El análisis elemental es una herramienta fundamental en el análisis de aceite usado. Si se usan adecuadamente, las tendencias en diferentes metales de desgaste pueden indicar un problema, lo que permite tomar medidas correctivas antes de que ocurran fallas catastróficas. Sin embargo, la efectividad del análisis elemental para identificar un problema y aislarlo a un componente específico o grupo de componentes puede mejorarse enormemente si se toma un tiempo antes de que el laboratorio informe el “desgaste activo de la máquina” para identificar la composición metalúrgica específica de todo el aceite. componentes humedecidos.
Por ejemplo, el alto contenido de cobre en una muestra de aceite podría indicar una serie de posibles problemas. Visto de forma aislada, es probable que el cobre se deba al desgaste de un componente que contenga cobre puro, como un núcleo más frío, dejando al descubierto cualquier aditivo que contenga cobre en el aceite. Sin embargo, observado junto con elementos como el estaño, zinc o aluminio, es más probable que el cobre se origine de una aleación que contiene cobre, como el latón o el bronce.
Para aprovechar al máximo los datos espectroscópicos elementales, es una buena práctica pasar un tiempo reuniendo información sobre la metalurgia de cada uno de los componentes y compilando una referencia, como la que se muestra en la Tabla 1 antes de que el laboratorio informe un problema.
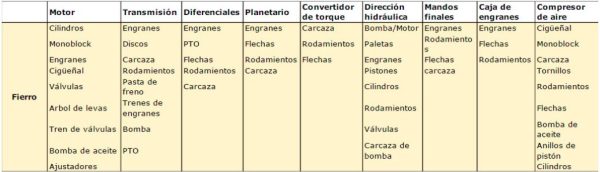
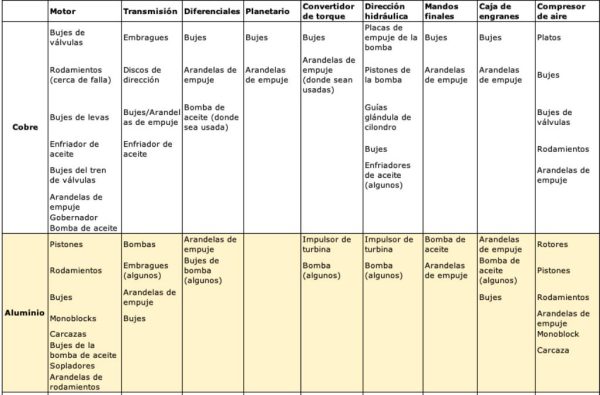
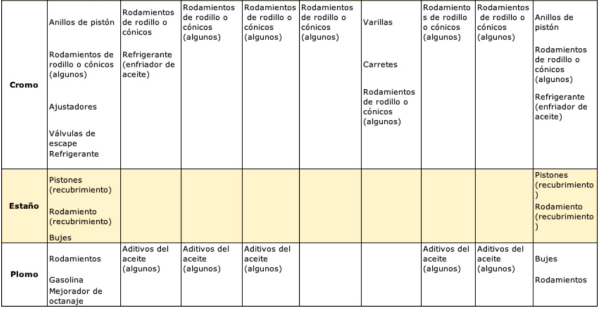
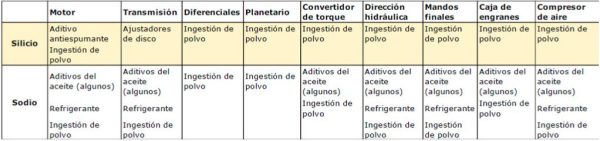
Tabla 1. Metalurgia de componentes comunes
En particular, identificar no solo elementos principales como el hierro del acero, sino también elementos menores como el cromo y el níquel, y elementos traza como el vanadio y el manganeso, puede ayudar a diferenciar entre diferentes aleaciones de acero u otros componentes.
También puede ser apropiado registrar las relaciones relativas de diferentes elementos en las diversas aleaciones presentes, de modo que estas relaciones también se puedan usar como una huella digital característica. Sin embargo, se debe tener cuidado de no tomar las relaciones exactas demasiado literalmente, porque la capacidad de los espectrómetros de plasma inductivo acoplado (ICP) y de electrodo de disco giratorio (RDE) para medir con precisión las concentraciones absolutas de ciertos elementos como el cobre y el plomo es significativamente más bajo que otros elementos como el hierro y el cromo, debido a las dificultades para vaporizar y atomizar completamente estos elementos.
David Doyle de CTC Analytical comparte un ejemplo de cómo la identificación de elementos mayores y menores permitió a una empresa de construcción aislar efectivamente un problema específico en su trituradora de cono.
Estudio de caso: análisis de residuos de desgaste de la trituradora de cono
El análisis de tendencia de las muestras de aceite que se tomaron rutinariamente en la trituradora de cono mostró un aumento constante en la cantidad de desgaste de hierro en muestras sucesivas, lo que indica un problema de desgaste activo. Cada informe de muestra fue cuidadosamente revisado por el fabricante del equipo original (OEM), quien estuvo de acuerdo con la evaluación del laboratorio de que los niveles de hierro eran excesivamente altos. Debido a que el OEM participó en la evaluación de los datos de la muestra, cada presente de desgaste de metal fue considerado cuidadosamente, al igual que los metales que no aparecieron en el análisis.
La parte desgastada a tiempo podría haber costado entre $ 2,000 y $ 12,000 en daños adicionales, y un tiempo de inactividad mínimo estimado de dos días.
En este caso, comprender la metalurgia de los componentes clave y los modos de falla típicos de este sistema, junto con el uso del análisis de aceite como herramienta de mantenimiento predictivo, permitió a la empresa de construcción evitar un problema mayor. Saber qué buscar y tener las piezas correctas a mano evitó que un problema relativamente menor se convirtiera en uno importante.
Noria Corporation. Traducido por Roberto Trujillo Corona, Noria Latín América.