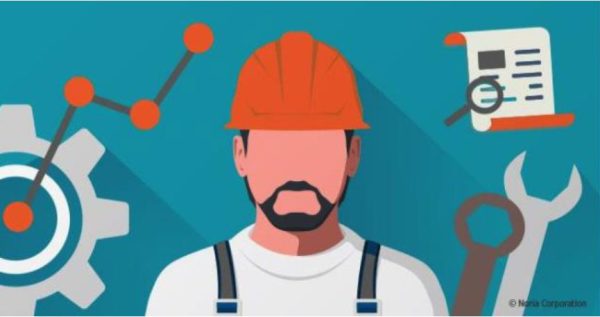
Según Aberdeen Research, el costo promedio por hora del tiempo de inactividad en todas las empresas es de $ 260,000 y parece estar aumentando. Esta cifra es superior a los datos de 2014 de $ 164,000. Esto es especialmente preocupante ya que casi toda la producción industrial y de fabricación se realiza utilizando máquinas, lo que hace que dependa en gran medida de las máquinas que funcionan continuamente.
Entonces, ¿cómo puedes ayudar a remediar este problema? El mantenimiento productivo total (TPM) es el proceso de usar máquinas, equipos, empleados y procesos de apoyo para mantener y mejorar la integridad de la producción y la calidad de los sistemas. En pocas palabras, es el proceso de involucrar a los empleados en el mantenimiento de sus propios equipos y enfatizar las técnicas de mantenimiento preventivo y proactivo. El mantenimiento productivo total se esfuerza por una producción perfecta. Es decir:
- Sin averías
- No se detiene ni corre lentamente
- Sin defectos
- Sin accidentes
Dado que el objetivo del mantenimiento productivo total es mejorar la productividad al reducir el tiempo de inactividad, la implementación de un programa TPM puede afectar en gran medida la efectividad general de su equipo (OEE) con el tiempo. Para hacer esto, el mantenimiento preventivo siempre debe estar a la vanguardia de la mente de todos. Por ejemplo, reparar máquinas con la mentalidad de “lo arreglaremos cuando se rompa” no es una opción con mantenimiento productivo total. Un programa TPM ayuda a deshacerse de esta mentalidad y la convierte en una de poner la maquinaria en el foco central de una operación y maximizar su disponibilidad.
La mejora de la OEE a través de TPM a menudo se realiza formando pequeños equipos multidisciplinarios para abordar áreas centrales como el mantenimiento preventivo y autónomo, la capacitación de los empleados que operan maquinaria y la seguridad y la estandarización de los procesos de trabajo. El mantenimiento productivo total se centra en el uso eficiente y efectivo de los medios de producción, lo que significa que todos los departamentos deben participar. Estos pequeños equipos trabajan juntos para aumentar la productividad y disminuir el tiempo de inactividad a través de la confiabilidad del equipo.
Beneficios del mantenimiento productivo total (TPM)
Pasar del mantenimiento reactivo al predictivo es una de las mayores ventajas de implementar un programa TPM. El mantenimiento reactivo o “extinción de incendios” es costoso, ya que no solo paga la factura de las reparaciones de maquinaria, sino que también se ocupa del costo del tiempo de inactividad no planificado. Echemos un vistazo a algunos de los beneficios directos e indirectos que resultan del mantenimiento productivo total.
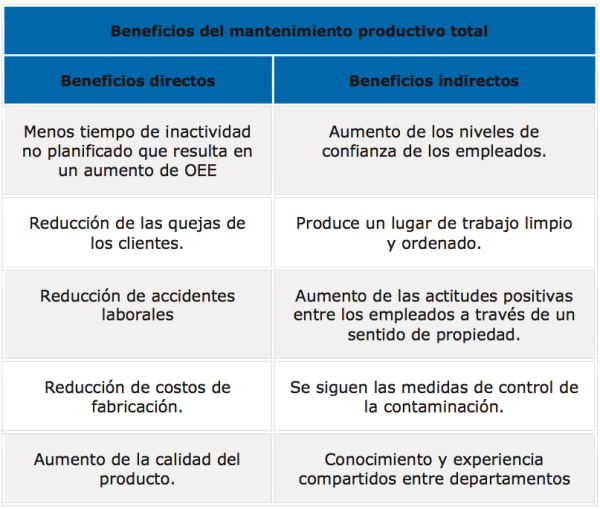
Los 8 pilares del mantenimiento productivo total (TPM)
El mantenimiento productivo total tradicional fue desarrollado por Seiichi Nakajima de Japón. Los resultados de su trabajo sobre el tema llevaron al proceso de TPM a fines de los años sesenta y principios de los setenta. Nippon Denso (ahora Denso), una compañía que creó piezas para Toyota, fue una de las primeras organizaciones en implementar un programa TPM. Esto dio como resultado un punto de referencia internacionalmente aceptado sobre cómo implementar TPM. Al incorporar técnicas de fabricación esbelta, TPM se basa en ocho pilares basados en el sistema 5-S. El sistema 5-S es un método de organización basado en cinco palabras japonesas y su significado:
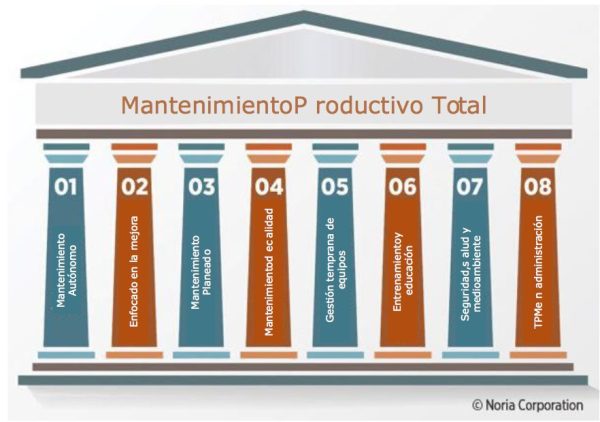
- Seiri (organizar): eliminar el desorden del espacio de trabajo
- Seiton (orden): asegure el orden siguiendo “un lugar para todo y todo en su lugar”
- Seiso (limpieza): limpia el espacio de trabajo y mantenlo así
- Seiketsu (estandarizar): estandarizar todos los procesos de trabajo, haciéndolos consistentes
- Shitsuke (sostener): reforzando constantemente los primeros cuatro pasos
Los ocho pilares del mantenimiento productivo total se centran en técnicas proactivas y preventivas para ayudar a mejorar la confiabilidad del equipo. Los ocho pilares son: mantenimiento autónomo; mejora enfocada (kaizen); mantenimiento planificado; gestión de la calidad; gestión temprana de equipos; entrenamiento y educación; seguridad, salud y medio ambiente; y TPM en administración. Analicemos cada pilar a continuación.
1. Mantenimiento autónomo: el mantenimiento autónomo significa garantizar que sus operadores estén completamente capacitados en el mantenimiento de rutina, como la limpieza, la lubricación y la inspección, además de colocar esa responsabilidad únicamente en sus manos. Esto les da a los operadores de máquinas un sentimiento de propiedad de sus equipos y aumenta su conocimiento de la pieza particular del equipo. También garantiza que la maquinaria esté siempre limpia y lubricada, ayuda a identificar problemas antes de que se conviertan en fallas y libera al personal de mantenimiento para tareas de nivel superior.
La implementación del mantenimiento autónomo implica la limpieza de la máquina según un estándar de “línea de base” que el operador debe mantener. Esto incluye capacitar al operador en habilidades técnicas para realizar una inspección de rutina basada en el manual de la máquina. Una vez capacitado, el operador establece su propio horario de inspección autónoma. La estandarización asegura que todos sigan los mismos procedimientos y procesos.
2. Mejora enfocada: La mejora enfocada se basa en el término japonés “kaizen”, que significa “mejora”. En la fabricación, kaizen requiere mejorar funciones y procesos continuamente. La mejora enfocada analiza el proceso como un todo y genera ideas sobre cómo mejorarlo. Hacer que los equipos pequeños tengan la mentalidad de trabajar juntos de manera proactiva para implementar mejoras regulares e incrementales en los procesos relacionados con la operación del equipo es clave para TPM. La diversificación de los miembros del equipo permite la identificación de problemas recurrentes a través de una lluvia de ideas interfuncional. También combina información de toda la empresa para que los equipos puedan ver cómo los procesos afectan a los diferentes departamentos.
Además, la mejora focalizada aumenta la e ciencia al reducir los defectos del producto y la cantidad de procesos al tiempo que mejora la seguridad al analizar los riesgos de cada acción individual. Finalmente, la mejora enfocada asegura que las mejoras estén estandarizadas, haciéndolas repetibles y sostenibles.
3. Mantenimiento planificado: El mantenimiento planificado implica estudiar métricas como tasas de falla y tiempo de inactividad histórico y luego programar tareas de mantenimiento basadas en estas tasas de falla o períodos de inactividad pronosticados o medidos. En otras palabras, dado que hay un tiempo específico para realizar el mantenimiento del equipo, puede programar el mantenimiento para el momento en que el equipo esté inactivo o produciendo a baja capacidad, rara vez interrumpiendo la producción.
Además, el mantenimiento planificado permite la acumulación de inventario para cuando se produce el mantenimiento programado. Como sabrá cuándo cada pieza de equipo está programada para actividades de mantenimiento, tener esta acumulación de inventario asegura que cualquier disminución en la producción debido al mantenimiento se mitigue.
Tomar este enfoque proactivo reduce en gran medida la cantidad de tiempo de inactividad no planificado al permitir que se planifique la mayor parte del mantenimiento en momentos en que la maquinaria no está programada para la producción. También le permite planificar el inventario más a fondo al darle la capacidad de controlar mejor las piezas que son propensas al desgaste y las fallas. Otros beneficios incluyen una disminución gradual de las averías que conducen al tiempo de actividad y una reducción de las inversiones de capital en equipos, ya que se está utilizando a su máximo potencial.
4. Mantenimiento de calidad: toda la planificación y estrategia de mantenimiento en el mundo es en vano si la calidad del mantenimiento que se realiza es inadecuada. El pilar de mantenimiento de calidad se centra en la detección y prevención de errores de diseño de trabajo en el proceso de producción. Lo hace mediante el análisis de causa raíz (específicamente los “5 por qué”) para identificar y eliminar las fuentes recurrentes de defectos. Al detectar de manera proactiva la fuente de errores o defectos, los procesos se vuelven más confiables, produciendo productos con las especificaciones correctas la primera vez.
Posiblemente, el mayor beneficio del mantenimiento de calidad es que evita que los productos defectuosos se muevan por la línea, lo que podría generar una gran cantidad de modificaciones. Con un mantenimiento de calidad específico, se abordan los problemas de calidad y se implementan contramedidas permanentes, minimizando o eliminando por completo los defectos y el tiempo de inactividad relacionados con los productos defectuosos.
5. Gestión temprana de equipos: el pilar TPM de la gestión temprana de equipos toma el conocimiento práctico y la comprensión general de los equipos de fabricación adquiridos a través del mantenimiento productivo total y los utiliza para mejorar el diseño de nuevos equipos. Diseñar equipos con el aporte de las personas que más lo utilizan permite a los proveedores mejorar la capacidad de mantenimiento y la forma en que la máquina opera en futuros diseños.
Cuando se discute el diseño del equipo, es importante hablar sobre cosas como la facilidad de limpieza y lubricación, la accesibilidad de las piezas, la colocación ergonómica de los controles de una manera cómoda para el operador, cómo se producen los cambios y las características de seguridad. Adoptar este enfoque aumenta la e ciencia aún más porque el nuevo equipo ya cumple con las especificaciones deseadas y tiene menos problemas de arranque, por lo tanto, alcanza los niveles de rendimiento planificados más rápido.
6. Capacitación y educación: la falta de conocimiento sobre el equipo puede descarrilar un programa TPM. La capacitación y la educación se aplican a los operadores, gerentes y personal de mantenimiento. Su objetivo es garantizar que todos estén en la misma página con el proceso TPM y abordar cualquier brecha de conocimiento para que los objetivos de TPM sean alcanzables. Aquí es donde los operadores aprenden habilidades para mantener proactivamente el equipo e identificar problemas emergentes. El equipo de mantenimiento aprende a implementar un cronograma de mantenimiento preventivo y proactivo, y los gerentes conocen bien los principios de TPM, el desarrollo de los empleados y el entrenamiento. El uso de herramientas como lecciones de un solo punto publicadas en o cerca del equipo puede ayudar aún más a capacitar a los operadores en los procedimientos operativos.
7. Seguridad, salud y medio ambiente: mantener un ambiente de trabajo seguro significa que los empleados pueden realizar sus tareas en un lugar seguro sin riesgos para la salud. Es importante producir un entorno que haga que la producción sea más eficiente, pero no debe correr el riesgo de la seguridad y la salud de un empleado. Para lograr esto, cualquier solución introducida en el proceso TPM siempre debe considerar la seguridad, la salud y el medio ambiente.
Además de los beneficios obvios, cuando los empleados vienen a trabajar en un ambiente seguro cada día, su actitud tiende a ser mejor, ya que no tienen que preocuparse por este aspecto significativo. Esto puede aumentar la productividad de manera notable. Considerar la seguridad debe ser especialmente frecuente durante la etapa inicial de gestión de equipos del proceso TPM.
8. TPM en administración: un buen programa TPM es tan bueno como la suma de sus partes. El mantenimiento productivo total debe ir más allá del piso de la planta al abordar y eliminar las áreas de desperdicio en las funciones administrativas. Esto significa apoyar la producción mejorando cosas como el procesamiento de pedidos, la adquisición y la programación. Las funciones administrativas son a menudo el primer paso en todo el proceso de fabricación, por lo que es importante que estén optimizadas y sin desperdicios. Por ejemplo, si los procedimientos de procesamiento de pedidos se simplifican, el material llega al piso de la planta más rápido y con menos errores, eliminando el tiempo de inactividad potencial mientras se rastrean las piezas faltantes.
Cómo implementar el mantenimiento productivo total (TPM)
Ahora que conoce la base (sistema 5-S) y los pilares sobre los que se basa el proceso TPM, echemos un vistazo a cómo implementar un programa TPM. Esto generalmente se realiza en cinco pasos: identificar un área piloto, restaurar el equipo a condiciones óptimas de operación, medir la OEE, abordar y reducir las pérdidas mayores e implementar el mantenimiento planificado.
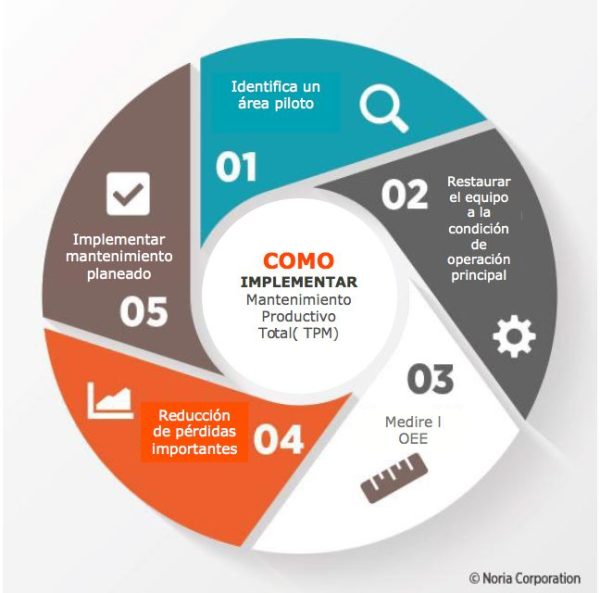
Paso 1: identificar un área piloto
El uso de un área piloto para comenzar la implementación ayuda a obtener una mayor aceptación del personal cuando ven los beneficios que resultan del proceso. Al elegir el equipo para un área piloto, considere estas tres preguntas:
- ¿Qué es lo más fácil de mejorar? Seleccionar el equipo que sea más fácil de mejorar le brinda la oportunidad de obtener resultados inmediatos y positivos; sin embargo, no prueba el proceso TPM tan fuertemente como las otras dos opciones.
- ¿Dónde está el cuello de botella? Elegir el equipo en función de dónde se detiene claramente la producción le proporciona un aumento inmediato en la producción total y proporciona una recuperación rápida. La desventaja es que emplear este equipo como piloto significa que está utilizando un activo crítico como ejemplo y se arriesga a la posibilidad de que esté fuera de línea por más tiempo de lo que desea.
- ¿Qué es lo más problemático? La reparación del equipo que da más problemas a los operadores será bien recibida, fortaleciendo el soporte para el programa TPM. Sin embargo, esto no le brinda tanta amortización inmediata como el enfoque anterior, y puede ser un desafío obtener un resultado rápido al resolver un problema no resuelto, lo que lleva al desinterés.
Si es la primera vez que implementa un programa TPM, su mejor opción suele ser el primer enfoque, el equipo más fácil de mejorar. Si tiene una experiencia extensa con un mantenimiento productivo total, puede optar por corregir el cuello de botella. Esto se debe a que puede crear existencias o inventarios temporales, asegurando que se pueda tolerar el tiempo de inactividad, lo que minimiza el riesgo.
Incluya a los empleados en todos los aspectos de su negocio (operadores, personal de mantenimiento, gerentes y administración) en el proceso de selección piloto. Es una buena idea usar un visual como un tablero de proyecto donde puede publicar el progreso para que todos lo vean.
Paso 2: Restaurar el equipo a la condición de funcionamiento principal
El concepto de restaurar el equipo a condiciones óptimas de operación gira en torno al sistema 5-S y el mantenimiento autónomo. Primero, los participantes de TPM deben aprender a mantener continuamente el equipo en su estado original usando el sistema 5- S: organizar, limpiar, ordenar, estandarizar y mantener. Esto puede incluir:
- Fotografiar el área y el estado actual del equipo y luego publicarlos en su tablero de proyecto.
- Despejar el área eliminando herramientas no utilizadas, escombros y cualquier cosa que pueda considerarse desperdicio.
- Organizar las herramientas y componentes que usa con regularidad (una tabla de sombra con contornos de herramientas es una opción popular).
- Limpiar a fondo el equipo y el área circundante.
- Fotografiar las mejoras del equipo y el área circundante y luego publicarlas en el tablero del proyecto.
- Crear un proceso de trabajo 5-S estandarizado para mantener la continuidad de este proceso.
- Auditar el proceso con menor frecuencia (primero diariamente, luego semanalmente, etc.) para garantizar que se siga el proceso 5-S (actualice el proceso para mantenerlo actualizado y relevante).
Una vez que haya establecido un estado de referencia del equipo, puede implementar el programa de mantenimiento autónomo capacitando a los operadores sobre cómo limpiar el equipo mientras lo inspecciona en bzusca de desgaste y anomalías. Crear un programa de mantenimiento autónomo también significa desarrollar una forma estandarizada de limpiar, inspeccionar y lubricar los equipos correctamente. Los puntos a tratar durante el período de planificación para el programa de mantenimiento autónomo incluyen:
- Identificar y documentar los puntos de inspección, incluidas las piezas que sufren desgaste.
- Aumentar la visibilidad cuando sea posible para ayudar con la inspección mientras la máquina está en funcionamiento (reemplazando la protección opaca con protección transparente).
- Identificar y etiquetar claramente los puntos de ajuste con sus configuraciones correspondientes (la mayoría de las personas colocan etiquetas con configuraciones directamente en el equipo).
- Identificar todos los puntos de lubricación y programar el mantenimiento durante los cambios o el tiempo de inactividad planificado (considere colocar puntos de lubricación de difícil acceso que requieran detener la máquina en el exterior del equipo).
- Capacitar a los operadores para que estén al tanto de cualquier problema emergente o potencial para que puedan informarlos al supervisor de línea.
- Crear una lista de verificación de mantenimiento autónomo para todas las tareas controladas por el operador.
- Auditar el proceso con menor frecuencia para garantizar que se siga la lista de verificación.
Paso 3: medir OEE
El paso tres requiere que realice un seguimiento de OEE para el equipo de destino, ya sea manualmente o utilizando software automatizado (siempre que incluya el seguimiento de código para el tiempo de parada no planificado). Para obtener detalles sobre cómo calcular OEE manualmente, consulte el artículo de Reliable Plant sobre OEE. La medición regular de OEE le brinda una con rmación basada en datos sobre si su programa TPM está funcionando y le permite realizar un seguimiento del progreso a lo largo del tiempo.
Dado que las mayores pérdidas con respecto al equipo son el resultado de un tiempo de inactividad no planificado, es importante clasificar cada evento de detención no planificado. Esto le brinda una visión más precisa de dónde se produce una detención. Incluya una categoría de tiempo de detención “desconocida” o “no asignada” por causas desconocidas.
Se recomienda que recopile datos durante un mínimo de dos semanas para obtener una representación precisa del tiempo de parada no planificado y una imagen clara de cómo las pequeñas paradas y los ciclos lentos afectan la producción. A continuación se muestra un ejemplo simplificado de una de las 5 principales tablas de pérdidas. Cada pérdida se clasifica y está en orden descendente desde la pérdida que causa más tiempo de inactividad hasta la pérdida que causa menos.
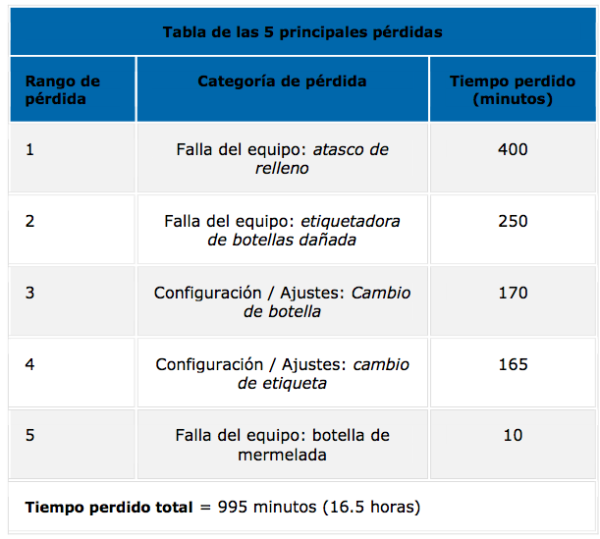
Paso 4: abordar / reducir las pérdidas importantes
Una vez que tenga una instantánea basada en datos de dónde están sus principales pérdidas, es hora de abordarlas. Este paso utiliza el pilar previamente discutido de mejora enfocada o kaizen. Para hacer esto, reúna un equipo multifuncional de operadores, personal de mantenimiento y supervisores que puedan diseccionar los datos de OEE utilizando el análisis de causa raíz e identificar la (s) causa (s) principal (es) de las pérdidas. El proceso de su equipo podría verse así:
- Seleccione una pérdida basada en OEE y datos de tiempo de detención. Esta debería ser la mayor fuente de tiempo de parada no planificado.
- Examine los síntomas del problema (s). Recopile información detallada sobre síntomas como observaciones, evidencia física y evidencia fotográfica. Se recomienda encarecidamente utilizar un diagrama de espina de pescado para rastrear síntomas y registrar información mientras está en el equipo.
- Con su equipo, discuta e identifique las posibles causas del (de los) problema (s), verifique las posibles causas con la evidencia que ha reunido y haga una lluvia de ideas sobre las formas más efectivas de resolver el problema.
- Programe el tiempo de inactividad planificado para implementar las soluciones acordadas.
- Una vez que se ha implementado el arreglo, reinicie la producción y observe cuán efectivo es el arreglo con el tiempo. Si resuelve el problema, tome nota para implementar el cambio y pasar a la siguiente causa del tiempo de detención. Si no, reúna más información y realice otra sesión de lluvia de ideas.
Paso 5: Implementar mantenimiento planificado
El último paso del proceso de implementación de TPM es la integración de técnicas de mantenimiento proactivo en su programa. Esto implica trabajar fuera del tercer pilar del mantenimiento planificado. Elija qué componentes deben recibir mantenimiento proactivo observando tres factores: componentes de desgaste, componentes que fallan y puntos de tensión. La identificación de los puntos de tensión a menudo se realiza mediante termografía infrarroja y análisis de vibraciones.
Luego, use intervalos de mantenimiento proactivos. Estos intervalos no están establecidos en piedra y se pueden actualizar según sea necesario. Para el desgaste y los componentes predichos basados en fallas, establezca el nivel de desgaste actual y luego un intervalo de reemplazo de referencia. Una vez que se hayan determinado, puede crear un programa de reemplazo proactivo de todos los componentes propensos al desgaste y fallas. Al hacer esto, use “tiempo de ejecución” en lugar de “tiempo de calendario”. Finalmente, desarrolle un proceso estandarizado para crear órdenes de trabajo basado en el programa de mantenimiento planificado.
Puede optimizar los intervalos de mantenimiento diseñando un sistema de retroalimentación. Las cosas como las hojas de registro para cada componente propenso al desgaste y a fallas donde los operadores pueden registrar la información de reemplazo y la condición del componente en el momento del reemplazo serán clave. Además, realice auditorías de mantenimiento planificadas mensualmente para verificar que se siga el cronograma de mantenimiento y que los registros de componentes se mantengan actualizados. Revise la información de los registros para ver si es necesario realizar ajustes en el programa de mantenimiento.
¿Qué pasa con los cuatro pilares restantes de TPM?
Es posible que haya notado que el proceso de implementación negó cuatro de los ocho pilares: gestión de calidad, gestión temprana de equipos, seguridad y TPM en la administración. Entonces, ¿cuándo debe presentar estas actividades? Deben instituirse según sea necesario. Echemos un vistazo a algunos ejemplos.
- El mantenimiento de la calidad debe introducirse en el proceso de TPM cuando los clientes o empleados plantean problemas importantes sobre la calidad.
- El mejor momento para usar la administración temprana de equipos es cuando los nuevos equipos están en la fase de diseño o se están instalando.
- La seguridad, la salud y el medio ambiente siempre deben estar a la vanguardia de cualquier diseño de proceso o programa. Úselo junto con el proceso de implementación de cinco pasos.
- El TPM en la administración debe abordarse antes de implementar la versión final de su programa de mantenimiento planificado. Problemas en la administración, como retrasos en las órdenes de trabajo, problemas de procesamiento y adquisición de piezas, retrasan en gran medida el resto del proceso de producción.
Mantenimiento de la mejora lograda con el mantenimiento productivo total (TPM)
La implementación de un programa de mantenimiento productivo total ofrece un éxito relativamente a corto plazo. El truco es mantener ese éxito a largo plazo. Esto comienza con los empleados. Si los empleados compran el programa TPM, imaginan el futuro mejorado de la compañía y pueden ver cómo este futuro mejorado los beneficia, puede crear una poderosa sensación de cohesión. Recompensar los logros es una excelente manera de fortalecer la cohesión establecida entre los empleados.
Otra forma de lograr una mejora sostenible con su programa TPM es tener un liderazgo activo y atractivo. Esto muestra la importancia del programa a través de no solo palabras sino acciones. Involucrar al liderazgo evita que los empleados vuelvan a caer en sus viejos hábitos y respire nueva energía en el proceso de manera regular.
Finalmente, no pase por alto a Kaizen. La mejora continua ayuda a que su programa TPM se adapte a los entornos cambiantes y evita que el programa se vuelva obsoleto y los empleados se desinteresen.
Mantenimiento productivo total: un estudio de caso
En el pasado, las industrias estadounidenses han sido reacias a implementar el mantenimiento productivo total en sus procesos actuales. De hecho, una encuesta realizada por el Centro de Investigación de Manufactura mostró que solo el 27 por ciento de los encuestados dijo que TPM era una iniciativa comercial actual, pero solo el 6 por ciento dijo que la estaban implementando por completo. Además, solo el 5 por ciento de los encuestados dijo que TPM era el enfoque de su planta para el mantenimiento y la confiabilidad.
A pesar de esta falta de interés, las plantas de todo el mundo están obteniendo beneficios significativos al hacer que el mantenimiento productivo total sea el foco de sus esfuerzos de mantenimiento. Un estudio publicado en el International Journal of Innovative Science, Engineering & Technology descubrió que, en una empresa de polímeros a pequeña escala, el valor de OEE antes de la implementación de TPM era del 75 por ciento. Después de que se implementó un programa TPM, OEE mejoró al 85 por ciento y se logró una mejor tasa de calidad. El estudio reveló además cómo la rentabilidad aumentó en un 12 por ciento, ya que los costos de desglose y mantenimiento cayeron bruscamente (80 y 20 por ciento) mientras que la e ciencia laboral aumentó. También se descubrieron muchos otros beneficios tangibles e intangibles como resultado de la implementación de un programa TPM.
Uno de los estudios de caso más discutidos para la implementación de TPM es el de la empresa cervecera latinoamericana Cervecería Cuauhtémoc Moctezuma, fabricantes de seis marcas de cerveza, incluidas Tecate, Dos Equis y Sol. Este artículo expone en detalle el éxito de TPM de la compañía, mostrando cómo se desarrolla el mantenimiento productivo total en un escenario del mundo real.
Noria Corporation. Traducido por Roberto Trujillo Corona, Noria Latín América.