Esta es la quinta entrega de la serie de lecciones de “anatomía” en lubricación de maquinaria. En esta ocasión, no vamos a disecar algún dispositivo u objeto sino más bien vamos a analizar el contenido proporcionado en un reporte de análisis de lubricantes típico, incluyendo cómo interpretar los resultados y otras recomendaciones. Esta interpretación puede ser la diferencia entre el costo de una falla y el paro de una máquina y el poder evitarla.
La interpretación de un reporte de análisis de lubricante puede resultar muy abrumadora para un ojo inexperto. El análisis de lubricantes no es económico, ni tampoco la máquina de la cual el análisis revela la información. Cada año, las plantas pagan millones de dólares a laboratorios comerciales para analizar muestras de lubricantes nuevos y usados. Desafortunadamente, la gran mayoría del personal de la planta que recibe los resultados del laboratorio no conoce los principios fundamentales para interpretarlos adecuadamente.
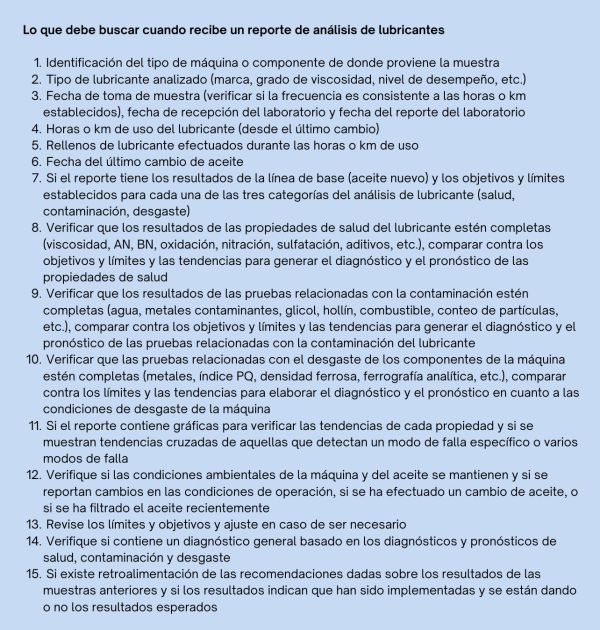
La gran mayoría de los reportes de análisis del lubricante traen una sección con un resumen escrito donde colocan las recomendaciones en términos sencillos. Sin embargo, dado que el laboratorio nunca ha visto la máquina ni conoce su historia completa, estas recomendaciones son genéricas y no se ajustan a las condiciones individuales de cada máquina. De ahí que es responsabilidad del personal de la planta que recibe los resultados del laboratorio el tomar sus propias acciones basadas en los conocimientos que tiene de la máquina, del ambiente y de las tareas de lubricación recientemente realizadas.
Por qué hacer análisis de lubricantes
Una razón obvia para hacer un análisis de lubricante es para conocer su condición, pero al mismo tiempo se desea conocer la condición de la máquina desde la última toma de muestra. Hay tres categorías del análisis del lubricante: salud (propiedades del fluido), contaminación y desgaste.
Salud (propiedades del fluido)
Este tipo de análisis se enfoca en identificar las condiciones físicas y químicas del lubricante, así como estimar su vida útil remanente (RUL, por sus siglas en inglés). Está diseñado para dar respuestas a preguntas como:
- ¿Coincide la muestra con el aceite especificado?
- ¿Es correcto el aceite utilizado?
- ¿Están los aditivos activos y son los correctos?
- ¿Se han agotado los aditivos?
- ¿Ha cambiado la viscosidad con respecto a la esperada? Si es así, ¿por qué?
- ¿Cuál es la vida útil remanente del lubricante (RUL)?
Contaminación
Detectando la presencia de contaminantes destructivos y localizando sus posibles fuentes (externas o internas), el análisis de lubricantes ayuda a responder preguntas tales como:
- ¿Está el aceite limpio?
- ¿Qué tipo de contaminantes hay presentes en el lubricante?
- ¿De dónde provienen los contaminantes?
- ¿Hay síntomas de contaminación con otro tipo de lubricante?
- ¿Hay alguna indicación de fugas internas?
Desgaste
Esta categoría del análisis del lubricante es usada para determinar la presencia e identificación de las partículas producidas como resultado del desgaste mecánico, la corrosión u otro tipo de degradación de la superficie. Responde a una serie de preguntas relacionadas con el desgaste, incluyendo:
- ¿Se está degradando anormalmente la máquina?
- ¿Se están produciendo partículas de desgaste?
- ¿De cuál componente interno de la máquina es probable que se esté originando el desgaste?
- ¿Cuál es el modo de desgaste y qué lo está causando?
- ¿Qué tan severo es el desgaste?
En última instancia, usted necesita saber si se han tomado acciones para mantener la máquina saludable y extender la vida útil del lubricante. El análisis del lubricante de una máquina puede ser comparado con el análisis de sangre del cuerpo humano. Cuando un doctor extrae una muestra de sangre, la coloca en una serie de máquinas analizadoras, cuidadosamente estudia los resultados y reporta sus conclusiones basado en su conocimiento, en investigación y en preguntas detalladas hechas al paciente. Del mismo modo, en el análisis del lubricante se toman muestras cuidadosamente y máquinas sofisticadas producen los resultados de las pruebas. El personal del laboratorio interpreta los resultados en la medida de sus posibilidades, pero sin detalles importantes sobre la máquina, por lo que el diagnóstico y el pronóstico pueden ser potencialmente inexactos. Algunos de estos detalles importantesson:
- Las condiciones ambientales de la máquina (temperaturas extremas, elevada humedad, vibración excesiva, etc.)
- El tipo de máquina (turbina de vapor, bomba, etc.), marca y modelo
- Tipo de lubricante usado
- Número de identificación del componente y la ubicación exacta del puerto de muestreo
- Los procedimientos de muestreo correctos para asegurar una toma de muestra consistente y representativa
- Cambios de lubricante y rellenos, así como la cantidad de rellenos desde la fecha del último cambio
- El uso de carros de filtración en el intervalo de la toma de muestras
- Horas totales de operación de la máquina o componente, desde su fecha de adquisición o desde la última reparación mayor
- Tiempo de uso del lubricante desde el último cambio
- Cualquier otra actividad inusual o que valga la pena destacar realizada sobre la máquina, que pueda causar cambios en el lubricante
Pruebas del análisis del lubricante
Para una máquina estándar incluida en un programa normal de análisis de lubricantes, el paquete de pruebas estaría constituido básicamente por pruebas de “rutina”. Alternativamente, en caso de requerir pruebas adicionales para resolver problemas no detectados con las pruebas de rutina, se tendrían que considerar las pruebas de “excepción”. Las pruebas de rutina varían de acuerdo al tipo de máquina y las condiciones ambientales, y por lo general siempre incluyen las pruebas de viscosidad, análisis de elementos metálicos (espectrométrico), humedad, conteo de partículas, infrarrojo por transformadas de Fourier (FTIR) y número ácido (AN). Otras pruebas basadas en el tipo de máquina incluyen ferrografía analítica, densidad ferrosa, demulsibilidad y número básico (BN).

Tabla 1. Pruebas más utilizadas en cada una de las tres categorías del análisis del lubricante
Viscosidad
Existen varios métodos para determinar la viscosidad de los lubricantes, la cual se reporta en términos de viscosidad absoluta o cinemática. La mayoría de los lubricantes industriales se clasifican por grados de viscosidad de acuerdo con la norma ISO 3448. Esto no implica que un grado ISO VG 320, tenga exactamente 320 centiStokes (cSt). De acuerdo con dicho estándar, cada lubricante se considera que corresponde a un grado de viscosidad determinado si su viscosidad cae dentro de un rango de más/menos 10 por ciento de la viscosidad media de dicho grado (típicamente la del grado ISO VG).
32%
de los profesionales de la lubricación no saben cómo interpretar un reporte de análisis de lubricantes, basado en una encuesta realizada en machinerylubrication.com
La viscosidad es la característica más importante de un lubricante. El monitoreo de la viscosidad es un elemento crítico porque cualquier cambio puede ser el síntoma de otros problemas, tales como oxidación, contaminación con glicol o estrés térmico.
Valores altos o bajos de viscosidad pueden ser ocasionados por un lubricante incorrecto, corte mecánico del lubricante y/o del mejorador del índice de viscosidad, oxidación del lubricante, contaminación con anticongelante, o con combustible, refrigerante o con un solvente.
El establecimiento de límites para los cambios de viscosidad depende del tipo de lubricante analizado. Sin embargo, se establece un límite de advertencia de 10 por ciento y un límite crítico de 20 por ciento por encima o por debajo del valor obtenido de la línea de base del lubricante nuevo.
Número ácido y número básico
Las pruebas de número ácido y número básico son similares, pero se utilizan para caracterizar diferentes tipos de lubricantes y aspectos relacionados con los contaminantes. En un análisis del lubricante, el número ácido representa la concentración de sustancias ácidas en el lubricante, mientras que el número básico representa la reserva alcalina del lubricante. Los resultados de ambas pruebas se expresan en términos de la cantidad de hidróxido de potasio en miligramos que se requieren para neutralizar los ácidos en un gramo de lubricante. La prueba de número ácido es usada principalmente en lubricantes no usados en motores de combustión interna (turbinas, compresores, engranajes –industriales y automotrices-, sistemas hidráulicos, bombas, etc.), mientras que el número básico se utiliza principalmente en lubricantes para motores de combustión interna.
Un número ácido demasiado alto o demasiado bajo puede ser el resultado de la oxidación del lubricante, de la presencia de un lubricante incorrecto o del agotamiento de los aditivos. Un número básico muy bajo puede originarse por un elevado paso de gases de combustión al cárter del motor (combustible, hollín, etc.), la presencia de un lubricante incorrecto, fugas internas de contaminantes (glicol) o por un intervalo de cambio de lubricante extendido y/o por elevadas temperaturas.
Infrarrojo por transformadas de Fourier (FTIR)
FTIR es una prueba rápida y sofisticada para determinar algunos parámetros, incluyendo contaminación con combustible, agua, glicol y hollín; también detecta productos de la degradación del lubricante como compuestos de oxidación, nitración y sulfatación; así como la presencia de aditivos como el dialquil ditiofosfato de cinc (ZDDP) y fenoles. El equipo infrarrojo reconoce cada una de estas características midiendo los cambios en la absorción de la luz infrarroja en rangos o numeroso longitudes de onda específicos. Muchos de los parámetros observados pueden no ser concluyentes, por lo que a menudo estos resultados son corroborados con otras pruebas para dar un mayor apoyo a los resultados. En la Tabla 2 se muestran los parámetros identificados por cambios en la absorbancia de luz infrarroja a diferentes números o longitudes de onda.
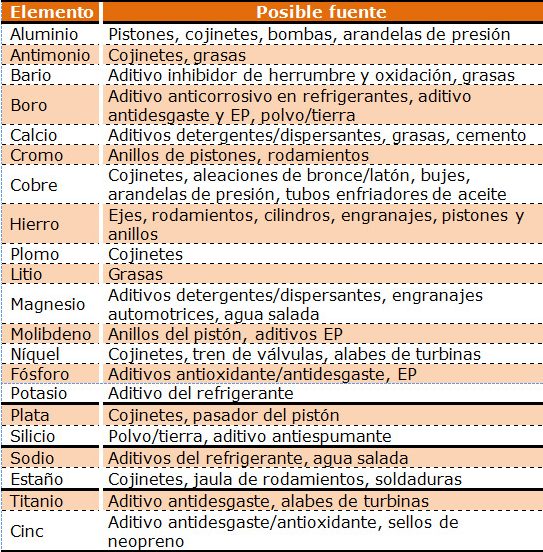
Tabla 2. Números de onda específicos por tipo de parámetro determinado por FTIR
Análisis de elementos metálicos
El análisis de elementos metálicos trabaja bajo el principio de la espectrometría de emisión atómica (AES, por sus siglas en inglés), a veces llamada análisis de metales de desgaste. Está diseñada para determinar la concentración de metales de desgaste, contaminantes y aditivos en el lubricante. Dos de las tecnologías de espectrometría de emisión atómica son las de electrodo de disco rotatorio (RDE – chispa) y la plasma inductivamente acoplada (ICP). Ambas tienen limitaciones en cuanto al tamaño de partícula. Para el RDE el tamaño de partícula está limitado a menos de 8 a 10 micrones, mientras que para el ICP el tamaño de partícula es de menos de 3 micrones. Sin embargo, son muy útiles porque se pueden llevar tendencias con sus resultados. En la Tabla 3 se presentan las fuentes más comunes de metales en el lubricante.
La mejor forma de monitorear estos resultados en determinando primero qué se espera encontrar en el lubricante. Un efectivo reporte de análisis del lubricante proporciona datos de referencia del lubricante nuevo (línea de base), de manera tal que los metales de los aditivos pueden ser fácilmente distinguidos de los metales de los contaminantes. Además, debido a que varios elementos metálicos pueden ser encontrados en alguna proporción (por ejemplo contaminantes en ciertos ambientes operacionales), es mejor analizar las tendencias en lugar de enfocarse en la medición de algún elemento específico en los resultados del análisis de metales.
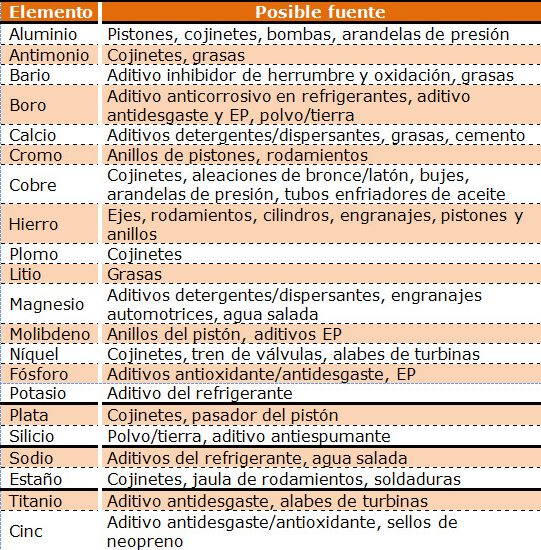
Tabla 3. Fuentes más comunes de metales en el lubricante
Conteo de partículas
El conteo de partículas mide el tamaño y la cantidad de partículas en el lubricante. Existen varias metodologías para evaluar el contenido de partículas, típicamente reportado con el estándar ISO 4406:99. Este consta de tres números separados por una diagonal y cada número se correlaciona con el conteo de partículas mayores de 4, 6 y 14 micrones. Para ver una ilustración de cómo se asignan los códigos de limpieza ISO en función de la cantidad de partículas determinadas en cada rango, lea este artículo ¿Qué tan importante es el código de contaminación sólida ISO 4406:99?
Análisis de humedad (agua)
El contenido de humedad (agua)en una muestra de lubricante se determina normalmente con la prueba de titulación Karl Fischer. Los resultados se reportan en partes por millón (ppm), aunque a menudo se indican en porcentaje. Este método determina el contenido de agua en sus tres formas: disuelta, libre y emulsionada. La prueba de crepitación y de la plancha caliente son pruebas no instrumentales de discriminación que se realizan antes de ejecutar la prueba de Karl Fischer. Resultados altos o bajos de agua pueden ser causados por ingresión a través de escotillas o respiradores abiertos, condensación interna por cambios de temperatura o fugas por los sellos.
Interpretando el reporte de análisis de lubricantes
Lo primero que hay que verificar en un reporte de análisis de lubricantes es la información concerniente al cliente, el tipo de máquina y/o componente y el lubricante, en la parte superior del reporte (Fig. 1). La inclusión de estos datos es responsabilidad del cliente. Sin esta información, la efectividad del reporte se verá disminuida. Conocer la máquina de donde fue tomada la muestra de lubricante repercute en la capacidad para identificar las fuentes potenciales de las propiedades evaluadas, especialmente las partículas de desgaste. Por ejemplo, el tipo de máquina ayuda a asociar las partículas de desgaste reportadas con ciertos componentes internos. La información del lubricante nuevo proporciona una línea de base para algunas de las propiedades, como el grado de viscosidad esperado, los aditivos activos y los valores de los números ácido/básico. Estos detalles pueden parecer sencillos, pero normalmente son olvidados o ilegibles en la etiqueta de identificación de la muestra o en el formato de requisición.
Fig. 1- Encabezado de un reporte de análisis de lubricante
Otra sección del reporte de análisis del lubricante presenta información relacionada con el lubricante y la muestra aportada por el cliente, como por ejemplo el fabricante del lubricante, la marca, el grado de viscosidad y el intervalo de servicio (horas/km), así como si el lubricante fue cambiado y si se han efectuado rellenos. Estos datos son importantes, ya que proporcionan una explicación para lo que podrían ser falsos positivos cuando se presenten resultados alarmantes.
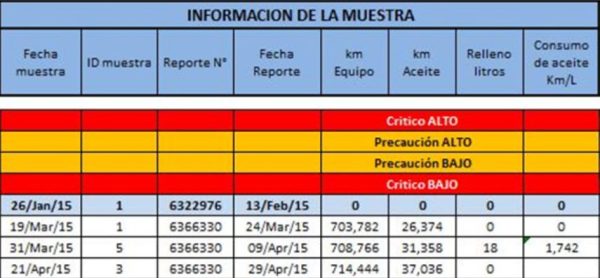
Fig. 2- Información de la muestra
En la sección de “pruebas físicas y químicas” del reporte se ofrecen detalles de la viscosidad del lubricante a 40 y 100°C, índice de viscosidad, así como el número ácido, el número básico y oxidación, nitración y sulfatación por FTIR. Para lubricantes industriales, la viscosidad es medida a 40°C, para así clasificarla dentro del grado de viscosidad ISO VG correspondiente. La viscosidad de los aceites de motor es medida a 100°C, para así clasificarla dentro del grado de viscosidad SAE correspondiente. Si se requiere calcular el índice de viscosidad, por ejemplo de un aceite de motor, se le debe determinar la viscosidad a 40°C. Los números ácido y básico deben ser tomados como referencia para determinar cualquier cambio en sus tendencias. Estos son unos de los mejores indicadores de la degradación del lubricante, que deben ser tomados en cuenta para determinar rápidamente si se debe cambiar inmediatamente o programar el cambio del lubricante.
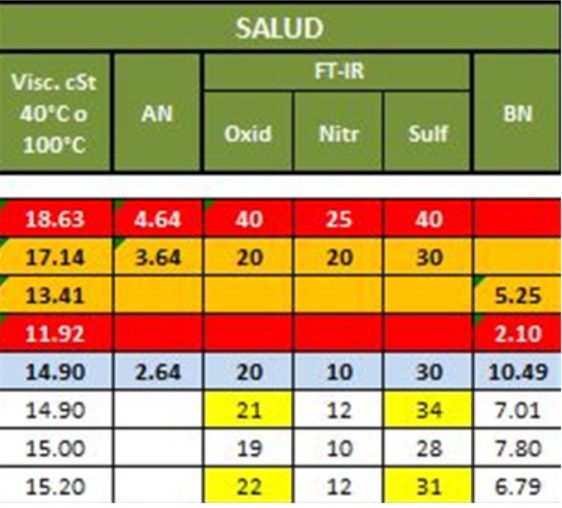
Fig. 3 – Resultados de la salud del lubricante
Luego viene la sección de contaminantes (Fig. 4), donde además de los elementos metálicos se muestran los resultados de agua, hollín, glicol, combustible y conteo de partículas. Para cada uno de ellos se utilizan pruebas específicas como agua por crepitación, Karl Fischer o FTIR, hollín y glicol por FTIR, combustible por FTIR o Fuel Sniffer, y conteo de partículas de acuerdo con el estándar ISO 4406:99. Los límites y alarmas en estas propiedades van a depender del tipo de máquina y de lubricante.
En la siguiente sección del reporte del análisis del lubricante (Fig. 4) se examinan los resultados de los elementos metálicos. Estos resultados ayudan a identificar metales de contaminantes, de desgaste y de aditivos presentes en el lubricante. Estos se reportan en partes por millón (ppm). Sin embargo, esto no significa que una contaminación con partículas, por ejemplo, puede sólo ser indicada por incrementos en sodio, potasio o silicio. En el ejemplo, el incremento en silicio y aluminio podría potencialmente indicar una contaminación con polvo/tierra como la causa raíz del problema. Una probable explicación de estos incrementos es que el polvo (silicio) ingresa en el lubricante desde una fuente externa, ocasionado abrasión de tres cuerpos en la máquina, produciendo incrementos en partículas de desgaste de aluminio, hierro y níquel.
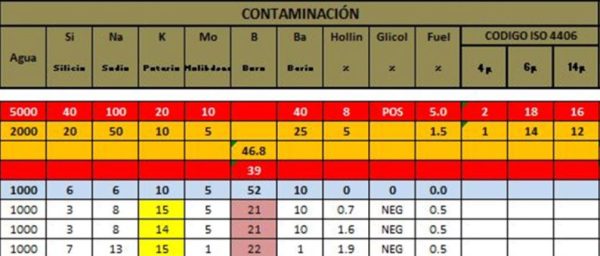
Fig. 4 – Resultados de contaminación del lubricante
Conociendo la metalurgia de los componentes de la máquina, cualquier incremento en los metales de desgaste puede ser correlacionado para llegar a la conclusión de cuál de los componentes de la máquina está experimentado dicho desgaste. Tenga presente para el análisis de la tendencia es importante que la muestra sea tomada con la frecuencia adecuada y sin interrupciones.
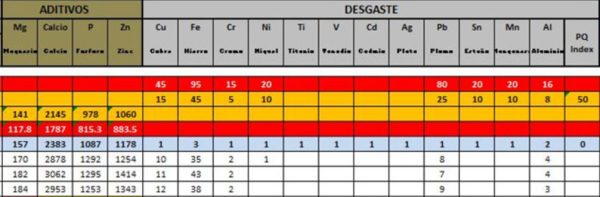
Fig. 5 – Análisis de elementos metálicos (Ref. Noria Latin America)
Además de los resultados que se muestran en todo el reporte de análisis del lubricante, los gráficos pueden ayudar a ilustrar las tendencias de dichos resultados (Fig. 6). En estos gráficos se muestran ejemplos de tendencias obtenidos de los resultados analizados. Junto a dichos gráficos se deben mostrar los promedios típicos, los límites normales y de advertencia. Estos límites deben ser modificados dependiendo de los resultados obtenidos, del tipo de lubricante y de las condiciones de operación de la máquina.
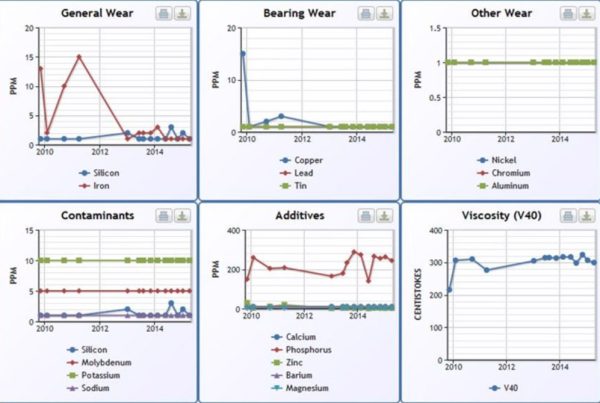
Fig. 6 – Los gráficos en un reporte de análisis de lubricante ayudan a ilustrar las tendencias de los resultados (Ref. Analyst)
Con los resultados de los elementos relacionados con los contaminantes y el desgaste, se establecen las alarmas por incrementos en las tendencias de los resultados. Para los elementos relacionados con los aditivos, se establecen las alarmas por tendencias a la baja. Tener la línea de base del lubricante nuevo como referencia es esencial para determinar el tipo de aditivo y su concentración. Esta línea de base es establecida para determinar cualquier reducción significativa que se presente con los aditivos.
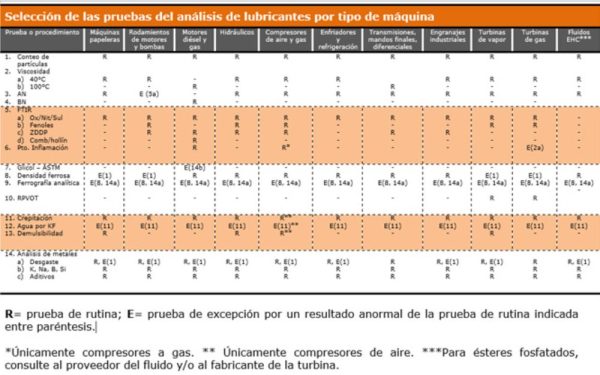
Fig. 7 – Selección de las pruebas del análisis de lubricante por tipo de máquina
La última sección del reporte de análisis del lubricante generalmente proporciona el diagnóstico y el pronóstico en cada una de las tres categorías del análisis del lubricante y las recomendaciones proactivas y preventivas, para que se mantengan las condiciones y frecuencias de muestreo si el escenario es normal con tendencia estable o para devolver a la máquina y al lubricante a un escenario normal si los resultados indican un escenario anormal con variación moderada o rápida. Estas recomendaciones son colocadas manualmente por el personal del laboratorio que interpreta los resultados y están basadas en la información suministrada por el cliente y los resultados obtenidos en el laboratorio. Si hay que dar alguna explicación de los resultados que se derivan de alguna situación no comentada por el cliente, los resultados deben ser reinterpretados por un consultor experto (Fig. 8) o por personal del cliente que esté familiarizado con el historial de la máquina respecto a sus condiciones de operación y el ambiente operacional. Comprender la información suministrada en esta parte del reporte es de suma importancia. Recuerde, siempre habrá una explicación cuando se haya excedido algún límite, y se debe investigar la causa raíz del mismo.
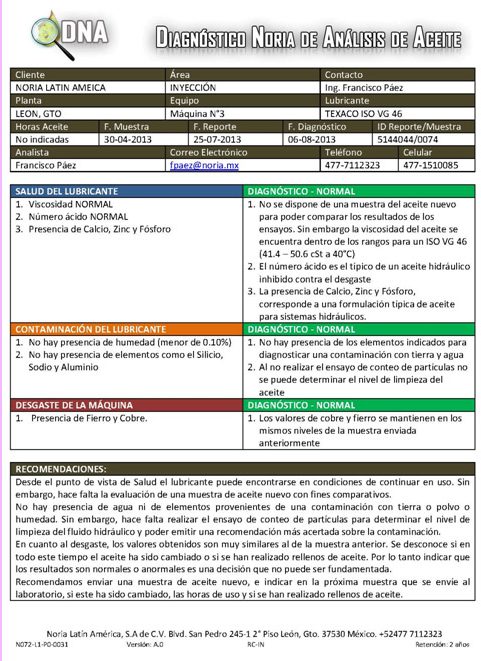
Fig. 8 – Interpretación de resultados y diagnóstico efectuado por un experto
Los límites estándar serán establecidos por el laboratorio donde se realizan los análisis del lubricante. Sin embargo, si por alguna razón hay que ajustar estos límites hacia arriba o hacia abajo, estos deben ser identificados correctamente. Por ejemplo, los límites que deben ser ajustados a la baja so aquellos que se establecen para las máquinas más críticas o que están consistentemente saludables. Un pequeño incremento en alguno de los resultados podría ser el motivo para realizar una prueba de excepción o tomar inmediatamente una segunda muestra para analizarla. En tales casos, esa segunda muestra debe garantizar que los resultados que se obtengan son representativos de las condiciones del lubricante y de la máquina y no un simple error en el muestreo o en el análisis de dicha muestra. Si se requiere una prueba de excepción, la Fig. 7 muestra cuáles pruebas deben ser realizadas cuando las pruebas de rutina no determinan el modo de falla presente.
Noria Corporation. Traducido por Roberto Trujillo Corona, Noria Latín América.