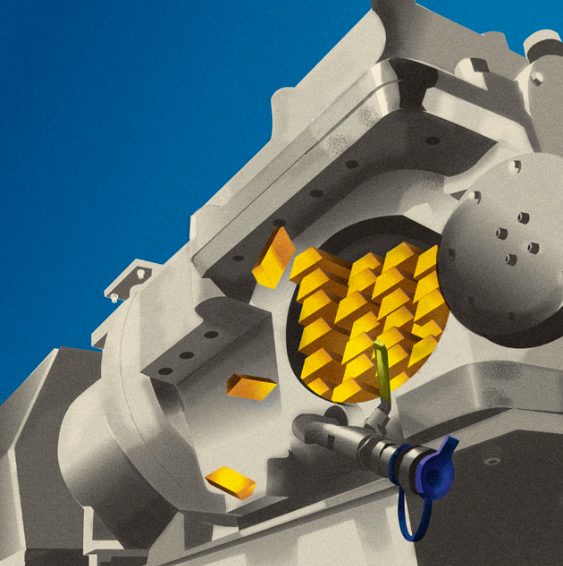
Quizá su planta tenga un programa de análisis de aceite bien establecido que provee excelentes resultados, pero ¿está usando toda la información disponible en los reportes? Si todo en el reporte está correcto y dentro de las especificaciones, ¿hace algo más con la información? ¿Sigue permitiendo que se ejecute la orden de mantenimiento preventivo basado en tiempo para cambiar el aceite y el filtro? Si respondió sí a esta última pregunta, podría estar gastando miles o quizá cientos de miles de dólares en cambios de aceite innecesarios. También podría estar introduciendo error humano y creando más problemas con mantenimientos no necesarios.
¿Qué es el cambio de aceite basado en condición?
Existen tres tipos de cambio de aceite: reactivo, preventivo y proactivo o predictivo. ¿Cuál de estos es cambio de aceite basado en condición? Es el cambio de aceite proactivo o predictivo, que se hace en el momento correcto y por las razones adecuadas.
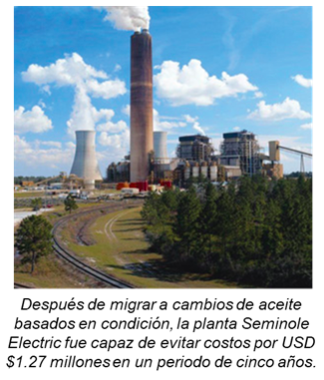
Anteriormente, cuando el análisis de aceite no era una práctica común en la mayoría de las fábricas grandes, el fabricante de equipo original (OEM, por sus siglas en inglés) establecía los lineamientos y recomendaba las frecuencias de cambio de aceite. Usualmente se protegen y se cargan hacia el lado seguro, dejando al lubricante con casi un 50% de su vida útil. Algunas veces incluso la garantía está involucrada, requiriendo que el aceite se cambie en intervalos específicos para asegurar que se mantenga la garantía. En años recientes, la mayoría de los OEM reconocerán un buen programa de análisis de lubricantes y permitirán intervalos de drenado de aceite extendidos sin comprometer las condiciones de la garantía. Desde luego, esto es algo que debe discutir y acordar antes de decidir extenderlos unilateralmente.
Los cambios de aceite basados en condición no deben tomarse a la ligera. Usted puede cosechar los beneficios de reducción de costos o experimentar fallas catastróficas si no se hace adecuadamente. También es importante nombrar un responsable (champion) del programa de análisis de aceite.
No todas las máquinas son candidatos para extender los intervalos de cambio. Necesita entender la máquina, los materiales de los que están hechos sus componentes y los parámetros de operación. También debe incorporar técnicas adecuadas de toma de muestra, así como un conjunto de pruebas de rutina y excepción para efectuarlas periódicamente y asegurar que no está omitiendo información valiosa al tomar decisiones de extender los periodos de cambio.
Con un buen programa de análisis de lubricantes usted puede establecer tendencias con la información de los equipos, lo que le ayudará a decidir cuáles máquinas son elegibles para un cambio de aceite extendido. Es cierto que, a mayor tamaño del depósito, mayores los ahorros. Sin embargo, si está realizando análisis de aceite de depósitos pequeños debido a su criticidad, ¿por qué no tomar ventaja de esa información también? Otros factores que pueden ser considerados para extender los intervalos de cambio incluyen el volumen, la cantidad de aceite de relleno, las temperaturas de operación, la calidad del filtro de aceite y tipo de respiradores instalados.
Adicionalmente, usted debería entender claramente cómo se hacen las diferentes pruebas del análisis de lubricante y las fortalezas y debilidades de cada una. Por esto es importante tener una buena comunicación con su laboratorio de análisis de lubricantes y discutir cualquier duda, así como las pruebas especiales que puedan requerirse para obtener toda la información necesaria para la toma de decisiones con respecto de la extensión de los intervalos de cambio. Entre más información le dé a su laboratorio sobre su programa y los objetivos que pretende alcanzar, mejores serán los resultados.
También es crítico establecer previamente una línea base para los aceites nuevos. Si su laboratorio no conoce las características y propiedades del aceite nuevo, ¿cómo va a saber que algo está mal con el aceite usado, si no tiene nada contra qué comparar?
Limitantes de las pruebas de análisis de aceite
Una de las debilidades de las pruebas del análisis de aceite es que pueden dar un falso sentido de que todo está bien. Por ejemplo, el análisis espectrométrico solo identifica partículas menores a 7 micrones (depende de la composición de la partícula y el método de análisis), por lo que puede haber trozos de metal en el aceite y solo ver resultados en el reporte con unas 100 ppm de hierro. Pueden utilizarse métodos alternativos para obtener la información necesaria, como digestión ácida o por microondas. Esto rompería las partículas más grandes de modo que pueda efectuarse un quemado más completo y por el espectro se les pueda identificar y cuantificar.
La ferrografía analítica es otro método excelente para detectar y caracterizar partículas ferrosas grandes, así como otras partículas en la muestra de aceite. Esta prueba no solo cuantifica las partículas, sino que identifica tamaños, formas y morfología de las partículas, lo que puede ayudar a determinar el tipo de desgaste que está ocurriendo.
Es importante tener en mente que un alto nivel de cobre pudiera no ser un desgaste, sino una lixiviación del enfriador. El dialquiditiofosfato de Zinc (ZDDP) es un aditivo que algunas veces causa lixiviación del cobre y por lo tanto resultados elevados de este metal. El silicio es otro falso positivo muy común. A menos que esté acostumbrado a ver silicio en sus análisis, un incremento drástico es, con mucha certeza, resultado de una reparación en la que se utilizó silicón para vulcanizar a temperatura ambiente (RTV) o un sellador a base de silicón.
El agua puede ser otro de los resultados engañosos en sus reportes. La mayoría de los laboratorios efectúan la prueba de crepitación para identificar la presencia de agua en las muestras de aceite, mientras que otros lo hacen por espectroscopia infrarroja por transformadas de Fourier (FTIR. La prueba de crepitación puede identificar agua por arriba de 500 ppm, aunque un buen técnico de laboratorio puede incluso encontrar agua a menor concentración en algunos aceites con bajo contenido de aditivos (por ejemplo, aceite para turbinas). La prueba de crepitación es aproximada y no se considera cuantitativa. Si necesita conocer la cantidad exacta de agua, haga una prueba de Karl Fischer, en el entendido de que también puede haber interferencias con esta prueba. Asegúrese de especificar que se utilice el método de evaporador o secado (también llamado codestilación), especialmente en aceites para motor.
El conteo de partículas es usualmente obtenido por medio de un contador láser. Aunque es un método preciso, los aceites muy oscuros, el agua y el aire atrapado pueden causar problemas. El conteo por bloqueo de poro se puede hacer en lugar del conteo láser cuando el aceite está demasiado oscuro o contaminado con agua. Este método no es tan preciso como el del láser, pero es una opción viable para evaluar la limpieza del fluido y evitar las interferencias mencionadas previamente.
Otra forma menos común para hacer conteo de partículas es el uso de una membrana Millipore. Puede ser costoso en tiempo y dinero, pero en situaciones específicas, se puede usar para un análisis de partículas en lugar de una ferrografía analítica.
Pruebas especiales
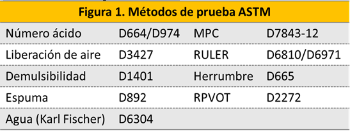
Aun con un extenso conjunto de pruebas, se requiere de pruebas especiales para proporcionar información adicional para extender los intervalos de cambio de aceite. Por ejemplo, puede hacerse la prueba de resistencia a la oxidación en recipiente rotatorio a presión (RPVOT) para determinar la estabilidad a la oxidación del lubricante en servicio en comparación con el lubricante nuevo. La prueba RULER ofrece otra manera de comparar el aceite usado contra el aceite en servicio para estimar la vida útil remanente (RUL, por sus siglas en inglés). Otras pruebas, como potencial de barniz, colorimetría por membrana (MPC, por sus siglas en inglés) y análisis espectrométrico cuantitativo (QSA, por sus siglas en inglés), pueden ayudar a identificar la cantidad de subproductos resultado de la degradación del aceite o el agotamiento de aditivos. Estos contaminantes suaves pueden causar problemas serios si no se atienden oportunamente.
La prueba de demulsibilidad se usa para determinar la capacidad del lubricante para separar el agua. Las pruebas de liberación de aire y de espumación también son importantes, debido que el aire no permite que se genere una película lubricante suficiente para mantener separadas a las superficies de la máquina. Las pruebas de herrumbre y corrosión a tira de cobre ayudan a identificar la cantidad de aditivos anticorrosivos que quedan en el lubricante, mientras que los números ácido y básico miden la tasa de cambio entre un lubricante nuevo y usado. Vea la Figura 1 para una lista de métodos ASTM.
Existen algunas pruebas especiales que pueden hacerse en lubricantes en servicio para ayudar a tomar decisiones sobre los intervalos de cambio. Una vez más, tener buena comunicación con el laboratorio será invaluable cuando requiera asegurar que tiene toda la información necesaria para alcanzar la reducción de costos y prevenir fallas catastróficas.
Reducción de costos
Con los lubricantes, existe el costo real (lo que usted paga al distribuidor por litro, kilogramo, balde o tambor) y el costo real. El costo real de un lubricante es el costo total desde la cuna a la tumba una vez que llega a su planta. Incluye la recepción, almacenamiento, despacho, instalación y disposición. Hace varios años se estimó este costo en un promedio de entre cuatro y siete veces el costo por litro. Para el caso especial del aceite contaminado (radioactivo), el costo podría ser hasta de 40 veces por litro. El costo medio de la industria por galón es de USD $9 a USD $14 para el aceite mineral y de USD $20 a USD $30 para el lubricante sintético, con la excepción de los sintéticos de alta especialidad que puede estar alrededor de USD $60 o más. Para el propósito de esta discusión, estimemos los aceites minerales a USD $10 por galón y los sintéticos a USD $25 por galón.
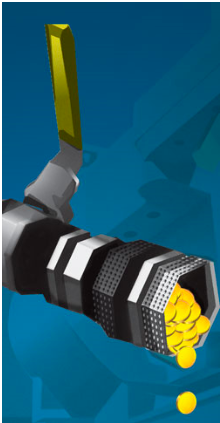
Con los lubricantes, existe el costo real (lo que usted paga al distribuidor por litro, kilogramo, balde o tambor) y el costo real. El costo real de un lubricante es el costo total desde la cuna a la tumba una vez que llega a su planta. Incluye la recepción, almacenamiento, despacho, instalación y disposición. Hace varios años se estimó este costo en un promedio de entre cuatro y siete veces el costo por litro. Para el caso especial del aceite contaminado (radioactivo), el costo podría ser hasta de 40 veces por litro. El costo medio de la industria por galón es de USD $9 a USD $14 para el aceite mineral y de USD $20 a USD $30 para el lubricante sintético, con la excepción de los sintéticos de alta especialidad que puede estar alrededor de USD $60 o más. Para el propósito de esta discusión, estimemos los aceites minerales a USD $10 por galón y los sintéticos a USD $25 por galón.
En la planta de Seminole Electric, que cuenta con dos unidades combinadas que utilizan carbón como combustible y generan 1,300 megavatios, el equipo monitoreado para efectuar los cambios de aceite basados en condición contiene 6,043 galones de aceite (ver Figura 2). Antes de que los cambios de aceite se hicieran en base a su condición, se efectuaban los cambios de aceite a algunas máquinas cada seis meses y en algunas cada 12 meses. Haciéndolo de esta manera, el consumo anual era de 7,948 galones de aceite. Si utilizáramos el costo promedio de USD $10 por galón y el costo real de siete veces el costo por galón, tendríamos un costo total real de USD $ 70 por galón. En un mundo perfecto, si se pudiera pasar un año sin efectuar un cambio de aceite en toda la maquinaria, se tendría un costo evitado de USD $ 556,360.
Como puede verse en la Figura 2, el tiempo promedio entre los cambios de aceite en la planta de Seminole Electric está ahora más cercano a 1.5 años, con algunos equipos que alcanzan los cinco años. En la maquinaria en las que se efectúan los cambios de aceite cada cinco años, se tiene un ahorro total de 18,145 galones de aceite, basado en las frecuencias de cambio de seis y 12 meses durante cinco años. Se evitan de cuatro a siete cambios de aceite, ya que la maquinaria se inspecciona generalmente cuando se hace el cambio de aceite en el quinto año o alrededor de 40,000 horas de operación. Esto equivale a un costo evitado de USD $1.27 millones para esos seis grupos de máquinas durante el período de cinco años.
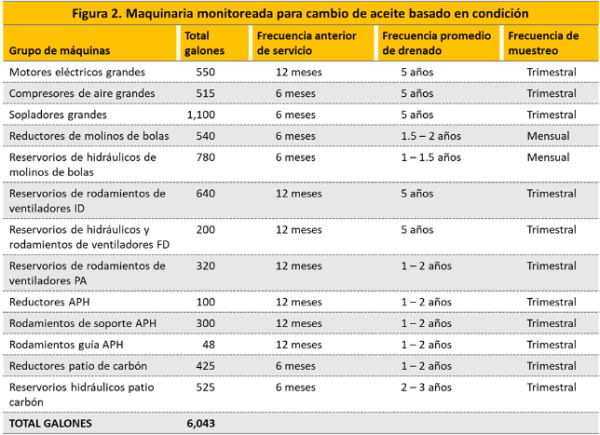
Tenga en cuenta que en esta lista no están incluidas las turbinas, los sistemas de control de las turbinas y las bombas de alimentación de calderas. Debido a su tamaño, estos depósitos, que suman en conjunto más de 25,000 galones de aceite, y los sistemas de filtración, generalmente tienen intervalos de cambio de aceite más largos.
Retorno de la inversión
Ahora consideremos el retorno de la inversión (ROI, por sus siglas en inglés) para los cambios de aceite basados en condiciones. El costo primario es el análisis del aceite. Con base en la Figura 2, se efectúan 792 tomas de muestra de aceite por año para el equipo listado, a un costo promedio de USD $20 a USD $40 por análisis de cada muestra. Tenemos un rango de entre USD $15,840 a $ 20 por muestra y $ 31,680 a $ 40 por muestra, lo que nos proporciona una idea del costo del análisis de aceite. Aunque USD $40 podría ser ligeramente alto, compensa por las pruebas especiales que en algunas ocasiones son necesarias para obtener información adicional a lo largo del año. Aún si incluye el salario de la persona que administra el programa de análisis de aceite en la planta, todavía estaría muy por debajo de la previsión de costos evitados de USD $556,360 por año.
Beneficios adicionales
Ahora que ha visto el potencial de reducción de costos del cambio de aceite basado en condición, examinemos algunos otros beneficios. Primero y sobre todo tenemos la liberación de horas hombre para desarrollar trabajo proactivo en equipos que realmente lo necesitan. También puede tener una reducción en las fallas de la maquinaria o en la mortalidad infantil, debido a que no necesariamente está exponiendo la maquinaria a errores humanos. Infortunadamente, muchas veces algo se hace mal, queda algo suelto o aparece alguna fuga. El sistema se mantendrá más limpio si no lo abre constantemente en un entorno industrial sucio o si no se revuelven los sedimentos que se han asentado en el fondo del depósito durante la operación. Probablemente también se reducirá el uso de los filtros, ya que no se cambiarán con base a un tiempo determinado, sino más bien cuando necesitan ser cambiados con base en la presión diferencial. También dejará menos huella en el medio ambiente al reducir el consumo de lubricantes nuevos y la generación de residuos de aceite usado para su disposición.
Es fácil ver cómo puede reducir sustancialmente los costos sin hacer nada más que un buen uso de la información que sus reportes de análisis de aceite le están dando. Debe ser alentador saber que está generando suficientes recortes en costo como para pagar por el programa de análisis de aceite. Si se maneja correctamente, puede comenzar a cosechar los beneficios del cambio de aceite basado en condición si hace las cosas adecuadas en el momento oportuno y por las razones correctas.
Noria Corporation. Traducido por Roberto Trujillo Corona, Noria Latín América.