En años recientes, la industria de generación de energía ha visto como se han incrementado los problemas relacionados con el barniz en las turbinas de combustión. Este incremento es atribuido a las elevadas temperaturas de operación, tanques de aceite más pequeños, más operaciones cíclicas y en horas pico, bases lubricantes más refinadas que tienen una menor solvencia para los precursores de barniz y el uso cada día mayor de filtración más fina que ha causado la generación de una mayor cantidad de cargas electrostáticas en el aceite de las turbinas.
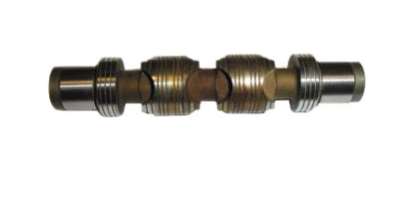
Depósitos de barniz en el carrete de una servo-válvula
La solvencia del barniz en los aceites de turbina depende de la temperatura, con un punto de transición entre 54 y 57°C. Frecuentemente la temperatura en los sistemas hidráulicos de control de las turbinas cae por debajo de estos límites, ocasionando la formación de depósitos en las válvulas de control.
El aspecto más problemático de la contaminación con barniz en los sistemas de lubricación y control de la turbina es que este material se deposita en las superficies de las servo-válvulas, ocasionando su atascamiento y el taponamiento del filtro de ultima oportunidad (LCF) que son parte del conjunto de la servo-válvula.
Los LCF están hechos de material sinterizado o de una malla fina que proporcionan una superficie conveniente para la formación de barniz, ya que están colocados donde el flujo de aceite es más lento, y es la sección más fría del sistema hidráulico de control. La baja temperatura promueve la formación de barniz debido a que éste tiene una menor solubilidad en el aceite a baja temperatura, lo que lo hace salir de la solución y depositarse en la superficie metálica del filtro.
Los filtros fabricados con fibra de vidrio normalmente no se tapan con el barniz. Se sabe que los filtros de flujo total de 6 micrones no presentan problemas prematuros de taponamiento relacionados con el barniz, a pesar de que el aceite presenta un elevado contenido de material promotor de este contaminante. El taponamiento de los filtros metálicos tipo vela en lugar de los de fibra de vidrio más grandes, se debe probablemente a diferencias en interacción entre el barniz con el metal versus la fibra de vidrio, la temperatura más fría en la sección hidráulica y la baja velocidad del fluido.
Además de los depósitos en las servo-válvulas, los precursores de barniz forman depósitos en los sellos mecánicos, cojinetes de Babbitt, zapatas de los cojinetes de empuje y orificios, generando restricciones al flujo de aceite. Cuando estos depósitos se forman en los intercambiadores de calor y en las paredes de los tanques, se reduce la transferencia de calor y se producen altas temperaturas en el sistema.
¿Qué es el barniz?
El barniz es una película delgada e insoluble que se forma sobre las superficies lubricadas dentro del sistema de lubricación de la turbina, incluyendo cojinetes y servo-válvulas. Este material está compuesto de una serie de sustancias provenientes de los aditivos y de la degradación termo-oxidativa del aceite con productos de alto peso molecular y que además tienen una limitada solvencia en la base lubricante. Estos compuestos son de naturaleza polar y comienzan con el tiempo a migrar, desde el interior del aceite hacia las superficies lubricadas de la máquina, dependiendo de las condiciones del sistema y del lubricante, y de su afinidad polar.
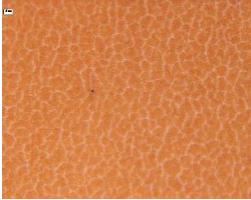
Esta microfotografía muestra el barniz sobre una membrana para análisis (0.45 micrones de porosidad) y a 100x de magnificación.
Inicialmente, las superficies muestran un color dorado/bronceado, que se van transformado en capas oscuras como las gomas, la cuales en el tiempo se convierten en un depósito duro, tipo laca. La composición química de este material insoluble varía dependiendo de las condiciones de operación de operación de la turbina, el tipo de base lubricante y los aditivos.
¿Cómo se formal el Barniz?
Todas las turbinas producen sustancias insolubles, aún ajo condiciones normales. La velocidad con que se generen estos insolubles es acelerada bajo condiciones inusuales o severas. Factores tales como oxidación, puntos calientes, contaminación con productos químicos, cargas electrostáticas relacionadas con filtración, microdieseling y compresión adiabática son algunas de las fuentes más comunes de la generación de barniz.
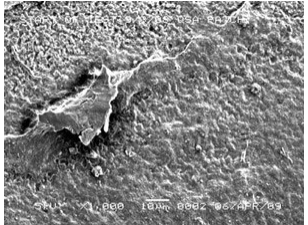
El mismo material de barniz es mostrado a una magnificación de 1000X utilizando un microscopio electrónico de barrido.
Típicamente los fluidos derivados del petróleo sufren una degradación/polimerización oxidativa que origina productos insolubles tipo lodo/barniz. Un número de compuestos químicos oxigenados se generan durante el curso de una oxidación térmica, incluyendo ácidos, alcoholes, ésteres, cetonas, etc. Sin embargo, algunos estudios han demostrado que los precursores de barniz son especies que contienen predominantemente dos átomos de oxígeno por molécula, que apunta a que la función hidroxil-ácido como intermediario activo en la formación de barniz.
La especie química responsable de la formación de barniz no siempre está relacionada con la base lubricante. El paquete de aditivos y su interacción con la base lubricante juegan un papel importante en la formación de barniz.
Para controlar los procesos de oxidación se le agregan a las bases lubricantes los aditivos inhibidores de oxidación. Los más comunes son los fenoles inhibidos y las aminas aromáticas. Los fenoles inhibidos actúan eliminando radicales. Son más apropiados para trabajar a bajas temperaturas, mientras que las aminas se desempeñan mejor altas temperaturas.
El paquete de aditivos fenol/amina ha demostrado ser más robusto, en la medida en que los fenoles también regeneran las aminas agotadas. Se sabe que un antioxidante del tipo amina, conocido como PANA, contribuye a la formación de depósitos en la medida en que se va agotando.
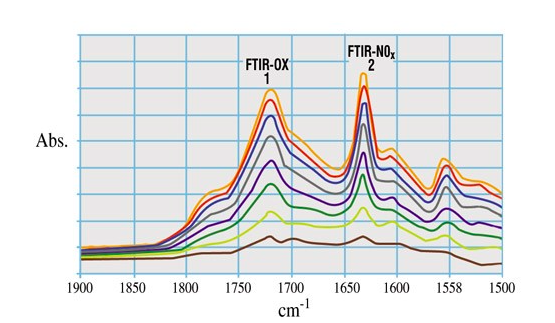
Este espectro infrarrojo muestra el barniz producido por oxidación y degradación térmica con picos de absorbancia característicos en la región de 1740 cm-1
Una vez que los aditivos se han agotado, el proceso de oxidación se acelera rápidamente. Los expertos recomiendan el monitoreo del agotamiento de los antioxidantes de fenol y amina. Cuando los antioxidantes fenólicos se acercan al nivel de agotamiento, se puede esperar que el nivel de aminas comience a disminuir y el potencial de formación de barniz a crecer.
Las elevadas temperaturas también contribuyen al proceso de oxidación. La regla general es que por cada 10°C (18°F) de incremento en la temperatura de operación, la velocidad de la oxidación se duplica (regla de Arrhenius). El agua, la aireación y las partículas de desgaste como el fierro y el cobre actúan como catalizadores acelerando la oxidación del lubricante.
Además de la oxidación, el otro camino importante para el deterioro del fluido en una turbina es la degradación térmica. Las tres fuentes más comunes de degradación térmica del fluido y que contribuyen a la formación de barniz son la compresión adiabática de las burbujas de aire atrapadas en el aceite, puntos calientes en el sistema y las cargas electrostáticas inducidas por el tamaño de poro del filtro de aceite.
Las fuentes más comunes de aire atrapado en el aceite son entradas por las líneas de succión, entrada por sellos de la bomba dañados y agitación en el tanque causada por el retorno violento del aceite. Cuando las burbujas son sometidas a una rápida compresión, como por ejemplo en la succión de una bomba de alta presión o en la región de máxima carga en un cojinete, estas burbujas pueden sufrir una rápida compresión adiabática lo que origina un rápido incremento en la temperatura del aceite. Típicamente, durante la compresión adiabática de las burbujas se pueden alcanzar temperaturas en el rango de los 550°C. A esta temperatura se inicia la degradación térmica del fluido y por consiguiente la formación de barniz.
La generación de cargas electrostáticas o triboeléctricas ocurre en los sistemas de lubricación de las turbinas como resultado de la fricción interna del fluido con los componentes del sistema. La magnitud de estas cargas depende de muchos factores que se interrelacionan entre s, incluyendo aspectos relacionados con el medio ambiente. Este efecto se manifiesta así mismo de diferentes maneras, siendo el más representativo el de un sonido audible como un “clic” cuando ocurre la descarga de la electricidad acumulada. Esto provoca chispas internamente en el sistema. Efectos menos aparentes implican la migración de estas cargas eléctricas aguas abajo del filtro, lo que produce daños en los componentes del sistema y en el filtro.
Recientemente, se ha puesto atención directa a la electrificación del fluido y a las descargas de la estática como uno de los principales contribuyentes a la formación de lodo y barniz en los sistemas de lubricación de las turbinas. La cantidad de carga generada por el flujo del hidrocarburo a través de los filtros está relacionada con alguna de las propiedades de los fluidos y de los filtros. La generación/acumulación de cargas generalmente se incrementa cuando se aumenta el flujo de aceite (velocidad a través de la media filtrante), cuando se reduce la conductividad del fluido, con algunos paquetes de aditivos y a baja temperatura (mayor viscosidad).
En la carcasa del filtro, la carga del elemento filtrante será de signo opuesto a la del fluido. La carga del fluido será transmitida aguas abajo, y si se acumula suficiente carga, se excede la constante dieléctrica del fluido. Entonces se produce a continuación una descarga en una parte conductora del sistema de filtración o del fluido que es de baja magnitud, lo que resulta en un potencial daño a los componentes del sistema. Lo grande del daño dependerá del material involucrado y de la magnitud de la carga generada.
Se han desarrollado varios métodos para tratar de aliviar el potencial de acumular cargas estáticas en los sistemas de lubricación. Entre ellos está el uso de aditivos anti-estáticos, los cuales no son adecuados para aceites de turbina; el uso de mallas conductoras aguas debajo de la media filtrante, las cuales tienen una limitada actividad en la prevención de acumulación de cargas en el fluido; e incrementando el tiempo para que la carga disminuya, lo cual requiere de cambios en el diseño del sistema. Filtrar el fluido con un flujo menor (por ejemplo, incrementando el tamaño del filtro) corrige el problema, pero no es una opción viable en algunos sistemas. Algunos fabricantes han introducido filtros con media de filtración diseñada para no generar cargas muy similares a los filtros estándar hechos a base de fibra de vidrio.
En el año 2004, se introdujo una nueva serie de media filtrante para disipar cargas electrostáticas (EDS) y eliminar el potencial problema de generación de dichas cargas durante la filtración de hidrocarburos. Extensos ensayos en condiciones controladas de laboratorio y en equipos operando en muchas aplicaciones industriales han mostrado que este tipo de media filtrante elimina los daños a los filtros y reduce significativamente la generación de cargas electrostáticas cuando se compara con las medias filtrantes de fibra de vidrio.
Tecnologías para la eliminación del barniz
Las soluciones actualmente disponibles para la eliminación del barniz en los aceites de turbina se dividen en tres categorías – purificación electrostática, limpieza/lavado químico y adsorción con media filtrante desechable.
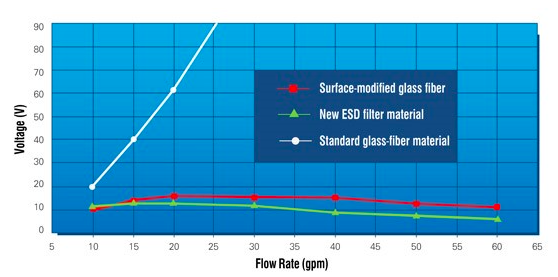
Cargas en el fluido usando filtro estándar de fibra de vidrio y media filtrante para disipar cargas electrostáticas (EDS).
El método de cargas electrostáticas, opera como una filtración riñón en el tanque principal, sometiendo al fluido a un campo eléctrico, haciendo que los precursores de barniz se carguen y se aglomeren en partículas grandes que luego son capturadas en un filtro o atraídos hacia una superficie cargada desechable.
Hay varios diseños basados en variantes del principio de cargas electrostáticas para lograr este objetivo. Los dispositivos del tipo electrostático eliminan los precursores de barniz del fluido, y a medida que el fluido es limpiado, los depósitos de barniz suave de la superficie de la máquina son re-suspendidos en el fluido y eliminados, dando como resultado una limpieza de los depósitos que se ha acumulado sobre dichas superficies en el tiempo.
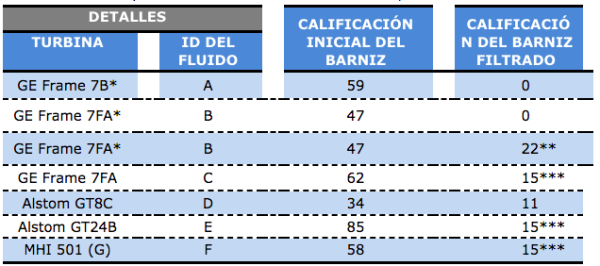
* Calificación del barniz determinado por Herguth Laboratories.
** Filtrado a 70°C
*** La calificación del barniz del filtrado es estimada. El valor inicial fue determinado
por Analyst Inc.
Tabla 1.
Debido a que la eliminación del barniz de los componentes del sistema es un proceso muy lento, se recomienda que estos dispositivos se operen por periodos largos de tiempo o se instalen permanentemente. Hay reportes donde esta práctica es muy sensible a elevados contenidos de humedad y a altos niveles de partículas de desgaste en el fluido.
El método de lavado/limpieza química elimina el barniz utilizando productos químicos de limpieza que se hacen circular a través del sistema para disolver el barniz depositado en los componentes de la turbina. Estos productos ablandan y disuelven los insolubles y la acción de lavado suspende los depósitos más duros en el fluido, y que son eliminados conjuntamente con el fluido cuando este es drenado del sistema. Este proceso se lleva a cabo por algunas horas o días, dependiendo del tamaño del sistema y de la cantidad de barniz acumulado en los componentes.
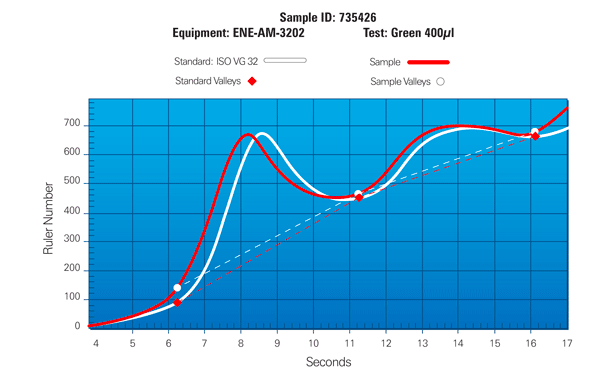
Aminas aromáticas = 99%, Fenoles Inhibidos > 100%
Resultados del análisis realizado a una muestra de aceite nuevo, sin usar
Una vez que la limpieza química se ha completado, el sistema debe ser lavado nuevamente con un fluido de lavado adecuado para eliminar cualquier residual del químico utilizado y asegurar la no contaminación del aceite nuevo cuando este se coloque en el sistema. Por ser este procedimiento más intensivo, la remoción de los depósitos de barniz es más rápida, sobre todo en sistemas de gran volumen. Adicionalmente, requiere de una estrecha supervisión ya que conlleva una pérdida de producción al encontrarse la turbina fuera de servicio.
El método de adsorción utiliza una media adsorbente con una gran área superficial y un alto volumen vacío, una velocidad del fluido relativamente baja y en algunos casos una afinidad electroquímica hacia los precursores de barniz. Muchos materiales pueden ser usados como adsorbentes, incluyendo celulosa comprimida, borra de algodón y media filtrante macro porosa como perlas de resina, tierras Fuller, carbón activado, etc.
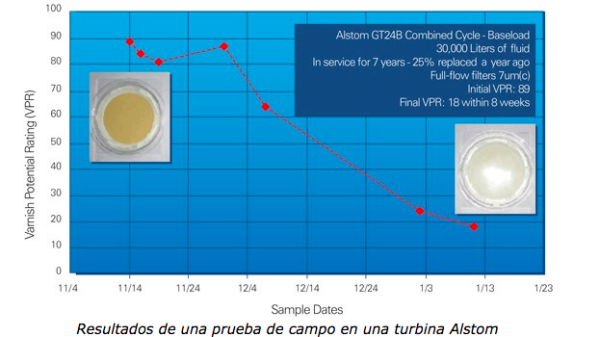
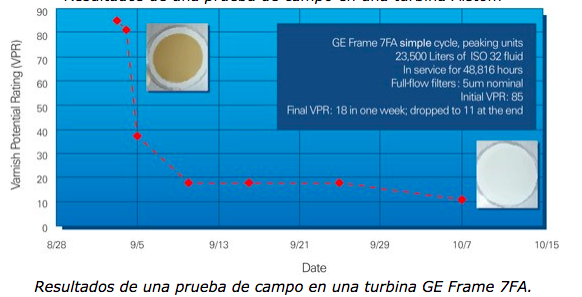
Hay dos tipos de adsorción: la fisisorción y la químisorción. La fisisorción, también conocida como adsorción física, es un proceso en el que las moléculas del adsorbente y las del precursores de barniz no forman enlaces químicos derivados de una reacción química, sino que están unidos por fuerzas electrostáticas débiles derivadas de momentos dipolares inducidos como las fuerzas de van der Walls. La estructura electrónica del precursor de barniz no cambia con la adsorción. Debido a su estructura química, se presume que las moléculas de barniz son atraídas por el adsorbente a través de las fuerzas moleculares débiles como los enlaces de hidrógeno.
Se ha desarrollado un medio filtrante basado en fisisorción, llamado Filtro Eliminador de Barniz (VFR). Este medio filtrante es un compuesto fabricado con una matriz de fibra de celulosa y otros materiales que le dan un alto volumen vacío y una matriz de fibra abierta. La resina unida, una matriz de fibra abierta con una gran permeabilidad, es necesaria para que el fluido entre en contacto con la gran área superficial de fibras largas donde se realiza la adsorción de los precursores de barniz. Las formulaciones especiales de resinas aglutinantes le proporcionan al medio filtrante una gran afinidad con los precursores polares de barniz, dando como resultado una elevada eficiencia en la eliminación y retención del material suspendido en el fluido.
El filtro VRF fue evaluado en un laboratorio utilizando muestras de aceite degradado obtenidas de turbinas en operación que habían reportado altos niveles de barniz. Los valores mostrados en la Tabla 1 fueron tomadas después de una filtración de una sola etapa a temperatura ambiente, excepto para el tercer ensayo, el cual fue llevado a cabo con una temperatura en el aceite de 70°C. La elevada calificación de barniz de la muestra filtrada a alta temperatura señala un bajo desempeño en la eliminación del barniz, posiblemente ocasionado por la alta solvencia de los precursores de barniz en el aceite y a la baja absorbancia a elevada temperatura.
También se realizaron ensayos para evaluar el impacto sobre los aditivos del aceite después de haber sido filtrados con el VRF. Los resultados indicaron que no un hubo ningún cambio significativo en los niveles de aminas aromáticas y los fenoles inhibidos entre la muestra de aceite que no se filtró y la muestra de aceite que se filtró 20 veces. La ausencia de algún agotamiento de estos aditivos indica que el filtro VFR no tiene efectos adversos notables sobre el lubricante.
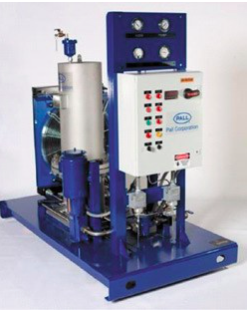
Este filtro eliminador de barniz portátil fue usado para tratar el aceite en dos turbinas en operación
Siguiendo el éxito obtenido en la validación en el laboratorio de la efectividad de este medio de filtración, se puso a prueba con dos turbinas en operación utilizando una plataforma con módulos de filtros VRF y su correspondiente sistema de control. El tratamiento del sistema de lubricación de la turbina implicaba la instalación de la plataforma de los filtros VRF en modo de filtración riñón, tomando el aceite en un extremo del tanque y devolviéndolo en forma continua en el extremo opuesto del mismo. Ambos ensayos corrieron simultáneamente con muy poca intervención de los operadores, utilizando un arreglo de tres módulos de filtros VFR por cada ensayo. La eliminación y retención del barniz en el medio filtrante se notó por el manchado de este ocasionado por el barniz depositado sobre el mismo.
Una diferencia significativa entre las dos turbinas tratadas con el VRF fue la cantidad de depósitos de barniz en los sistemas de lubricación. El interior de la carcasa del filtro principal del sistema de lubricación de la turbina Alstom se notó la presencia de una capa gruesa de barniz de color marrón. En el sistema de lubricación de la turbina GE Frame 7FA no se observaron tales depósitos.
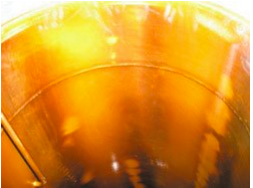
Se encontraron depósitos de barniz en el interior de la carcasa del filtro del sistema de lubricación de la turbina Alstom
Luego de la limpieza de la turbina Alstom, se retiró la plataforma con los filtros VRF, y se le reinstaló el filtro electrostático que se había estado utilizando antes del tratamiento con el VRF. Se tomó una muestra de la turbina Alstom seis meses después del tratamiento con el VRF y se encontró un elevado nivel de barniz. Se tomó una muestra de la turbina GE Frame 7FA dos meses después del tratamiento con VRF y se encontró que el nivel de barniz era muy similar al que se encontró cuando el tratamiento fue finalizado.
Se cree que la razón por la cual se presentaron de nuevo altos niveles de barniz en la turbina Alstom, fue debido a que los depósitos pesados de barniz del sistema de lubricación, no fueron completamente eliminados durante los ocho días que duró el tratamiento, a pesar de que los precursores de barniz en la fase aceite habían disminuido a niveles bastante bajos. La diferencia en la velocidad de limpieza del aceite, que fue mayor en el caso de la turbina Alstom, y el ligero incremento en los niveles de barniz después de su disminución inicial, pueden también ser atribuidos en gran parte a la presencia de los depósitos pesados de barniz en el sistema de lubricación de la turbina Alstom.
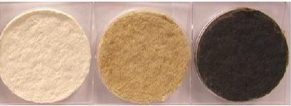
Esta imagen muestra un medio VRF usado recibido en campo (derecha), lavado con hexano (centro) y lavado con tolueno (izquierdo)
Los dos ensayos de campo revelaron que la cantidad y tipo de barniz en los sistemas de lubricación tienen relación con la rapidez con que al aceite se le puede eliminar el barniz y por cuanto tiempo después del tratamiento puede mantenerse libre de niveles elevados de barniz. Existen también otras variables además de los niveles de depósitos, tales como el tipo de barniz, la temperatura, el ciclo de trabajo, el estado de los depósitos, etc., que tienen influencia en la velocidad con que el barniz es eliminado del aceite y de su disolución de nuevo en el fluido.
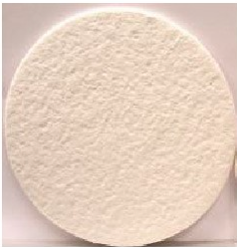
Foto de un medio VRF sin usar
En resumen, la disminución de los problemas relacionados con el barniz en los sistemas de lubricación y control de las turbinas requiere no solamente de la limpieza de los precursores de barniz del aceite y de los depósitos solubles de las superficies lubricadas, sino de evitar también su formación. La tecnología de filtros de adsorción está diseñada para eliminar los precursores polares de barniz y ha demostrado también ser eficaz en la eliminación del barniz en los sistemas de lubricación de las turbinas.
Además, las cargas electrostáticas inducidas por la filtración, pueden ser controladas utilizando medias filtrantes disipadoras de corriente, que producen menos cargas en el aceite, disminuyendo el daño asociado a este, debido a la filtración más fina requerida por las turbinas actuales.
Noria Corporation. Traducido por Roberto Trujillo Corona, Noria Latín América.