El análisis de criticidad se define como el proceso de asignar a los activos una calificación de criticidad basada en su riesgo potencial de falla.
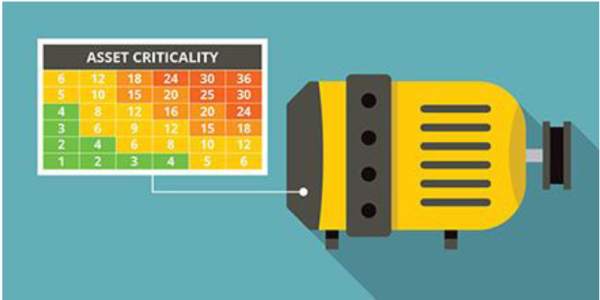
¿Qué es el análisis de criticidad?
El análisis de criticidad se define como el proceso de asignar a los activos una calificación de criticidad basada en su riesgo potencial. El riesgo se define como “el efecto de la incertidumbre sobre los objetivos”, de acuerdo con ISO 31000:2009 – Gestión del riesgo – Principios y directrices. Dado que no puede cuantificarse realmente, el riesgo, en este caso, se considera como todas las formas posibles en que los activos pueden fallar y los efectos que la falla puede tener en el sistema y la operación como un todo. Dado esto, el análisis de criticidad está estrechamente relacionado con un análisis de modos de falla y efectos (FMEA, por sus siglas en inglés) y un análisis de modos de falla, efectos y criticidad (FMECA, por sus siglas en inglés), que se discutirá más adelante. Una vez que se ha realizado un análisis de criticidad, un FMEA generalmente se realiza en el 20 por ciento superior de los activos más críticos.
¿Cuál es el propósito del análisis de criticidad?
Entonces, ¿por qué es importante el análisis de criticidad? Usted está escuchando constantemente acerca de la criticidad: hacer un análisis de criticidad para priorizar los activos para un plan de mantenimiento productivo total (TPM, por sus siglas en inglés), un programa de mantenimiento basado en condición o un análisis causa raíz (RCA, por sus siglas en inglés) en equipos de alta prioridad. La criticidad juega un papel en casi todos los tipos de mantenimiento. Todo se reduce al riesgo y lo que hace que cada pieza del equipo sea crítica. El análisis de criticidad le permite comprender los riesgos potenciales del activo que podrían afectar su operación. Asegura que la confiabilidad se vea con una lupa desde una perspectiva basada en el riesgo en lugar de la opinión de cada persona.
Según el Life Cycle Institute, un modelo de análisis de criticidad debe cubrir múltiples áreas de su organización, incluyendo:
- Impacto en el cliente
- Impacto en la seguridad y el medio ambiente.
- Capacidad para aislar fallas de un solo punto
- Historial de mantenimiento preventivo (PM, por sus siglas en inglés)
- Historial de mantenimiento correctivo
- Tiempo medio entre fallas (MTBF, por sus siglas en inglés)
- Tiempo de entrega de repuestos
- Probabilidad de falla
Debido a que el modelo de criticidad se ocupa de múltiples áreas de una organización, un análisis de criticidad debería ser un esfuerzo de toda la empresa. La inclusión de departamentos que se ocupan de operaciones, ingeniería, mantenimiento, compras y salud y seguridad garantiza que el análisis considere todas las funciones de la operación como un todo. Debe comprender que el riesgo se puede definir de manera diferente en varios equipos. Tener un equipo diverso que brinde información ayuda con la subjetividad de la asignación de riesgos.
El análisis de criticidad también es importante porque puede usarse en una variedad de escenarios dentro de una organización. Algunos de estos escenarios podrían verse así:
- Se puede emplear un puntaje de criticidad como entrada para ayudar a determinar la clasificación de prioridad final para las tareas de mantenimiento, que a su vez se puede usar junto con la prioridad de la orden de trabajo.
- Puede ayudar a identificar estrategias de mitigación de riesgos de alto nivel para equipos específicos. Por ejemplo, esto podría involucrar la aplicación de una técnica de monitoreo de condición a activos de alta criticidad.
- Puede ayudar a determinar la cantidad óptima de repuestos para cada pieza de equipo.
- Puede proporcionar información valiosa para las discusiones presupuestarias, por lo que el equipo de alta criticidad tiene mayor prioridad para las actualizaciones o el reemplazo.
- El análisis de criticidad ayuda a los ingenieros de confiabilidad a enfocar sus esfuerzos y energía en los activos más críticos.
Cómo realizar un análisis de criticidad
Es importante tener en cuenta que no hay un enfoque definitivo para realizar un análisis de criticidad. Los siguientes son dos métodos ampliamente utilizados, un enfoque simplista para comenzar y otro método en profundidad.
¿Entonces, en dónde debe empezar? Muchas organizaciones solo quieren saber qué activos deben incluirse en una evaluación de criticidad. En lugar de asumir que todos sus activos son críticos, haga una lista de los activos clave que su equipo considera críticos y calcule el costo del tiempo de inactividad y las reparaciones. Puede que le sorprendan los resultados. Por ejemplo, puede tener cientos de motores en movimiento constante, que son bastante críticos, pero el activo más crítico es la caldera que produce vapor para mantener esos motores en movimiento.
Dado que el objetivo de este enfoque es encontrar un buen punto de partida, echemos un vistazo a algunos pasos de acción que puede seguir para comenzar un plan de criticidad.
- Compile una lista abreviada de activos, que no supere el 20 por ciento de todos los activos. La mejor práctica para esto es una relación de 5 a 1 o mayor.
- Reúna un equipo de personal del lado de operaciones, mantenimiento, ingeniería y adquisiciones de la organización para realizar una encuesta sobre la maquinaria de la planta. Los operadores de maquinaria también deberían estar incluidos en este equipo.
- Luego, clasifique la criticidad de los activos utilizando una fórmula establecida. Lifetime Reliability Solutions utiliza la siguiente fórmula para determinar el impacto financiero de un activo: Criticidad de la maquinaria = Frecuencia de falla (por año) x Consecuencia de costos ($) = Riesgo ($ por año). La consecuencia del costo en esta fórmula es el costo de la producción perdida más los costos de reparación. Por ejemplo, si tiene muchas máquinas idénticas, el tiempo de inactividad de la máquina puede ser de US $ 400 por hora, por máquina.
Ahora que tiene una idea básica sobre cómo comenzar, veamos un enfoque más profundo y racionalizado para el análisis de criticidad. Este método incluye tres pasos: acordar la matriz de riesgos que se utilizará, ensamblar la jerarquía de sus activos y evaluar los riesgos de falla para cada activo.
1. Acuerde la matriz de riesgos. Esto se re ere principalmente a las matrices de riesgo corporativas existentes y cómo la mayoría de estas matrices pueden necesitar ser ajustadas para incluir una evaluación de la criticidad de la maquinaria. Dos áreas clave donde podrían necesitarse modificaciones son acordar los niveles de riesgo desde un nivel corporativo y de máquina, y combinar las categorías de riesgo superpuestas. A nivel corporativo, una falla que conduce a una pérdida de US $ 1 millón en ingresos podría considerarse menor o moderada, pero a nivel operativo de equipo o planta, podría verse como importante. En segundo lugar, las matrices de riesgos que incluyen categorías separadas para cosas como salud, seguridad, medio ambiente y comunidad se pueden combinar, porque si una de estas categorías se ve afectada por una falla, las demás también lo serán. La combinación de categorías acelerará el análisis de criticidad.
2. Ensamble su jerarquía de activos. Se recomienda que su jerarquía de máquinas o activos se distribuya a lo largo de líneas funcionales, lo que significa que el piso de su planta tiene un cierto número de unidades de proceso, esas unidades de proceso están formadas por sus propios sistemas de máquinas, y cada uno de esos sistemas está compuesto por componentes individuales. Esto le permite realizar un análisis de criticidad mucho más rápido que si su jerarquía de activos estuviera organizada por líneas de clase de máquinas. Incluso si sus activos ya están organizados a lo largo de líneas funcionales, aún deben revisarse para asegurarse de que nada esté fuera de línea. Tener una jerarquía correctamente ensamblada al principio acelera el análisis de criticidad más adelante.
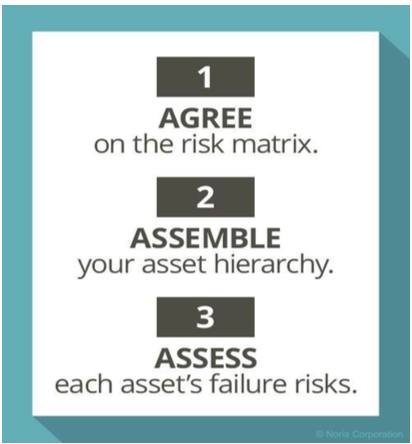
3. Evalúe los riesgos de falla de cada activo. Al evaluar los riesgos de falla para ayudar a determinar la criticidad de la maquinaria, tenga en cuenta los siguientes puntos:
- Entienda que el riesgo se relaciona con eventos, no con máquinas;
- Elija un solo evento: el evento de resultado máximo razonable (RMR);
- Observe solo la dimensión con el nivel de riesgo más alto; y
- Comience en la parte superior de la jerarquía y avance hacia abajo.
En segundo lugar, cada equipo puede tener una miríada de posibles eventos de falla, y los riesgos asociados con cada uno de esos eventos son diferentes. Sería extremadamente lento intentar identificar todos estos posibles eventos. Múltiples consultores y expertos en confiabilidad recomiendan elegir solo un evento, el que mejor represente el resultado máximo razonable (RMR) en términos de riesgo para ese equipo en particular. Esto significa que debe buscar un evento que sea más probable y uno en el que se determine que el riesgo general es el más alto.
Esta determinación debe llevarse a cabo en un entorno tipo taller, ya que las personas de diferentes departamentos tendrán diferentes opiniones sobre el evento RMR. En esta discusión deben incluirse personas que conocen mejor la maquinaria y quienes entienden las consecuencias de una falla desde una perspectiva comercial.
En tercer lugar, considere evaluar solo una dimensión de riesgo, la que tenga el nivel de riesgo más alto, para evitar perder el tiempo. Como se mencionó anteriormente, mirar cada evento individualmente generalmente termina siendo una pérdida de tiempo, ya que muchos afectan directamente a los demás. A menudo, es bastante obvio qué dimensión del riesgo viene con el mayor nivel de riesgo. Por ejemplo, si está evaluando la criticidad de una válvula de alivio de presión en una planta de gas natural, los riesgos asociados con la seguridad son lo que observará (incluido el impacto ambiental y comunitario). Si está evaluando un componente que proporciona electricidad para operar la maquinaria de la planta, lo más probable es que considere el impacto económico de esa falla.
Finalmente, para garantizar que su enfoque de análisis de criticidad sea racional y eficiente, comience en la parte superior de la jerarquía de maquinaria y continúe hacia abajo. Lo mejor de este enfoque es, por lógica, que cualquier activo o componente de la maquinaria en el nivel inferior de la jerarquía no puede tener una clasificación de criticidad más alta que el activo por encima de él. En otras palabras, tan pronto como haya identificado una máquina en una de las categorías inferiores de su jerarquía donde los índices de criticidad son bajos, cualquier elemento debajo de esta máquina también debe pertenecer a la misma categoría, eliminando la necesidad de analizar su criticidad. Como puede imaginar, esto enfatiza la importancia de construir su jerarquía correctamente desde el principio.
Visualización del análisis de criticidad
Cuando se trata de establecer visualmente clasificaciones de criticidad, encontrará que hay muchas teorías sobre la mejor manera de hacerlo. Uno de los enfoques más comunes es usar una cuadrícula de 6×6, que traza la probabilidad de una falla contra la gravedad de la falla, lo que resulta en un número de prioridad de riesgo (RPN, por sus siglas en inglés).
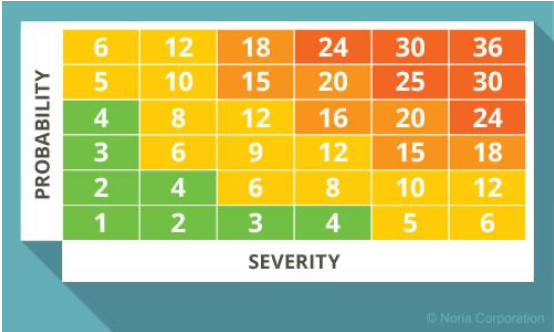
Figura 1. Definición del número de prioridad de riesgo
Quizás un enfoque más común es evaluar todas las categorías principales (operacional, salud, seguridad y medio ambiente, confiabilidad, etc.) individualmente para determinar el peor de los casos. Este tipo de análisis hará que los miembros del equipo asignen a cada consecuencia un número de riesgo, que luego se agrega o multiplica contra cada uno, dando un RPN nal. La mayoría de las organizaciones usan un puntaje de criticidad derivado de una clasificación definida de 0-6 a 0-10 para cada categoría, con un 0 que no tiene impacto y un 6 (o 10) que tiene el mayor impacto. Por ejemplo, si está calificando el riesgo de seguridad, salud e impacto ambiental de un activo, puede definir el impacto que tendría una falla basándose en lo siguiente:
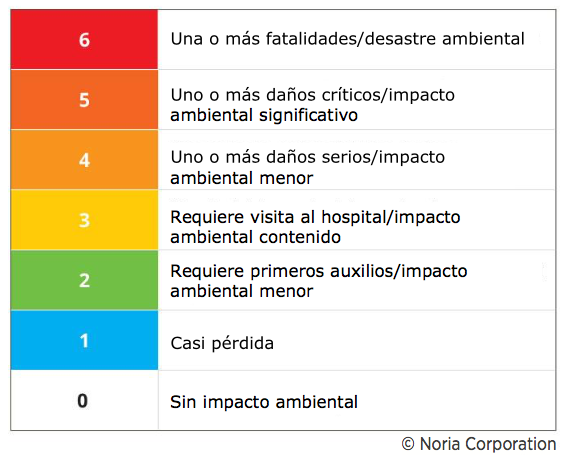
Figura 2. Clasificación del impacto de la falla
Esta forma de realizar y visualizar un análisis de criticidad debe hacerse en dos fases. La primera fase es el análisis inicial de un equipo multifuncional con aportes de operaciones; mantenimiento; adquisición de ingeniería; y medio ambiente, salud y seguridad (EH&S, por sus siglas en inglés). La segunda fase es mantener el proceso de análisis perene o mantener el proceso de análisis de criticidad durante todo el ciclo de vida del activo. Esto le ayuda a determinar cuándo se ha mitigado el riesgo o si hay algún cambio significativo con cada activo.
La creación de un elemento visual para su proceso de realizar un análisis de criticidad y determinar las calificaciones finales de criticidad se puede realizar en 10 pasos:
- Paso 1: Elija las características por las cuales desea evaluar cada activo. Estas características deben cubrir múltiples aspectos del negocio, como el impacto en los clientes, el impacto de EH&S, la capacidad de aislar y recuperarse de fallas de un solo punto, historial de mantenimiento preventivo, historial de mantenimiento correctivo, etc.
- Paso 2: Dele a cada característica una calificación usando una escala de 0 a 10 para representar la importancia para el negocio. También puede usar una escala mayor (cuanto mayor sea la escala, más fácil será identificar los activos críticos), pero la escala no debe exceder de 100.
- Paso 3: De na la descripción de cada característica en la escala para mayor precisión.
- Paso 4: En liste (o importe) su jerarquía de activos.
- Paso 5: De na la función principal de cada activo para identificar una falla de un solo punto.
- Paso 6: Analice el efecto que tendría una falla de un solo punto para cada activo en todas las características.
- Paso 7: Calcule la calificación de criticidad para cada activo dividiendo el puntaje bruto (suma de todas las características) por el total de puntos ponderados posibles, multiplicado por 100.
- Paso 8: Identifique el 10-20 por ciento superior de los activos críticos.
- Paso 9: Revise su análisis y encuentre las características que hacen que cada activo sea crítico.
- Paso 10: Finalmente, identifique los activos que son más importantes para las áreas importantes del negocio, como la confiabilidad, el costo, el valor de reemplazo, el desarrollo del plan de mantenimiento, etc.
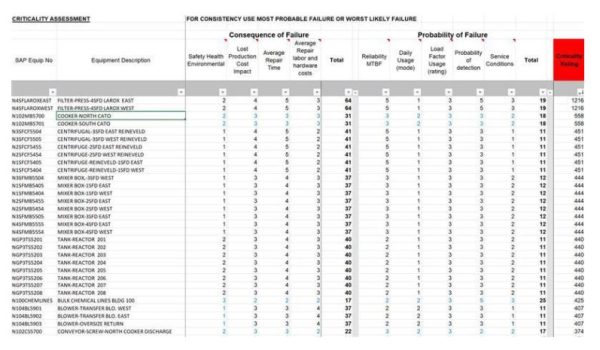
Figura 3. Ejemplo de evaluación de criticidad
Análisis de criticidad: El enfoque FMECA
El análisis de modos de falla, efectos y criticidad (FMECA, por sus siglas e inglés) fue desarrollado afines de la década de 1940 por el ejército de los Estados Unidos para pasar de un enfoque de “identificar la falla y solucionarla” a un enfoque de “anticiparse a la falla y prevenirla”. Esta metodología fue luego estandarizada y publicada como estándar militar: MIL-STD_1629A. FMECA implica un análisis cuantitativo de fallas, lo que significa que usa cantidades y números para evaluar el riesgo y el potencial de falla.
FMECA y FMEA son herramientas estrechamente relacionadas que se utilizan para realizar un análisis de criticidad; uno es una herramienta cualitativa (FMEA) que analiza escenarios de “qué pasaría si”, mientras que el otro (FMECA) es la herramienta cuantitativa que considera los RPN. Utilizando FMEA con FMECA, puede realizar un análisis de criticidad para garantizar que ciertas áreas del negocio, como el diseño, las operaciones y los costos, estén optimizados.
La parte de FMEA de este enfoque de criticidad implica definir el sistema, construir los límites del sistema y los diagramas de parámetros, identificar los modos de falla, analizar los efectos de falla, determinar las causas raíz de los modos de falla y proporcionar los resultados al equipo de diseño. La parte de FMECA incluye transferir todo lo aprendido de FMEA a FMECA, clasificar los efectos de falla por severidad, realizar cálculos de criticidad, clasificar la criticidad del modo de falla y determinar los elementos de mayor riesgo, tomar medidas para mitigar la falla y documentar el riesgo restante, y hacer un seguimiento de la efectividad de la acción correctora.
La realización de un análisis de criticidad utilizando la metodología FMECA proporciona valor en el departamento de diseño y desarrollo, operaciones y beneficios de costo, que incluyen:
- Los beneficios de diseño y desarrollo incluyen una mayor confiabilidad de los activos, mejor calidad del equipo, mayores márgenes de seguridad y una disminución en el tiempo de desarrollo y rediseño.
- Los beneficios operativos incluyen una forma más efectiva de reducir costos, programas optimizados de mantenimiento preventivo y predictivo (PdM), análisis de crecimiento de confiabilidad durante el desarrollo del producto y una disminución en los desperdicios y las actividades que no generan valor agregado o el aumento de los principios de manufactura esbelta.Los beneficios de costo incluyen la capacidad de mitigar o reconocer fallas antes de que ocurran, cuando son menos costosas de reparar, minimizan los costos de garantía y aumentan las ventas debido a la satisfacción del cliente.
Debido a que lleva bastante tiempo ponerlo en práctica, el enfoque FMECA generalmente no es el método “de referencia” para realizar un análisis de criticidad; sin embargo, algunos grupos de consultoría de confiabilidad tienen recursos para ayudarlo si su organización elige este método.
Análisis de criticidad: el resultado final
El análisis de criticidad es una gran herramienta para identificar la prioridad de las tareas de mantenimiento. Una buena manera de verlo es que la prioridad de la tarea de mantenimiento debe establecerse por el nivel de riesgo que conlleva no realizar esa tarea. Coincidentemente, este nivel de riesgo asociado con no realizar una tarea de mantenimiento en particular está determinado por las consecuencias de la falla potencial que podría ocurrir si la tarea no se completa y la probabilidad de que ocurra esa falla si la tarea no se realiza en un tiempo predeterminado.
Una vez que tenga sus clasificaciones de criticidad, un análisis de criticidad puede ayudarle a elegir una estrategia adecuada de mitigación de riesgos que pueda aplicar a cada activo. Vea el ejemplo en la figura 4.
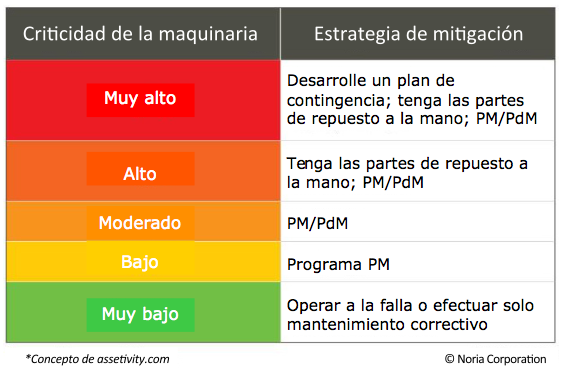
Figura 4. Estrategia de mitigación
Noria Corporation. Traducido por Roberto Trujillo Corona, Noria Latín América.