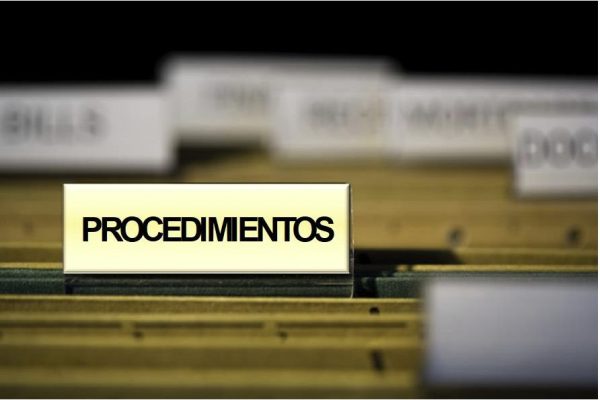
Imagine una operación en la que no hay accidentes con tiempo perdido, la efectividad global del equipo (OEE, por sus siglas en inglés) está aumentando y hay un plan para abordar la falta de habilidades. Estos sitios existen, y es probable que estén utilizando un mantenimiento basado en procedimientos.
Este tipo de mantenimiento simplemente implica tener todas las actividades de mantenimiento documentadas en procedimientos, que se siguen paso a paso cuando se efectúan tareas de mantenimiento correctivo, preventivo y predictivo.
Para lograr este nivel de excelencia operacional se requiere disciplina, pero no solo la disciplina que trata de que las personas hagan lo que deberían estar haciendo (o que no hagan lo que no deberían hacer), sino también la disciplina en el proceso y la eliminación de las variaciones.
Ese es el objetivo del mantenimiento basado en procedimientos: eliminar la variación en todos los aspectos del mantenimiento, incluyendo la recopilación de datos, reparaciones, calibración y puesta en servicio. Otro objetivo del mantenimiento basado en procedimientos es eliminar y reducir las probabilidades de errores por parte del personal de mantenimiento.
Al garantizar que todas las actividades se realicen de la misma manera, las organizaciones pueden lograr tres entregables clave: construir una biblioteca de conocimiento para sobrellevar la la carencia de habilidades, identificar áreas clave de variabilidad y reducirla para lograr resultados consistentes de las actividades y minimizar las probabilidades de cometer errores durante las actividades de mantenimiento.
El uso de los procedimientos debe pensarse con suficiente antelación. Si no lo hace, la adopción de los procedimientos fracasará.
Los procedimientos deben organizarse para que puedan ubicarse rápidamente. Deben estar escritos de manera que no haya una interpretación errónea del significado de la tarea y que se puedan entender en el idioma local o incluso por quienes no hablan el idioma como lengua original. Por último, deben ser utilizados por el personal de apoyo, capturando los comentarios y utilizándolos para implementar mejoras.
Historia de los procedimientos en el mantenimiento
El uso de procedimientos se remonta a muchas décadas atrás, y los resultados hablan por sí mismos. Considere el submarino USS Thresher, que se perdió junto con 129 vidas el 10 de abril de 1963. Una investigación sobre la pérdida del submarino concluyó que fue a causa de una inundación, probablemente causada por la falla de un componente del sistema de agua de mar que pudo haber sido instalado incorrectamente durante una revisión en el astillero. Hubo otros factores, pero el hallazgo principal fue que el componente se instaló de forma incorrecta.
El resultado de la investigación llevó a la Marina de los EE. UU. A implementar un nuevo programa para abordar la seguridad de los submarinos. Este programa se conoció como “SubSafe”. El programa SubSafe requería procedimientos detallados por escrito y el desarrollo de listas de verificación que debían seguirse al pie de la letra por todo el personal dedicado al mantenimiento de componentes específicos de todos los sistemas que afectan la seguridad de los submarinos.
Hasta la fecha, la marina no ha perdido ni un submarino debido a un error de mantenimiento bajo el programa SubSafe. Esto muestra el impacto que un sólido programa de mantenimiento basado en procedimientos puede tener en la confiabilidad y seguridad.
Más tarde, en la década de 1960, se buscó mejorar la confiabilidad de los aviones comerciales. Este estudio, que fue publicado por Nowlan & Heap, reveló que la mayoría de las fallas no habían sido inducidas por el tiempo o por desgaste, sino que fueron aleatorias o desencadenadas por un mantenimiento o instalación inadecuados. Al observar los seis patrones de falla, se observó que el patrón de falla seis, que experimenta un alto nivel de mortalidad infantil seguido de una tasa de falla aleatoria y consistente, fue más frecuente en 68 por ciento.
Esto indica que la mayor probabilidad de falla es cuando el equipo es nuevo o ha sido reparado. Entonces, ¿qué condujo a ese aumento en la probabilidad de falla? Las causas podrían estar relacionadas con el diseño, defectos de fabricación, defectos de instalación, puesta en marcha inadecuada, mantenimiento de rutina inadecuado y mano de obra de mantenimiento.
Teniendo en cuenta las causas de la alta probabilidad de falla para equipos nuevos o recientemente revisados, se determinó que la respuesta no era hacer más mantenimiento. La solución estaba relacionada con el control de la variabilidad en las actividades. Entre estas actividades se incluyen cosas como revisión del diseño, programas de calidad y certificación de proveedores, y el desarrollo de procedimientos para operar y mantener los equipos.
Hubo un esfuerzo consciente para dejar de depender solo de la capacitación en el trabajo, la intuición, etc., y moverse hacia el uso de procedimientos técnicos detallados. Como resultado de estos cambios, junto con el cambio al mantenimiento basado en condición en lugar del mantenimiento basado en tiempo (preventivo), las tasas de incidentes de aeronaves en todo el mundo han caído de casi 40 incidentes por 1 millón de despegues a principios de la década de 1960 a solo uno o dos incidentes por 1 millón de despegues en 2016.
Importancia de los procedimientos
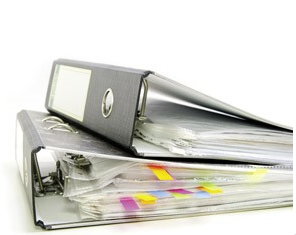
El mantenimiento basado en procedimientos sirve para abordar dos problemas clave al realizar actividades de mantenimiento. Primero, reduce la variación que ocurre cuando diferentes mecánicos realizan el mismo trabajo. Considere cuántas formas hay de reparar una bomba.
¿Cómo se efectúa el desmontaje? ¿El desmontaje se hace con un soplete y un martillo, o se realiza con las herramientas adecuadas? ¿La reparación se hace en una habitación limpia o en un taller sucio que puede contribuir a que se contamine? ¿Se inspeccionan las piezas según un estándar o se deja a la experiencia del mecánico?
¿Existe una lista estándar de piezas que se deben sustituir o se genera según los resultados de la inspección? ¿Se utiliza un componente de bloqueo de rosca durante el reensamble? ¿Se verifican las tolerancias en base a la experiencia o con apoyo de las especificaciones técnicas? ¿Se aprietan los sujetadores con un medidor de torque o solo por la fuerza del mecánico? ¿Cómo se prueba la bomba antes de volver a ponerla en servicio o almacenarla?
Si le hiciera estas preguntas a un grupo de mecánicos, probablemente obtendría una amplia gama de respuestas, y dos personas no tendrían el mismo proceso para reparar y poner en servicio una bomba. Esta variación hace que sea prácticamente imposible establecer una causa raíz de una falla prematura o un bajo desempeño de una bomba reparada. Un procedimiento basado en la experiencia del personal puede capturar el conocimiento colectivo y ponerlo en un método repetible y consistente, eliminando esta variación.
En segundo lugar, el mantenimiento basado en procedimientos minimiza las probabilidades de que un individuo cometa un error. Existen varios factores que pueden contribuir a un error, y es importante comprender estos factores para garantizar que los procedimientos sean escritos para abordarlos.
Por ejemplo, los factores antropométricos son aquellos relacionados con el tamaño o la fuerza de la persona que realiza la actividad. Estos factores se abordan principalmente a través de un rediseño o con herramientas, pero no con procedimientos.
Los factores sensoriales humanos son aquellos relacionados con la facilidad con la que las personas pueden ver, oír, sentir e incluso oler lo que sucede a su alrededor. Estos también se abordan principalmente mediante el rediseño o con herramientas y no a través de procedimientos.
Los factores fisiológicos se refieren a las tensiones ambientales, como las temperaturas altas o bajas, el exceso de ruido, la humedad, etc. Una vez más, estos no pueden abordarse mediante procedimientos.
Los factores psicológicos están relacionados con las causas por las cuales se cometen errores. Los errores psicológicos se dividen en dos tipos: errores involuntarios, que ocurren cuando alguien realiza una tarea incorrectamente, y errores intencionados, que ocurren cuando alguien se propone hacer algo deliberadamente, pero lo que hacen es inapropiado.
El error en cuestión puede ser un error o una violación. Un error es una aplicación incorrecta de una buena regla, la aplicación correcta de una mala regla o una respuesta inapropiada a una situación anormal. Una violación es cuando alguien comete un error a sabiendas y deliberadamente. Los procedimientos ayudan a abordar los errores no intencionados, pero no las violaciones.
Teniendo en cuenta las diferentes formas en que se realizan las actividades, los tipos de errores cometidos y empleando un ciclo de retroalimentación, el mantenimiento basado en procedimientos toma el conocimiento de todos los mecánicos y lo incorpora al procedimiento. El resultado es la forma más segura, eficiente y confiable de completar la tarea.
Cómo los procedimientos impactan la confiabilidad
Una vez que se implementa el mantenimiento basado en procedimientos, la operación verá mejoras notables en cinco áreas clave: seguridad, confiabilidad, fallas en el arranque, tiempo promedio de reparación y gestión del conocimiento.
La seguridad mejorará a medida que las tareas estén bien planificadas y se hayan identificado todos los riesgos. Esto permite el desarrollo de actividades de reducción efectiva de riesgos. Además, los procedimientos se pueden utilizar en caso de una falla, lo que puede reducir los riesgos asociados con el trabajo no planificado.
La confiabilidad aumentará a medida que las tareas se completen de manera consistente con las especificaciones técnicas adecuadas. Esto reduce las fallas prematuras. En caso de que ocurra una falla, se puede analizar para determinar la causa raíz, ya que los procedimientos y actividades están definidos y son consistentes.
Las fallas en el arranque disminuirán, ya que los procedimientos asegurarán que todos los ajustes se hagan correctamente, se inspeccione el área, se eliminen todos los objetos extraños y se realicen las actividades adecuadas de puesta en marcha.
El tiempo medio para reparar se reducirá, ya que hay un procedimiento que ayuda a disminuir el tiempo de reparación y toda la información requerida está disponible.
La gestión del conocimiento es otro beneficio del mantenimiento basado en procedimientos. Con este enfoque, la experiencia y el conocimiento de los mecánicos veteranos pueden capturarse en los procedimientos y transferirse a los mecánicos junior.
Primeros pasos en el mantenimiento basado en procedimientos
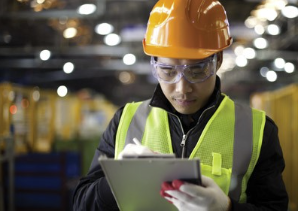
El mantenimiento basado en procedimientos es utilizado por muchas industrias que exigen una elevada disponibilidad, como es la industria de la energía nuclear, aviación y marina, por nombrar algunas. Pero solo porque estas industrias lo usen no significa que usted no pueda. Esto es lo que necesita para comenzar con el mantenimiento basado en procedimientos:
Comience documentando los pasos para ejecutar las tareas de mantenimiento preventivo (PM). Repase cada tarea y documente cada paso del procedimiento, incluyendo las especificaciones técnicas específicas. Una vez que se haya desarrollado el procedimiento, revíselo y asegúrese de que represente la mejor práctica para efectuar la tarea. Esto puede requerir muchas revisiones. El procedimiento puede ser desarrollado por un mecánico senior, un planificador, o contratando temporalmente a algún trabajador u operario jubilado recientemente para que ayude a proporcionar información.
Cree una lista de verificación que se pueda usar al completar el procedimiento. Las listas de verificación se emplean en todas las principales industrias como una forma de asegurarse de que no se olvide nada. Puede haber alguna resistencia a utilizar listas de verificación, ya que los mecánicos pueden decir que son suficientemente hábiles y no las necesitan. Sin embargo, los médicos y los pilotos las usan para asegurarse de que no se olvide nada, entonces, ¿por qué no deberían usarlas los mecánicos?
Defina un programa de capacitación y certificación para los nuevos procedimientos, pues requerirá que los mecánicos reciban capacitación sobre la tarea y el mantenimiento basado en procedimientos antes de que se les permita realizar actividades críticas. Esta capacitación debe ser realizada por las personas responsables del desarrollo del procedimiento.
Una vez que los mecánicos hayan recibido capacitación, refuerce el uso de los procedimientos. Realice auditorias para verificar que se sigan y que solo personal capacitado los esté utilizando. Trate de recompensar a quienes adoptan el mantenimiento basado en procedimientos. Además, utilice los comentarios proporcionados sobre los procedimientos. Esto no significa tomar todos los comentarios como verdad absoluta. En su lugar, significa revisar, evaluar y usar los comentarios o dar explicaciones de por qué no se usarán. Este enfoque ayudará a garantizar que se proporcione retroalimentación.
A medida que más tareas de mantenimiento se convierten en procedimientos, desarrolle y use una sola plantilla. Esto fomentará la coherencia en toda la organización, haciendo que el mantenimiento basado en procedimientos sea más fácil de implementar y mantener.
Una precaución cuando se utiliza a los mecánicos para escribir procedimientos es capacitarlos primero en el proceso. Los procedimientos deben ser específicos y ejecutables sin ninguna información innecesaria. Otro enfoque es que un mecánico escriba el procedimiento y luego lo edite un escritor técnico. Ambos enfoques tienen sus pros y sus contras, así que asegúrese de elegir el adecuado para su organización.
Escriba procedimientos utilizables
Escribir procedimientos no es una tarea fácil. Muchas personas tienen opiniones diferentes sobre la secuencia, las especificaciones, etc. Una vez que esto se resuelve, el procedimiento debe escribirse de manera tal que pueda ser seguido por todos los mecánicos, incluidos por quienes no hablan el idioma como su lengua original. Podemos seguir aprendiendo de la industria de la aviación. Esta industria ha desarrollado un lenguaje técnico simplificado.
El inglés técnico simplificado es una versión controlada del inglés que está diseñada para ayudar a los usuarios de habla inglesa a comprender la documentación de mantenimiento. La escritura técnica puede ser compleja y difícil de entender, incluso para hablantes nativos del inglés. El inglés técnico simplificado hace que los procedimientos sean fáciles de entender y seguir, eliminando problemas de idioma y reduciendo las fallas prematuras e inducidas por el mantenimiento.
El inglés técnico simplificado proporciona un conjunto de reglas de escritura y un diccionario de vocabulario controlado. Las reglas cubren la gramática y el estilo. El diccionario especifica las palabras que se pueden usar y las que no. En lo que respecta a las palabras seleccionadas, solo hay una palabra para un significado y una sola forma de pronunciar una palabra.
Algunos de los beneficios del lenguaje técnico simplificado incluyen reducir la ambigüedad, mejorar la claridad de la escritura técnica, mejorar la comprensión para las personas cuando el idioma empleado no corresponde con su idioma materno y aumentar la confiabilidad de la maquinaria al disminuir la probabilidad de que se introduzcan defectos durante el mantenimiento y el ensamblaje.
La especificación simplificada del lenguaje técnico no es fácil de aprender, pero hay capacitación y software disponibles. Incluso sin convertirse en un experto, puede hacer que sus procedimientos sean más legibles y aumentar la confiabilidad. Comience con algunas pautas básicas de escritura y revisando los procedimientos antes de emitirlos.
Algunas de las mejores prácticas para escribir procedimientos son:
- Use oraciones cortas. El límite máximo recomendado es de 20 palabras en una oración de procedimiento y 25 palabras en una oración descriptiva.
- Restrinja los grupos de sustantivos a menos de tres.
- Restrinja los párrafos a menos de seis oraciones.
- Evite la jerga o estilo callejero.
- Evite la voz pasiva.
- Sea lo más específico posible.
- Utilice artículos como “un/una” y “el” siempre que sea posible.
- Use tiempos verbales simples (pasado, presente y futuro).
- Escriba pasos secuenciales como oraciones separadas.
- Ponga en primer lugar las advertencias y precauciones, con la excepción de ciertas condiciones.
- Use la palabra “que” después de las cláusulas subordinadas que usan verbos como “asegurarse” y “mostrar”.
- Introduzca los elementos de una lista con un guión.
- Use gráficos donde sea necesario para aclarar el significado. Una imagen vale mas que mil palabras.
- Use la palabra “advertencia” para proteger contra daños al personal, pero la palabra “precaución” para proteger contra daños a la maquinaria o equipo.
Una vez escrito el procedimiento, revise y elimine cualquier información que no sea relevante (es decir, en lugar de aceite lubricante sintético, use solo aceite). Los procedimientos bien escritos deberían ayudar a eliminar cualquier interpretación errónea y dar claridad al mecánico u operario que realiza la actividad. Aquí hay un ejemplo de cómo la redacción de un paso de procedimiento podría estar abierta a interpretación. La tarea “reemplazar el filtro” podría significar volver a colocar el filtro que sacó o instalar un filtro nuevo. Aquí puede ver cómo una persona podría realizar una tarea y cómo otra la realizaría de manera diferente.
Una vez que la tarea está clara, se debe agregar una especificación técnica para que la tarea se pueda realizar de forma estándar, como “Apriete a 15 libras-pie”. Una vez aclarada la tarea y agregando una especificación técnica, el resultado sería: “Instale un filtro nuevo y apriete a 15 libras-pie”. Esta tarea es simple, clara, fácil de entender y se puede realizar de manera consistente y repetible.
Si una organización decide no seguir un lenguaje técnico simplificado, al menos debe haber un estándar para la escritura de los procedimientos, de modo que todos lo hagan de la misma manera. Aunque puede parecer una locura tener un procedimiento para escribir un procedimiento, es vital para la coherencia y la repetibilidad.
Ponga los procedimientos a disposición del personal
Una de las partes más difíciles de implementar el mantenimiento basado en procedimientos es el cambio que trae a una organización. De hecho, habrá un cambio en la forma en que se realiza el mantenimiento para todos los niveles del departamento de mantenimiento. Por ejemplo, los mecánicos deben seguir procedimientos y especificaciones y confiar menos en la experiencia personal y la intuición.
Los supervisores de mantenimiento ahora se centran en garantizar que los procedimientos se usen y actualicen. Los planificadores se muestran más decididos a actualizar los procedimientos para que estén disponibles para su uso.
Ayudar a una organización a través de este cambio no es fácil. Se requerirá un enfoque bien pensado. Personalmente, me gusta utilizar la infraestructura de conciencia, deseo, conocimiento, habilidad y reforzamiento (ADKAR, por sus siglas en inglés). Este método permite a las organizaciones planificar y gestionar el cambio que se está implementando, así como atraer a las personas hacia el cambio.
Cada paso en esta infraestructura proporciona acciones específicas que deben tomarse, como la conciencia de la necesidad de cambio, el deseo de participar y apoyar el cambio, el conocimiento para saber cómo cambiar, la capacidad de implementar las habilidades y comportamientos necesarios y el refuerzo para sostener el cambio.
El propósito de usar una infraestructura como ADKAR es identificar cualquier preocupación asociada con el cambio, abordar esas preocupaciones, expresar cómo el cambio beneficiará al personal, proporcionar el conocimiento y la capacitación y, finalmente, demostrar que el cambio no es una moda pasajera. Cuanto más tiempo se dedique a planificar y gestionar el cambio, más probable será que el cambio se adopte y se mantenga.
El mantenimiento basado en procedimientos tiene la oportunidad de impulsar mejoras significativas en seguridad, confiabilidad y operaciones. Pero antes de que una organización pueda saltar al mantenimiento basado en procedimientos, debe haber un plan sobre cómo se implementará, quién redactará los procedimientos, con qué estándar se escribirán los procedimientos y cómo se capacitará al personal sobre los nuevos procedimientos.
Con la adopción del mantenimiento basado en procedimientos por la Marina, la aviación y la industria nuclear, los resultados están comprobados. Si este tipo de organizaciones está utilizando el mantenimiento basado en procedimientos, ¿qué impide que su organización lo use?
Noria Corporation. Traducido por Roberto Trujillo Corona, Noria Latín América.