El mayor enemigo de la lubricación es la contaminación, especialmente los contaminantes sólidos como las partículas de tierra. Una vez que la contaminación ingresa al aceite, se convierte en un factor crucial para la falla del lubricante y, en última instancia, la falla de la máquina. Un programa de confiabilidad sólido no estaría completo sin un plan de acción para ayudar a minimizar la contaminación en los lubricantes.
Si bien todas las máquinas lubricadas son propensas a las trampas de la contaminación, los sistemas hidráulicos son de particular interés, ya que experimentan condiciones de operación únicas y a menudo requieren componentes que son inherentemente sensibles a los contaminantes.
La forma en que los contaminantes afectan la confiabilidad de los sistemas hidráulicos ha sido el foco de cientos de estudios durante las últimas décadas. Para una breve historia de la participación crucial de Ernest C. Fitch y comprender la influencia de la contaminación en los sistemas hidráulicos, consulte la figura 2.
Hoy en día, los fabricantes de sistemas hidráulicos y los usuarios finales son más conscientes de la sensibilidad a los contaminantes de los componentes de la máquina. Sin embargo, mientras que el “por qué” se ha expresado y discutido abiertamente, el “cómo” no se entiende tan ampliamente. Esto no solo incluiría cómo reducir los contaminantes en el sistema sino también cuánto.
En los sistemas hidráulicos, las medidas proactivas de control de la contaminación de fluidos, tanto la exclusión como la eliminación de contaminantes, requieren una inversión que va más allá del equipo. Un enfoque optimizado normalmente incluye una combinación de ambos.
Dado que la exclusión es la primera línea de defensa casi siempre es más rentable mantener los contaminantes fuera que eliminarlos después de que estén en el aceite. Se ha estimado que cuesta al menos 10 veces más eliminar un gramo de suciedad de lo que costaría excluirlo en primer lugar.
Un principio por considerar es el estado óptimo de referencia (ORS, por sus siglas en inglés), donde cada decisión de lubricación se esfuerza en la optimización considerando todos los factores relevantes, como el costo, la seguridad, el tiempo de inactividad, la sensibilidad de los componentes, etc. Este principio puede aplicarse también en el contexto del control de la contaminación. Por un lado, podría ser que invierta excesivamente en prácticas de filtración para garantizar que las máquinas se mantengan limpias.
Por otro lado, podría intentar ahorrar dinero sin invertir en el control de la contaminación, pero el resultado probablemente sería operaciones poco confiables y eventualmente una parada prematura e inesperada. El objetivo debería ser invertir la cantidad correcta en el control de la contaminación para optimizar el retorno de la inversión.
¿Qué tan limpio?
¿Qué tan limpios deben estar sus sistemas? Debe decidir cuáles son sus motivos. ¿Cuál es el historial de fallas del sistema? ¿La consecuencia del tiempo de paro es demasiado grande? Esta es una decisión de mantenimiento estratégica. En teoría, está intentando minimizar el efecto neto entre la inversión y los ahorros correlacionados de una mayor confiabilidad.
En otras palabras, el costo invertido en la limpieza del aceite debe ser tal que cualquier inversión mayor o menor aumentaría el efecto neto general. En realidad, esta cantidad exacta es imposible de precisar, pero con algunas consideraciones de los factores conocidos, puede determinar un nivel de limpieza requerido con cierta confianza en los beneficios.
En algunos casos, es posible que los beneficios del aceite más limpio no superen los medios, pero para la gran mayoría, la falla de estas máquinas implica demasiado riesgo para no invertir en algún nivel de control de la contaminación. En este caso, se puede calcular el nivel requerido de limpieza del aceite.
La culminación de esta cuestión del nivel de limpieza por parte de la industria ha dado lugar a muchos métodos a lo largo de los años, uno de los cuales se describe en la norma ISO 12669. A continuación se ofrece una descripción más detallada de este método junto con las opciones sobre cómo implementarlo mejor.
Nivel de limpieza requerido
Como se mencionó anteriormente, no es realista suponer que alguien pueda “limpiar el aceite” hasta el punto en que se eliminen todos los contaminantes. Cada paso de limpieza requiere un mayor costo de mantenimiento, ya sea con mejores equipos o más tiempo y mano de obra. Entonces, antes de comenzar a trabajar en una dirección, debe establecer un objetivo para optimizar los costos. Este objetivo es el nivel de limpieza requerido (RCL, por sus siglas en inglés).
El RCL se deriva de un cálculo que involucra varios factores, incluidos los componentes de la máquina, las condiciones de funcionamiento y las influencias ambientales, entre otros. La Figura 1 muestra la gráfica resultante entre la suma calculada de los factores contribuyentes y el RCL representado usando el código de limpieza ISO 4406.
Para aquellos que no están familiarizados con el código de limpieza, los tres números de rango, como 15/13/10, corresponden al número de contaminantes mayores de 4, 6 y 14 micrones, respectivamente.
La suma calculada de los factores contribuyentes se conoce como peso total. Estos factores, seis en total, tienen cada uno su propia tabla de ponderación y se resumen a continuación.
Presión de trabajo y ciclo de trabajo: Esta escala, de 1 a 8, no solo se define por el rango de presión de trabajo sino también por el nivel de inconsistencia que experimenta la presión del sistema durante el funcionamiento. Cuanto más constante y baja sea la presión, menor será el número. Cuanto mayor sea la presión y su variación, mayor será el número.
Sensibilidad a los contaminantes de los componentes: Esta escala, del 1 al 8, analiza los tipos de componentes a los que está expuesto el fluido hidráulico. Los componentes más sensibles, como válvulas y bombas, deben ser la consideración principal. Por ejemplo, una servoválvula de alto desempeño garantizará un factor de peso más alto debido a la posibilidad de que los contaminantes atasquen el carrete contra el bloque de válvulas debido a los diferenciales de holgura y presión.
Expectativa de vida del sistema: Esta escala, de 1 a 5, requiere un tiempo de ciclo de vida esperado (en horas) del sistema hidráulico. Cuanto más tiempo se espere que el sistema permanezca en servicio, mayor será el control de la contaminación. Si se permite perpetuamente que la contaminación significativa permanezca en el sistema durante un período prolongado de tiempo, el grado de daño que puede causar es mayor.
Costo total de reemplazo de componentes: Esta escala, de 1 a 4, toma en consideración los tipos de componentes en el sistema, principalmente por la cantidad de mano de obra y el costo que tomaría reemplazarlos. Los componentes más grandes y los sistemas más complejos generalmente justifican un factor de peso más alto.
Costo del tiempo de inactividad: Esta escala, de 1 a 4, depende del impacto general del equipo en la producción. Puede que sea la consideración más intuitiva. Si la producción no se ve afectada por el componente, entonces el factor de peso permanece bajo. Cuanto mayor sea la interrupción de la producción y los costos generales de inactividad causados por una falla del sistema, mayor será el factor de peso.
Riesgo: Esta escala, de 1 a 6, es similar en consideración al costo del tiempo de inactividad, pero en lugar de un riesgo de producción, es un riesgo de seguridad. Esto está asociado a peligros potenciales que podrían crearse para las personas en el área circundante como resultado de una falla del sistema. (Aunque la norma ISO 12669 no enumera explícitamente el impacto ambiental como un factor, se sugiere que este factor de riesgo también tenga en cuenta el medio ambiente).
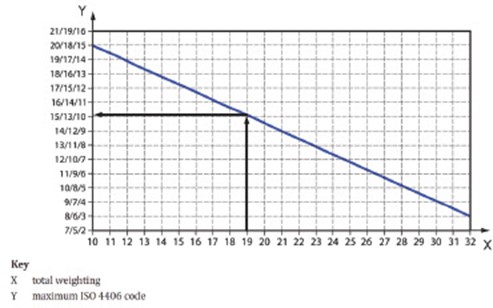
Figura 1. Gráfico resultante entre la suma calculada de
factores contribuyentes y el RCL representado usando el código de limpieza ISO 4406
Una vez que se han determinado las ponderaciones para las seis categorías, todos los factores contribuyentes se pueden sumar a un solo número. Luego, este número puede correlacionarse con un código de contaminación ISO como objetivo para el RCL del sistema hidráulico. En general, este enfoque debería ser apropiado para la mayoría de las aplicaciones.
Sin embargo, sigue siendo una guía, no una regla estricta y rápida, especialmente cuando el RCL se encuentra en los extremos de la escala donde los códigos de contaminación ISO son altos (por encima de 20) o bajos (por debajo de 10).
Si el RCL calculado sugiere 20/18/15 como el objetivo para el sistema, el aceite entrante podría estar más limpio que este nivel, en cuyo caso no hacer nada para limpiar el aceite puede ser aceptable. Si el aceite es considerablemente más limpio que el objetivo, valdría la pena mantener el aceite a este nivel en lugar de permitir que se contamine más. Después de todo, el costo de mantener los contaminantes fuera del aceite puede ser solo alrededor del 10 por ciento en comparación con lo que se necesita para filtrarlos.
Por otro lado, si el RCL calculado es extremadamente bajo, como 10/8/5 o menos, requerirá más que solo filtración para lograr el objetivo. Esto puede no ser realista dado el entorno de su máquina. Como se indicó anteriormente, se debe minimizar el efecto neto tanto de la inversión en aceite más limpio como de la rentabilidad de los beneficios.
Entendiendo ISO 12669
ISO 12669 está diseñado para sistemas hidráulicos, aunque la estrategia esencial se puede adaptar para su aplicación en otros sistemas lubricados. Esta norma revisa la necesidad de establecer objetivos únicamente sobre los niveles de contaminación de partículas sólidas, por lo tanto, no incluye una consideración de nivel objetivo de limpieza para insolubles suaves, agua o cualquier otro contaminante. La norma también está destinada a proporcionar consideraciones de limpieza de fluidos para los requisitos de lavado inicial, proceso de fabricación, montaje, puesta en servicio y requisitos de filtrado operativo.
Cuando las consideraciones de los componentes son relevantes para calcular el RCL, el fabricante del componente puede ofrecer recomendaciones sobre las sensibilidades de la máquina y los factores de peso del RCL sugeridos. Del mismo modo, los fabricantes de filtros pueden dar recomendaciones sobre los factores de peso de RCL cuando hayan desarrollado evidencia que correlacione los métodos de filtración y las aplicaciones del sistema hidráulico.
Las pruebas de sensibilidad a los contaminantes para componentes se originaron a partir de estudios realizados en el Centro de Investigación de Fluidos de Potencia de la Universidad Estatal de Oklahoma en la década de 1970. Estos estudios, junto con una encuesta del Departamento de Comercio e Industria (DTI, por sus siglas en inglés) del Reino Unido, ayudaron a enfatizar la importancia de la filtración de fluido hidráulico como una estrategia más eficaz para prolongar la vida útil de los componentes.
A finales de la década de 1990, el comité técnico de control de contaminación de la Asociación Británica de Fluidos de Potencia fue fundamental en el desarrollo de métodos iniciales para determinar el RCL. Esto influyó en los factores de peso concluyentes aplicados en la norma ISO 12669 actual.
Mantenimiento proactivo en tres sencillos pasos
El aceite más limpio prolonga la vida útil de sus máquinas al mantener las zonas de fricción menos expuestas a los efectos peligrosos de los contaminantes. Cuando el esfuerzo para lograr esto se optimiza cuidadosamente, el retorno de la inversión puede ser una ventaja significativa, incluso una ventaja competitiva. La creación de este objetivo de RCL es solo el primer paso de una estrategia completa de control de contaminación de mantenimiento proactivo. Los siguientes son los tres pasos:
- Establezca el objetivo de limpieza. Esto puede determinarse a través de la experiencia y optimizarse con una metodología como la que se describe en ISO 12669 junto con el estado óptimo de referencia. En última instancia, el objetivo debe reflejar sus objetivos de confiabilidad.
- Tomar acciones específicas para lograr estos objetivos a través de un enfoque doble, reduciendo el ingreso y mejorando la filtración. Reducir la entrada es más rentable, pero no es una solución independiente perfecta. Combinar esto con una filtración mejorada es necesario para cualquier aplicación crítica.
- Mida los niveles de contaminantes con frecuencia mediante análisis de aceite. Como dice el refrán, lo que se mide se hace. Conocer el historial de contaminación es vital para un programa sostenible. Los niveles de contaminación son un indicador adelantado, mientras que las tasas de desgaste y fallas son un indicador rezagado. Las medidas proactivas se pueden justificar y reforzar con más datos para validar la causa y el efecto. Se recomienda que este tipo de resultados se publiquen abiertamente para que todos los involucrados los comprendan.
Pionero de los fluidos de potencia
El Dr. Ernest C. Fitch (1924-2011), también conocido como “Bucko”, comenzó su participación en la energía fluida a principios de la década de 1950 cuando comenzó el programa académico de energía fluida en la Universidad Estatal de Oklahoma. Este tema se convirtió en el foco de su carrera. En 1956 y en la década de 1960, la NASA y la Fuerza Aérea de los Estados Unidos le otorgaron contratos importantes en investigación de fluidos de potencia para estudiar los efectos de los contaminantes e investigar métodos de prueba de control de contaminación para sistemas hidráulicos.
Durante las décadas siguientes, sus contribuciones se convirtieron en la piedra angular de una industria que rápidamente se vio revolucionada por los beneficios del control de la contaminación. Continuó su investigación líder en la industria durante más de 30 años, participó en muchos comités de estándares y fue autor de varios libros y más de 200 artículos técnicos.
Su Centro de Investigación de Fluidos de Potencia proporcionó la investigación para muchas normas ISO que se utilizan hoy en día en esta industria, incluidas las de contadores de partículas, Tasa Beta de filtración y procedimientos de muestreo de fluidos hidráulicos y aceites lubricantes, por nombrar solo algunos. Puede encontrar un relato extenso de su vida en MachineryLubrication.com .
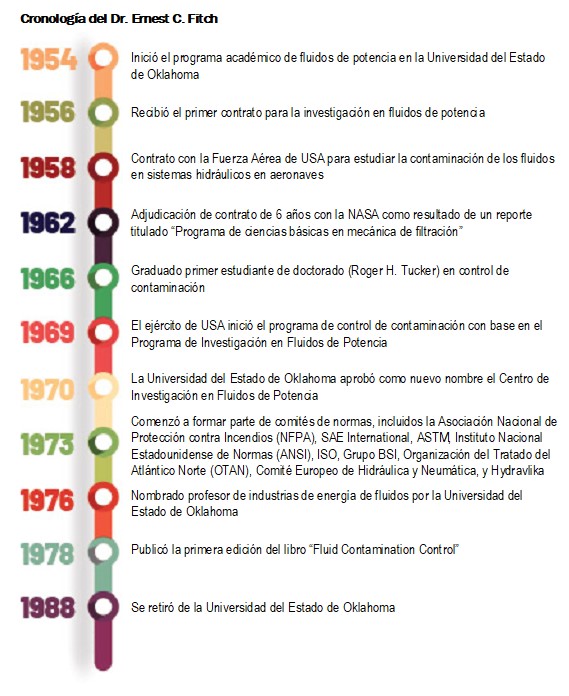
Noria Corporation. Traducido por Roberto Trujillo Corona, Noria Latín América.