Para que sea efectivo, un programa de mantenimiento de lubricación debe reducir los paros no programados lo más posible en forma costo-eficiente. Otros objetivos son:
- Maximizar el tiempo disponible de los equipos
- Reducir errores
- Utilizar nueva tecnología en donde sea aplicable
- Utilizar herramientas de monitoreo de condición
- Emplear productos que ahorren energía en donde se justifique
- Reducir los materiales peligrosos y el desperdicio
- Utilizar productos “verdes” amigables con el medio ambiente en sonde sea posible
- Impulsar el aprendizaje y mejorar el ambiente de trabajo
Antecedentes
En las estaciones de generación de energía y en otras instalaciones industriales, lograr las metas de producción de una manera costo-eficiente requiere que el equipo involucrado en la generación y entrega se desempeñe efectiva y confiablemente.
El equipo de operación se desgaste, ya sea como resultado de la operación o por el desgaste inherente del equipo. Se daña. Como resultado, la reducción del desgaste y el daño consecuente es un aspecto crítico para alcanzar los objetivos de costo de producción.
Afortunadamente, las partes raramente fallan sin dar señales de alerta, y el mantenimiento predictivo puede ayudar a maximizar el tiempo disponible de la máquina, por lo general con muy poco gasto o incluso sin gastar. Incrementar el tiempo de máquina disponible a menudo puede lograrse haciendo mejor uso de los recursos disponibles.
Alcanzar este objetivo no es sólo cuestión de tecnología. Un aspecto esencial es el entrenamiento apropiado para que se comprenda mejor cómo se debe efectuar una tarea correctamente y cómo hacerla bien. También se trata de hacer más fáciles las tareas, para asegurar que se lleven a cabo y se logre el máximo desempeño.
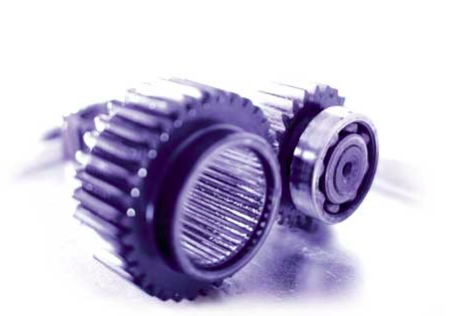
Aplicación del Lubricante
El equipo rotatorio contiene rodamientos que requieren lubricación. Proveer el lubricante correcto, en el momento correcto y en el sitio correcto puede ser una de las formas más costo-eficiente de maximizar la disponibilidad de la máquina. Si esto se hace correctamente es tan fácil como hacerlo mal. Desafortunadamente, más no siempre es mejor y en muchas aplicaciones aplicar lubricante en exceso, aun cuando se aplique el lubricante correcto, puede provocar fallas.
Afortunadamente, generalmente es simple hacer esto pero requiere que estén en su sitio cierto número de elementos. Por ejemplo, el equipo debe ser mantenible, deben emplearse los lubricantes apropiados, deben aplicarse en forma correcta, y debe tenerse un efectivo monitoreo de condición.
Desafortunadamente, también es fácil hacer mal las cosas y hacer sustituciones inapropiadas, aun cuando se haga con buenas intenciones. Este tipo de sustituciones puede provocar problemas inmediatos de compatibilidad o daños a los rodamientos pero en el lago plazo pueden causar fallas de corrosión por estrés, enfermedad al operario y posibles daños al medio ambiente. Los aditivos suplementarios “El mecánico en una botella” requieren ser revisados cuidadosamente por cualquier impacto que puedan ocasionar en el reciclado de aceite de desecho y/o requerimientos de disposición.
El Problema
Se ha documentado que, en Canadá, las pérdidas tribológicas exceden $10 billones al año y 25 por ciento de esas pérdidas podría haberse ahorrado simplemente aplicando la tecnología conocida hasta hoy. Las pérdidas en los Estados Unidos se estima que son 10 veces más elevadas tomando como base las diferencias de población.
Tan solo nueve por ciento de los rodamientos operan el tiempo suficiente para alcanzar su vida de diseño. La principal causa de falla, con un 43 por ciento, es la lubricación inapropiada, seguida por mal montaje con un 27 por ciento. Ambas son prevenibles.
La contaminación causa entre un 70 a un 85 por ciento de las fallas de los sistemas hidráulicos.
El Instituto de Investigación de Energía Eléctrica (EPRI, por sus siglas en inglés) encontró que la principal causa de falla de un motor está relacionada con falla del rodamiento, con un 41 por ciento. También hallaron que las bombas de alimentación de calderas estaban ligeramente mejor, con 49 por ciento de fallas relacionadas con problemas tribológicos.
Las Causas
Los costos de las deficiencias tribológicas pasan en gran parte inadvertidos, y se atribuye a la falta de conciencia acerca del costo real y las soluciones. Algunos factores que contribuyen a esto son las muy diversas unidades de trabajo típicamente involucradas con lo que podrían ser barreras sistémicas a la mejora.
Las barreras comúnmente son causadas por objetivos y/o metas financieras en conflicto. Estas están compuestas por falta de motivación al cambio y/o reingeniería. Más allá, la causa raíz de un problema a menudo pasa desapercibida porque los rodamientos son capaces de operar por años con una inadecuada lubricación. La máquina probablemente experimentará una falla temprana debido al daño; una vez que este ocurre, no es reversible. Otras penalizaciones económicas asociadas incluyen mayores pérdidas de fricción y desperdicio.
Esto puede complicarse por el hecho de que si sólo consideramos los costos de capital pertenecientes a los lubricantes por sí solos, estos son insignificantes. Por esta razón, algunas veces se les da una baja prioridad equivocadamente. Por ejemplo, una estación de generación de energía de gran tamaño podría tener un centenar de diferentes códigos de lubricantes en existencia en una variedad de empaques y tamaños, pero el costo anual podría ser de apenas unas decenas de miles de dólares.
Desafortunadamente, los costos de mantenimiento para aplicar tales lubricantes están por lo menos en el orden de una magnitud mucho mayor, y las implicaciones de una falla los son aún más. Por ejemplo, prevenir una falla de desajuste en la tasa de flujo, exceso de velocidad, falta de abasto o alguna otra falla insignificante debería ser suficiente para justificar una revisión. Usar el lubricante equivocado como un lubricante para cuerdas de tubería que podría causar ruptura por corrosión tiene múltiples implicaciones. Los sistemas actualmente implementados raramente son adecuados para prevenir tales problemas.
En la mayoría de los casos, el costo de una falla de rodamiento, descompostura de una válvula, costos de la mano de obra de lubricación o pérdidas de producción exceden el costo del lubricante. Consecuentemente, el objetivo debería estar en maximizar la disponibilidad del equipo de forma que el costo inicial de un lubricante sea sólo uno de los factores a considerar.
Retomando el Control
Retomar el control requiere una evaluación completa del ciclo de lubricación, desde el almacenamiento hasta la disposición. Los cuartos o salas de lubricación. La distribución del lubricante, provisiones de grasa, relleno de fluidos, mantenimiento del lubricante, filtración, monitoreo de condición del lubricante, entrenamiento a los lubricadores y disposición del lubricante usado son algunos de los factores a considerar.
La evaluación cubrirá el equipo para lubricación del reactor, la turbina de vapor y equipos auxiliares, y el balance de todos los equipos de la planta, incluyendo el equipo de repuesto y la planta generadora de emergencia. Los lubricantes incluidos serán los aceites minerales, lubricantes sintéticos y grasas, así como los compuestos anti-aferramiento y los fluidos de éster fosfatado resistentes al fuego que se utilizan en los sistemas de control de la turbina.
Los aspectos relacionados con las compras, tales como entrenamiento, especificaciones,, aprobación de proveedores, criterios de selección, pruebas independientes, QA, ISO 14000 y aspectos “verdes”, seguridad de los trabajadores y reutilización y/o reciclado de lubricantes también pueden incluirse.
Al final, los lubricantes y fluidos para equipo eléctrico tales como transformadores, mandos eléctricos e interruptores también serán cubiertos.
Metodología
A pesar de las diferencias de un sitio a otro, la metodología incluye típicamente la creación de un equipo de trabajo de cuatro a seis personas con asistencia proporcionada por un líder o uno de los participantes. Si está involucrado más de un sitio, se requiere un contacto para cada planta; sin embargo, se sugiere que a menos que los temas sean genéricos, sólo uno de los sitios serán revisados a la vez.
Inicialmente, esto implicará compartir información, lo que puede lograrse sin llevar a cabo reuniones cara a cara. El siguiente paso será una visita de uno a dos días al sitio para intercambiar información, identificar temas prioritarios y acordar las líneas de tiempo. Esto debe hacerse en el plazo de unas pocas semanas o meses, no de años.
Seguirá una revisión de los equipos relacionados con lubricación y los componentes lubricados en el sitio. El entregable sería un reporte delineando cualquier aspecto específico de preocupación escrito en términos generales sugiriendo las mejoras y cómo debe implementarse el cambio. Es posible que algunas acciones se pongan en ejecución después de seis meses, mientras que otras tomarán más tiempo en implementarse y verificarse. Primero deben realizarse consideraciones drásticas o probarse productos significativamente diferentes en un número mínimo de máquinas, preferentemente en aquellas que tienen menor impacto en la producción. Se proporcionará asistencia continua durante la fase de implementación.
Otras Consideraciones
Es importante considerar quién o cuál grupo de trabajo paga el costo incremental para un producto más costo-efectivo. U control de costos obsesivo o inapropiado puede poner en riesgo la efectiva implementación de las prácticas de mantenimiento mejoradas. ¿Quién paga por el monitoreo de condición del equipo, o mejor alineación, o un mejor aceite sintético para engranes? Tome en consideración este ejemplo de qué no hacer en una aplicación de caja de engranajes de un pulverizador: Un aceite de engranes base Polialfaolefinas (PAO) tiene un probado beneficio basado en los ahorros de energía por el consumo de potencia del motor en 20 días. Esto no toma en cuenta los beneficios de una vida más larga, menos desgaste, seguridad mejorada, y posibles ahorros mayores por disminuir un grado de viscosidad. No se hizo debido a que el departamento de mantenimiento pagaría por el aceite más costoso; sin embargo operaciones tendría el beneficio. La administración debe involucrarse más. Una posibilidad es que un porcentaje de los costos de operación (u otra característica medible) se suprima de las mejoras que disminuyan los costos y los proyectos sean evaluados por algún criterio o fundamentado en las decisiones de un comité.
Como recordatorio, el foco debe estar en las mejoras reales cuantificables, no solamente en la consolidación o reducción de lubricantes. El énfasis debe estar en emplear el producto correcto, en la cantidad correcta y en el momento correcto. Hacer esto es una decisión y también tiene implicaciones de costo.
Una mejor solución con frecuencia es fácil de implementar y no requiere de nuevas investigaciones o correr riesgos. La clave es implementar un apropiado entrenamiento técnico, impulsar el conocimiento y mejorar el ambiente de trabajo.
Noria Corporation. Traducido por Roberto Trujillo Corona, Noria Latín América.