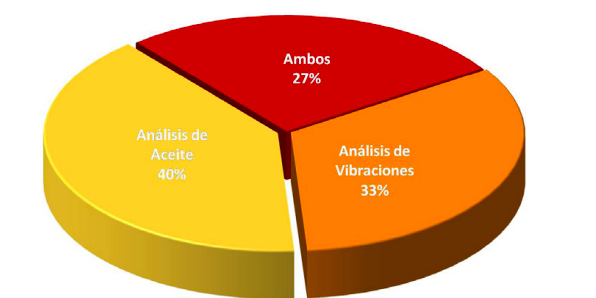
En industrias como la generación de energía y petroquímica, el análisis de vibración ha sido históricamente la técnica seleccionada para monitorear la condición de los grandes componentes críticos de equipo rotatorio. Inversamente, las compañías de transporte han confiado en el análisis de aceite para tomar efectivas decisiones de mantenimiento. Es común en industrias como las de metales primarios, papeleras, petroquímica, el uso de ambas técnicas. En general, el análisis de vibración y el análisis de aceite son las técnicas más eficientes para monitorear la salud de la maquinaria. Las dos técnicas son aliadas naturales debido a su naturaleza complementaria de sus respectivas fortalezas. Desafortunadamente, las dos técnicas raramente son combinadas para formar una efectiva unión.
La actividad típica del análisis de vibración es realizada por el grupo de monitoreo de condición, mientras que el análisis de aceite lo realiza el equipo de lubricación. Para empeorar las cosas, el programa de análisis de aceite normalmente consiste en el envío ocasional de muestras al laboratorio por resultados que más parecen de química que de monitoreo de condición. Con mucha frecuencia, el análisis de aceite es utilizado para programar los cambios de aceite mientras que las recomendaciones acerca de las condiciones del equipo son proporcionadas principalmente por el análisis de vibración.
Esto está cambiando en muchas organizaciones. Por ejemplo, la Estación de Generación Nuclear de Palo Verde en Arizona ha logrado un dramático cambio en su programa de monitoreo de condición. Ellos combinan el análisis de aceite con el análisis de vibración en un solo grupo, efectúan su análisis de aceite en sitio y trabajan como un equipo. Sus resultados han sido excepcionales. En un estudio para la determinación de fallas detectadas por tecnología, encontraron que el análisis de aceite fue responsable de la detección del 40% de las fallas, el análisis de vibración el 33% y entre ambas técnicas el 27% restante de las fallas detectadas. La pérdida de eficiencia de cada tecnología reduce su resolución de detección y su habilidad para controlar las causas de falla de la maquinaria.
En una investigación efectuada en la Universidad de Monash, en Melbourne Australia, la correlación entre el análisis de aceite y el análisis de vibración demostró ser generalmente buena. Sin embargo, hay casos donde una técnica indica una falla, mientras que la otra indica que no hay cambio o incluso un resultado contradictorio. Por ejemplo, en aplicaciones en las que el desgaste deslizante es prevalente, uno puede detectar incremento en la generación de desgaste y una disminución de los niveles de vibración. Esto es causado por lo que los investigadores han llamado un efecto de “lapeado”.
Esencialmente el desgaste deslizante pule suavemente la superficie, reduciendo las vibraciones en general hasta el punto en el cual hay demasiado espacio y se induce la vibración mecánica. El efecto es intensificado por la presencia de partículas abrasivas.
Inversamente los investigadores australianos encontraron que el análisis de vibración identifica muy eficientemente la presencia de un diente fracturado en un engrane, pero por el tamaño tan grande de las partículas de desgaste generadas, el análisis de partículas de desgaste es inefectivo. Las partículas de desgaste se precipitan hasta el fondo del tanque y nunca podrán ser recogidas en una muestra de aceite hasta que se oxiden y se disuelvan en el aceite, en un proceso que puede durar meses. Los investigadores australianos concluyeron que ambas técnicas son requeridas para un efectivo monitoreo y diagnóstico de la condición de la maquinaria en la planta, debido a que cada técnica evalúa síntomas diferentes y complementarios.
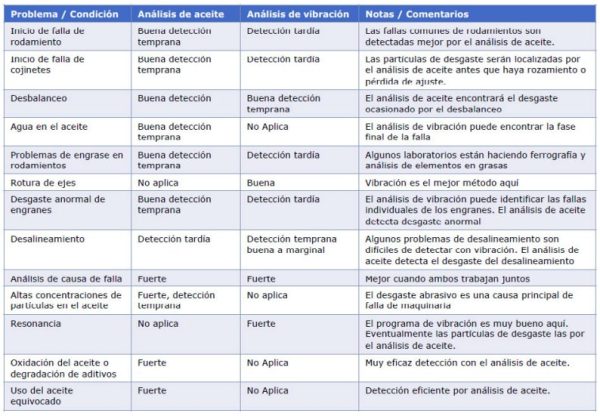
Tabla 1. Asociando el análisis de aceite y el análisis de vibración
Un ejemplo en el que ambas técnicas son requeridas para resolver efectivamente un problema es el caso de una caja de engranajes, cuando se incrementa la vibración en la frecuencia de contacto de los engranes. La inspección del conteo de partículas y del porcentaje de partículas ferrosas revela incremento en ambas categorías, mejorando la confianza en el diagnóstico de la existencia de problemas. No fue hasta que se observaron cambios en la tendencia en la viscosidad que la real naturaleza del problema fue detectada. Se observó una reducción en la viscosidad de 220 cSt a 40 °C a 70 cSt a 40 °C. Una revisión de la bitácora mostró que el aceite fue cambiado hacía dos semanas. Con toda seguridad, el cambio de aceite fue efectuado con un aceite equivocado, provocando el desgaste y la vibración. Sin la combinación de las tecnologías de monitoreo de condición, la causa de falla no habría sido detectada. En general, podemos sacar las siguientes conclusiones acerca de la combinación del análisis de aceite y el análisis de vibración en la detección y análisis de las fallas en la maquinaria:
- Ambas técnicas son requeridas para el control de las causas de falla de la maquinaria.
- Frecuentemente, una técnica sirve como indicador inicial de la falla de la maquinaria mientras que la otra sirve como un indicador de confirmación.
- El análisis de aceite es generalmente más fuerte en la detección de fallas en cajas de engranajes, sistemas hidráulicos y equipo reciprocante.
- El análisis de vibración es generalmente más fuerte en la detección en sistemas de cojinetes de alta velocidad.
- El análisis de vibración es frecuentemente mejor para localizar el punto de falla dependiendo de la aplicación.
- El análisis de aceite es frecuentemente más fuerte en determinar el mecanismo de desgaste que induce la falla.
- Ambas técnicas son requeridas para determinar efectivamente la causa de falla.
- La correlación entre el análisis de aceite y el análisis de vibración es muy buena, pero hay circunstancias contrarias.
En conclusión, el análisis de aceite y el análisis de vibración son aliados naturales en el logro de la confiabilidad de la maquinaria. Frecuentemente ofrecen sus fortalezas complementarias en el control de las causas de falla de la maquinaria y en la identificación y comprensión de la naturaleza de las condiciones anormales. El éxito depende de efectuar cambios en las organizaciones para poner el desarrollo del monitoreo de condición y el diagnóstico en manos de los especialistas de la tecnología. Necesitamos seleccionar las herramientas adecuadas en nuestra bolsa para completar nuestro trabajo de asegurar la confiabilidad de la maquinaria.
Noria Corporation. Traducido por Roberto Trujillo Corona, Noria Latín América.