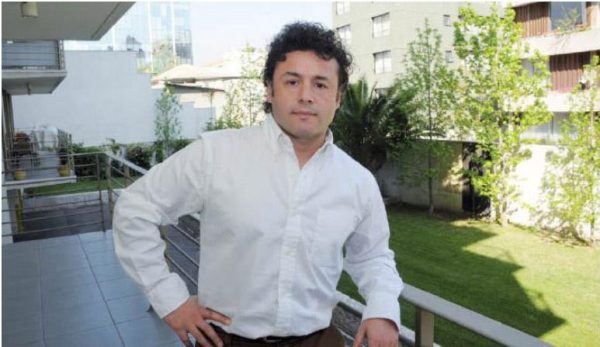
Uno de los desafíos futuros para la industria minera es la instauración de sistemas de mantenimiento predictivos, que no sólo registren una gran cantidad de datos, sino que de forma incipiente y clara, permitan tomar decisiones para gestionar los activos Daniela Tapia
La innovación, las nuevas tecnologías, el gran tamaño y la mayor complejidad en los requerimientos de los procesos productivos, han puesto a prueba al mantenimiento, función que cada día se hace más gravitante en las faenas mineras. En la constante búsqueda por contar con operaciones más rentables y seguras, una mayor disponibilidad, confiabilidad y disminución de los riesgos en los equipos, mantenedores y operadores han tenido que asumir estos nuevos desafíos.
Lo anterior ha llevado a considerar a la mantenibilidad y confiabilidad como factores clave en la dirección de un proyecto y a su integración efectiva en la realización del mismo.
Además, la gestión de activos ha cobrado relevancia en la minería, a través de sistemas corporativos de implementación de procesos de mantenimiento.
Por ello, en las industrias intensivas en el uso de capital, como la minería, el desempeño de los activos instalados es una fuente de valor y retorno fundamental. Y el proceso de mantenimiento de esos activos, entendido como el conjunto de operaciones que aseguran el correcto funcionamiento y desempeño de los mismos, es igualmente importante para el negocio.
Sin embargo, la tendencia está apuntando hacia una combinación de elementos como el mantenimiento proactivo, que busca dar las condiciones óptimas para el trabajo de los equipos. Por otra parte, está el mantenimiento preventivo basado en modelos estadísticos de toma de decisiones y el mantenimiento predictivo que, a través del análisis de los síntomas de los equipos, permite mejorar la oportunidad y confiabilidad de las decisiones, aumentando la capacidad para determinar la causalidad de eventos.
En entrevista con Revista Nueva Minería & Energía, el gerente técnico de la empresa de ingeniería en mantenimiento Shen-Re y académico de esta disciplina en la Universidad de Chile, Eduardo Salamanca, habla sobre estos temas y la norma ISO 55000, que proporcionará una visión global, conceptos y terminología en Gerencia de Activos.
¿Cómo surgió el concepto “gestión de activos” y cuán relevante es para la actividad minera?
El concepto de gestión de activos físicos apareció cuando se entendió que la función de mantenimiento no era suficiente para aumentar la rentabilidad y minimizar los riesgos de sustentabilidad que pudieran tener los procesos productivos. A partir del mantenimiento habitual -que también depende de factores como la forma en que se operan los equipos y las diferentes fuentes de error humano- se comprendió y conceptualizó el término de gestión de activo físico.
El mantenimiento está circunscrito dentro de la gestión de activos físicos. Esta última considera la función de la continuidad operacional y la disminución de los riesgos como un factor importante dentro del negocio. Entonces, al tener menor probabilidad de que fallen los equipos, los procesos productivos minimizan sus costos unitarios de producción y no se corren riesgos por algún efecto en sustentabilidad. Ejemplo de ello, son las mineras que se encuentran próximas a lugares urbanos, o cuyos desechos pueden afectar reservas naturales.
¿La gestión de activos corresponde a una especificación más integral y desarrollada que el mantenimiento?
Efectivamente. En rigor, la gestión de activos físicos busca que el activo tenga un alto retorno para el negocio minimizando sus riesgos. Por lo tanto, va a tratar de unir todos los entes que tienen relación con la función del equipo para poder maximizar sus indicadores. Esto depende de cómo la organización esté alineada con ello o de qué manera la misma decisión de mantenimiento a realizar va a estar al servicio de la producción o minimizar los costos de oportunidad por no producir.
¿Qué políticas o nuevas tendencias se han trazado para mantener en buenas condiciones los activos físicos de las compañías mineras?
En general, las estrategias de mantenimiento que se insertan dentro de la gestión de activos físicos han motivado mejoras diferentes en cada una de las faenas mineras, tanto desde el punto de vista de la operación confiable de los equipos o en la confiabilidad basada en minimizar el error humano.
En general, en minería se debe separar dos áreas importantes, tales como los equipos móviles y los equipos jos. Los equipos móviles son todos los equipos que tienen que ver con el trabajo en el rajo de la mina, en tanto, la vida de estos equipos depende mucho de cómo se operen. Los equipos móviles poseen en general una serie de transductores que permiten medir cómo se operan estas máquinas para tener continuidad operacional. Se están instaurando metodologías de monitoreo predictivo que permitan detectar las fallas antes de que ocurran.
En general, los equipos móviles son complejos o tienen una característica diferente de mantenimiento debido a que dependen mucho de cómo se operan, pues las cargas y la velocidad a las que están afectados generan esfuerzos diferentes en los componentes de los equipos. Poder monitorear los síntomas que emite la máquina en el caso del mantenimiento predictivo se torna un reto mayor.
En el caso del mantenimiento de equipos estáticos o estacionarios, obviamente ha habido un avance y una consolidación mayor respecto de algunas estrategias de mantenimiento como las predictivas, pero en este aspecto los aportes más grandes han sido desde el punto de vista de la innovación y los diseños de equipos que permiten tener consideraciones de confiabilidad.
Estrategias de mantenimiento
¿Cuán madura cree usted que se encuentra la industria en torno al mejoramiento de la confiabilidad y por consiguiente, en las estrategias de mantenimiento?
La confiabilidad es el complemento de la probabilidad de falla, por lo que ésta depende mucho de una serie de herramientas o elementos que van a incidir en ella. Por ejemplo, en el caso de las inferencias estadísticas o análisis de confiabilidad se basan en tener buenos históricos de fallas, por lo que ciertas compañías mineras han destinado muchos recursos para poder tener bases de datos de dignas que permitan hacer análisis estadísticos y luego optimizar y aumentar la confiabilidad de los equipos.
Por otro lado, en el mantenimiento predictivo ha habido una serie de innovaciones que han permitido tener mayores herramientas predictivas. Prueba de ello, es que hay un desarrollo tecnológico que ha hecho que los transductores y los sistemas de medición hayan bajado de precio y sean más fiables, lo que hace que los sistemas de adquisición permitan hacer una mayor gestión sobre el trabajo de los activos.
También tiene que ver el mantenimiento proactivo, es decir, el hecho de entender que algunas variables son vitales para extender la vida de los equipos. Por ejemplo, en el caso de los contaminantes en los aceites o en los sistemas o leo hidráulicos, además de poder tener un sistema que detecte los problemas que tienen o de tener un análisis que permita definir los cambios en los componentes, es muy importante evitar que el aceite tenga contaminantes lo que va a permitir que los sistemas vivan más tiempo.
¿A través de qué parámetros se puede medir esta evolución?, ¿qué papel juegan las nuevas tecnologías?
La evolución se va a medir a través de los KPI o indicadores de resultados y de proceso que se puedan tener. Los KPI primero, van a estar al servicio de un resultado que se está buscando tanto en la disponibilidad como en la con abilidad de los sistemas, pero los indicadores con los cuales mediré la forma en que estoy haciendo el mantenimiento o la gestión de activos físicos indicará donde estoy colocando mi atención. Si solamente me jo en parámetros de cumplimiento para mantenimiento preventivo (porcentaje de cumplimiento de tareas) va a indicar en qué estado evolutivo está la organización.
Sin embargo, si estamos cifrando nuestro interés en indicadores asociados a mantenimiento proactivo y a la cantidad de fallas que se pueden evitar en mantenimiento predictivo, va a ser un indicador de cómo la organización está creciendo para poder alcanzar las mejores prácticas y estándares en lo que se re ere a gestión de activos físicos.
¿Qué porcentaje de los costos destina una compañía minera al mantenimiento?
Esto es variable. En general, estamos hablando del costo directo inversional del orden de un 20 o 25%, pero este es un costo directo asociado al costo operativo. Sin embargo, no se considera el costo de pérdida relacionado a pérdidas productivas y tampoco se consideran los costos asociados a potenciales riesgos u ocurrencia de eventos que puedan afectar la salud, la comunidad, el medio ambiente y la seguridad del negocio.
Ahora bien, una etapa clave que marcará los costos de mantenimiento futuros y por ende, los costos unitarios de producción es la etapa de diseño. Desde un punto de vista inversional y de gestión deben ser considerados los elementos que permitan alcanzar alta confiabilidad y disponibilidad de los activos en su etapa de producción, a través de todas las etapas de configuración y ejecución de un nuevo proyecto minero.
Mantenimiento predictivo
Hace tiempo que se habla del mantenimiento predictivo ¿Es el camino que utilizan hoy las compañías o aún falta al respecto?
Respecto a esta materia, separo los equipos móviles de los equipos fijos por las características técnicas que tienen. Muchos han intentado avanzar desde el mantenimiento preventivo hacia el predictivo, algunos con éxito pero otros no. En forma genérica, esto depende de cómo ha sido el plan de instauración de un proceso de mantenimiento predictivo, porque es muy importante definir qué modos de fallas se podrán evitar, en qué equipos se va a trabajar, cómo el personal va a estar capacitado para gestionar las tareas de mantenimiento, debido a cómo se aplicó el mantenimiento predictivo.
Como hay una tradición de mantenimiento preventivo donde hay que cumplir un plan matriz, cambio de componentes o realizar ajustes, muchas personas creen que al instaurar mantenimiento predictivo es la panacea para aumentar confiabilidad. Un buen mantenimiento predictivo predecirá la falla para poder planificar su intervención, pero no permitirá que alcancemos la vida útil de un equipo considerado en su etapa de diseño.
El monitoreo remoto de equipos, estandarizados e integrados a sistemas de control, ¿puede ser una realidad a corto plazo?
Hay esfuerzos importantes. Por ejemplo, Codelco a través de su alianza con Micomo iluminará los lugares de trabajo mediante un sistema de conexión de alta velocidad, lo que va a permitir que se pueda manejar una gran cantidad de información.
El problema que se viene en torno al mantenimiento es qué hacer con la gran cantidad de información a manejar y cómo de forma incipiente podemos tomar decisiones para que los modos de falla se detecten lo antes posible para evitar pérdidas productivas.
ISO 55000
¿Qué marca el cambio entre el PAS 55 y la norma ISO 55000?, ¿cuáles son las debilidades de PAS 55 que se desean corregir y mejorar en esta versión internacional de la ISO 55000?
Hay varios elementos. La PAS 55, que es utilizada por al menos 49 organizaciones de 15 industrias intensivas en activos físicos, tales como minería, petróleo y gas, energía, transporte, etc, da un marco de trabajo que invita a poder cumplir una serie de elementos, pero es bastante genérica y no integra otras certificaciones ISO asociadas.
La tendencia apunta hacia la ISO 55000 que proporcionará una visión global, conceptos y terminología en Gerencia de Activos.
La PAS 55 es una norma británica que propone, a través del ciclo de vida completo del activo incluyendo diseño, construcción, puesta en marcha, operación, mantenimiento, mejoramiento y cierre, 28 puntos para una correcta Gestión de Activos Físicos. Algunos elementos claves en esta norma son la identificación y minimización de los riesgos y la integración de las diferentes áreas relacionadas con el activo, los que estarán al servicio de las metas y aspiraciones de la gerencia corporativa.
Aunque la serie de normas ISO 55000 aún están en confección, se conocen algunos elementos de mejora que promoverá la nueva norma basada en la PAS 55. Ejemplo de
esto, es que propondrá canales para definir “buenas prácticas” en los diferentes tópicos de los 28 puntos propuestos, buscará un enfoque no escalable o flexible y será compatible con otros estándares como la ISO 9001, 14001 y 18001. Además, buscará una alta importancia hacia políticas, estrategias, objetivos y planes.
¿Cuál será el impacto de la ISO 55000 en los procesos mineros?
Va a tener un impacto importante en cuanto se quiera instaurar el sistema. Por un lado, las certi caciones en general permiten tener un marco de trabajo en pos de aumentar la con abilidad e incrementar la disponibilidad de los equipos a través de una visión más holística y cubriendo todo el ciclo de vida del activo, en general.
Probablemente todos los diseños y sus etapas respectivas deberán cumplir esta norma, muy sintonizada, por ejemplo con la norma de con abilidad y mantenibilidad NCC30 de Codelco referente a nuevos proyectos. Así también las nuevas exigencias para el cierre de los procesos mineros, como las impulsadas por el Sernageomin, deberán incluir estos elementos para minimizar los riesgos y los efectos en el medio ambiente y la comunidad.
¿Cuáles son los desafíos que usted visualiza para la gestión del mantenimiento en la industria minera? Destaco fuertemente algunos factores tales como, la instauración de sistemas predictivos, los cuales tienen que ser mucho más que la creación de una unidad, y trascender en la toma de decisiones para gestionar los activos y la identi cación y minimización del error humano en cada uno de los elementos que in uyen en la con abilidad de un activo.
Asimismo, subrayo la instauración de una mentalidad proactiva, que busque dar las condiciones óptimas posibles para el funcionamiento; el involucramiento del área operativa, entendiendo que en forma importante la vida de un activo depende de cómo es operado, y un registro con able de los eventos de falla a través de un uso correcto de los CMMS (Sistemas de Gestión de Mantenimiento) existentes.
El problema es que no hay un mecanismo que le avise al mantenedor cuándo se produce una anomalía determinada. Por ello, es necesario contar con una buena base histórica de datos que permita hacer un análisis real.
Noria Corporation. Traducido por Roberto Trujillo Corona, Noria Latín América.