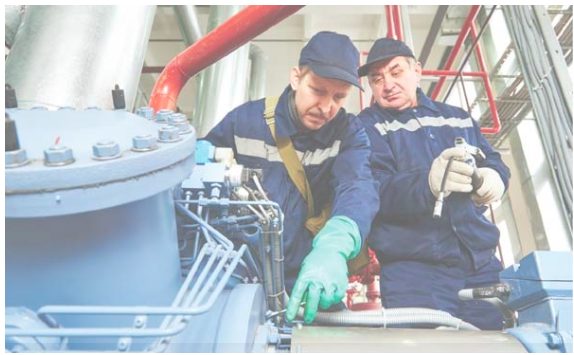
¿Qué es el mantenimiento reactivo y cómo sabe si su empresa lo practica? Mucha gente esconde el mantenimiento reactivo y lo llama de diferente manera, pero si usted contesta honestamente “si” a varias de las preguntas siguientes, entonces es probable que esté atrapado en la rutina reactiva:
¿Mide qué tan rápido se repara un componente de una máquina cada vez que se descompone? ¿Felicita a su personal cuando repara una máquina en lugar de evitar que falle? ¿Cree que la disminución de los costos de mantenimiento se comienza reduciendo mano de obra y/o materiales? ¿Están aumentando sus costos de mantenimiento a pesar de que ha implementado diversas estrategias? ¿Está recompensando la falla?
Algunas de estas preguntas pueden sonar ridículas, así que déjeme explicarle. Por ejemplo, usted se pregunta ¿Qué compañía podría premiar una falla? ¿Pero usted paga horas extras a sus mecánicos por acudir en la noche o los fines de semana para hacer una reparación? Si es así, usted está recompensando la falla de esa máquina.
Una mejor estrategia sería recompensar a su equipo de trabajo cuando no haya fallas en la maquinaria. ¿No cree usted que el personal de mantenimiento se enfocaría en mantener una máquina en óptimas condiciones si su recompensa estuviera ligada a la continua operación y disponibilidad en lugar de a la falla? Es un problema cultural muy importante en varias plantas y no es un obstáculo fácil de superar.
Cambiar de mantenimiento reactivo a proactivo requiere de una diferente manera de pensar, ejecutar y administrar. Cuando se diseña, implementa y administra efectivamente, el mantenimiento proactivo resulta en óptima confiabilidad de los activos a un costo óptimo. Todos ganan. La empresa obtiene más valor de su maquinaria, se reducen el presupuesto de mantenimiento y los costos iniciales, por lo tanto, los márgenes de ganancia aumentan, el trabajo del personal se vuelve más fácil, etc. La lista de beneficios es interminable.
Entonces, ¿Por qué no todos se esfuerzan por hacer este cambio? El cambio es difícil y a las personas no les gusta el cambio. Aunque el cambio no es simple ni fácil, es posible. No solo es alcanzable el cambio, muchas personas lo están logrando.
Hay muchas estrategias para la gestión del cambio, incluyendo algunas que se analizarán más adelante. Sin embargo, lo primero que debe hacer es creer que el cambio tendrá un efecto duradero en la organización y las personas que la integran.
Cualquier persona que trabaje en el área de mantenimiento y confiabilidad es consciente de las frustrantes consecuencias de una falla inesperada en la maquinaria (la definición del mantenimiento reactivo). Algunas compañías tienen cientos e incluso miles de componentes de maquinaria por mantener, y una sola falla podría detener las operaciones. Si la empresa está trabajando a toda su capacidad, esta pérdida nunca será recuperada. Aunque no hay duda de la importancia de reparar algo tan rápido como sea posible cuando falla la máquina, pocas personas se dan cuenta de los costos elevados que conlleva trabajar con el mantenimiento reactivo.
45%
de las plantas utilizan una estrategia proactiva de mantenimiento, según una encuesta realizada recientemente por MachineryLubrication.com
Enfoques de la gestión de mantenimiento
Existen tres enfoques básicos para la gestión de mantenimiento: reactivo, predictivo/preventivo y proactivo. El mantenimiento reactivo, que es detonado por las fallas, es el resultado de una falta de mantenimiento preventivo y predictivo. Por otro lado, el mantenimiento proactivo mantiene a los equipos en servicio y en buenas condiciones mediante el mantenimiento preventivo y predictivo, así como un enfoque especial en la eliminación de la causa raíz de las fallas.
Un enfoque de mantenimiento reactivo puede ser perjudicial para su organización porque podría quedar atrapado en un círculo vicioso de constantes trabajos urgentes, dejando de lado las tareas de mantenimiento que podrían llevar a una reducción del mismo trabajo de emergencia en el futuro. Además, el mantenimiento reactivo es mucho más costoso que las tareas proactivas. Esto se debe a que las tareas de mantenimiento reactivo son más complejas, como abrir una caja de engranes para cambiar un rodamiento, mientras que las tareas de mantenimiento proactivo son relativamente simples, como son las inspecciones sensoriales y los pequeños ajustes.
Comenzando el viaje al mantenimiento proactivo
Este cambio no puede hacerse tan fácilmente como presionar un botón; será un proceso largo, pues es más una evolución que un cambio. Incluso cuando todo esté dicho y hecho, es posible que nunca se deshaga del mantenimiento reactivo. Sin embargo, puede reducir significativamente las reparaciones no planeadas.
La implementación de un software de gestión de activos (CMMS, Computerized maintenance management system) que puede configurarse para adaptarlo a las necesidades específicas de su organización, puede ayudar en el proceso del cambio de mantenimiento reactivo a proactivo. Necesita organización, medición y análisis de miles de datos. Sin la ayuda de este software y una estructura de soporte detrás, sus esfuerzos deberán multiplicarse muchas veces.
El objetivo principal de este software es ayudar a planear y programar su mantenimiento preventivo y proactivo. No puede eliminar los costos de mantenimiento, pero sí puede redirigirlos. Si usted enfoca su tiempo, dinero y energía en asegurarse que las tareas proactivas se realicen y se hagan correctamente, obtendrá como resultado una drástica reducción de las tareas de reparación. De hecho, está negociando trabajo complejo y más difícil (mantenimiento reactivo) por un trabajo fácil y rentable (mantenimiento proactivo). El software debería ser capaz de ayudarlo a facilitar esta negociación.
Mantenimiento preventivo
El primer paso hacia el mantenimiento proactivo es utilizar los datos de experiencias anteriores para manejar los plazos y decisiones de mantenimiento. Por ejemplo, si usted sabe que una bomba tiene un promedio de vida de tres años en condiciones normales de operación y medio ambiente de su planta, y sabe esto porque cuenta con un historial de 10 años, entonces con certeza podrá planear y programar la sustitución de esta bomba cada 2.5 años de operación. Si bien no es la mejor de las prácticas de mantenimiento, porque podría estar cambiando una bomba perfectamente operativa a los 2.5 años, esta estrategia puede reducir costos generales tanto a corto como a largo plazo, a diferencia de una falla catastrófica desconocida que ocurre inesperadamente.
Este enfoque aún requiere mano de obra significativa para realizar tareas que en el momento pueden parecer innecesarias. Sin embargo, este esfuerzo adicional puede dar resultados a largo plazo, cuando se agregan a la ecuación factores como el incremento en los tiempos en que la máquina puede producir y la capacidad de efectuar una planeación del trabajo.
Según el caso de estudio realizado por la oficina de eficiencia de energía y energía renovable (Office of Energy Efficiency and Renewable Energy), la estrategia de sustitución periódica de componentes en el mantenimiento preventivo ahorra entre un 12% y 18% en comparación con el mantenimiento reactivo.
Mantenimiento predictivo
El siguiente paso hacia el mantenimiento proactivo es evaluar la condición actual de la maquinaria. El mantenimiento predictivo le permitirá planificar las acciones correctivas antes de que el equipo sufra una falla catastrófica, diversas herramientas tecnológicas pueden ayudar, el objetivo principal de cada una de ellas es medir los síntomas de la falla o las fallas. Estas herramientas generalmente son no invasivas y pueden monitorear las condiciones de la maquinaria y de los componentes a través del monitoreo y análisis.
El único defecto que tiene esta estrategia es que en la mayoría de los casos está midiendo fallas o síntomas de falla, esto significa que para cuando tenga una medición anormal en sus lecturas, el problema ya existe. Sin duda, es de gran valor saber que existe un problema y ser capaz de realizar acciones correctivas antes de que se convierta en catastrófico, pero hay una mejor opción. Si su programa ha evolucionado hasta este punto, un caso de estudio de la NASA sugiere que está ahorrando hasta un 50% en costos de mantenimiento, en comparación con el mantenimiento reactivo.
Mantenimiento proactivo
Hasta este punto, los pasos evolutivos han sido bastantes fáciles y graduales. Dar el salto al mantenimiento proactivo requiere un cambio difícil para la mayoría de las organizaciones porque requiere de un cambio de mentalidad, procesos, procedimientos y cultura. El mantenimiento proactivo no se enfoca en reparar máquinas o ser más efectivo en las tareas correctivas en máquinas que muestran señales de problemas. En cambio, se concentra en eliminar la causa raíz de los problemas. Si puede eliminarla, no tendrá las fallas que por estas causas raíz se podrían haber convertido en trabajos urgentes.
Una de las formas más simples de avanzar por el camino hacia el mantenimiento proactivo es a través de la educación o la capacitación del personal de mantenimiento, para que sepan qué buscar y por qué. Esto es esencialmente a lo que se reduce el mantenimiento proactivo: conocer las causas principales que conducen a la mayoría de las fallas de la máquina, saber cómo son y saber por qué es importante corregir el problema en esta etapa en lugar de esperar hasta la falla. Este tipo de inspecciones pueden ahorrar enormes cantidades de dinero a las empresas, pero a menudo se pasan por alto por su simplicidad.
Por ejemplo, considere revisar el nivel de aceite en un componente lubricado por salpique. Aunque esto es extremadamente fácil de hacer y solo requiere entrenamiento básico, el no hacerlo podría provocar una falla catastrófica del componente y todo lo relacionado con una falla.
Con el trabajo proactivo, se desea negociar el costo del paro de la máquina en el futuro, por el tiempo, el dinero y la energía de una simple inspección. Casi siempre es favorable el intercambio y conducirá a una reducción masiva en los costos de mantenimiento y producción. Por supuesto, no siempre funciona.
No todos los programas y estrategias se ajustan a un molde perfecto. Cada programa necesita equilibrar el costo de implementación con el gasto de ser complaciente. Por ejemplo, es perfectamente aceptable utilizar un modo de mantenimiento reactivo para un componente barato que sea fácilmente modificable y fácilmente disponible. No tiene sentido gastar mucho tiempo, dinero y energía en una bomba que cuesta USD $500 en un catálogo de pedidos por correo, tiene tres repuestos disponibles, toma cinco minutos cambiarla y no es parte de un proceso crítico.
El programa ideal podrá usar diversos modos de mantenimiento para asegurarse que la planta funcione de la manera más eficiente y efectiva posible. Comprender las diferentes filosofías de mantenimiento y tener una excelente comprensión de las operaciones, la criticidad de la máquina, costos, etc., será esencial para adaptar un enfoque equilibrado en su planta. Solo cuando sus variables se extiendan completamente, podrá optimizar su programa y comenzar a obtener el máximo provecho de su gente y de sus máquinas.
Noria Corporation. Traducido por Roberto Trujillo Corona, Noria Latín América.