Una mayor “lectura entre líneas” utilizando datos de viscosidad, número ácido (AN) y análisis infrarrojo podría indicarnos si la menor protección antidesgaste es el resultado de la adición de aceite incorrecto o del agotamiento de los aditivos.
Lamentablemente, si bien todos estos parámetros son importantes para nuestro análisis, utilizan unidades muy variables y cada uno tiene su propio grado de variación aleatoria (fragilidad de los datos).
Esto dificulta la representación gráfica de los valores a lo largo del tiempo en un gráfico común. Además, se aplica una lógica de alarma diferente a los distintos parámetros. Una forma de evitar este problema es utilizar clasificaciones percentiles derivadas estadísticamente en lugar de valores de parámetros reales.
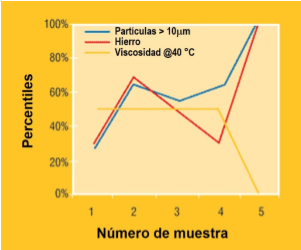
Figura 1
Beneficios
Esta sencilla técnica produce los siguientes beneficios para el analista de lubricantes:
- Todos los parámetros se pueden revisar en un gráfico de tendencia común utilizando unidades comunes (el percentil). Esto facilita ver qué está subiendo y qué está bajando simultáneamente, facilitando el proceso de lectura entre líneas. En la Figura 1, es evidente que la viscosidad está disminuyendo mientras que el conteo de partículas y el hierro han aumentado drásticamente, lo que sugiere que es posible que se haya agregado aceite incorrecto a la máquina y que eso haya inducido altos índices de desgaste.
- Se pueden configurar alarmas comunes para todos los parámetros y mostrarlas en un gráfico común. Por ejemplo, una desviación estándar puede representar una advertencia, mientras que dos pueden sugerir una situación crítica (Tabla 1).
- Los efectos de ruido de la variación normal se eliminan porque los cálculos de percentil de cada parámetro se basan en su propia desviación estándar.
- Los percentiles pueden ser comprendidos por cualquier persona, incluida la gerencia. El conteo de partículas, el AN (mg KOH/g de aceite), etc. no son tan obvios para el observador inexperto.
- Los parámetros de análisis no relacionados con el aceite, que van desde los límites de vibración hasta la longitud del faldón, se pueden incorporar fácilmente en los gráficos y, por lo tanto, en los procesos de análisis y toma de decisiones.
- La técnica es rápida y sencilla.
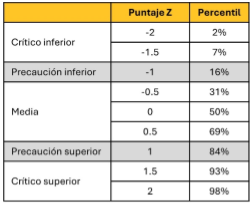
Tabla 1
Transferir datos a percentiles
- Utilizando datos históricos, determine el valor promedio (media) para cada parámetro (ecuación 1).
- Calcule la desviación estándar para cada parámetro utilizando el mismo conjunto de datos utilizado para calcular la media (ecuación 2).
- Genere un puntaje Z restando el valor medio de la lectura actual y luego divida por la desviación estándar (ecuación 3). Este número indica cuántas desviaciones estándar está por encima o por debajo del valor medio.
- Utilice tablas de distribución normal acumulativa. La mayoría de los programas de hojas de cálculo disponibles comercialmente generan un valor de distribución acumulativa para un puntaje Z determinado.
- Presente el valor de distribución normal como un valor de percentil
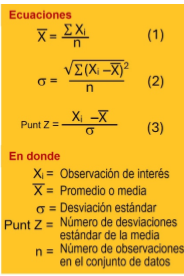
Figura 2
Por ejemplo, supongamos que una máquina tiene un nivel medio de hierro de 15 ppm y una desviación estándar de 3 ppm. Un valor observado de 18 ppm daría como resultado un puntaje Z de 1, o una desviación estándar mayor que la media. El valor de 18 ppm se encontraría en el percentil 84.
Si nuestra observación se produjo en la media (15 ppm), nuestro valor sería el percentil 50. La Tabla 1 ilustra dónde aparecen los distintos puntajes Z en la curva de distribución normal acumulativa.
Esta y otras técnicas se pueden aplicar de manera eficaz para simplificar los datos del análisis de aceite y facilitar el proceso de diagnóstico. Pruebe variaciones sobre el tema de percentiles, como el uso de un promedio móvil de 10 muestras y una desviación estándar en lugar de los valores fijos cuando sea apropiado. Esta simplificación es importante para que el análisis de aceite gane aceptación en la corriente principal del proceso de toma de decisiones.
Cómo hacer que las estadísticas trabajen para usted
Al intentar programar acciones de mantenimiento basadas en datos de análisis de aceite, las estadísticas simples pueden ser una herramienta poderosa para simplificar los datos, identificar relaciones entre los parámetros del análisis de aceite y aumentar la confianza en las conclusiones.
Las técnicas estadísticas como el análisis de correlación pueden ayudarnos a garantizar que estamos tomando la decisión correcta. También pueden ayudarnos a centrar nuestros esfuerzos en descubrir la causa raíz de la condición anormal.
La revisión de los datos de análisis de aceite de nueve máquinas hidráulicas idénticas que realizan la misma función en el mismo entorno revela una variación sustancial en los niveles de zinc en función del tiempo en que el aceite está en servicio. Una investigación más profunda nos lleva a concluir que los resultados del número ácido (AN) también disminuyen en función del tiempo. Al calcular la correlación, vemos que los valores de zinc y AN están altamente correlacionados (Figura 3).
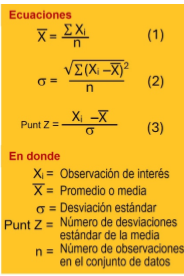
Figura 3
El papel del ZDDP
Sabemos que el dialquilditiofosfato de zinc (ZDDP) utilizado en la mayoría de los aceites antidesgaste reacciona con el reactivo de hidróxido de potasio (KOH) utilizado para medir el AN, elevando los números cuando el aceite es nuevo.
El AN disminuye a medida que se agota el aditivo. Una vez que se agota el aditivo antidesgaste/antioxidante ZDDP, deja al aceite base con una protección reducida contra la oxidación y los números de acidez comenzarán a aumentar desde su punto mínimo a medida que el aceite base se degrada.
Además, una vez que se agota el ZDDP, la máquina está sujeta a un mayor desgaste debido a la pérdida de la protección antidesgaste del fluido. El zinc y el nitrato de amonio tienden a correlacionarse bien en la mayoría de los aceites formulados con un aditivo antidesgaste ZDDP. Es importante cuantificar esta correlación con datos de pruebas específicos para una aplicación.
El análisis indica que una de las máquinas está funcionando con niveles bajos de zinc y de ácido nitroso. Debido a que tanto el zinc como los números de acidez (AN) se han reducido, y sabiendo que la correlación entre estos dos parámetros es fuerte en esta aplicación, tenemos una gran confianza en que nuestro aditivo ZDDP ha disminuido, tal vez hasta el punto de agotarse. Esta es una situación que justifica una acción de mantenimiento. Es probable que el aceite simplemente haya llegado al final de su vida útil.
Degradación
Otra posibilidad es que un estrés anormal haya acelerado la degradación. Un análisis adicional del aceite y una inspección de la máquina deberían identificar si la degradación es normal o anormal. Si es anormal, el proceso debería revelar la causa raíz específica del problema.
Una vez identificada la causa raíz, se puede programar una acción de mantenimiento para corregir la situación. Si se considera que la tasa de degradación es normal, simplemente cambiamos o reconstituimos el aceite sin realizar más investigaciones.
Al comprender cómo se correlacionan los distintos parámetros del aceite, podemos investigar síntomas anormales y tomar decisiones con un fuerte sentido de confianza de que estamos abordando problemas de mantenimiento reales y no solo persiguiendo falsas alarmas.
Drew Troyer. Traducción por Roberto Trujillo Corona, Noria Latín América