La mayoría de los fabricantes de maquinaria proporcionan guías en cuanto a cómo el aceite debe ser mantenido para una operación confiable. Debido a que los componentes tienen poca tolerancia a la contaminación o a la oxidación, se realiza un muestreo y monitoreo frecuente del aceite mientras el equipo está en operación para mantenerlo sin problemas en esas condiciones. Sin embargo, muchas veces se presta poca atención a la calidad del aceite cuando el equipo ha sido detenido por mantenimiento o se encuentra en espera (stand-by). Esta situación podría afectar la confiabilidad de la máquina.
Por ejemplo, cuando una turbina de vapor se detiene por un período prolongado de tiempo o un paro programado de tres semanas por mantenimiento, no se consideran las consecuencias de no tener el aceite caliente y circulando a través de todo el sistema. De hecho, la calidad del aceite cuando se llena una turbina durante el giro inicial o el arranque es a menudo muy diferente a cuando la unidad sale de operación después de está funcionando.
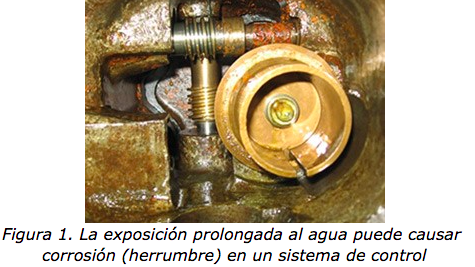
Los cojinetes de las turbinas están diseñados para una lubricación a película fluida (gruesa), la mayoría de las veces, hidrodinámica. Esto significa que se forma una cuña de aceite en un cojinete hidrodinámico, para separar y mantener una película lubricante entre el eje y el cojinete. El espesor de la película es una función de la velocidad del eje, de la carga y de la viscosidad del aceite. Bajo estas condiciones de película fluida (gruesa), un incremento en la viscosidad o la velocidad, incrementa el espesor de la película, mientras que un incremento en la carga o una disminución de la velocidad, disminuye el espesor de la película de aceite.
Para el desarrollo de una película lubricante, la geometría de la superficie del cojinete y del eje son tan importantes como la velocidad, la viscosidad y la carga. Para mantener una cuña de aceite y una película fluida entre las superficies, los perfiles del eje y del cojinete deben estar en forma perpendicular. Si alguna de las dos superficies se daña a causa de partículas que se han introducido dentro del cojinete, la efectividad para formar la cuña de aceite disminuye, dando como resultado una película de aceite más delgada. La disminución del espesor de la película de aceite incrementa la sensibilidad para tener daños adicionales o producir contacto metal-metal durante el paro o el arranque de la turbina.
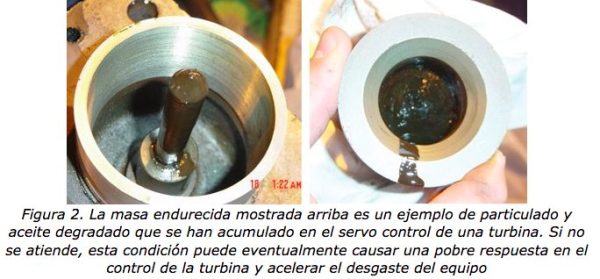
Cuando el rotor de una turbina opera en condiciones normales, en el cojinete se presentan condiciones de lubricación hidrodinámica. Sin embargo, cuando el rotor esta acoplado al engranaje de giro o comienza a girar a baja velocidad, el cojinete se encuentra en condiciones de lubricación límite. Esta condición se refleja en un contacto metálico y desgaste, generando un alto coeficiente de fricción. En este punto, el espesor de la película lubricante entre el eje de la turbina y el cojinete se encuentra en su valor más bajo. El espesor de la película se incrementará cuando se incremente la velocidad, se incremente la viscosidad, se disminuya la carga o cuando la geometría entre el eje y la superficie del cojinete se mejoren una con respecto a la otra. Si la superficie se vuelve más rugosa (hay daño en la superficie del cojinete), el riesgo de contacto entre el eje y el cojinete se incrementa. Esta relación entre la rugosidad de la superficie y el espesor de la película lubricante es importante en la consideración de la lubricación hidrodinámica de un cojinete de turbina.
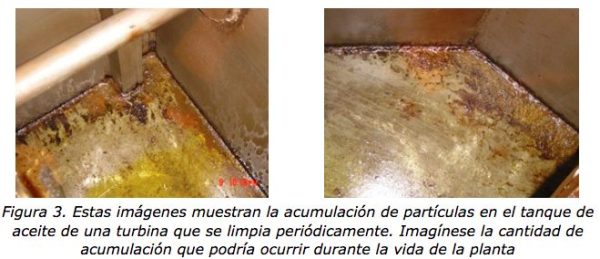
Una preocupación importante relacionada con las rugosidades, incluyendo las canaletas y surcos a lo largo del cojinete o de la superficie de babbitt, es que permiten que el aceite a alta presión fluya lejos de las áreas donde la película es más delgada. Esto permitiría un incremento en el contacto y en las fuerzas de corte sobre el babbitt que los que ocurrirían con ejes suaves, concéntricos y redondos sobre la superficie suave de un cojinete de babbitt. Esta es la razón del porqué superficies que aparentan tener un daño mínimo pueden aun causar fallas en los cojinetes durante el arranque u operación a baja velocidad antes de que se desarrolle un completa lubricación hidrodinámica con un espesor de película normal.
Durante el arranque de la planta, cuando la turbina está acoplada al engranaje de giro o a baja velocidad, el sistema de lubricación suministra aceite contaminado con partículas a los cojinetes principales y de empuje. Esto es especialmente perjudicial para los cojinetes principales porque ellos llevan la fuerza para hacer que los ejes entren en contacto con la superficie de los cojinetes, proporcionando una película lubricante muy delgada. Esta forma de lubricación es llamada lubricación límite. Debido a que existe una película de aceite muy delgada entre el eje y la superficie del cojinete, y muchas de las partículas tienen un tamaño mayor que dicho espesor de película, la superficie del cojinete se puede dañar en la medida en que las partículas quedan embebidas en la superficie del babbitt. En algunos casos, las partículas pueden dañar el eje, requiriendo su mecanizado y/o rectificado.
Contaminación con agua
La contaminación con agua en sistemas de lubricación o control es particularmente indeseable porque tiende a emulsionarse con el aceite. Un elevado contenido de agua en un sistema de lubricación puede también afectar la lubricidad y producir herrumbre. Cuando un sistema de lubricación o de control se detiene, las regiones normalmente húmedas, tales como las tuberías de drenaje de aceite, quedan expuestas al aire. La ampliación de la superficie de acero al carbono que queda expuesta a las condiciones ambientales incrementa la cantidad de corrosión interna (herrumbre) que se genera dentro del sistema.
Durante la operación de la unidad, la cantidad de agua en los sistemas de lubricación o de control se mantiene normalmente dentro de especificaciones del fabricante por el sistema de acondicionamiento del aceite. Estos sistemas a menudo contienen algún tipo de demulsificante para remover el agua. Aún si el contenido de agua está por encima del objetivo establecido, las superficies de acero están cubiertas de aceite, por lo que la corrosión (herrumbre) se encuentra controlada. Sin embargo, cuando la turbina se detiene por semanas o meses, el agua se separa del aceite en las tuberías y componentes donde normalmente se encuentra. Si esta separación ocurre, puede presentarse corrosión en el sistema, crecimiento bacteriano y/o afectar el funcionamiento del sistema de control. Además, cuando se drena el aceite, gran parte de las superficies del sistema normalmente llenas con aceite quedan expuestas al medio ambiente (aire y oxígeno). Por lo tanto, mientras mayor sea el tiempo en que el sistema de lubricación de la turbina permanezca detenido, mayor será el tiempo que la máquina tiene para oxidarse (corroerse/herrumbrarse).
Contaminación con partículas
La contaminación con partículas no sólo puede causar desgaste en la máquina, también puede obstruir los puertos de lubricación, los filtros en línea y los sistemas de control. Durante la operación, los parámetros utilizados para monitorear las tendencias del aceite permanecen estables, pero cuando el sistema, que está diseñado para lubricar y mantener limpias las tuberías y los sistemas, se detiene, la tasa de oxidación de las superficies expuestas se incrementa. Entonces, cuando la unidad es puesta nuevamente en funcionamiento, la nueva corrosión (herrumbre) producida dentro de la tubería o cualquier superficie, se desprende por agitación o es lavada cuando el aceite comienza nuevamente a fluir. Además, si existen lugares donde el aceite quede estancado, puede producirse fácilmente el asentamiento de partículas y depósitos. Cuando se restituye el flujo de aceite, estas partículas y depósitos son arrastradas por la corriente de aceite y circular por todo el sistema de lubricación.
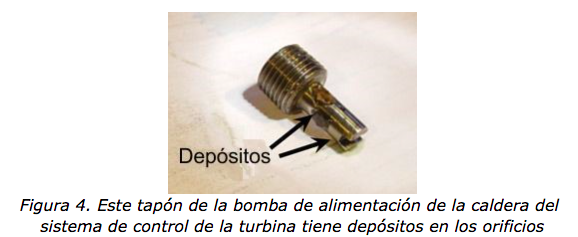
Un área de gran preocupación es el sistema de control. Dada la complejidad del sistema y el flujo a baja velocidad dentro de las tuberías de control, el sistema actúa como un punto de recolección de dichas partículas.
Crecimiento bacteriano
Cuando un sistema de lubricación está detenido por mucho tiempo, puede producirse un crecimiento de bacterias. Áreas de bajo flujo pueden acumular grandes cantidades de lodo a través de los años. Con esta cantidad de bacterias, un cambio repentino en la temperatura, como por ejemplo cuando el sistema entra nuevamente en operación, da como resultado la muerte de las bacterias y sus restos son esparcidos por todo el sistema.
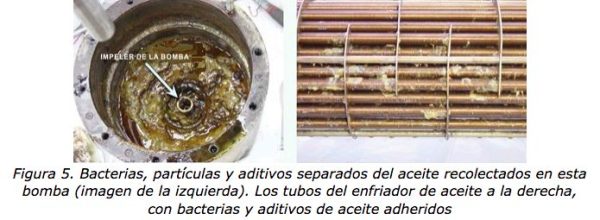
Códigos de limpieza
La mayoría de las plantas tienen un programa de monitoreo de la maquinaria donde se establecen los límites de las propiedades del lubricante. Estos límites son establecidos para las condiciones normales de funcionamiento. Uno de los parámetros más comúnmente monitoreado es el nivel de limpieza. La Organización Internacional de Estandarización (ISO) ha desarrollado el método ISO 4406 para cuantificar el contenido de partículas contaminantes. Los resultados obtenidos en una prueba de conteo de partículas identifican la cantidad de partículas en un volumen dado de aceite que se encuentran dentro de un rango para un tamaño específico de partícula, fijado en 4, 6 y 14 micrones. Los resultados normalmente se muestran en un formato como este 17/15/13, el cual proporciona un rango numérico representando el primer número (17) la cantidad de partículas medidas más grandes que 4 micrones, el segundo número (15) la cantidad de partículas medidas más grandes que 6 micrones; y el tercer número (13) la cantidad de partículas medidas más grandes que 14 micrones, respectivamente.
Casos de estudio
En un reciente paro de una turbina, el sistema de lubricación fue puesto en operación y la turbina fue acoplada al engranaje de giro. Mientras el sistema estuvo en operación, un sistema de filtración externo fue conectado al tanque principal de la turbina para funcionar en paralelo con el sistema de filtración normal. El filtro externo estaba equipado con un filtro dual de 7 micrones y procesaba cuatro veces el volumen de aceite de la turbina por hora. Se tomaron muestras de aceite, con intervalos de 20 minutos, del centro del tanque de la turbina y se documentaron los resultados del conteo de partículas por bloqueo de poro durante 31 horas.
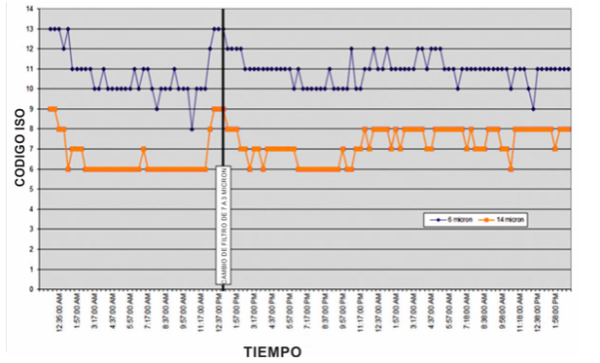
Figura 6. Los resultados del conteo de partículas por bloqueo de poro revelaron que una gran cantidad de partículas se introducen en el sistema de lubricación después de 12 horas de operación
Como lo indica la figura 6, después de aproximadamente 12 horas de operación, una gran cantidad de partículas debe haberse liberado dentro del sistema, forzando al cambio de filtros. En este punto, se tomó la decisión de disminuir el tamaño de poro del filtro. Una vez la turbina en operación, se desconectó el sistema de filtración externa. La inspección de la última serie de filtros reveló una cantidad significativa de partículas capturadas dentro del filtro.
En otro ejemplo, un equipo de filtración externa con contador de partículas fue conectado al tanque de una turbina durante el arranque de la planta de generación. Esta funciona normalmente durante las horas pico de los meses de verano en el sur de los estados Unidos, estando detenida al menos seis meses durante el año. El contador de partículas registró los niveles de contaminación sólida en el tanque principal de la turbina por encima de 4, 6 y 14 micrones. La figura 7 muestra los cambios en los niveles de partículas desde el momento en que la turbina está acoplada al engranaje de giro, hasta que se sincroniza con la red de energía eléctrica.
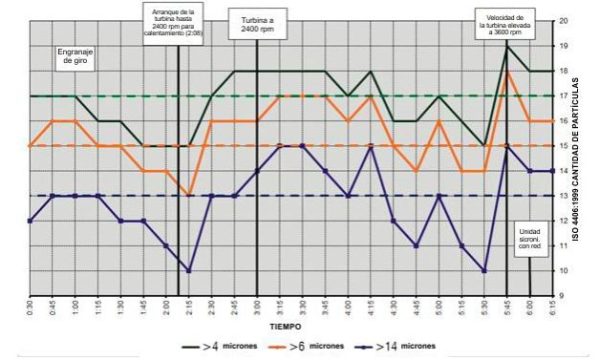
Figura 7. Este gráfico ilustra los cambios en el contenido de partículas del aceite durante el arranque de la turbina. Las líneas punteadas son las “alertas” del código ISO 4406 para cada tamaño específico de partícula
Note que cuando la turbina se desacopla del engranaje de giro y la velocidad se incrementa a 2,400 rpm para calentamiento, se liberó una gran cantidad de partículas en el sistema de lubricación. Esto hizo que los niveles de los tres tamaños de partículas se incrementaran por encima de los objetivos establecidos y se mantuvieron altos por más de dos horas, para luego disminuir. Colocando filtración externa se lograron disminuir los niveles de partículas a límites aceptables, sin embargo, cuando se incrementó la velocidad de la turbina para sincronizar el generador con la red eléctrica, de nuevo se incrementaron los valores.
Las plantas generalmente no monitorean los niveles de partículas cuando los equipos son colocados de nuevo en operación. Cuando una turbina está operando a su velocidad normal, es espesor de la película lubricante mínimo entre el eje y el cojinete está en el orden los 50 micrones para ejes con diámetros entre 20 y 40 centímetros. El espesor mínimo se incrementa a 250 micrones para cojinetes principales con diámetros de 75 centímetros. Sin embargo, cuando la turbina está acoplada al engranaje de giro, el espesor de la película lubricante es de apenas unos cuantos micrones.
A medida que la velocidad se incrementa, de la misma manera se incrementa el espesor de la película entre el eje y el cojinete. Si una gran cantidad de partículas ingresa en el cojinete principal cuando el espesor de la película lubricante es de apenas unos cuantos micrones, estas partículas pueden rayar o dañar el eje y/o el perfil del cojinete, lo cual afecta la dinámica del aceite dentro del cojinete. Esto a menudo produce recalentamiento del cojinete y su posibilidad de falla.
Para controlar las partículas, se deben seleccionar los filtros teniendo en cuenta la tasa de filtración Beta (β) para un tamaño de poro específico, que permita cumplir con el código ISO de contaminación sólida objetivo.
Entender lo que está ocurriendo proporciona una mejor manera de identificar y valorar el riesgo. Una vez que el riesgo ha sido identificado, se pueden tomar acciones, evaluar las consecuencias, mitigar y desarrollar contingencias e implementar un plan para controlarlos.
Hay muchas formas para disminuir el riesgo cuando se regresa a operación equipos de grandes dimensiones. Una revisión a los datos de vibración y otros parámetros pueden proporcionar bastante información en cuanto al desempeño del equipo cuando se está calentando para llegar a las condiciones normales de operación. También le dice qué se requiere para extender la salud del equipo o incrementar su eficiencia operativa.
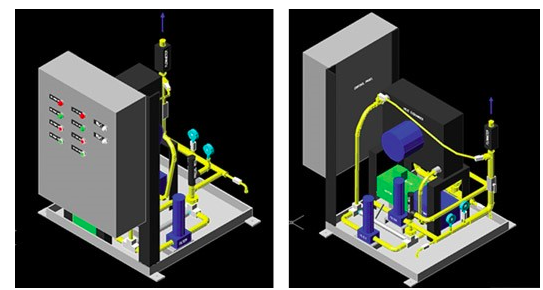
Figura 8. Conectar un sistema de filtración riñón al tanque o reservorio ayuda a disminuir los riesgos cuando un equipo es colocado nuevamente en operación
Quizás el método más versátil y rentable para ayudar a disminuir los riesgos de los equipos es disponer de un sistema de filtración riñón. Este tipo de sistema se puede conectar al tanque o reservorio para apoyar el regreso del equipo a operación.
La unidad de filtración debe estar dimensionada para procesar el contenido del tanque de aceite o reservorio varias veces por hora. Además, esta unidad debe estar equipada con un enfriador para los meses de verano cuando las cargas térmicas sobre la planta limitan la operación de los equipos. Además del filtrado y el enfriamiento, el sistema de filtración riñón debe incluir un deshidratador, el cual proporciona una excelente forma para extraer el agua del aceite antes de acoplar la turbina al engranaje de giro. Esto reducirá la cantidad de agua que puede ser introducida en las regiones de alta presión diferencial de la película de aceite en el cojinete principal, disminuyendo el riesgo o la cantidad de intermitencias en la formación de la película lubricante, lo cual puede causar daños y erosión de las superficies cubiertas o no con babbitt.
Tenga presente que los costos de un sistema de filtración auxiliar pueden ser recuperados rápidamente por una reducción en los costos de mantenimiento. De hecho, el costo de remplazar un cojinete dañado o el de mantener los equipos de la planta operando correctamente durante los meses picos de verano puede fácilmente justificar las reducción de los riesgos de que se repitan las fallas. Por ejemplo, una reducción del 10 por ciento de la potencia en una planta nuclear durante las temperaturas pico en el verano, pagaría el sistema de filtración externa de la mayoría de los equipos críticos en pocos días..
Noria Corporation. Traducido por Roberto Trujillo Corona, Noria Latín América.