Al seleccionar un lubricante para engranajes abiertos para usar en una aplicación particular, se debe considerar el método de aplicación utilizado. Los métodos típicos de aplicación utilizados en sistemas de engranajes abiertos son:
- Sistemas de pulverización/aspersión
- Alimentación por gravedad o por goteo
- Baño de aceite (sistemas de inmersión por salpicadura y rueda loca)
- Mano, cepillo o vertido.
Por lo general, si el lubricante para engranajes abiertos se va a aplicar mediante un sistema de goteo, un lubricador de alimentación forzada o un sistema de pulverización, debe ser lo suficientemente líquido como para fluir a través del equipo de aplicación. Para aplicaciones con cepillo, el lubricante para engranajes abiertos debe ser lo suficientemente fluido como para que pueda aplicarse uniformemente el cepillo sobre los dientes. En cualquier caso, durante la operación, el lubricante para engranajes abiertos debe ser lo suficientemente viscoso y pegajoso para resistir la salida por los dientes del engranaje.
Cuando los engranajes abiertos se lubrican por goteo o mediante el uso de sistemas de inmersión por salpicadura y rueda loca, el lubricante para engranajes abiertos no debe ser tan pesado que forme canales cuando los dientes del engranaje se sumergen en él. Finalmente, cuando se lubrican engranajes abiertos, la consistencia o grado y su facilidad de bombeo deben permitir una fácil aplicación en las condiciones ambientales predominantes.
Sistemas de pulverización/atomización
El tipo más común de sistema de pulverización/aspersión utilizado en la lubricación de engranajes abiertos es el sistema de pulverización mecánico intermitente. Su uso depende de que el lubricante permanezca en los dientes del engranaje durante varias revoluciones. Los sistemas de pulverización intermitente utilizan válvulas dosificadoras que dirigen el lubricante a una boquilla de aire/grasa que pulveriza el lubricante sobre los engranajes abiertos con la ayuda de presión de aire. Los componentes básicos de este tipo de sistema son una bomba, un controlador, una válvula dosificadora, un colector de aspersión y boquillas de aspersión.
El funcionamiento de este tipo de sistema es muy sencillo. Una señal de un controlador enciende la bomba para suministrar el lubricante a una válvula dosificadora de desplazamiento positivo. La válvula dosificadora puede ser de tipo progresiva, de dos líneas o de inyector. El lubricante dosificado se envía por un conducto en un colector de pulverización, donde el lubricante para engranajes abiertos se dirige a una boquilla.
Un segundo paso de aire presurizado (generalmente en el rango de 80 a 120 libras por pulgada cuadrada) se dirige a la misma boquilla. Este aire presurizado expulsa el lubricante desde la boquilla hacia el engranaje abierto. Después de dispensar una cantidad predeterminada de lubricante, tanto el sistema de aire como la bomba se apagan hasta el siguiente ciclo de lubricación. Por lo general, hay un retraso en el cierre del aire para garantizar que el lubricante haya salido de la boquilla. El propósito de esto es eliminar el lubricante de la punta de la boquilla, evitando así que se seque y obstruya la boquilla.
El tiempo de pulverización debe ser igual al tiempo necesario para una o dos revoluciones para garantizar una cobertura completa. Se deben realizar inspecciones periódicas para garantizar que se esté aplicando una cantidad suficiente de lubricante para engranajes abiertos para brindar una protección adecuada. Dos horas es el intervalo de tiempo máximo permitido entre aplicaciones según las guías de AGMA 9005-E02.
La cantidad de lubricante para engranajes abiertos que se debe utilizar depende de la aplicación en la que se utiliza el engranaje abierto (molinos, hornos, dragas, etc.) y de la velocidad de la línea de paso del engranaje, el consumo de energía eléctrica nominal del motor eléctrico que alimenta el engranaje (para molinos y hornos), el tipo de engranaje y el tipo de lubricante para engranajes abiertos que se aplicará. En muchas aplicaciones, su proveedor de lubricante puede recomendar la cantidad inicial a utilizar.
Estas tasas de aplicación se expresan en gramos por centímetro de ancho de cara por hora. En lugar de una recomendación inicial dada por el proveedor de lubricante, AGMA ha emitido pautas de cantidad de lubricante en la norma AGMA 9005-D94 que se pueden usar para métodos de aplicación intermitente.
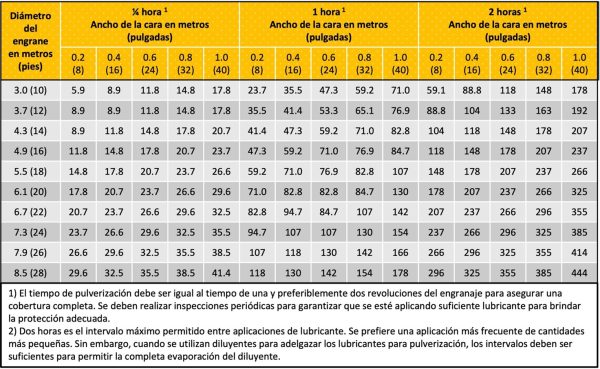
Para garantizar que se aplique una cantidad correcta de lubricante para engranajes abiertos y se mantenga la confiabilidad de la operación, es importante que mantenga un patrón de rociado perfecto sin espacios. Distribuya el lubricante para engranajes abiertos uniformemente por toda la altura y el ancho del flanco del diente en el lado cargado del engranaje.
El número de boquillas de pulverización que se utilizarán para una aplicación específica está determinado por el ancho del engranaje. Normalmente, se requieren de cuatro a seis boquillas pulverizadoras; deben estar espaciados adecuadamente para proporcionar una cobertura de lubricante adecuada en toda la cara de los dientes del engranaje.
Como guía, para engranajes abiertos de baja velocidad que funcionan a hasta 10 metros por segundo (2000 pies por minuto), las boquillas de los extremos deben colocarse de 50 a 65 milímetros (2 a 215 pulgadas) del borde de la cara del engranaje con las boquillas restantes espaciadas. De 130 a 180 milímetros (5 a 7 pulgadas) desde el centro. La ubicación de la boquilla también es una función del patrón de aspersión.
Las boquillas de pulverización generalmente se colocan para dirigir el lubricante para engranajes abiertos a los perfiles cargados de los dientes del engranaje (no al piñón) a una distancia máxima de 150 a 200 milímetros (6 a 8 pulgadas) de los dientes del engranaje 2 En las Figuras 1 y 2 se ilustran el patrón de pulverización correcto en los flancos de los dientes y una ilustración de la separación correcta de las boquillas de pulverización.
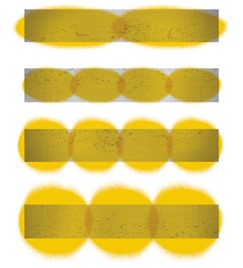
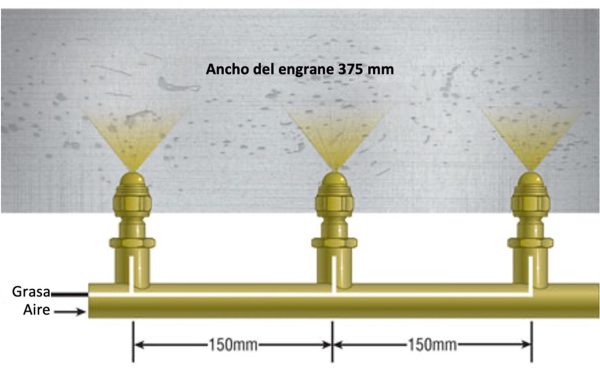
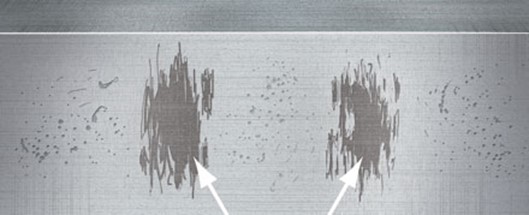
Los patrones de rociado inadecuados normalmente provocan raspaduras en las áreas resaltadas en la figura 3. Se requieren boquillas de pulverización adicionales correctamente espaciadas y una mayor presión de aire para mejorar la película lubricante.
La presión de aire a la barra rociadora también debe ajustarse correctamente; de lo contrario, el lubricante no se atomizará correctamente. Una presión de aire demasiado baja dará como resultado una apariencia salpicada, grumosa o fibrosa (como se ilustra en la Figura 3), mientras que una presión de aire demasiado alta tenderá a expulsar el lubricante del engranaje. Para la mayoría de los lubricantes, el ajuste de la presión de aire no debe establecerse por debajo de 75 psi (35 kpa o 5 bar) ni por encima de 90 psi (42 kpa o 6 bar).
Incluso si las boquillas de aspersión se monitorean mediante mecanismos de control de flujo, se recomiendan verificaciones periódicas del patrón de aspersión como parte del mantenimiento de una cobertura adecuada y uniforme del engranaje abierto en la cara del engranaje.
Las barras de aspersión tienen muchos diseños diferentes y muchos de los sistemas de aspersión más antiguos no permiten un fácil acceso para verificar el patrón de aspersión mientras el engranaje abierto está operativo. Si la barra rociadora no se abre hacia afuera con la puerta, la forma más segura de verificar el patrón de rociado es cuando la máquina está apagada. Un procedimiento recomendado para inspeccionar los patrones de aspersión es el siguiente:
- Asegúrese de que se cumplan los procedimientos de bloqueo, candado y etiqueta, luego abra la puerta de inspección y coloque un trozo de cartón o papel limpio sobre el conjunto de engranajes, donde la boquilla rociadora atomiza el lubricante en el juego de engranajes.
- Opere el sistema de lubricación y verifique la cobertura del lubricante en el cartón o papel. La cobertura debe superponerse de una boquilla rociadora a la siguiente y no debe haber espacios dentro de la altura y el ancho apropiados para cubrir los dientes del engranaje que transporta la carga.
- Si se encuentran espacios, es necesario ajustar la presión del aire, el ángulo de pulverización y la pulverización para obtener la cobertura adecuada.
- Una vez realizados los ajustes, repita el proceso hasta lograr el patrón de pulverización perfecto (como se muestra en la Figura 1).
Si es necesario cambiar la barra rociadora, se debe modificar el diseño de la barra rociadora para que se pueda verificar el patrón de rociado durante la operación del equipo (como se muestra en la Figura 4).
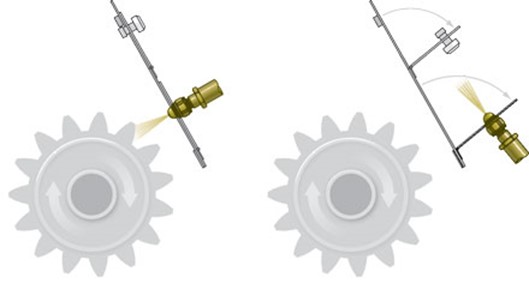
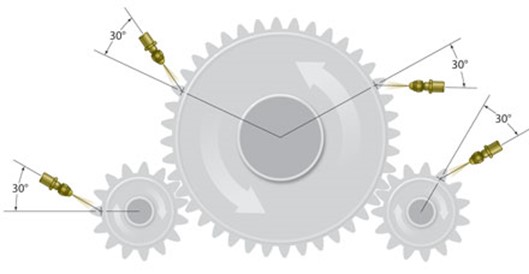
La barra rociadora debe colocarse en un ángulo de 30 grados para rociar el lubricante para engranajes abiertos sobre el lado impulsor o cargado del piñón o la corona. Ajustar el ángulo de pulverización a 30° (como se muestra en la Figura 5) logrará una muy buena distribución del lubricante hacia arriba o hacia abajo, siempre hacia el flanco del diente que soporta la carga.
La distancia entre la boquilla rociadora y el engranaje es de aproximadamente 200 milímetros más o menos 50 mm (8 pulgadas más o menos 2 pulgadas), dependiendo de la presión del aire y la altura de los dientes. El ancho del diente del engranaje determinará la cantidad de boquillas pulverizadoras necesarias para lubricar adecuadamente la transmisión de engranajes abiertos.
Para garantizar aún más que se aplique la cantidad adecuada de lubricante una vez que las boquillas y los patrones de la barra rociadora estén configurados, se recomienda pesar la cantidad de lubricante que se expulsa de cada inyector. Con el tiempo, las boquillas rociadoras de los inyectores no suministran la cantidad adecuada de lubricante para la que están diseñadas por ciclo de aplicación.
La aplicación de demasiado lubricante puede causar desperdicio, mientras que una lubricación insuficiente puede provocar un mayor desgaste y una eventual falla de los componentes. La cantidad de lubricante que se debe expulsar de cada inyector se puede obtener del fabricante del sistema de lubricación automática. Por ejemplo, un inyector estilo Lincoln SL-1 normalmente expulsa 1.31 gramos (0.046 onzas) por ciclo de lubricante.
Los ajustes del temporizador en el sistema de lubricación automática eventualmente deben configurarse en la frecuencia más corta dependiendo del tipo de utilizado. Para fluidos base asfáltica y sintéticos de alta viscosidad, el intervalo de tiempo típico de fraguado es de 10 a 20 minutos, mientras que para grasas semifluidas y lubricantes para engranajes abiertos de tipo gel/polímero espesado, el intervalo de tiempo típico es de 15 a 30 minutos.
Se puede utilizar una luz estroboscópica para comprobar el aspecto de los engranajes durante el funcionamiento. La luz estroboscópica debe ajustarse a la misma velocidad a la que gira el engranaje. Un engranaje bien lubricado tendrá una apariencia de color oscuro a semitransparente dependiendo del tipo de lubricante que se utilice, y aparecerán hilos de lubricante a medida que los dientes del engranaje y el piñón se separen. Un engranaje sobrelubricado se volverá negro y el exceso de lubricante goteará, se desprenderá o se acumulará en los dientes y las zonas de raíz del engranaje.
Además, se pueden tomar lecturas de temperatura en la cara del engranaje usando un termómetro sin contacto para verificar si el engranaje abierto está lubricado adecuadamente. Una temperatura uniforme en los dientes del engranaje indica que el engranaje está siendo lubricado adecuadamente.
Además de usarse para verificar la lubricación adecuada, la lámpara estroboscópica y la lectura de temperatura se pueden usar para verificar desalineación. Cualquier desalineación da como resultado un menor contacto entre los engranajes acoplados, lo que resulta en un mayor desgaste. Una diferencia de aproximadamente 18 ºC (30 ºF) a través del diente del engranaje, y áreas de lubricante más oscuras a más claras a través de la película de contacto, indican desalineación.
Sistemas de alimentación por gravedad o por goteo
Los sistemas de alimentación por gravedad o por goteo se encuentran en molinos, hornos, palas, dragas y excavadoras. Estos sistemas constan de uno o más lubricadores, bandejas en cascada, líneas de alimentación presurizadas o ruedas aplicadoras. Permiten que el lubricante gotee en el engranaje a un ritmo determinado. Este método de aplicación se limita a engranajes abiertos con velocidades de línea de paso de 7.5 metros por segundo (1500 pies por minuto) o menos.
Para este tipo de sistemas por lo general se utilizan lubricantes asfálticos o aceite sintético de alta viscosidad. Si en estos sistemas se utilizan líneas de alimentación presurizadas o ruedas aplicadoras, se puede utilizar una grasa semifluida o un tipo de lubricante espesado con gel/polímero.
Sistema de baño de aceite (inmersión por salpique y rueda loca)
Los sistemas de baño de aceite son el método más simple para lubricar engranajes abiertos. Se permite que el engranaje o una rueda loca acoplada con el engranaje se sumerja en el lubricante, llevándolo hasta el engrane. Los sistemas de inmersión de rueda loca generalmente se limitan a sistemas de engranajes abiertos con velocidades de línea de paso inferiores a 1.5 metros por segundo (300 pies por minuto). Algunos sistemas también contendrán bombas de recirculación y sistemas de filtración. El sistema de inmersión por salpique y rueda loca se puede encontrar en aplicaciones de molinos y hornos.
Como recomendación general, en estos sistemas se puede utilizar aceite asfáltico, sintético de alta viscosidad, grasa semifluida y lubricante para engranajes abiertos tipo gel/polímero. Si se utiliza una grasa semifluida tipo gel/polímero, el lubricante debe tener una consistencia de semifluida a fluida. Si el lubricante es del tipo de fluido de base asfáltica o sintética de alta viscosidad, la viscosidad del fluido debe ser de un mínimo de 1000 centistokes (cSt) a 40 grados Celsius.
A mano, con brocha o vertido
Este método de aplicación es uno de los más antiguos y peligrosos utilizados para aplicar lubricantes para engranajes abiertos. Se ha utilizado para aplicar lubricantes en molinos, hornos, palas, dragas y excavadoras. Generalmente, mediante este método se aplican lubricantes de tipo asfáltico y sintéticos de alta viscosidad.
Esto puede resultar no sólo en la aplicación de una cantidad inadecuada de lubricante, sino también en la introducción de contaminantes en los engranajes. La aplicación adicional de este método mientras el engranaje abierto está operativo puede generar consideraciones de seguridad que pueden provocar lesiones o incluso la muerte a la persona que aplica el lubricante.
Espesor de la película lubricante y criterios de selección
El régimen de lubricación principal requerido para lubricar engranajes abiertos es la lubricación elastrohidrodinámica (EHD, por sus siglas en inglés). Según la teoría de lubricación EHD, el factor crítico es el espesor de la película del lubricante, el cual depende de la viscosidad dinámica del lubricante a las temperaturas de funcionamiento, la velocidad promedio de la superficie del engranaje, temperatura, cargas, geometría del engranaje, etc.
Se ha establecido que la condición de lubricación que existe en la mayoría de los engranajes es predominantemente elastrohidrodinámica. Los dientes de los engranajes están sujetos a enormes presiones de contacto en áreas relativamente pequeñas (posiblemente hasta 435,000 psi) y, sin embargo, se lubrican exitosamente con películas muy delgadas de lubricante. Hay dos razones para esto:
- La alta presión hace que las superficies se deformen elásticamente y distribuyan la carga en un área más amplia.
- La viscosidad del lubricante aumenta considerablemente con la presión, aumentando así la capacidad de carga del lubricante.
Una vez determinado el espesor de la película, otro parámetro importante que debe calcularse es la relación Lambda. Esta relación se define como la relación entre el espesor de la película EHD del lubricante y la rugosidad compuesta de las superficies metálicas en contacto.
A medida que la relación Lambda se aproxima a 1 (es decir, el espesor de la película es del mismo orden que la rugosidad de la superficie), se puede esperar que haya un mayor contacto entre los dos engranajes en contacto.
Cabe señalar que este cálculo se basa únicamente en la viscosidad del aceite base del lubricante; no tiene en cuenta ninguna contribución al espesor de la película que pueda realizar el sistema espesante del lubricante o sus aditivos sólidos. Además, algunos tipos de lubricantes para engranajes abiertos, como los tipo grasa y espesados en gel/polímero, pueden contener fluidos base de viscosidad ligera.
Estos fluidos base de viscosidad ligera se utilizan como reducción de los fluidos base de alta viscosidad presentes en la formulación para mejorar la bombeabilidad del producto durante condiciones de baja temperatura ambiente.
Los fluidos base de viscosidad ligera son volátiles y se disipan en condiciones de funcionamiento. Posteriormente, la viscosidad base de estos lubricantes aumenta, generando una película lubricante duradera y pegajosa que se adhiere al engranaje.
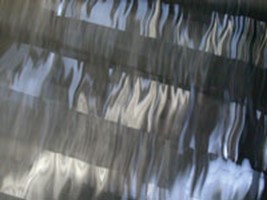
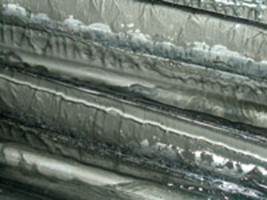
Además de tomar en consideración el espesor de la película lubricante proporcionado por el lubricante seleccionado, otras consideraciones que se deben tener en cuenta al recomendar el tipo, grado y cantidad adecuados a aplicar son:
- Los requisitos del OEM.
- El tipo de aplicación de engranajes abiertos: molinos, hornos, palas, dragas, etc.
- La temperatura ambiente encontrada en el área en la que opera la máquina.
- Las condiciones climáticas en las que funciona la máquina: hielo, nieve, humedad, polvo.
- Cómo se aplica el lubricante.
- Si se aplica mediante un sistema de lubricación automática o en aerosol, el tipo de sistema de lubricación instalado: Farval, Lincoln, Worner, Droppsa, etc.
- El tipo y proporción de la bomba utilizada en el sistema de lubricación automática.
- El ancho del piñón.
- Si el engranaje es de piñón doble o simple
- La potencia nominal del motor eléctrico.
- La posición y el número de boquillas de aspersión.
Una vez que se conocen todas estas condiciones, se puede seleccionar el lubricante de engranajes abiertos adecuado para la aplicación dada en función de los diferentes temas, métodos de aplicación y características discutidos en este documento.
Finalmente, al cambiar de lubricantes para engranajes abiertos o aplicar lubricantes en equipos nuevos donde no se usó lubricante anteriormente, se deben seguir los siguientes procedimientos:
Procedimiento en equipos nuevos:
- Limpie todos los revestimientos y residuos de los engranajes.
- Cubra el engranaje y el piñón con una película ligera de lubricante para engranajes abiertos mediante algún tipo de método de pulverización.
Procedimiento de puesta en marcha:
- Haga funcionar el equipo lentamente sin carga para verificar que haya lubricante en toda la zona de carga.
- Aumente gradualmente la velocidad y la carga mientras enciende el sistema de lubricación automática.
- Monitoree continuamente hasta que se mantenga un recubrimiento adecuado.
Para sistemas de pulverización:
- Antes del arranque, purgue las líneas de lubricante y verifique los patrones de rociado para una cobertura completa.
- Ajuste la presión y el volumen del aire según sea necesario.
Para sistemas de goteo:
- La mayoría de los lubricantes para engranajes abiertos están diseñados para adherirse donde se aplican. Los tubos de goteo no deben estar separados más de 2 pulgadas.
Procedimiento a seguir al cambiar de un tipo de lubricante para engranajes abiertos a otro:
Aunque es mejor limpiar completamente el engranaje, el piñón y las protecciones del engranaje, se puede realizar la conversión de un tipo de lubricante para engranajes abiertos a otro aplicando el lubricante para engranajes abiertos que se usará directamente sobre la mayoría de las aplicaciones existentes.
Procedimiento:
- Purgue bien las líneas de lubricante.
- Inicie los ajustes de sincronización un 50 por ciento más altos que los ajustes operativos para garantizar que todas las líneas estén purgadas y lavadas y que hayan formado una película de cobertura de lubricante suficiente antes de reducir la tasa de consumo de lubricante a los ajustes operativos.
- Reajuste el temporizador para mantener una película lubricante adecuada. La cantidad de lubricante no debe reducirse bruscamente sino a intervalos de cinco minutos de 150 a 200 horas para molinos y de 100 a 150 horas para palas, dragas y excavadoras.
- Se debe monitorear el desempeño del producto.
- Al reducir la cantidad de consumo a la unidad de control del sistema de pulverización, se debe configurar para garantizar que los intervalos entre ciclos de pulverización sean lo más cortos posible. Los ciclos de pulverización cortos y frecuentes garantizan que el lubricante se suministre uniformemente al componente; esto aumenta la confiabilidad funcional.
- Ajuste la presión y el volumen del aire según sea necesario.
- Se requieren inspecciones de los sistemas de lubricación, las condiciones de los flancos de los dientes y el patrón de pulverización para garantizar un funcionamiento fiable. El sistema de pulverización debe mantenerse minuciosamente de acuerdo con las instrucciones del fabricante.
Referencias
1) ANSI/AGMA 9005-D-94 – “Lubricación de engranajes industriales, Tabla 10”, página 10
2) ANSI/AGMA 9005-D-94 – “Lubricación de engranajes industriales, página 11
Sobre el Autor
Lawrence G. Ludwig Jr. es el químico jefe y director técnico de Schaeffer Manufacturing. Para obtener más información, visite www.schaefferoil.com.