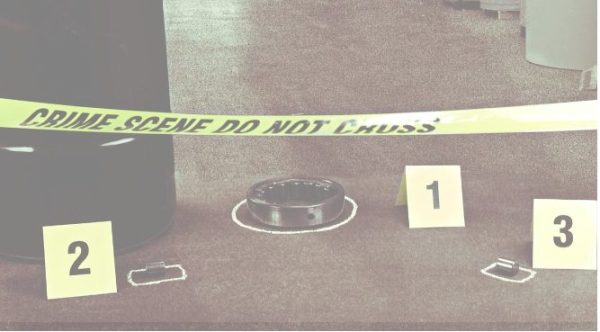
Las fallas de la maquinaria son la pesadilla de todos los departamentos de mantenimiento. Determinar su causa exacta también puede ser bastante difícil. Las fallas de maquinaria discutidas en este artículo desafiaron las soluciones rápidas y fueron bastante costosas en mano de obra, material y tiempo muerto. Varias resoluciones fueron propuestas y probadas con poco éxito hasta que se llevó a cabo un análisis cuidadoso. El enfoque sistemático que se empleó, así como los resultados que se lograron en estos tres ejemplos, deberían proporcionar una mejor idea de cómo analizar tipos similares de fallas de maquinaria en sus instalaciones.
Falla en cojinetes de respaldo
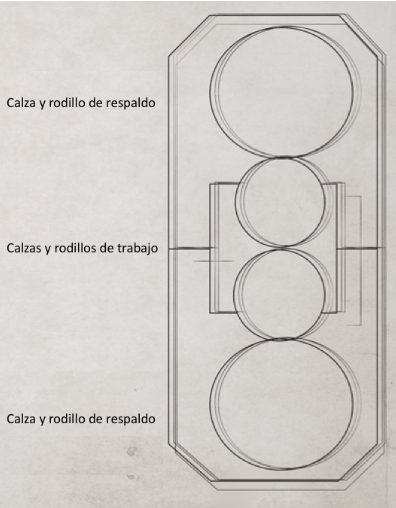
En un laminador de acero, pequeños rodillos de aproximadamente 60 centímetros de diámetro efectuan el rolado del acero para reducir su espesor. Como la calidad de la superficie es muy importante, estos rodillos se deben rectificar con frecuencia; su pequeño diámetro los hace más fáciles de manejar. Debido a esto, los rodillos de trabajo deben estar respaldados por rodillos más grandes de 90 centímetros de diámetro para evitar que se doble y distorsione el espesor de la lámina. Normalmente, los rodillos más pequeños o «de trabajo» son accionados y tienen rodamientos antifricción, mientras que los rodillos de respaldo (no accionados) tienen cojinetes con babbitt o lisos. Los rodillos de trabajo están lubricados con grasa o niebla de aceite. Los cojinetes de respaldo reciben aceite de un sistema de circulación. Los rodillos de respaldo generalmente permanecen en el molino durante varias semanas antes de requerir un rectificado. Las fallas en los cojinetes en estos rodillos son raras. La Figura 1 ilustra la disposición de los rodillos del molino.
Las fallas en los cojinetes de los rodillos de respaldo se incrementaron súbitamente en los últimos seis laminadores de acabado sin razón aparente. La gerencia del departamento culpó instantáneamente al lubricante en el sistema de circulación de aceite. Aunque cada carga de aceite nuevo fue revisada por un laboratorio para determinar su calidad, se tomaron muestras del sistema y se verificaron en un laboratorio externo para asegurarse de que no había contaminación. Cada muestra presentó resultados correctos. El aceite se compró según las especificaciones, se tomaron muestras de cada carga y se archivaron registros de varios años para demostrar que la calidad del aceite ingresado era constante. También se verificó el flujo de aceite hacia los cojinetes y se determinó que estaba dentro del objetivo.
Hasta este punto, el molino estaba perdiendo un cojinete por semana. Anteriormente, era normal perder un cojinete por año. Los costos se dispararon y parar uno de los molinos era una posibilidad real. Se efectuó una reunión con supervisores y reparadores para analizar todas las formas en que un cojinete de reserva podría fallar. La lista compilada se muestra en la tabla 1.
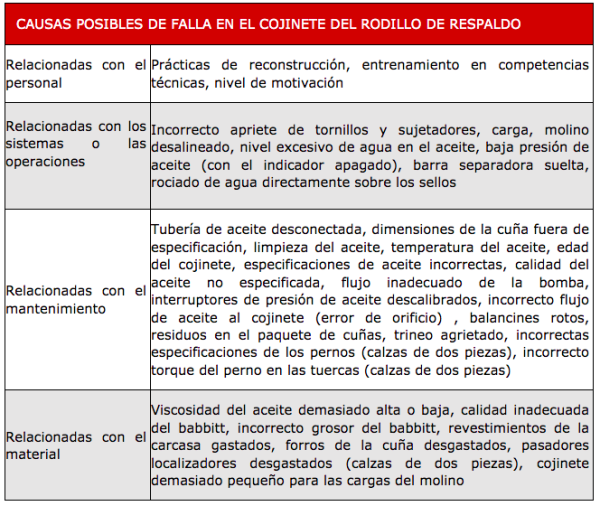
Tabla 1. Posibles causas de falla del cojinete del rodillo de respaldo
Esta lista debe ser exhaustiva, por lo que es posible que algunos puntos no se apliquen a un molino en particular. Al tratar de determinar la causa de cualquier falla de cojinete, debe concentrarse en lo que ha cambiado recientemente si el problema es de origen reciente. Algo ha cambiado, y eso posiblemente incluye prácticas actuales.
Análisis
Varios elementos de la lista se consideraron poco probables o se habían revisado recientemente, por lo que no se tomaron en cuenta. Los elementos restantes se dividieron entre todo el personal. Después de que se revisaron todos los demás elementos de la lista, se investigaron las dimensiones de la calza de cojinete. Una calza de un cojinete es una carcasa en la que se coloca el cojinete antes de colocarse en el rodillo. El orificio en el que se insertó el rodamiento tenía 90 centímetros de diámetro. Las dimensiones internas de la calza son críticas. La diferencia entre las medidas verticales y horizontales no puede exceder de 0.05 pulgadas o el cojinete no se asentará correctamente.
La ubicación de las fallas en los cojinetes era aleatoria, por lo que no se pudo identificar ningún patrón. Las pérdidas se presentaron tanto en el lado del accionamiento como en el lado del operador del molino en los seis laminadores de acabado.
El taller de reparación de cojinetes tuvo la suerte de contar con un supervisor meticuloso que registró todo en una computadora. Cada calza de cojinete estaba numerada y se guardaba un registro de dónde estaba cada una de ellas durante cualquier programa de laminación. Los registros de la computadora demostraron que cuatro calzas estuvieron involucradas en todas las fallas de los cojinetes. Esto fue sorprendente, pero la causa aún tenía que ser probada.
Las cuatro calzas se hicieron a un lado y no se usaron por un tiempo para ver qué pasaría. Todas las fallas en el cojinete cesaron. La comprobación de las dimensiones internas de estas cuatro calzas mostró un desgaste muy superior a las tolerancias para un buen asiento del cojinete. Estas calzas se enviaron de inmediato para su reconstrucción y se reanudó la vida normal de los cojinetes.
El método Kepner-Tregoe también fue útil en el análisis de los cojinetes que fallaron. En lugar de enumerar todas las causas posibles de un problema, el método de Kepner-Tregoe busca describir qué es o qué no es el problema, dónde ocurre o dónde no, cuándo ocurre o cuándo no, y su extensión. Básicamente, está construyendo una valla alrededor del problema para mantener dentro buena información y bajo consideración y fuera la mala información. Está determinando qué ha cambiado desde la condición anterior «sin problemas». La verdadera causa satisfará todas las condiciones desenterradas al usar este método. Si una condición no puede ser satisfecha por la causa sospechada, debe descartarse y considerarse otra.
Con este problema de cojinetes, las calzas desgastadas cumplieron todas las condiciones de ubicación, tiempo y capacidad de causar el problema. Ninguna de las otras causas posibles podría hacer eso. Además, colocar a un lado las calzas sospechosas equivale a cambiar solo un parámetro a la vez, lo que evita la confusión del problema.
Fallas de bomba hidráulica
En esta planta en particular, la mayoría de los sistemas hidráulicos usaban bombas de paletas. Las pérdidas fueron muy altas, y no fue necesario analizar mucho para determinar que el 80 por ciento del tiempo consumido por la bomba se estaba ocupadando en cambiar las bombas. También fue necesario aumentar el tamaño de la cuadrilla de mantenimiento para mantenerse al día con el trabajo. Se preparó un diagrama de espina de pescado que enumeró todas las posibles causas de la corta vida de la bomba (ver la tabla 2).
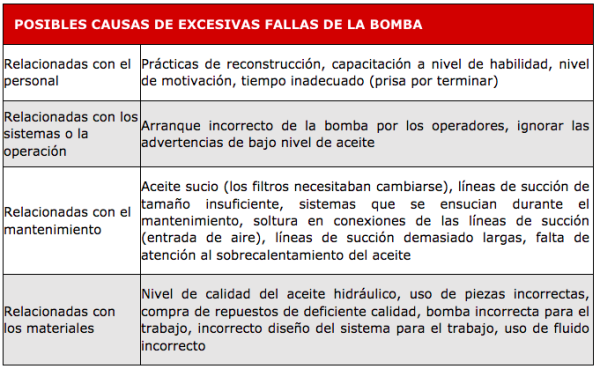
Tabla 2. Posibles causas de excesivas fallas de la bomba
Análisis
Debido a que las bombas de paletas son muy sensibles a la suciedad y las siderúrgicas están inherentemente sucias, se sospechaba que las bombas de paletas podrían no ser del tipo correcto para este entorno. Una investigación determinó que la cuadrilla de mantenimiento de las bombas estaba reconstruyendo bombas descompuestas con partes de otras bombas fuera de servicio. El fabricante de la bomba desaconsejó firmemente esta práctica e insistió en que solo se utilicen conjuntos nuevos de álabes, rotores y placas de desgaste para la reconstrucción de las unidades. Esto chocaba con esa antigua práctica en la planta.
La estrategia fue cambiar los tipos de bombas. Las bombas de engranajes son menos costosas que las bombas de paletas y son mucho más resistentes a la suciedad. También fallan gradualmente, dando una advertencia al mover los cilindros con más lentitud. Las bombas de paletas fallan repentinamente, sin previo aviso.
También se notó que todos los sistemas en la planta estaban diseñados con la bomba y el motor sobre el tanque. Cuando se arranca la bomba en este tipo de sistema, se advierte a los mecánicos que «carguen» las bombas, lo que significa que deben arrancarse y detenerse los motores al menos tres veces antes de retirarse para asegurarse de que la bomba haya alcanzado el pico. Sin embargo, los operadores a menudo encendían las bombas y no se aseguraban de hacerlo correctamente. Si la bomba no se ceba adecuadamente, el aire que ingresa a la línea de succión causará cavitación y destruirá la bomba.
Mientras el personal de la planta decidía qué hacer con esas pérdidas de las bombas, recién salían al mercado fluidos hidráulicos antidesgaste. Las compañías de lubricantes aseguraban que la vida útil de la bomba sería mayor con estos fluidos. Esta estrategia se agregó a la lista de posibles acciones.
El sobrecalentamiento del aceite también era persistente en todos los sistemas y generalmente comenzaba con un problema en el sistema de descarga. Asegurar que los enfriadores funcionaran adecuadamente ayudó, pero el diagnóstico rápido y la reparación del sistema de descarga solo trajo una mejora mínima en las pérdidas de la bomba.
Acción
Dado que parecía que las pérdidas de la bomba tenían múltiples causas, se tomó la decisión de corregir primero la causa más fácil: el fluido. El cambio a fluidos antidesgaste logró una pequeña mejora.
A continuación, se instalaron mejores filtros en cada sistema. Cambiar los filtros mensualmente se convirtió en la rutina porque no se confiaba en los indicadores de cambio de presión diferencial. Además, fue más fácil programar los cambios en el mismo turno. Esto también resultó en alguna mejora.
La práctica de «relleno con filtro» se inició entonces. Anteriormente, para llenar un sistema, los fabricantes de moldes traían un tambor de fluido al sitio e insertaban una bomba neumática en el tapón más grande de la tapa. Bombeaban aceite directamente del tambor al sistema a través de una abertura en la parte superior del tanque. Cuando el tambor estaba vacío, a menudo colocaban la bomba neumática en el piso, retiraban el tambor vacío y regresaban con un tambor lleno.
Para contrarrestar esto, se taparon herméticamente todas las aberturas en la parte superior del tanque, excepto el respiradero y un filtro enroscable conectado a una de las aberturas en el tanque. El mecánico no tuvo más remedio que conectar la manguera al filtro al llenar el tanque. Con este método, el filtro retiró toda la suciedad de la bomba y del aceite. Esto condujo a una mejor vida útil de la bomba.
Posteriormente, las bombas de paletas se cambiaron a bombas de engranajes para evitar que la cuadrilla de las bombas intentara realizar reparaciones. Cuando falla una bomba de engranajes, no se puede reparar adecuadamente, excepto en una taller especializado. La estrategia consistía en evitar que el personal poco calificado intentara hacer reparaciones. La vida útil de la bomba mejoró notablemente con esta acción.
La planta aún no estaba satisfecha y convirtió sus tanques hidráulicos en tanques verticales con las bombas montadas en un costado. Esto dio a las bombas una «cabeza positiva» y disminuyó las posibilidades de que tuvieran falta de fluido en el arranque. Este movimiento fue el más productivo de todos. La vida de la bomba aumentó tanto que la cuadrilla de bombas pensó que alguien más estaba haciendo su trabajo.
Este problema proporciona un excelente ejemplo de qué hacer cuando hay una multitud de posibles causas y se cree que todas contribuyen. Si no se puede eliminar ninguna como una posible causa, una buena estrategia es corregir primero la más fácil. Las plantas con frecuencia viven con un problema que debería haberse corregido hace años. Estos problemas de «convivencia» requieren mucho tiempo de mantenimiento y se convierten en rutina o en parte del síndrome «como hacemos las cosas aquí». Esté atento constantemente a estos problemas y elimínelos, pero solo después de un análisis adecuado.
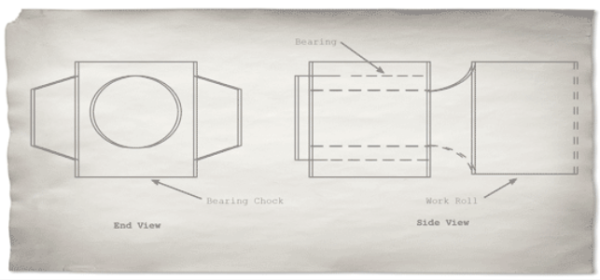
Fallas en los rodamientos del rodillo de trabajo
En el molino descrito anteriormente, los rodamientos del rodillo de trabajo eran del tipo antifricción. Un total de 40 rodamientos estaban en el laminador a la vez, y todos eran lubricados con grasa. Las características de desempeño de la grasa eran las especificadas por el fabricante y cada carga se probó al recibirla. Por lo general, se perdían de 15 a 20 rodamientos cada año, principalmente en los laminadores de acabado de mayor velocidad. Las pérdidas, que generalmente se atribuían a la edad o aspersión de agua mal direccionada y solo ocasionalmente a la grasa, se consideraban normales y difíciles de reducir. La Figura 2 ilustra el rodamiento típico.
Cuando los rodamientos de la mesa de trabajo comenzaron a fallar repentinamente en los laminadores de acabado a razón de uno por día, se preparó un diagrama de espina de pescado para enumerar las posibles formas en que podrían fallar los rodamientos (ver la tabla 3).
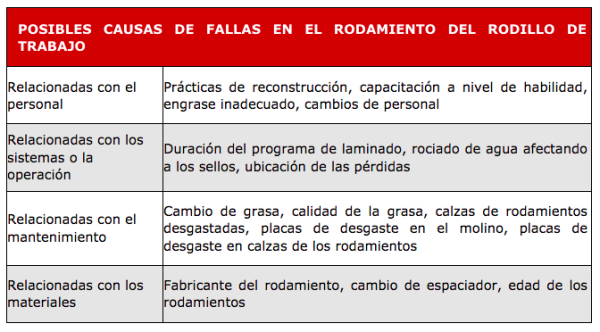
Tabla 3. Posibles causas de fallas en el rodamiento del rodillo de trabajo
La gerencia de operaciones inmediatamente culpó a la grasa. A pesar de que se tenían años de registros disponibles para confirmar la calidad de la grasa, se tomaron muestras. Todos los resultados fueron perfectos.
Cada elemento de la lista anterior se verificó o descartó debido a la verificación reciente. Solo un elemento se destacó como sospechoso: la ubicación de las pérdidas. Una investigación demostró que todas las pérdidas se habían producido en un stand en particular y solo en el lado del operador. Esto apuntó directamente a que la carcaza del laminador contribuía a las fallas. Las placas de desgaste en el interior de la carcasa del soporte, contra las que se frotaban las calzas de los rodamientos fueron revisadas y se descubrió que estaban muy gastadas. Fueron cambiadas de inmediato y las fallas pronto regresaron a los niveles normales.
Estos tres ejemplos ilustran la efectividad del uso de un diagrama de espina de pescado para garantizar que se consideren todas las causas posibles de una falla. El método Kepner-Tregoe también puede ayudar a establecer qué, dónde, cuándo y el alcance del problema.
El primer y el último ejemplo surgieron repentinamente con mucha gente entrando en pánico y sacando conclusiones. En los tres problemas, el uso de un diagrama de espina de pescado obligó al personal a retener la acción hasta que se anotaron al menos todas las causas posibles.
Los segmentos del diagrama (mantenimiento, personal, sistemas y material) son solo cuatro de las posibles áreas a evaluar. En situaciones especiales, puede haber otras. Considere todas las posibilidades con un diagrama de espina de pescado y use el método de Kepner-Tregoe para ayudar a reducir la lista. Finalmente, siempre recuerde buscar algo que ha cambiado recientemente. Este será el mejor enfoque para determinar la causa de la próxima falla de la maquinaria.
Noria Corporation. Traducido por Roberto Trujillo Corona, Noria Latín América.