Las transmisiones de engranes encerrados (reductores e incrementadores de velocidad) operan en tres regímenes de lubricación: película gruesa, película mixta y condiciones de película límite. El régimen ideal de lubricación para engranajes encerrados es el de película fluida, en donde la viscosidad del lubricante es suficiente para brindar la separación de las superficies en contacto de los engranes y rodamientos. Esta película fluida se forma bajo condiciones de cargas ligeras. Conforme incrementan la presión y las cargas, se presentan condiciones de película mixta, en donde la carga se soporta parcialmente por la película lubricante y en parte por las superficies en contacto de los engranes y los rodamientos. Bajo condiciones de película mixta, la película lubricante se presuriza, pero es demasiado delgada para evitar el contacto de las asperezas más elevadas de las superficies opuestas. Cuando la carga sigue aumentando, esta delgada película se rompe y se presenta la lubricación a película límite- Aquí es donde ocurre contacto metal-metal.
Protección al desgaste de los engranes
En muchas aplicaciones industriales, los engranajes encerrados están sujetos a altas cargas, debido a su diseño o a que se utilizan en aplicaciones para las que no están destinados. Estas condiciones pueden someter a las transmisiones de engranes a operar con una elevada densidad de potencia, que es el resultado directo del aumento en la aplicación de potencia (HP) y torque a los engranajes. Estas condiciones pueden incrementar el esfuerzo en los engranes y rodamientos, lo que puede llevar a un desgaste acelerado. Por lo tanto, es importante que los lubricantes para engranajes tengan la capacidad para proteger contra el desgaste anormal, rayado, picado (pitting) y abrasión, especialmente cuando se encuentran condiciones de alta carga. Esta protección contra el desgaste se logra empleando en su formulación sistemas de aditivos antidesgaste o extrema presión y, en algunos casos, añadiendo lubricantes sólidos como el bisulfuro de molibdeno, grafito, boratos y compuestos orgánicos de molibdeno solubles en aceite.
Los aditivos de extrema presión y antidesgaste evitan el contacto metal-metal mediante la adición de compuestos que forman película una película que protege la superficie, ya sea por absorción física o por reacción química con la superficie del metal, a n de formar una película de bajo esfuerzo cortante en el punto de contacto.
Existen varios ensayos que permiten medir las propiedades antidesgaste y extrema presión de los lubricantes para engranajes. Algunos de estos métodos son:
- Cuatro bolas EP ASTM D2783
- Cuatro bolas desgaste ASTM D4172
- Carga continua Falex ASTM D3233
- FZG ASTM D5182, DIN 51 354
- Timken EP ASTM D2783
El índice de desgaste por carga es indicador de la capacidad que tiene un lubricante para evitar el desgaste cuando se le aplican cargas, mientras que el punto de soldadura es la mínima carga aplicada para que cuatro bolas de acero se suelden entre sí.
Cuatro bolas EP ASTM D2783
En el ensayo ASTM D2783, se emplean cuatro bolas o esferas de acero de idéntico tamaño y metalurgia (Figura 1).
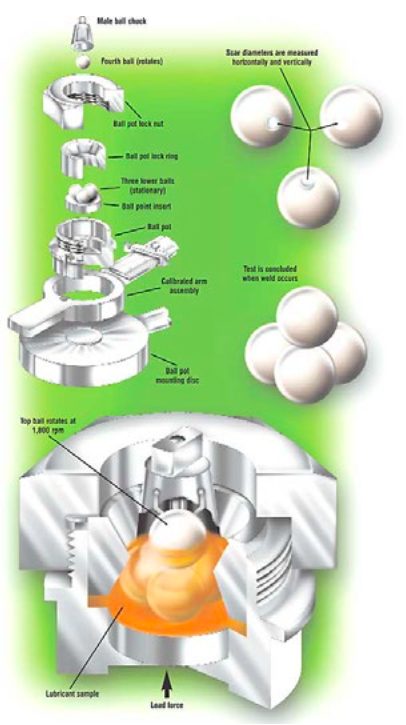
Figura 1. Ensayo de cuatro bolas
Tres bolas de acero, las cuales están inmersas en el aceite a analizar, se aseguran dentro de una copa del aparato de ensayo. La cuarta esfera se coloca en un maneral rotatorio encima de las otras tres esferas. Esta esfera gira a una velocidad de 1,779 rpm y se somete a series progresivas de incremento de carga, con una duración de 10 segundos cada una hasta que esta esfera se suelda a las otras tres.
Después de cada serie de 10 segundos se descarta la esfera en el maneral y se revisan las otras tres esferas extrayéndolas de la copa y se mide el diámetro de la cicatriz de desgaste en ellas. Este diámetro de cicatriz se emplea para calcular el índice de desgaste por carga. Se emplean nuevas esferas de acero con cada etapa de carga aplicada.
Las cargas se aplican en series consecutivas, siendo la primera carga de 6 kilogramos fuerza (kgf). Las series son de 6, 8, 10, 13, 16, 24, 32, 40, 50, 63, 80, 100, 126, 200, 250, 315, 400, 500, 620 y 800 kgf. Si no se presenta soldadura a 800 kgf, se reporta el lubricante con un punto de soldadura de +800 kgf.
Cuatro bolas desgaste ASTM D4172
El ensayo ASTM D4172 evalúa las propiedades de prevención al desgaste del lubricante en condiciones de deslizamiento acero sobre acero. No se pretende predecir las características de desgaste con otras combinaciones de metales diferentes a las de acero-acero y tampoco mide las características extrema presión del lubricante. Para este ensayo se utiliza el mismo aparato del ensayo de cuatro bolas EP y se prepara de la misma manera. Este ensayo se hace a 1,3200 rpm bajo una carga de 40 kgf a 75°C (167°F) por espacio de una hora. Después de este tiempo, se lavan las tres esferas estacionarias y se miden las cicatrices de cada una redondeando el valor a una décima de milímetro. Se hace otra medición en cada esfera a 90 grados de la primera. Se reporta el promedio de las seis mediciones, en milímetros.
Mientras menor sea el diámetro, el lubricante proporciona un mayor nivel de protección bajo condiciones de deslizamiento. Cuando se compara la capacidad de los lubricantes para engranes industriales, deben tomarse en cuenta los resultados obtenidos en ambos ensayos, cuatro bolas desgaste ASTM D6142 y cuatro bolas EP ASTM D2783. Algunos lubricantes para engranajes industriales tienen buenas propiedades extrema presión pero no son efectivos para reducir el desgaste a bajas cargas.1
Carga continua Falex ASTM D3233
Este ensayo se emplea para medir las propiedades de soporte de carga de lubricantes líquidos (Figura 2).
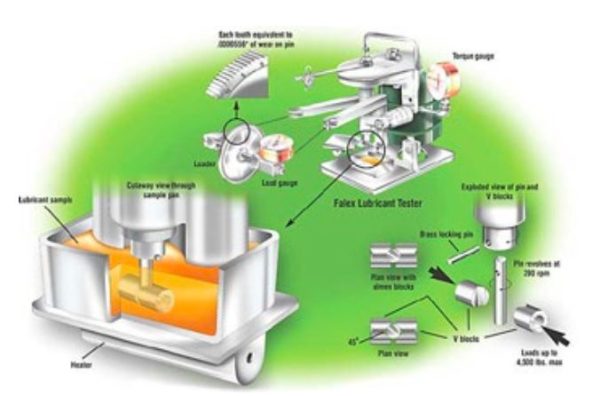
Figura 2. Ensayo de carga continua Falex
Se ha visto cierta correlación directa con las condiciones de servicio en campo, en donde se presentan condiciones de alta carga. El ensayo emplea dos procedimientos para evaluar las propiedades de soporte de carga del lubricante para engranajes industriales y su capacidad para proteger contra la abrasión. El procedimiento A se conoce como el método Falex de arranque, mientras que el procedimiento B se conoce como el método Falex de un solo paso.
Ambos procedimientos consisten en hacer girar un perno de acero a 290 rpm, impulsados por un motor de 1/3 HP contra los bloques estacionarios en forma de V que están sumergidos en 60 ml del lubricante que se está probando. La carga aplicada a los bloques en V contra el perno giratorio se hace mediante un mecanismo de trinquete. En el procedimiento A, se incrementan las cargas comenzando en 300 libras de fuerza (lbf) (1,334.4 newtons) en forma continua. En el procedimiento B, las caras se aplican comenzando en 250 lbf (1,112 newtons) manteniéndola en intervalos de un minuto en cargas incrementales. En ambos métodos de prueba, el ensayo termina cuando el lubricante no puede soportar la carga aplicada, resultando ya sea en la ruptura del perno o el aferramiento de los bloques en V. La máxima carga que puede aplicarse en este ensayo es de 4,500 lbf (20,016 newtons). Se considera que un lubricante brinda suficiente protección al desgaste bajo condiciones de alta carga si alcanza un valor de 1,500 lbf (6,672 newtons).
FZG ASTM D5182, DIN 51 354
El ensayo FZG ASTM D5182, DIN 51 354 se utiliza para evaluar las características antidesgaste, de transporte de carga y resistencia al rayado de un lubricante para engranajes industriales. El aparato de prueba FZG simula un conjunto de engranajes mal alineados que operan en un baño de lubricante, y consta de dos conjuntos de engranajes dispuestos en una configuración de cuatro esquinas, impulsado por un motor eléctrico con una potencia mínima de 7.4 HP a 1440 rpm. El conjunto de engranajes de prueba está inmerso en el lubricante de prueba, mientras se aplican etapas de carga progresivas (1 a 13) hasta que se presenta rayado o abrasión de los dientes del engranaje.
Cada etapa de carga tiene una duración de 15 minutos a una velocidad constante de 1,450 rpm y una temperatura de 90°C (194oF), comenzando en la cuarta etapa de carga. Las diferentes etapas de carga someten al lubricante a presiones de contacto que van de 21,178 psi (4,928 kg/m2) para la etapa 1 hasta 289,000 psi (141,101.4 kg/m2) para la etapa 13. Se examinan los engranajes antes y después de cada etapa de carga para ver la abrasión o rayado en los dientes. La etapa en la cual se observen daños en más del 20 por ciento de la cara del piñón que está recibiendo la carga por rayado y/o desgaste abrasivo se considera que es la carga de falla. Cuanto mayor sea la etapa de carga, mejor resistencia a la abrasión tiene el lubricante.
Timken EP Test ASTM D2783
El ensayo Timken EP ASTM D2783 es un método rápido para medir la resistencia a la abrasión y la capacidad de soporte de carga de aceites para engranajes industriales. Este método se utiliza ampliamente para fines de especificación y para diferenciar lubricantes que tienen características de bajo, medio y alto nivel de extrema presión. Los resultados obtenidos por este método no se correlacionan directamente con los resultados obtenidos durante el servicio en campo.
Durante el ensayo, se coloca un galón del lubricante a probar en el depósito del mecanismo de ensayo. El aparato funciona con un rodamiento Timken de cono y taza (rodillos cónicos) que, rota contra un bloque estacionario de acero endurecido, a una velocidad de 405.88 ± 2.54 pies/min., que equivale a una velocidad de 800 rpm. La muestra de lubricante se calienta a una temperatura de 30 °C (100 °F), y se aplica por gravedad a la taza y el bloque del aparato desde un depósito con capacidad de un galón; el aceite se retorna al depósito por medio de una bomba. Se efectúan dos determinaciones: la carga mínima (valor de rayado) que romperá la película de lubricante entre la taza giratoria y el bloque jo y causará abrasión, y la carga máxima (carga OK) a la cual la taza giratoria no romperá la película lubricante y causará abrasión entre ella y el bloque jo. Se aplican pesos fijos que actúan a través de un brazo de palanca con una relación 10 a 1 por medio de un dispositivo de carga automática con el n de forzar el bloque en contacto contra la taza giratoria. Cada carga se aplica durante 10 minutos. Al final de cada corrida de 10 minutos se examina el bloque de prueba jo para revisar las marcas de desgaste. Se determina que hay rayado cuando los bordes de la huella de desgaste se vuelven desiguales. La carga OK es la última carga antes de que se perciba el rayado.2
Se considera que un lubricante extrema presión para engranajes tiene buenas propiedades extrema presión si tienen una carga Timken OK de al menos 60 libras.
Noria Corporation. Traducido por Roberto Trujillo Corona, Noria Latín América.