Cuando las mentes creativas y dedicadas se unen para proporcionar el producto adecuado para cada cliente, no sorprende que Equistar Chemicals recurriera al análisis de aceite para mejorar las operaciones de la planta y poder producir mejores productos.
Esta empresa con valor de US $6 mil millones, se ubica entre los principales productores mundiales de etileno y propileno, con una capacidad anual de etileno de más de 11 mil millones de libras (5 mil millones de kg) y más de 6 mil millones de libras (3 mil millones de kg) de polietileno. Equistar cuenta con 5000 empleados y 16 plantas de fabricación a lo largo de la Costa del Golfo y en el Medio Oeste de los Estados Unidos.
Las siguientes historias de casos son ejemplos de los últimos años en donde los costos de mantenimiento y el tiempo de inactividad de la producción se han reducido o evitado mediante el uso de un programa de análisis de aceite en la planta Morris en Morris, Illinois.
El análisis de aceite en Equistar se realiza para monitorear la condición de los lubricantes en servicio, identificar la presencia de contaminación y determinar la condición de los componentes de la maquinaria. Las tecnologías de análisis de aceite y análisis de vibraciones están integradas y se complementan entre sí para diagnosticar problemas en la maquinaria.
En la Planta Morris, los resultados de ambas tecnologías se analizan juntos en la misma base de datos. Esto le da a la planta la ventaja de diagnosticar simultáneamente los niveles de vibración y las tendencias de las muestras de aceite. En algunos casos, Equistar ha visto un aumento en las partículas de desgaste en las tendencias de la muestra de aceite antes de que sean visibles los aumentos en las tendencias del nivel de vibración.
Falla del cojinete de empuje
Un enero, los resultados de la muestra de aceite indicaron un aumento en la concentración de partículas ferrosas de desgaste en el aceite de la caja de engranajes y la turbina de agua de enfriamiento de la planta de etileno (Figura 1).
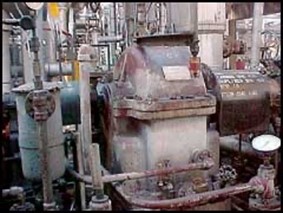
La turbina y la caja de engranajes tienen un depósito común, lo que complica el diagnóstico de la fuente de las partículas ferrosas en el aceite. El grupo de confiabilidad solicitó una ferrografía analítica completa de la muestra. Reveló que la mayoría de las partículas eran de babbitt. Además, las partículas se decoloraron al estar expuestas a altas temperaturas y se concluyó que se originaron por acción de corte/cizallamiento.
Se sospechó que el cojinete de empuje grande o el cojinete radial de la caja de engranajes estaban fallando. Se redactó una orden de trabajo, se balancearon los engranajes de repuesto, se inspeccionaron los cojinetes de repuesto y se hizo la planificación para la inspección/reparación de la caja de engranajes.
Durante este tiempo, los niveles de vibración, que se habían mantenido bajos, mostraron un aumento en la dirección axial (empuje). Poco después, se detuvo la caja de engranajes. La inspección de la caja de engranajes reveló que el cojinete de empuje estaba fallando y habría estado operativo solo por un corto tiempo antes de fallar por completo. Una falla completa del cojinete habría resultado en daños al juego de engranajes.
Esta oportunidad de detener la caja de engranajes antes de que fallara por completo redujo significativamente los costos de mantenimiento y el tiempo de inactividad de la máquina. Una falla completa de la caja de engranajes podría haber resultado potencialmente en el disparo de la Máquina de Carga de Gas Etileno.
Vibraciones y análisis de aceite confirman falla de cojinete
En enero, la muestra de análisis de aceite del giroscopio de la extrusora de la Línea 2 indicó un aumento en el contenido de hierro. Las muestras en el conjunto del embrague de aluminio solo indicaron la presencia de hierro en el aceite. Las lecturas de vibración tomadas en esta unidad indicaron un aumento en los niveles de amplitud de vibración (Tabla 1).
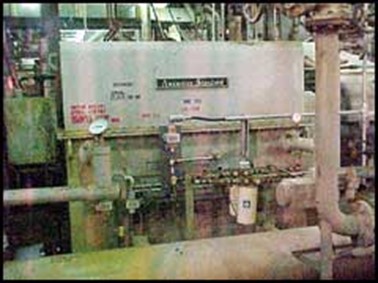
El espectro de vibración indicó un defecto en la pista interior del rodamiento. La unidad se apagó y una inspección visual reveló que la pista del rodamiento se había astillado, pero no había daños en el conjunto del embrague de aluminio. El conjunto se reconstruyó internamente sin reemplazar el eje o el embrague.
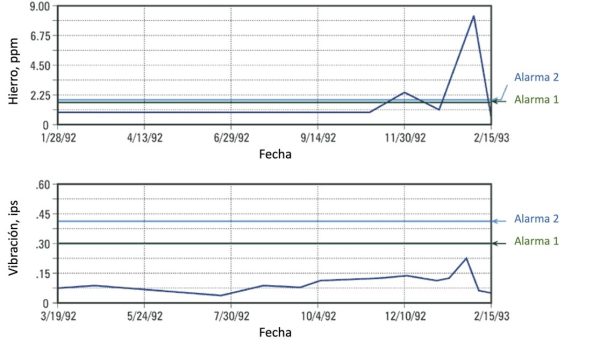
Los costos de mantenimiento y el tiempo de inactividad de la producción se minimizaron al localizar esta falla del rodamiento. Una falla total del rodamiento habría dañado potencialmente el conjunto del embrague. Los ahorros en costos de mantenimiento se estimaron entre US $15,000 y US $20,000.
Ferrografía analítica salva caja de engranajes
En febrero, los resultados de las muestras de aceite de la caja de engranajes del reactor de propileno (Figura 3) indicaron un aumento en el hierro de 19.9 ppm a 54.3 ppm (Gráfica 2). La ferrografía analítica reveló las partículas originadas por el desgaste de los engranajes.
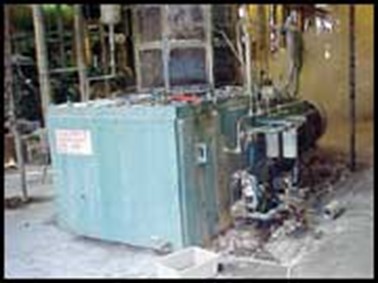
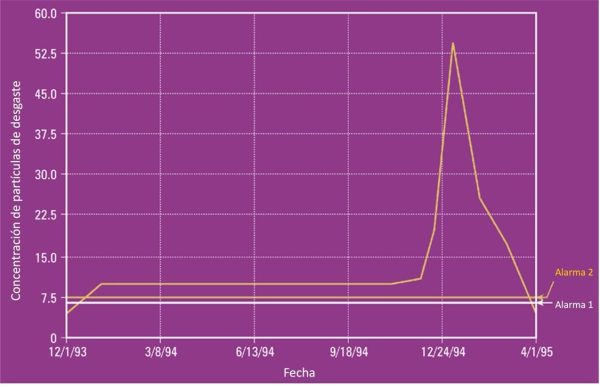
Se inspeccionó la caja de engranajes y se encontró que la boquilla de rociado de aceite para el juego de engranajes cónicos intermedios estaba obstruida. El engranaje comenzaba a mostrar un desgaste mínimo, se limpió la boquilla de aceite, se reinstaló y se reinició la caja de engranajes.
Esta fue una reparación simple, gracias al programa de análisis de aceite. La detección temprana de este problema evitó la falla completa de estos engranajes. Se evitaron varios días de inactividad junto con los costos de mantenimiento asociados con el cambio de la caja de engranajes.
El análisis de aceite ahorra US $25,000
A principios de septiembre, el personal de mantenimiento observó un gran aumento en la concentración de partículas ferrosas de desgaste en la muestra de aceite de una caja de engranajes del extrusor satélite (Figura 4). Se revisaron los filtros y se encontró que estaban recogiendo metales (Gráfica 3).
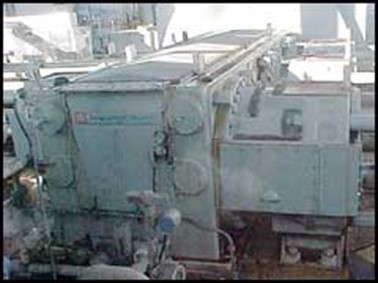
Se recomendó la inspección del flujo adecuado de las boquillas de rociado de aceite en la caja de engranajes, así como la inspección del engranaje y el cojinete. La inspección reveló que las boquillas de aspersión se habían tapado parcialmente, lo que reducía el flujo de aceite. Las boquillas fueron removidas y limpiadas.
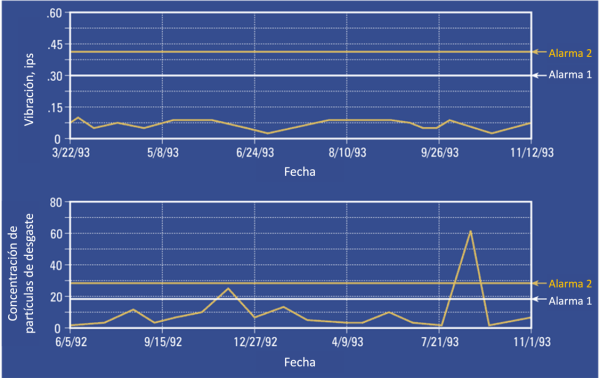
Los engranajes y rodamientos se inspeccionaron más a fondo para ver si estaban desgastados y se encontró que estaban en buenas condiciones. La unidad se restableció después de solo un par de horas de inactividad. La estimación de los ahorros en costos de reparación de mantenimiento de las cajas de engranajes es de US $ 20,000 a US $ 25,000 más varios días de tiempo de inactividad de producción evitado.
Cojinete del cigüeñal del compresor
En octubre de ese mismo año se observó un gran aumento de cobre en la muestra de aceite del cigüeñal del hipercompresor de Polietileno (Gráfica 4). Se recomendó una inspección del cojinete de empuje del cigüeñal. El análisis ferrográfico indicó que las partículas provenían del desgaste de los cojinetes, con algunas partículas de hasta 35 micrones.
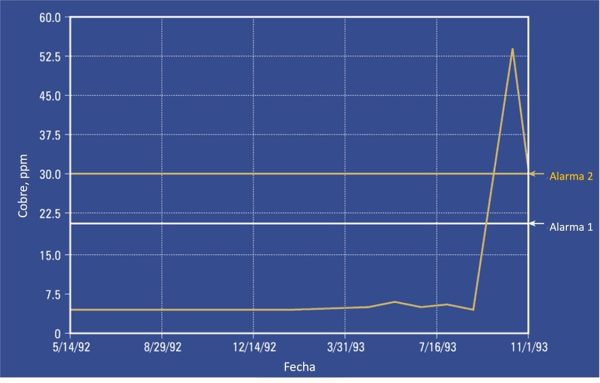
El compresor se apagó y una inspección del cojinete de empuje (zapatas) reveló que estaba muy desgastado y que el cigüeñal se había movido hacia el sur. Los filtros de aceite habían sido contaminados por la presencia de cobre en el sistema de lubricación.
Una inspección más detallada condujo al cojinete del pedestal del motor, que tenía una pista interna agrietada y permitió que el cigüeñal del compresor se moviera hacia el sur. Esto afectó al cojinete de empuje. Se cambiaron los cojinetes de empuje y los cojinetes del pedestal y la unidad volvió a ponerse en funcionamiento. Los ahorros tanto por los costos de mantenimiento como por el tiempo de inactividad de la producción debido a la detección temprana de esta falla se estimaron en cientos de miles de dólares.
AN salva compresor de gas
El número ácido (AN) del aceite de uno de los compresores de gas del ciclo comenzó a aumentar, lo que indicaba que el aceite se estaba volviendo corrosivo. El AN había aumentado en los últimos dos meses de 0.9 a 4.67 (Gráfica 5).
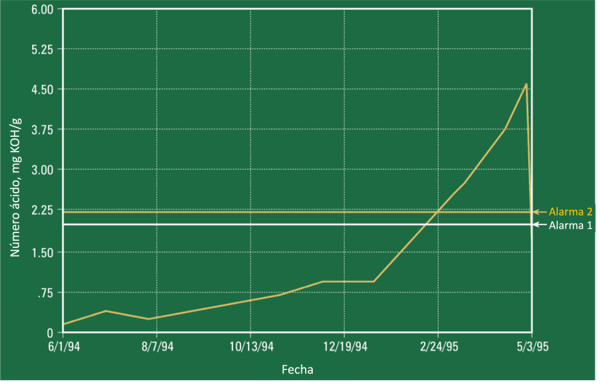
Dado que se debía evitar detener el proceso mientras se cambiaba el aceite, el equipo de confiabilidad indicó que se drenaran algunos tambores de aceite y a la vez se agregara aceite nuevo de reposición hasta que se cambiaron 1600 litros. El AN se redujo a 1.6.
Nuevamente, el análisis de aceite alertó al equipo de un problema que quizás no se supo hasta que la maquinaria ya estaba dañada.
Estas historias de casos han demostrado el valor de un programa de análisis de aceite integrado, como el que tiene la Planta Morris. Los puntos de muestreo están etiquetados y las muestras se recolectan siempre en el mismo lugar, lo que garantiza que se recolecten muestras representativas en todo momento. El laboratorio envía los resultados el mismo día que se completan las pruebas.
El análisis de aceite y los datos de vibración se diagnostican y se hace una recomendación para corregir o reparar el problema de la maquinaria. El programa de análisis de aceite ha demostrado ser una valiosa herramienta de monitoreo de condición que permite al equipo de confiabilidad en la Planta Morris reducir sustancialmente los problemas de la maquinaria y los costos de mantenimiento.
Referencia: Tiimothy J. Smith, Equistar Chemicals. Traducción por Roberto Trujillo Corona, Noria Latín América