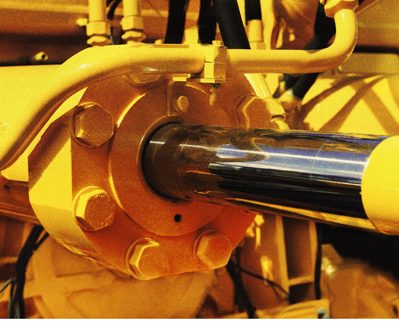
Ahora que el clima es cada día más frío, es posible que no esté demasiado preocupado por el aumento de la temperatura del aceite, pero el hecho es que cualquier sistema hidráulico industrial que funcione a más de 60 ºC (140 ºF) está demasiado caliente. Tenga en cuenta que por cada aumento de 10 ºC (18 ºF) en la temperatura de operación por encima de los 60 ºC, la vida del aceite se reduce a la mitad. Los sistemas que operan a altas temperaturas pueden producir lodo y barniz, lo que provoca que los carretes de las válvulas se atasquen.
Las bombas y los motores hidráulicos pasan más aceite en derivación (bypass) a altas temperaturas, haciendo que la máquina funcione a una velocidad más lenta. En algunos casos, las altas temperaturas del aceite pueden desperdiciar energía eléctrica haciendo que el motor de accionamiento de la bomba consuma más energía para operar el sistema. Las juntas tóricas (O-rings) también se endurecen a temperaturas más altas, lo que genera más fugas en el sistema. Entonces, ¿qué controles y pruebas debe realizar si la temperatura del aceite es superior a 60 grados Celsius?
Causas de generación de calor
Cada sistema hidráulico genera una cierta cantidad de calor. Aproximadamente el 25 por ciento de la potencia eléctrica de entrada se utiliza para compensar las pérdidas por calor en el sistema. Cada vez que pasa aceite al depósito sin realizar algún trabajo útil, se genera calor.
Las tolerancias dentro de las bombas y las válvulas son normalmente de diez milésimas de pulgada. Estas tolerancias permiten que una pequeña cantidad de aceite pase en derivación continuamente algunos componentes internos, haciendo que la temperatura del fluido aumente. Cuando el aceite fluye a través de las tuberías, se encuentra una serie de resistencias. Por ejemplo, los controles de flujo, las válvulas proporcionales y las servoválvulas controlan la velocidad de flujo del aceite restringiendo el flujo. Cuando el aceite fluye a través de las válvulas, se produce una «caída de presión». Esto significa que existe una presión más alta en el puerto de entrada de la válvula que en el puerto de salida. Cada vez que el aceite fluye de una presión más alta a una presión más baja, se genera calor, el cual es abrsorbido por el aceite.
Cuando se diseña inicialmente un sistema, el depósito y los intercambiadores de calor están dimensionados para eliminar el calor generado. El depósito permite que parte del calor se disipe a través de las paredes hacia la atmósfera. Si tienen el tamaño adecuado, los intercambiadores de calor deben eliminar el exceso de calor, permitiendo que el sistema funcione aproximadamente a 50 ºC (122 ºF).
Bombas compensadoras de presión
El tipo más común de bomba es la bomba de pistón compensadora de presión. Las tolerancias entre los pistones y el plato son de aproximadamente 10 micrones (Figura 1). Una pequeña cantidad de aceite en el puerto de salida de la bomba pasará en derivación (bypass) estas tolerancias y fluirá hacia la carcasa de la bomba. El aceite regresará entonces al depósito a través de la tubería de drenado de la carcasa de la bomba. Este flujo de aceite no trabaja y, por lo tanto, se convierte en calor.
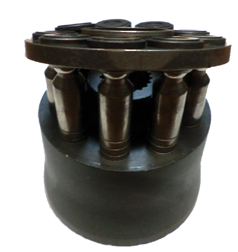
Figura 1. Las tolerancias entre los pistones y el plato de una bomba de pistón compensadora de presión son de aproximadamente 0.0004 pulgadas (10 micrones).
La velocidad de flujo normal fuera de la tubería de drenado de la carcasa es de 1 a 3 por ciento del volumen máximo de la bomba. Por ejemplo, una bomba de 30 galones por minuto (gpm) debe tener aproximadamente 0.3 a 0.9 gpm de aceite que regrese al tanque a través del drenado de la carcasa. Un aumento severo en este índice de flujo causará que la temperatura del aceite aumente considerablemente.
Para verificar el flujo, la tubería puede redirigirse a un contenedor de dimensiones conocidas y sincronizado (Figura 2). A menos que haya verificado que la presión en la manguera sea cercana a 0 libras por pulgada cuadrada (psi), no sostenga la tubería durante esta prueba. En su lugar, asegúrela al contenedor.
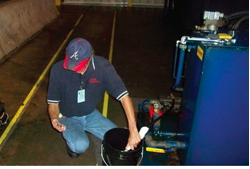
Figura 2. Revise el flujo de aceite redirigiendo la tubería de drenaje de la carcasa a un contenedor de un tamaño conocido y sincronizando la velocidad de flujo.
También se puede instalar permanentemente un medidor de flujo en la tubería de drenado de la carcasa para controlar el caudal. Esta comprobación visual se puede realizar con regularidad para determinar la cantidad de aceite en derivación. Cuando el flujo de aceite alcanza el 10 por ciento del volumen de la bomba, la bomba debe cambiarse.
En la Figura 3 se muestra una típica bomba de compensación de presión de desplazamiento variable. Durante el funcionamiento normal cuando la presión del sistema está por debajo del ajuste del compensador (1,200 psi), el plato oscilante interno se mantiene en el ángulo máximo por el resorte. Esto permite que los pistones entren y salgan completamente, permitiendo que la bomba entregue el volumen máximo. El flujo desde el puerto de salida de la bomba se bloquea por medio del carrete compensador.
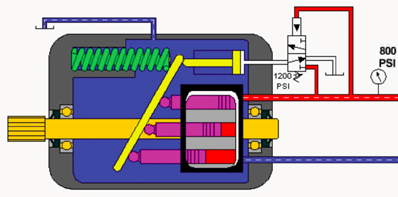
Figura 3. Esta ilustración muestra una bomba compensadora de presión de desplazamiento variable en funcionamiento normal.
Una vez que la presión aumenta a 1,200 psi (Figura 4), el carrete del compensador se desplaza, dirigiendo el aceite al cilindro interno. A medida que el cilindro se extiende, el ángulo del plato oscilante se mueve a una posición casi vertical. La bomba solo entregará suficiente aceite para mantener el ajuste del resorte de 1,200 psi. El único calor generado por la bomba en este momento es el aceite que pasa por los pistones y a través de la tubería de drenado de la carcasa.
Para determinar la cantidad de calor que genera la bomba al compensar, se puede usar la siguiente fórmula: caballos de fuerza (HP) = gpm x psi x 0.000583. Suponiendo que la bomba está pasando en derivación 0.9 gpm y el compensador está ajustado a 1,200 psi, la cantidad de calor generado es: HP = 0.9 x 1,200 x 0.000583 = 0.6296 HP.
Siempre que el enfriador y el depósito del sistema puedan eliminar al menos 0.6296 HP de calor, la temperatura del aceite no debería aumentar. Si el fliujo en derivación aumenta a 5 gpm, la carga de calor aumenta a 3.5 caballos de fuerza (HP = 5 x 1,200 x 0.000583). Si el enfriador y el depósito no son capaces de eliminar al menos 3.5 HP de calor, la temperatura del aceite aumentará.
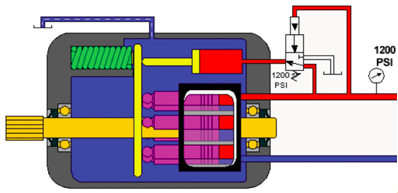
Figura 4. Observe los cambios en el carrete del compensador, el cilindro interno y el plato cíclico de la bomba a medida que la presión aumenta a 1,200 psi.
Las válvulas de alivio
Muchas bombas de compensación de presión utilizan una válvula de alivio como respaldo de seguridad en caso de que el carrete compensador se quede en la posición cerrada. La válvula de alivio debe ajustarse a 250 psi por encima del ajuste del compensador de presión. Si la configuración de la válvula de alivio está por encima del ajuste del compensador, no debe fluir aceite a través del carrete de la válvula de alivio. Por lo tanto, la tubería del tanque de la válvula debe estar a temperatura ambiente.
Si el compensador se quedara pegado en la posición mostrada en la Figura 3, la bomba entregaría el volumen máximo en todo momento. El exceso de aceite no utilizado por el sistema volvería al tanque a través de la válvula de alivio. Si esto ocurriera, se generaría una cantidad significativa de calor.
A menudo, la presión en el sistema se ajusta aleatoriamente intentando hacer que la máquina funcione mejor. Si se ajusta manualmente la presión del compensador por encima de la configuración de la válvula de alivio, el exceso de aceite regresará al tanque a través del alivio, causando que la temperatura del aceite aumente entre 16 a 22 ºC (30 a 40 ºF). Si el compensador no se mueve o se ajusta por encima de la configuración de la válvula de alivio, se generará una gran cantidad de calor.
Suponiendo que el volumen máximo de la bomba es de 30 gpm y la válvula de alivio está configurada a 1,450 psi, se puede determinar la generación de calor. Si se usa un motor eléctrico de 30 HP para conducir este sistema (HP = 30 x 1,450 x 0.000583 = 25), entonces 25 HP se convertirán en calor cuando el motor esté en modo inactivo. Como 746 vatios (W) equivalen a 1 HP, se perderán 18,650 W (746 x 25) o 18,65 kilovatios (kW) de energía eléctrica.
Otras válvulas utilizadas en el sistema, como las válvulas de descarga del acumulador y las válvulas de purga de aire, también podrían fallar y permitir que el aceite dererive hacia el depósito a alta presión. Las tuberías del tanque de estas válvulas deben estar a temperatura ambiente. La derivación de los sellos del pistón del cilindro es otra causa común de calor.
Remoción de calor
El intercambiador de calor o enfriador debe ser mantenido para asegurar que pueda eliminar el exceso de calor. Si se utiliza un intercambiador de calor de tipo aire, las aletas del enfriador deben limpiarse regularmente. Puede ser necesario un desengrasante para limpiar las aletas. El interruptor de temperatura que enciende el ventilador debe ajustarse a 46 ºC (115 ºF). Si se usa un enfriador de agua, se debe instalar una válvula moduladora en la tubería de agua para regular el flujo a través de los tubos enfriadores al 25 por ciento del flujo de aceite .
El depósito debe limpiarse al menos una vez al año; de lo contrario, los lodos y otros contaminantes no solo pueden recubrir el fondo del depósito sino también los costados. Esto permitiría que el depósito actúe como una incubadora en lugar de disipar el calor hacia la atmósfera.
Hace poco estuve en una planta donde la temperatura del aceite en un apilador era de 175 ºC (350 ºF). Se descubrió que las presiones estaban desajustadas, la válvula manual de descarga del acumulador estaba parcialmente abierta y el aceite pasaba continuamente a través de un control de flujo que impulsaba un motor hidráulico. El motor impulsaba cadenas transportadoras que solo funcionaban de cinco a 10 veces durante un turno de ocho horas.
El compensador de la bomba y la válvula de alivio se ajustaron correctamente, la válvula manual se cerró y el electricista desenergizó la válvula direccional del motor, bloqueando el flujo a través del control de flujo. Cuando se verificó la unidad 24 horas más tarde, la temperatura del aceite había descendido a 55 ºC (132 ºF). Por supuesto, el aceite se había degradado y tuvo que efectuarse un lavado (flushing) del sistema para eliminar los sedimentos y el barniz. También se tuvo que cambiar el aceite al sistema.
Todos estos problemas fueron inducidos por el hombre. El encargado de ajustar la perilla local había ajustado el compensador por sobre la válvula de alivio, lo que permitía que el volumen de la bomba volviera al tanque a alta presión cuando no había nada en el apilador. Alguien tampoco cerró completamente la válvula manual, lo que permitió que el aceite pasara nuevamente al tanque a alta presión. Además, el sistema se había programado incorrectamente permitiendo que las cadenas funcionaran continuamente cuando deberían operar solo si se quitaba una carga del apilador.
La próxima vez que ocurra un problema de calor en alguno de sus sistemas, busque aceite que esté fluyendo desde una presión más alta a una presión más baja en el sistema. Ahí es donde probablemente encontrará su problema.
Noria Corporation. Traducido por Roberto Trujillo Corona, Noria Latín América.