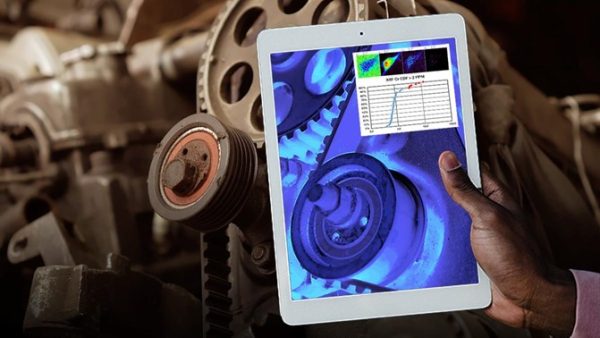
Este artículo informa datos de análisis de aceite de motores diésel, que demuestran el uso del filtrograma con fluorescencia de rayos X para cuantificar la severidad del desgaste y la contaminación. Se realizaron dos mediciones independientes en cada muestra de filtrograma: Conteo de partículas por bloqueo de poro y análisis de elementos de partículas grandes por fluorescencia de rayos X (XRF, por sus siglas en inglés). El análisis de las distribuciones acumulativas según ASTM D7720 indica umbrales de severidad para el análisis de metales de desgaste por XRF.
¿Qué puede esperar aprender?
- El cuantificador de partículas por filtrograma (FPQ)determina el conteo de partículas y el código ISO para partículas de desgaste acumuladas en un filtrograma de > 4 micrones.
- La fluorescencia de rayos X (XRF)reporta el análisis de elementos de las partículas de desgaste en cada muestra de filtrograma.
- La determinación de la severidad del desgaste y la contaminaciónrequiere el análisis de partículas de desgaste de más de 4 micrones, incluidos Fe, Cr, Ni, Cu, Sn, Pb, Al y Si, además del conteo de partículas.
- Las muestras de filtrogramaretienen las partículas de desgaste si es necesario para futuras referencias, eliminación de fallas y análisis de causa raíz de fallas (RFCA).
Introducción
Esta presentación demuestra el uso de fluorescencia de rayos X con filtrograma según ASTM D8127 para cuantificar el desgaste anormal originado en aleaciones de hierro, aleaciones de metales blancos y aleaciones de metales amarillos en una población de 52 muestras de aceite de motor diésel en servicio. Estas muestras de aceite en servicio se analizaron con extractos de un proceso de conteo de partículas por bloqueo de poro y partículas de más de 4 micrones retenidas en la muestra del filtrograma. Cada filtrograma se analiza de forma no destructiva con fluorescencia de rayos X de dispersión de energía (XRF) para evaluar la composición de elementos, incluidos hierro (Fe), cromo (Cr), níquel (Ni), cobre (Cu), plomo (Pb) y estaño (Sn) para cuantificar el desgaste anormal de cientos de componentes móviles del motor en cada muestra de aceite de motor.
El análisis del aceite de motor se centra ampliamente en la espectrometría de emisión óptica (OES) para medir Fe, Cr, Ni, Cu, Pb, Sn y Si para cuantificar el desgaste anormal y la contaminación. Sin embargo, la limitación del tamaño de partículas de moleculares a ultrafinas para OES opaca su efectividad para distinguir el desgaste anormal de los componentes y la contaminación por polvo en el aceite de motor por lo siguiente: 1) existen numerosos tamaños de partículas que van de unos cuantos micrones a algunos milímetros y que varían de fuentes normales o benignas de estos siete elementos, y 2) el desgaste severo y las partículas de contaminación por polvo suelen ser más grandes que el rango de medición de OES.
OES detecta estos siete elementos en el aceite de motor provenientes de muchas fuentes dentro de su rango de medición. Por ejemplo, “el aumento de la concentración de cobre puede alcanzar más de 300 ppm”.
Por alarmante que parezca, se ha informado que el sulfuro de cobre, incluso en estas altas concentraciones, es generalmente benigno y, como tal, puede no estar asociado (causa o efecto) con fallas del enfriador, desgaste acelerado u oxidación del lubricante. El cobre que se encuentra en los aceites para motores diésel puede provenir de una amplia variedad de fuentes y puede existir en el aceite en distintos estados.
Desde la perspectiva del analista de lubricantes, determinar la fuente, la naturaleza y el estado del cobre es esencial para interpretar correctamente la alarma, en términos de confiabilidad del motor y la respuesta adecuada. Aunque es muy valioso, el análisis de elementos por OES tiene una capacidad limitada y, de hecho, “puede producir falsas alarmas o enmascarar alarmas reales a menos que se realicen simultáneamente otras pruebas de excepción”.
El cuantificador de partículas por filtrograma con fluorescencia de rayos X (FPQ XRF) realiza un conteo de partículas por bloqueo de poro, seguido de un análisis multielementos por fluorescencia de rayos X de energía dispersiva, según ASTM D7684, ASTM D8127 e ISO 21018-3. Las Figuras 1 y 2 muestran el cuantificador de partículas por filtrograma (FPQ) con un área activa en la membrana del filtro de 4 micrones donde se acumulan las partículas de desgaste. Se etiqueta la muestra de FPQ, se realiza un análisis de elementos XRF y se conserva la muestra para un examen visual y microscópico.
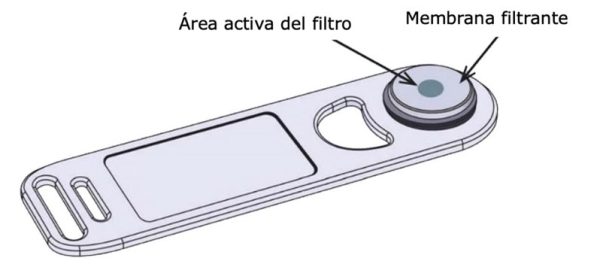
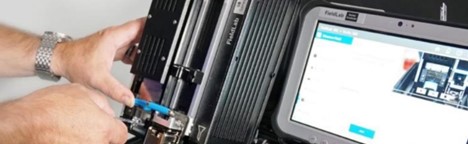
La Figura 3 describe el proceso de dos pasos para extraer partículas mayores de 4 micrones de muestras de aceite en servicio y analizar la composición de elementos de las partículas depositadas en el área activa del filtro.
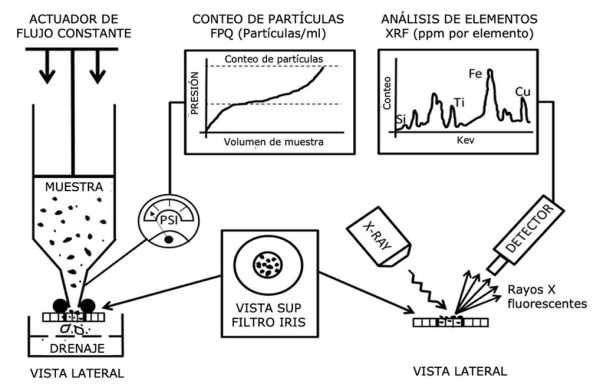
Las ventajas de este proceso de 2 pasos incluyen:
Método rápido sin disolventes:
- Sin dilución ni preparación de muestras para digestión ácida.
- Adecuado para condiciones de campo.
- Presentación de partículas repetible y consistente con volumen medido para el cálculo de la concentración de ppm.
Datos potentes para la detección de desgaste avanzado:
- Resultado de la medición del conteo de partículas.
- La prueba XRF no destructiva informa 16 elementos (ppm): Fe, Ag, Al, Cr, Cu, Ni, Pb, Si, Sn, Ti, Mo, Co, Mg, W, V y Zn.
- Se conserva la muestra con partículas disponibles para futuras investigaciones.
- Se correlaciona con otras técnicas de partículas grandes.
Partículas de desgaste severo
El deslizamiento severo, la fatiga por rodadura y la fatiga por flexión son mecanismos de falla que acortan exponencialmente la vida funcional de los componentes de la máquina. El daño de cada mecanismo es acumulativo y progresivo.
Las partículas de desgaste de cada uno de estos mecanismos contienen evidencia sobre el componente dañado, el daño causado y la etapa o severidad del progreso de la falla. El desgaste normal, el desgaste severo, avanzado y catastrófico presentado en la Figura 4, representa niveles de severidad crecientes.
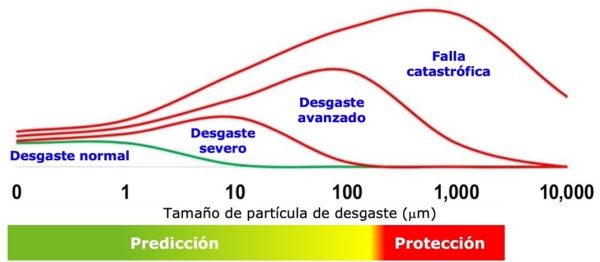
La abrasión, adhesión y fatiga anormales (Figura 5) son partículas de desgaste grandes en los metales base, no solo en los óxidos.
- Las partículas de micropitting varían entre 10 mm y 50 mm.
- Las partículas laminares y trozos varían desde 50 mm hasta varios cientos de micrones.
- La espectrometría de emisión óptica no ve partículas grandes.
El cuantificador de partículas por filtrograma mide el conteo de partículas y el código ISO para partículas sólidas acumuladas en una membrana filtrante de 4 micrones. Esto incluye las etapas importantes de desgaste severo y desgaste avanzado que conducen a partículas de desgaste por falla catastrófica, con rangos de tamaño que se muestran en la Figura 4. Observe que el rango para la predicción de una falla catastrófica inminente requiere medir las partículas de desgaste en el rango de tamaño del punto ciego de OES entre 4 micrones a 2 milímetros.
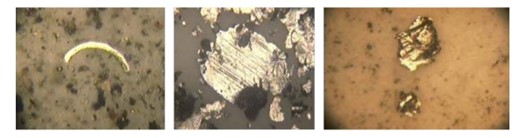
Límites de severidad para datos FPQ XRF y OES
Se analizó una población de 52 muestras de aceite de motor en servicio con XRF y OES. Se utilizaron las distribuciones acumulativas por ASTM D7720 que se muestran en la Figura 6 para seleccionar los límites de severidad preliminares. Los límites de severidad preliminares de XRF para Fe, Cr y Ni cuantifican el desgaste anormal de cilindros, anillos de pistón, engranajes, ejes, ruedas de distribución, cadenas de distribución, empujadores de válvulas, guías, cigüeñal, árbol de levas, eje de balancín, pasadores de pistón, rodamientos de rodillos y bombas de aceite.
Además, los límites de severidad de XRF preliminares para Cu, Sn, Pb y Al cuantifican las superficies de rodadura de los cojinetes de biela, el eje del balancín y los cojinetes del pasador del pistón; y Si cuantifica el polvo en el aire de admisión. Los límites de severidad de OES utilizados aquí son límites de alarma estándar aceptados en la industria.
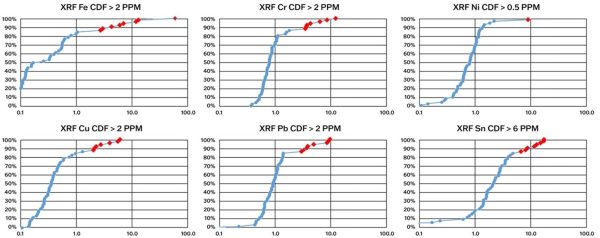
La Tabla 1 reporta los límites de severidad preliminares para XRF basados en distribuciones acumulativas dentro de los límites aceptados por la industria para mediciones de OES.
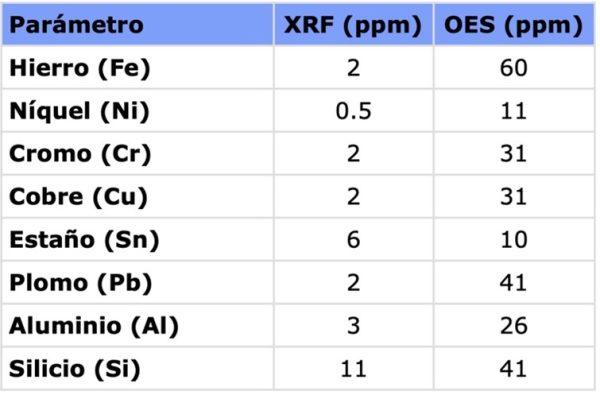
Los valores de parámetros alarmantes basados en estos límites se resaltan en las Tablas 1 y 2. Las muestras están numeradas del #1 al #52, en orden, según la medición de Fe por XRF de mayor a menor. Los valores alarmantes de los parámetros de desgaste de metal se muestran resaltados para las muestras #1 a #9. No hay parámetros alarmantes para las muestras #10 a #52.
Los resultados de XRF muestran una clasificación de severidad alta para las muestras #1 a #7 según múltiples parámetros de aleaciones ferrosas (Fe, Cr y Ni) y aleaciones no ferrosas (Cu, Pb, Sn, Al). Además, XRF muestra una alta severidad para la muestra #8 basada en Fe y está respaldada por Cr elevado. Finalmente, la muestra #9 tiene una severidad alta basada en Sn, respaldada por Pb elevado.
Los resultados de OES muestran Fe y Al alarmantes para las muestras #2 y #5.
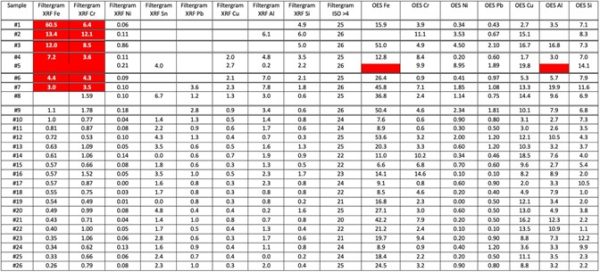
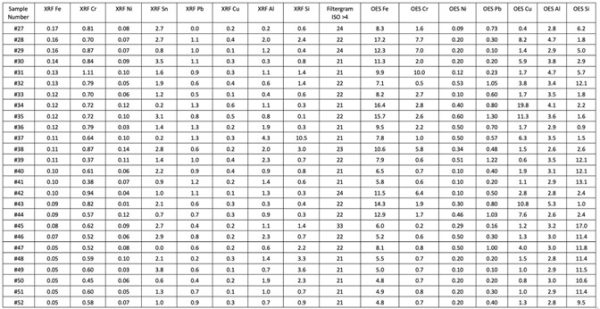
Los gráficos de la Figura 7 resumen las mediciones de ppm de las Tablas 2 y 3 y muestran aleaciones ferrosas y no ferrosas para todas las muestras #1 a #52.
El gráfico XRF de la izquierda muestra ppm para partículas de desgaste mayores de 4 micrones acumuladas en el filtrograma. Las muestras #1 a #8 tienen aleaciones ferrosas severas, las muestras #1, #2 y #3 tienen severa aleación de metales blandos blancos y amarillos, las muestras #4, #5, #6, #7 y #9 tienen severa aleación de metal blando blanco.
El gráfico OES de la derecha muestra ppm para sustancias y partículas disueltas menores de 4 micrones. En este gráfico, las muestras #2 y #4 destacan por tener alto Fe y Al, pero el resto parece ruido.
Una distinción muy importante a observar en la Tabla 2 y la Figura 5 es la capacidad de detectar y cuantificar el desgaste anormal en aleaciones de metales blandos.
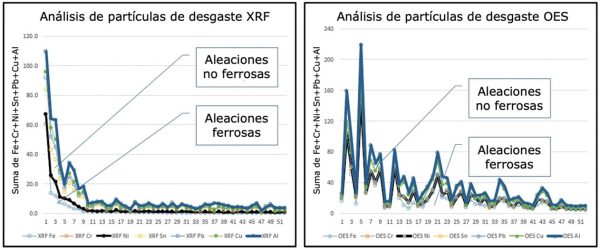
Esta tabla muestra el análisis de partículas de desgaste grandes de múltiples elementos. La Figura 8 identifica componentes críticos de maquinaria rotativa con necesidades similares para monitorear aleaciones ferrosas, aleaciones de metal blanco y aleaciones de metal amarillo.
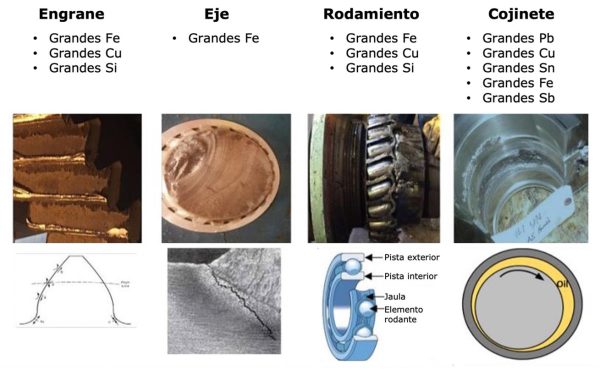
Análisis de fallas de causa raíz
La ferrografía analítica, la espectrometría de filtro Rotrode (RFS, por sus siglas en inglés), la microscopía electrónica de barrido (SEM, por sus siglas en inglés) y la digestión ácida son los métodos estándar para el análisis de partículas de desgaste ferrosas y no ferrosas de aceite en servicio en el punto ciego de OES (mayores de 4 micrones hasta un rango de 2 milímetros). Ocasionalmente, uno de estos métodos que requieren mucho tiempo se utiliza con una justificación especial, como por ejemplo para un análisis de causa raíz de fallas (RCA, por sus siglas en inglés).
Las muestras de los filtrogramas (Figura 9) se conservan y están disponibles para:
- Nueva prueba y comparación
- Análisis microscópico de partículas de desgaste.
- Investigación futura
- Ejemplo de historia de caso, y
- Eliminación de fallas
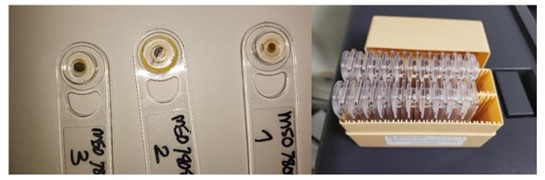
Fuentes:
- Jim Fitch, “Copper and Your Diesel Engine Oils”, Revista Practicing Oil Analysis, Septiembre 2004.
- Ray Garvey, “Severe Sliding and Fatigue Wear Debris Analysis for Machinery Components”, Spectro Scientific Blog, Septiembre 2022.
- Steffen Bots, “How to Set Elemental Limit Values for Motor Oils”, Revista Machinery Lubrication, Octubre 2015.