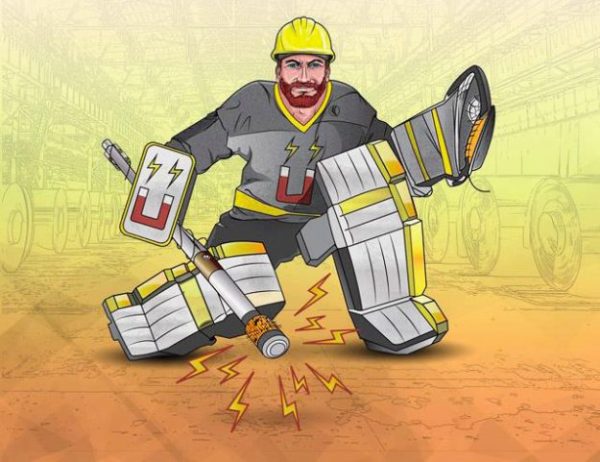
Los componentes lubricados fallan por diversas razones, las cuales se pueden clasificar en función del tipo de falla, específicamente en fallas tempranas, fallas aleatorias o dependientes de eventos y fallas basadas en la condición.
Un evento de falla temprana puede ser el resultado de una lubricación inadecuada. Cuando un sistema está en reposo, a menos que el rodamiento tenga lubricación hidrostática aplicada, las superficies deslizantes estarán en contacto.
A medida que los componentes comienzan a girar, las superficies permanecen en contacto hasta que se forma la película lubricante. Durante este tiempo, persiste la mayor incidencia de falla. Conforme se forma una película y los aditivos tensoactivos comienzan a proteger, se establece un régimen de lubricación. Antes de que esto ocurra, las asperezas de la superficie y las partículas contribuirán al desgaste de la superficie y la posible falla del componente.
Cuando hay un desbalanceo o tolerancias no uniformes entre las superficies de las piezas, o se utilizan materiales o componentes incorrectos, existe la posibilidad de un desgaste prematuro. Las malas prácticas de mantenimiento, mano de obra e instalación pueden conducir a un evento de falla temprana. Varias partículas pueden indicar estos escenarios.
Otra clase de falla es la aleatoria o dependiente de un evento. Estos tipos de fallas pueden ocurrir en cualquier momento durante el ciclo de vida del sistema. Son causadas por exceso de velocidad o por sobrecargar un componente. A medida que aumentan la velocidad y la carga, existe la posibilidad de que las superficies de deslizamiento o rodadura entren en contacto y generen calor, así como también que las partículas entren en contacto con las superficies. En ambas situaciones, las superficies y las partículas producen desgaste.
Las fallas basadas en la condición se deben principalmente a la contaminación, generada tanto internamente por partículas de desgaste (normales o aceleradas) como por fuentes externas, como suciedad o producto del proceso. La contaminación también puede ser líquida o gaseosa. Los gases, como el sulfuro de hidrógeno u oxígeno puro, pueden producir corrosión severa, que genera partículas de desgaste. Los líquidos como el combustible y los refrigerantes contribuirán a fallas del sistema en los motores de combustión interna.
El agua es el contaminante que con más frecuencia causa la oxidación del metal y la degradación de lubricante en sistemas lubricados por aceite. Estos fluidos comprometen la viscosidad del aceite, lo que da como resultado el contacto con la superficie o desarrollo de oxidación. Esto lleva a un aumento en la probabilidad de falla.
Cuando ocurre una falla temprana
Cada activo tiene una vida útil. A menudo no es hasta que ocurre una falla prematura que se producirá una investigación a fondo. Si la culpa es por lubricación inadecuada, defectos en los componentes o malas prácticas de mantenimiento, el análisis de aceite de rutina combinado con el análisis de partículas de desgaste puede indicar una falla en proceso.
Aunque no es realista realizar un análisis de partículas de desgaste en cada activo, es razonable analizar regularmente los activos críticos para detectar partículas de desgaste. También se recomienda realizar un análisis de partículas de desgaste al comenzar un programa de análisis de aceite. Esto ayudará a establecer qué activos pueden ser más vulnerables a fallas.
Cuándo realizar un análisis de partículas de desgaste
El lubricante puede proporcionar información sobre lo que ocurre dentro de un sistema sin tener que desmontar e inspeccionar la maquinaria. Antes de extraer una muestra de aceite para el análisis de partículas de desgaste, es prudente considerar el sobrecalentamiento, la vibración y la alta presión del sistema. Estos pueden indicar si el aceite debe analizarse en busca de partículas de desgaste.
Una vez que se analiza una muestra de aceite, ciertos indicadores alentarán el uso del análisis de partículas de desgaste. La primera indicación será un aumento en el desgaste de metales como el hierro, el aluminio y el cobre. En seguida, verifique si ha habido un aumento en el índice cuantificador de partículas (PQI, por sus siglaseninglés).ElPQIesunapruebaque mide la distorsión de un campo magnético aplicado a una muestra de aceite mientras está dentro de la botella y se utiliza para cuantificar las partículas ferrosas en la muestra. Es beneficioso cuando se utiliza junto con la concentración de metal de desgaste. La prueba tiene limitaciones, ya que no mide metales no ferrosos, y una sola partícula grande se lee como muchas partículas más pequeñas. Cuando el PQI es más bajo que los niveles de hierro, es probable que no haya partículas mayores de 10 micrones.
Si el PQI aumenta dramáticamente mientras los niveles de hierro permanecen constantes o disminuyen, puede haber partículas ferrosas más grandes. Esta tendencia creciente indica que debe efectuar una ferrografía o análisis de partículas de desgaste.
Análisis de partículas de desgaste
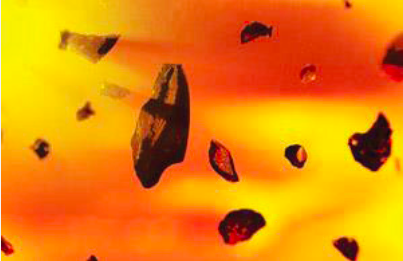
La ferrografía puede ser de lectura directa o analítica. En la ferrografía de lectura directa, un sensor magnético mide partículas ferrosas de hasta 200 micrones. Los resultados se informan en DS (partículas chicas, menores de 5 micrones) y DL (partículas grandes, mayores de 5 micrones). La relación entre los dos indica la gravedad del desgaste.
La ferrografía de lectura directa es excelente para llevar la tendencia de las partículas de desgaste ferroso y a menudo se usa como una herramienta de detección para la ferrografía analítica, que explora la forma y el tamaño de las partículas capturadas.
La medición de partículas se expresa como un valor o índice de concentración de partículas de desgaste (WPC, por sus siglas en inglés) sin unidades y un porcentaje de partículas pequeñas a grandes. Si aumenta la proporción de partículas grandes (DL) contra las partículas pequeñas (DS), sugiere una mayor generación de partículas grandes.
En la ferrografía analítica, se produce una placa con la ayuda de imanes para separar las partículas de desgaste y organizarlas según el tamaño. Se usa un microscopio para identificar el tipo de desgaste generado con base en la forma y el tamaño de la partícula.
La muestra de aceite se diluye para mejorar el flujo por la placa de vidrio (portaobjetos). La placa descansa sobre un cilindro magnético, que atrae las partículas ferrosas, las cuales se alinean, quedando depositadas las partículas más grandes en el punto de entrada. Las partículas no ferrosas fluyen hacia abajo y se depositan al azar. Se agrega solvente a la muestra restante. Después de que el solvente se evapora, quedan solamente las partículas en el porta objetos. Posteriormente se analiza la placa por un técnico capacitado.
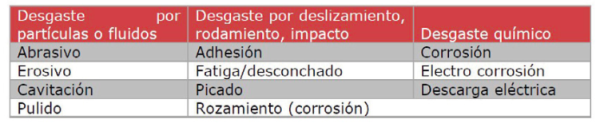
Tabla 1. Tres categorías de partículas de desgaste
Hay tres categorías principales de partículas de desgaste: desgaste por fluidos o partículas, desgaste por deslizamiento/rodamiento/impacto y desgaste químico. La Tabla 1 resume estas categorías y enumera los mecanismos de cada una.
Otros artículos de interés: https://noria.mx/lublearn/determinacion-de-hierro-en-muestras-de- aceite/
Noria Corporation. Traducido por Roberto Trujillo Corona, Noria Latín América.