reportada
El aceite utilizado en el sistema de rodamientos de los soportes del molino necesita separar el agua rápidamente. Las especificaciones de compra establecían un número muy estricto que tenía que medirse mediante la prueba ASTM D-2711. Otra prueba para evaluar la demulsibilidad es la ASTM D-1401, pero esta se usa para aceites de baja viscosidad. Los aceites de mayor viscosidad utilizados para estos soportes tenían que ser analizados con la primera prueba, aunque tomaba mucho más tiempo que la prueba ASTM D-1401.
Se estaba experimentando un aumento en los niveles de agua en muestras analizadas de los lotes de aceite nuevo. Las muestras tomadas del aceite en servicio tenían el mismo problema. En condiciones normales, los niveles de agua deberían haber permanecido por debajo del 5 por ciento, pero ahora eran del 20 por ciento. El laboratorio aseguró a la fábrica que las muestras de aceite nuevo estaban dentro de la especificación. Como esta situación continuó por varios meses, se llevó a cabo una investigación. Había una preocupación de que pronto comenzaran a aumentar las fallas en los soportes.
Por suerte, el laboratorio cerró, lo que significaba que la planta tenía que encontrar otro. Cuando se envió la siguiente muestra al nuevo laboratorio, se recibió de inmediato una llamada indicando que la demulsibilidad estaba fuera de las especificaciones. Se drenó el aceite del sistema y se sustituyó por una carga de aceite de otra marca. Resultó que el laboratorio anterior había estado usando la prueba ASTM D-1401 porque era más rápida que la prueba ASTM D-2711, pero no lo informó a la planta. El proveedor de aceite ni siquiera tenía el equipo para realizar la prueba D-2711, pero confiaba en que su proveedor de aditivos le hubiera proporcionado el porcentaje correcto a usar. Este fue un caso de tener disponibles todas las herramientas necesarias, pero aún así obtener información incorrecta.
Tres fases de prevención
Estos casos de estudio abarcan acciones preventivas para tres tipos de situaciones: una situación visible, una situación de cambio de métodos y una situación invisible. A continuación, se describe cada uno de ellos:
Una situación “visible”
Estas situaciones son como el caso del sistema hidráulico mal diseñado o el problema del rodamiento del motor eléctrico. El problema es muy costoso y la solución está a la vista, o se requiere un cambio de diseño. La solución también requiere tiempo, dinero y la voluntad de hacerlo. La mayoría estará de acuerdo en que vale la pena intentar resolver el problema, ya que es fácilmente visible. Estas situaciones generalmente se designan como «crisis». La alternativa es aprender a vivir con el problema.
Una situación de cambio de métodos
Estas situaciones implican una forma tradicional de hacer las cosas, por ejemplo, que cada departamento compre sus lubricantes sin intentar efectuar una consolidación, o que no se informen los volúmenes de aceite añadidos a un sistema. Aunque se ven los problemas, no todos visualizan una solución o no están de acuerdo en que se necesita. El personal ha aprendido a vivir con el problema. Básicamente, debe cambiarse la forma en que se hacen las cosas.
Una situación "invisible"
Muchas veces se pueden tomar medidas para evitar que sucedan cosas malas. Entre ellas se incluye el monitoreo de condición, inspecciones regulares, monitoreo frecuente de los medidores del sistema y muestreo de aceite para efectuar análisis en laboratorio. Cada sistema en planta tiene parámetros que deben verificarse periódicamente. Estas verificaciones consisten en personas que realizan una evaluación de la condición y el llenado de informes precisos. Cuando estas personas hacen su trabajo correctamente, se previenen las cosas malas.
Los gerentes miopes solo «ven» a las personas que reparan cosas. Quienes están enfocados en la prevención trabajan en un ambiente menos dramático. En consecuencia, cuando la economía es mala, a menudo estos trabajos son eliminados.
Los líderes no solo deben garantizar que lo «visible» se maneje de manera eficiente, sino también que lo «invisible» no se descuide. Lo «invisible» generalmente requiere reconocer las señales de cosas malas que están por suceder, que a menudo se pueden identificar por medio de inspecciones regulares empleando los sentidos, la vista, el tacto, el olfato o el oído. Sin embargo, la mayoría de lo «invisible» debe ser detectado por algún equipo, incluyendo pruebas de temperatura, vibración, sonido y de laboratorio.
Lo «invisible» también implica la convicción de que la tecnología se puede usar para predecir eventos a fin de evitarlos o planificarlos. Esta convicción es un atributo importante de liderazgo. Recuerde, los administradores no ven lo «invisible», pero los líderes sí.
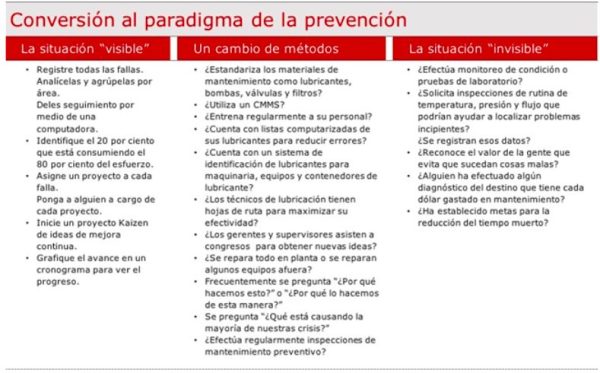
Noria Corporation. Traducido por Roberto Trujillo Corona, Noria Latín América.