Matthew Adams, Noria Corporation. Traducción por Roberto Trujillo, Noria Latín América
Qué es el desgaste adhesivo
Una de las principales preocupaciones de la lubricación de maquinaria es la generación de desgaste. Comprender este proceso, por qué ocurre, su presencia y desarrollo, cómo detectarlo y analizarlo, y qué medidas de prevención deben tomarse para evitarlo, puede mejorar en gran medida la confiabilidad de la maquinaria y el trabajo para minimizar el tiempo de paro asociado, lo que resulta en una experiencia más rentable y agradable. Echemos un vistazo más de cerca al desgaste adhesivo y analicemos los parámetros mencionados anteriormente. Si bien hay muchos tipos de generación de desgaste dentro de la lubricación, revisaremos específicamente el desgaste adhesivo. El desgaste adhesivo es el resultado de la transferencia de material de una superficie a otra, que suele tener lugar en aplicaciones deslizantes mal lubricadas. A medida que analicemos el desgaste adhesivo, resultará evidente que existen varios nombres alternativos asociados a menudo con este tipo de desgaste. Como tal, durante la discusión o el análisis uno puede encontrar terminología como raspado, agarre, agrietamiento, frotamiento y desgarre, y debe tener en cuenta que todos estos pueden y deben caer dentro del ámbito de la adhesión.Fuentes de desgaste adhesivo
Durante una lubricación deslizante inadecuada, las asperezas o los picos en la superficie están sujetos a interactuar entre sí. A medida que esto sucede, una fuerte interfaz adhesiva puede resultar en “soldadura en frío” y el potencial de superficies más rugosas y la generación de desgaste se intensifica por medio de la transferencia de fragmentos de material. Es importante saber que hay dos elementos básicos que fomentan el desgaste adhesivo: 1) la propensión de distintos tipos de materiales a formar sólidos o compuestos una vez que se produce el contacto y 2) la limpieza de las superficies que interactúan entre sí. Dicho esto, hay diversos factores de influencia que deben tenerse en cuenta. También deben tomarse en consideración el paquete de aditivos y el espesor de la película lubricante, el tamaño de los componentes que conforman el activo, y ciertos parámetros específicos de operación, como la carga y la velocidad. A medida que comienza a producirse el desgaste adhesivo, a menudo se forman otros dos tipos de desgaste. A cargas muy elevadas, las partículas suelen ser óxidos, pero a cargas más bajas son metálicas. El proceso de oxidación ocurre cuando las películas de protección y desgaste comienzan a desgastarse y el proceso metálico comienza inmediatamente después. Es durante la transición del desgaste oxidativo al metálico cuando a menudo hay un aumento inmediato en la tasa de desgaste. La severidad del desgaste adhesivo generado durante este proceso es directamente proporcional a la carga aplicada y la distancia recorrida durante el contacto en este tiempo. Ahora que comprendemos mejor cómo se produce el desgaste adhesivo, podemos empezar a analizar las causas de esta interacción indeseable entre las superficies. Hay una multitud de causas notorias que impulsan este contacto no deseado y se reducen aproximadamente a cuatro fuerzas impulsoras principales: 1) carga extrema o inadecuada, 2) temperaturas y presiones elevadas, 3) aceleración o desaceleración en la zona de carga, y 4) humedad excesiva presente en la zona de carga. Como se mencionó anteriormente, tener un espesor de película lubricante suficiente y un paquete de aditivos disponible para combatir lo relativo a la carga, así como considerar la temperatura máxima de funcionamiento al seleccionar los lubricantes, ayudará a reducir estas preocupaciones, pero a medida que las temperaturas superen el rango objetivo identificado, haya presencia notable de humedad y comience a producirse una carga excesiva, es probable que surja uno o más de estos escenarios y comience el proceso de generación de desgaste adhesivo. Los componentes más comunes que se verán afectados directamente por el desgaste adhesivo son los rodamientos, los cilindros, las cajas de engranajes, los pistones y las placas oscilantes.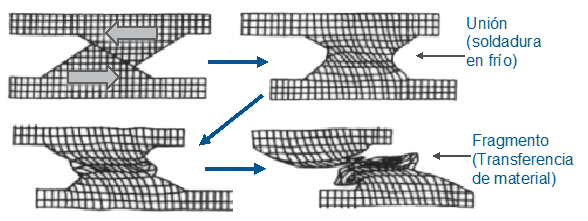
Figura 1: Interacción de desgaste adhesivo entre superficies
Presencia y desarrollo
Reconocer la presencia del desgaste adhesivo en los sistemas de lubricación es clave, y saber cómo se ve este desgaste y cómo progresa puede ayudar a minimizar esta preocupación. La apariencia general del desgaste adhesivo casi siempre variará dependiendo de su nivel de severidad. Este rango de gravedad se divide comúnmente en tres áreas específicas: 1) desgaste normal o leve, 2) desgaste moderado y 3) desgaste excesivo o severo. El desgaste adhesivo normal o leve ocurre durante el desgaste inicial de las asperezas a pequeña escala y puede verse como un pulido. Este desgaste puede aparecer durante el período de rodaje o asentamiento de la máquina o más comúnmente durante la etapa inicial de desgaste adhesivo. Este desgaste de etapa inicial a menudo no es visible a simple vista, pero comúnmente se nota con una inspección más detallada de los pequeños desgarros de soldadura que con frecuencia se forman en una línea. Es importante tener en cuenta una indicación temprana de este patrón de desgaste, pero es típico el uso continuo del equipo. El desgaste adhesivo moderado se vuelve mucho más notable y, a menudo, forma líneas o marcas de color oscurecidas en el componente. También pueden comenzar a aparecer algunos tonos azulados en la superficie del componente debido a la naturaleza térmica del rayado presente en esta etapa. Los desgarres adicionales por soldadura se vuelven notorios y, a menudo, provocan que el metal se desplace o “se salga” de la cara del componente y se aprecie un leve rayado. Es importante realizar un seguimiento y monitorear la tendencia del desarrollo del desgaste en esta etapa y trabajar para ejecutar un plan en el futuro cercano para abordar esta situación durante una parada del equipo. El desgaste adhesivo excesivo o severo es la etapa más dañina del desgaste adhesivo. En esta etapa de desgaste, el “desplazamiento” del metal comienza a volverse excesivo y se acumula a medida que se mueve a lo largo de la superficie, tomando la apariencia de estar “embarrado”. Esto conduce a raspaduras más notorias, superficies rasgadas, grietas y macropitting. En casos más severos, la capa superficial puede dislocarse de la subsuperficie debido a la alta fricción tangencial, lo que resulta en un efecto de acumulación o avalancha de material que promueve aún más el progreso de este “embarrado”. Si se observa un desgaste adhesivo excesivo o severo, existe una mayor preocupación por la falla del equipo y se debe establecer un plan para retirar del servicio este equipo y realizar un reemplazo tan pronto como sea posible. Vale la pena mencionar que, como cualquier otra progresión de desgaste, es imperativo identificar qué patrón de desgaste está presente y trabajar para aislar y separar ciertos patrones entre sí. Hacerlo ayudará a generar resultados correctos del análisis de la causa raíz.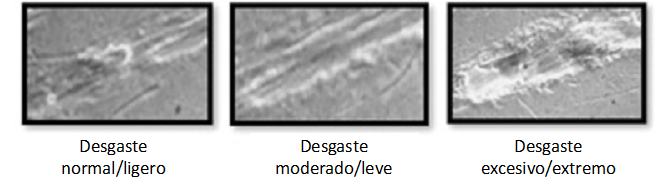
Figura 2: Ejemplos del progreso del desgaste de las superficies
Detección y análisis
Es imperativo identificar la detección de cada etapa de la generación de desgaste adhesivo y existen formas específicas de validar esta preocupación a través del análisis. Las inspecciones visuales básicas son el método más simple para identificar problemas relacionados con el desgaste adhesivo. Las inspecciones de la superficie de la máquina deben realizarse con el activo fuera de servicio mientras que las inspecciones visuales, cuando corresponda, de la generación de partículas de desgaste acumuladas en los puertos de inspección, como los visores del fondo, sedimentos y agua BS&W (por sus siglas en inglés) y los Pods de monitoreo de condición (CMP, por sus siglas en inglés) se pueden observar mientras el activo está en servicio. Generalmente, estas inspecciones visuales solo funcionan para identificar el desgaste adhesivo durante las últimas etapas de uso debido a que el desgaste incipiente a menudo es más pequeño de lo que el ojo humano puede observar. Durante las inspecciones visuales, es obligatorio que el observador busque específicamente un desgaste notable en las superficies de la máquina en cuestión e informe cualquier anomalía visible observada para que la planificación y acción detalladas puedan iniciarse rápidamente si es necesario. La inspección con boroscopio es otra herramienta de análisis visual que debe utilizarse para buscar la generación de desgaste adhesivo. Esta inspección visual avanzada proporcionará muchos más detalles sobre cualquier inquietud relacionada y brindará información sobre el desgaste adhesivo mucho antes en el proceso de generación. El uso de esta herramienta de análisis e inspección a menudo se activa en respuesta a una inquietud notada durante el mantenimiento predictivo, como el análisis de vibraciones o el análisis de aceite, pero se puede utilizar como una herramienta independiente durante el tiempo de inactividad programado. El análisis de vibraciones es otra opción comúnmente utilizada para detectar el desarrollo y la generación de desgaste. Si bien el análisis de vibración tradicional proporcionará conciencia de las preocupaciones relacionadas con el desgaste y las fallas en etapas posteriores en el proceso, el análisis de alta frecuencia centrado en el impacto puede ayudar a obtener información valiosa durante las primeras etapas de desarrollo del desgaste de la superficie. El análisis de aceite también puede ayudar a identificar el desgaste adhesivo. Si bien la detección temprana del desgaste adhesivo no se distingue comúnmente en el crecimiento de la población de partículas debido a la liberación limitada de material de la superficie en la etapa inicial de generación de desgaste, existen medidas adicionales dentro del análisis de aceite que pueden proporcionar indicios del creciente potencial de que ocurra desgaste adhesivo. Un parámetro específico que vale la pena observar es la tendencia de los aditivos para el control de fricción y desgaste. Si bien esta tarea a veces puede ser difícil debido a que ciertos elementos aparecen tanto como paquetes de aditivos como contaminantes en el sistema, se puede justificar hacerlo. Si se conoce bien el activo en cuestión y se comprende el análisis de aceite en general, se puede identificar la pérdida de aditivos de control de desgaste y fricción en el sistema que pueden pronosticar el avance inicial de las partículas de desgaste adhesivo. A medida que la generación de desgaste adhesivo avanzado comienza a aumentar en el activo, la valiosa información obtenida a través del análisis espectrométrico, conteo de partículas, análisis de humedad, pruebas de membrana (parche), densidad ferrosa y ferrografía analítica proporcionará detalles específicos con respecto al volumen, tamaño, forma y fuente potencial del problema.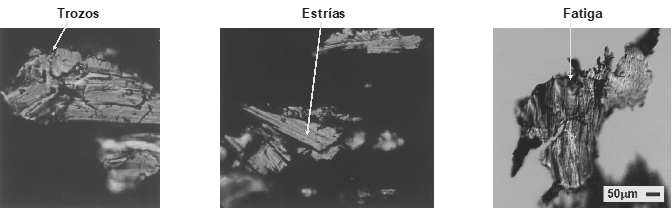
Figura 3: Ejemplos de partículas de desgaste adhesivo
Prevención
Como profesionales de la confiabilidad, necesitamos tener un conocimiento sólido de la generación de desgaste, por qué surge y cómo abordar o minimizar su aparición. Como ya hemos señalado en la sección de fuentes de desgaste, el desgaste adhesivo generalmente es causado por una carga excesiva o insuficiente y por una selección incorrecta del lubricante. Identificar adecuadamente los problemas de carga durante la fase de instalación y utilizar el lubricante con las características correctas, que tenga en cuenta la aplicación, el espesor de la película, la temperatura, los factores estresantes de la superficie y el ambiente de operación constituirá un caso sólido para minimizar los problemas de generación de desgaste adhesivo. Además, identificar la entrada de humedad, abordar los problemas de alineación, y monitorear adecuadamente el activo a través de los métodos de detección y análisis indicados proporcionará apoyo adicional para minimizar la posibilidad de que este problema ocurra durante la operación. Referencias- Noria Corporation Oil Analysis III Training Manual. Tulsa, OK: Noria Corporation
- WF Gale y TC Totemeier. Libro de referencia de Smithells Metals (octava edición), Butterworth-Heinemann, 2004
- https://onyxinsight.com/wind-turbine-failures-encyclopedia/bearing-failures/adhesive-wear/
- https://www.tribonet.org/analyzing-the-evolution-of-adhesive-wear/
- https://www.wmv.nl/adhesive,_abrasive_and_tribo_oxidative_wear_prevention
- Trevor M. Hunt. Manual de análisis de partículas de desgaste y detección de partículas en líquidos, Elsevier Science Publishers LTC, 1993
- Atlas de partículas de desgaste, Noria Corporation, 2012