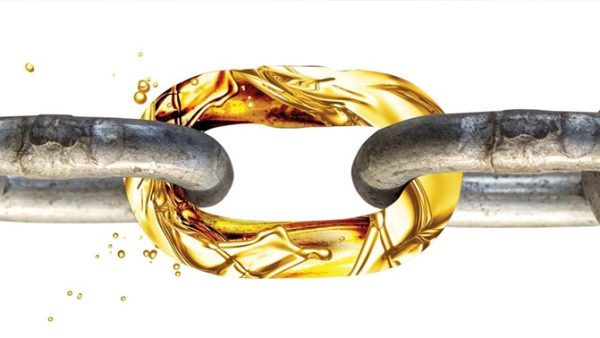
El mantenimiento se considera frecuentemente como un mal necesario y tiende a retrasarse o cancelarse para satisfacer las demandas de producción. Sacar el equipo de servicio para realizar reparaciones o mejorar la funcionalidad puede ser difícil de vender, especialmente si la única actividad de mantenimiento es la lubricación. A medida que la industria ha evolucionado, también lo han hecho las prácticas y filosofías sobre cómo y cuándo realizar el mantenimiento y la lubricación. Ahora hay más opciones y herramientas disponibles para guiar las acciones del personal en casi todas las tareas de lubricación. Sin embargo, para comprender realmente cómo esta evolución ha cambiado el panorama, es necesario saber dónde comenzó el mantenimiento y dónde se encuentra hoy.
Filosofías de mantenimiento
La mayoría de la gente está familiarizada con el término “mantenimiento reactivo”. Este enfoque implica reparar máquinas sólo después de una avería o fallo. Con demasiada frecuencia, las filosofías reactivas son adoptadas por organizaciones que tienen escasez de personal o están estancadas en la mentalidad de “así es como siempre lo hemos hecho”. Esto conduce a presupuestos de mantenimiento exagerados, un rendimiento operativo deficiente y un personal que está constantemente apagando incendios. Como alguien que trabajó de forma reactiva durante años, puedo dar fe del estrés que esto supone para su equipo. Por ejemplo, era difícil saber cuándo o a qué hora iba a volver a casa cada día. Incluso los fines de semana o días festivos siempre existía el riesgo de que me llamaran a trabajar. Esta filosofía de mantenimiento no es sostenible y en gran medida ha quedado relegada a equipos pequeños o no críticos.
En un esfuerzo por alejarse del estado reactivo y en los casos donde la seguridad es primordial, se implementó un mantenimiento planificado o programado. Este enfoque, conocido como “mantenimiento preventivo”, implica tener un período o intervalo establecido en el que se programa y luego se realiza el mantenimiento. La industria aérea ofrece un buen ejemplo de esta filosofía. Hacer funcionar el motor de un avión hasta que falle no es una opción debido a las consecuencias para la seguridad. Por tanto, el mantenimiento se programa en función del número de horas o vuelos. La misma práctica se adoptó en la industria. Esto incluía seguir de cerca las recomendaciones o intervalos del fabricante de equipos originales (OEM, por sus siglas en inglés) para evitar fallas. Probablemente utilice un método similar con el mantenimiento de su vehículo. Al introducir un componente de programación en sus actividades de mantenimiento, puede agregar cierta dirección y continuidad a un proceso diario. Aunque el mantenimiento preventivo puede ayudar a reducir el caos de las fallas, aún puede generar altos costos de mantenimiento cuando se reemplazan piezas buenas.
Más recientemente se han puesto a disposición nuevas herramientas y accesorios para ayudar a monitorear los equipos y detectar problemas potenciales antes. Este seguimiento de los síntomas de fallas y averías se conoce como “mantenimiento predictivo”. Las formas más comunes de este enfoque incluyen el uso de análisis de vibraciones, ultrasonido, termografía, análisis de aceite y una serie de otras tecnologías para proporcionar una alerta temprana de un problema inminente. El mantenimiento predictivo funciona bien para máquinas que funcionan continuamente y, a menudo, da como resultado una reducción del tiempo de inactividad no planificado. Sin embargo, normalmente conlleva costos iniciales considerables, no sólo para las herramientas necesarias sino también para capacitar a las personas que se espera que capturen los datos pertinentes. Se requiere diligencia para garantizar que los datos se recopilen desde el mismo lugar y de la misma manera cada vez. Las prácticas inconsistentes distorsionarán los datos y harán mucho más difícil tomar las medidas adecuadas.
En lugar de reparar las máquinas, el “mantenimiento proactivo” elimina las causas de sus fallos. Se puede utilizar para prolongar la vida útil del equipo, en lugar de simplemente mejorar el proceso de reparación o identificar cuándo una máquina va a fallar. El mantenimiento proactivo se centra en las causas raíz de las fallas y las aborda antes de que conduzcan a un problema final. Gran parte del mantenimiento proactivo ocurre antes de que se encienda una máquina, incluida la alineación y el balanceo. Sin una mentalidad proactiva, las fallas de la maquinaria seguirán afectando a la mayoría de los departamentos de mantenimiento. Analizar lo que salió mal y tomar medidas para evitar que vuelva a suceder son las características distintivas de ser proactivo.
4 estrategias de análisis de aceite
El análisis de aceite pertenece al ámbito del monitoreo de condición, pero puede usarse de varias maneras para determinar qué sucede dentro de un sistema mecánico. También se puede dividir en cuatro estrategias diferentes:
- Reactivo: Se toma una muestra de aceite o grasa solo después de que se identifica un problema potencial mediante una inspección sensorial.
- Preventivo: Se extraen muestras de rutina, pero los resultados no se analizan.
- Predictivo: Se obtienen y analizan muestras buenas y se toman medidas en función de los resultados del laboratorio.
- Proactivo: Se toman muestras de lubricantes nuevos antes de ponerlos en servicio. Las muestras se toman del lugar correcto, de la manera correcta, utilizando las pruebas correctas y con la estrategia de interpretación correcta.
Actividades de lubricación
En un programa de lubricación existen tareas de aplicación de lubricantes, análisis de su condición y eventual eliminación de los mismos una vez que llegan al final de su vida útil. Más allá de estas tareas de primera línea están las actividades de gestión para garantizar que el trabajo se complete correctamente. Quizás la tarea de lubricación más sencilla implique el uso de una pistola de engrasar. Sin embargo, estos dispositivos han sido mejorados en los últimos años y ahora incorporan tecnología avanzada. Antes de utilizar una pistola de engrasar, asegúrese de considerar la tarea en relación con las diferentes filosofías de mantenimiento analizadas anteriormente.
Engrase reactivo
Probablemente hayas escuchado la frase “la rueda que rechina recibe la grasa”. Al realizar la lubricación en estado reactivo, se espera hasta que se experimente un problema antes de añadir grasa a un rodamiento o máquina. Pero engrasar en respuesta a un ruido o a una temperatura elevada es muy reactivo. Cuando surgen estos síntomas, el daño ya se ha producido.
Engrase preventivo
Engrasar una máquina según una fecha del calendario o un número de horas de funcionamiento es una práctica común en la industria, pero agregar grasa según el tiempo puede provocar que la máquina se engrase demasiado o muy poco. Aunque puede ayudar a prevenir algunas fallas, se utilizará mucha mano de obra para mantener el programa de mantenimiento preventivo (PM, por sus siglas en inglés).
Engrase predictivo
Las herramientas predictivas para el engrase han ganado popularidad en los últimos años debido a su capacidad para identificar intervalos precisos y volúmenes de grasa a agregar. El ultrasonido se emplea con frecuencia para escuchar un rodamiento y detectar si se necesita grasa y cuánta. Este tipo de engrase requiere personal capacitado y las herramientas necesarias, pero puede reducir en gran medida, si no eliminar, la probabilidad de engrasar excesivamente una máquina. El muestreo y análisis de grasa también se utilizan cada vez más para determinar la condición de la grasa y la máquina, así como la frecuencia óptima de relubricación.
Engrase proactivo
Al balancear todas las mejores prácticas, podrá ser más proactivo con su engrase. Esto comienza con la selección de la grasa adecuada para la aplicación. Para aplicaciones críticas, también puede incluir tomar muestras de la grasa antes de su uso para verificar su limpieza. Además, realice los cálculos adecuados para confirmar el volumen correcto de grasa en los rodamientos y guiar sus actividades futuras.
Esta misma metodología se aplica a las aplicaciones de aceite. Si bien puede confiar en el movimiento rotativo de una máquina para aplicar aceite a varios componentes internos, usted controla muchos otros factores que pueden proporcionar una señal de éxito. La carga de trabajo variará mucho según la mentalidad del individuo u organización.
43% | de los profesionales de la lubricación dicen que su planta utiliza una estrategia de mantenimiento proactivo, según una encuesta reciente en MachineryLubrication.com |
Lubricación reactiva
El aceite a menudo se aplica manualmente desde un recipiente de relleno o una lata de aerosol en función de un resultado de inspección anormal, como una mirilla que muestra un nivel bajo de aceite o una cadena que parece seca. En estos casos se deben tomar medidas inmediatas para garantizar que no se produzcan daños permanentes. En las máquinas lubricadas por salpique, un nivel de aceite demasiado bajo puede tener efectos catastróficos. Esto también se aplicaría al cambio del aceite sólo después de que haya superado su vida útil.
Lubricación preventiva
Cambiar el aceite según un período de tiempo o intervalo operativo es común para la mayoría de las máquinas no críticas o de pequeño volumen, pero puede llevar a reemplazar el aceite que aún está en buen estado o a pasar demasiado tiempo entre cambios de aceite. Esto puede suponer un desperdicio tanto de mano de obra como de lubricante.
Lubricación predictiva
Utilizar el análisis de aceite para identificar el intervalo de cambio de aceite adecuado es el mejor enfoque para grandes volúmenes de aceite y máquinas críticas. Cuando se analiza una muestra de aceite, se pueden distinguir muchas de sus características y determinar si debe permanecer en servicio y cuánta vida más puede tener. Esto mejora enormemente su capacidad de toma de decisiones y puede minimizar el impacto de una falla del lubricante al planificar una parada o cambiar a una máquina auxiliar.
Lubricación proactiva
Para ser proactivo al lubricar una máquina, debe eliminar las causas raíz de las fallas. Esto se logra asegurando que se aplique el aceite adecuado y que esté limpio y libre de defectos. Se deben examinar y mejorar sus prácticas de almacenamiento y manipulación para asegurarse de que los lubricantes estén lo más limpios posible cuando lleguen a la máquina. Esto incluye filtrar el aceite antes de ponerlo en servicio y usar contenedores de transferencia que puedan sellarse herméticamente. Estas prácticas reducirán la cantidad de fallas experimentadas en su planta.
No pase por alto las inspecciones
A menudo se pasan por alto las inspecciones como base de un programa de lubricación de clase mundial. El personal que camina junto a las máquinas todos los días es la mayor fuente de información para impulsar su programa. Si bien he descrito varias formas de utilizar los resultados de las inspecciones para tomar mejores decisiones sobre lubricación, se debe poner mayor énfasis en las inspecciones mismas. No basta con tener una lista de verificación o hacer rondas simples. Profundice en lo que observa en la máquina, la mirilla o el respirador. Esta será una actividad sumamente valiosa que dará frutos en todos los aspectos del mantenimiento, independientemente de la filosofía empleada.