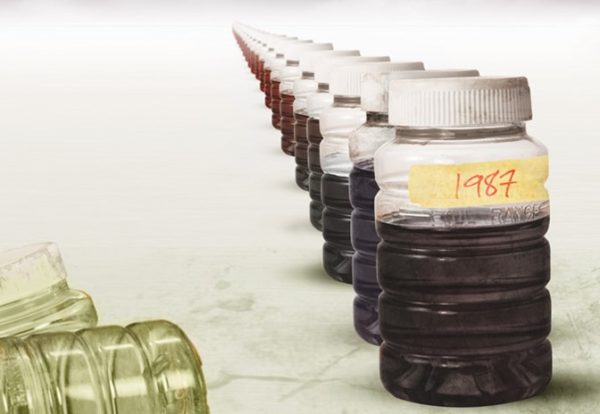
La edición de enero-febrero de 2017 de Machinery Lubrication detalló cómo la Cooperativa Seminole Electric cerca de Jacksonville, Florida, pudo extender la vida útil de los lubricantes utilizados en sus sistemas de control electrohidráulico (EHC). Este artículo de seguimiento explicará las consecuencias no deseadas de pasar 30 años sin un cambio de aceite.
Después de 30 años, el fluido a base de éster fosfatado de la instalación se volvió inmanejable y se efectuó un lavado químico de alta velocidad en el sistema con un fluido de enjuague y un nuevo llenado de fluido. Esto resultó ser una experiencia reveladora, ya que el líquido se oscureció poco después del lavado.
Algunos creían que esto se debía a la generación de nuevos desechos o problemas dentro del sistema. Otros pensaron que el aceite nuevo estaba limpiando el sistema. Cualquiera que sea la razón, el fluido nuevo estaba empeorando rápidamente, y cuando se tienen 10,000 litros por unidad, debe tratarse como un activo en lugar de una mercancía.
Nuevos problemas
Los problemas comenzaron poco después de que se completó el primer lavado químico en la segunda unidad y se volvió a poner en servicio. El nuevo líquido se volvió negro rápidamente. Estaba tan oscuro que no se podía ver la luz de una linterna a través del aceite en una botella. El filtro final se cambió de un elemento de 3 micrones a un elemento del tipo de eliminación de barniz de 1 micrón.
La esperanza era que este filtro ayudaría a solucionar los problemas que ocurrían después del enjuague químico. Esto resultó ser un problema en sí mismo, ya que el elemento no podía durar ni un mes antes de alcanzar la presión diferencial terminal. Se envió a analizar uno de los elementos del filtro saturado para identificar la composición de los desechos que lo obstruían. Una vez que se determinara esto, se podría desarrollar un plan de acción para corregir el problema.
El análisis del filtro detectó cinco categorías distintas de materiales. Más del 86 por ciento se derivó del fluido EHC, que estaba compuesto por ésteres fosfatados y sus productos de degradación (barniz). Otro 8.63 por ciento se reportaron como contaminantes de metales/metaloides asociados con medios de eliminación de ácidos.
Se encontró que un 2.11 por ciento adicional eran metales de desgaste o partículas consistentes con las esperadas del desgaste de los componentes metálicos del equipo, mientras que el 1.85 por ciento se caracterizó como contaminantes metálicos a menudo asociados con la mezcla de lubricantes extraños. El 1.27 por ciento final se clasificó como contaminantes halógenos, que pueden estar asociados con la descomposición de fluoropolímeros o el agua de mar.
Se pensó que no todos estos materiales fueran problemas actuales con el aceite nuevo después del lavado. Por supuesto, incluso con una descarga de alta velocidad, todavía habría alguna acumulación o material residual de una operación de 30 años que el nuevo fluido podría limpiar y eliminar.
De los productos de descomposición derivados del fluido, el 58.86 por ciento era carbono. Lo más probable es que esto haya sido causado por el microdiéseling, que es una degradación térmica inducida por la presión. Una burbuja de aire pasa de un área de baja presión a una zona de alta presión y, a través de la compresión adiabática, se calienta a temperaturas muy altas.
Aunque no se transfiere mucho calor entre el fluido y la burbuja, la temperatura dentro de la burbuja puede alcanzar los 1093 ºC (2000 ºF). Cuando esto ocurre, se forman partículas de hollín de tamaño submicrónico, que pueden hacer que el aceite se oscurezca.
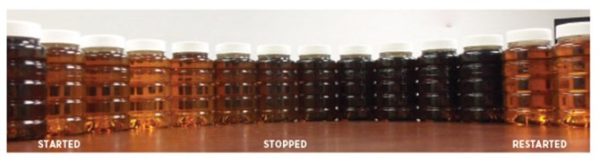
Cambios en el sistema
Como con cualquier planta, muchas cosas fueron cambiadas, modificadas y actualizadas a lo largo de los años. Desafortunadamente, los ingenieros de diseño y lubricación no se comunicaron. Aunque ciertos cambios para mejorar un sistema pueden no afectar su funcionamiento, pueden ser muy perjudiciales para el fluido.
Entre las preocupaciones con el fluido de éster fosfatado se incluyen una caída de presión dentro del sistema, picos de presión, tiempo de residencia inadecuado en el depósito para la liberación de aire, fluido devuelto incorrectamente al tanque y la falta de un tubo de bajada o difusor en la línea de retorno. Desafortunadamente, estas áreas problemáticas no son fáciles de ubicar dentro de un sistema y, por lo general, son difíciles de solucionar.
En este caso, el depósito estaba bien diseñado con tubos de bajada, difusores, deflectores y un volumen lo suficientemente grande para que el tiempo de residencia de liberación de aire fuera el adecuado. Había tres bombas de tornillo sumergidas, cada una con una capacidad de 175 galones por minuto (GPM), junto con una válvula reguladora de presión constante y tres válvulas de alivio, una por bomba. No había acumuladores en el sistema original, por lo que dos bombas funcionaban continuamente para satisfacer los picos y oscilaciones del sistema.
Con 350 GPM de las dos bombas, el tiempo de residencia en el depósito es de poco más de siete minutos. El tiempo de liberación de aire del aceite nuevo suele ser de tres a cinco minutos. Después de un año, el fluido tuvo un tiempo de liberación de aire de 7.4 minutos y hasta 11 minutos antes de la eliminación de partículas submicrónicas. Si había un pico en el sistema la tercera bomba arrancaba automáticamente, pero no se apagaba automáticamente.
La válvula reguladora de presión constante fue diseñada para manejar 1100 GPM. Cuando la válvula no funciona correctamente, las válvulas de alivio de cada bomba alivian el exceso de flujo y presión. Inicialmente, esto no fue un gran problema ya que las válvulas de alivio descargaban en un cabezal común que drenaba en la línea de retorno principal al fondo del tanque a través de un difusor.
Con el tiempo, se colocaron líneas de descarga separadas en las válvulas de alivio. Una permaneció en el cabezal de retorno, mientras que las otras dos estaban embridadas hasta la parte superior del tanque. Cuando la válvula reguladora de presión constante se atascó, hubo una generación excesiva de calor en las válvulas de alivio y aireación adicional del aceite que regresaba al tanque.
Antes del lavado químico, la válvula reguladora de presión constante y tres válvulas de alivio se enviaron para su reconstrucción y calibración. Ahora se calibran anualmente según sea necesario. Durante el lavado, cuando se efectuó el drenado del tanque, se agregaron nuevos bajantes con difusores a las líneas de descarga de las dos válvulas de alivio. También se instalaron acumuladores aproximadamente un año después del lavado, por lo que la planta ahora puede operar con una bomba a 175 GPM, lo que aumenta el tiempo de residencia para la liberación de aire en el tanque.
El resto del sistema consta de 10 válvulas de cierre, 10 válvulas de control, 3 kilómetros de tubería, numerosos orificios y otras válvulas de restricción de fluidos. Los actuadores de las válvulas de cierre y control fueron reemplazados hace varios años. La filtración no se había verificado en el sistema anterior.
El nuevo sistema se ha medido con un flujo de descarga de aproximadamente 50 GPM. Esta reducción del flujo solo puede ayudar a disminuir los problemas inducidos por el calor dentro del sistema que son perjudiciales para el fluido.
Oscurecimiento del fluido
La corrección en los elementos de filtración no resolvió el problema del oscurecimiento del filtro. Si bien los códigos ISO fueron excelentes (15/13/10 a 16/13/11), el fluido continuó oscureciéndose. Sin embargo, el color del fluido no era el problema real. La instalación necesitaba saber cuántas partículas submicrónicas había en su fluido. Se cree que estas partículas causan la obstrucción o recubrimiento de los medios de remediación con ácido, lo que dificulta el control de la generación de ácido y el mantenimiento del número ácido adecuado.
El análisis del filtro usado había revelado el tipo de residuos, 58.86 por ciento de carbono, que en este caso era hollín. Se pueden usar dos métodos para recolectar partículas submicrónicas: colorimetría de membrana filtrante (MPC) y análisis gravimétrico. Estos métodos utilizan una membrana de nitrocelulosa, por la que se hace pasar un volumen específico de fluido antes de secarla y analizarla.
El método MPC puede tener un mayor peso de la membrana si el sistema tiene un exceso de barniz, ya que el solvente utilizado puede hacer que los contaminantes semisolubles se precipiten y acumulen en la membrana junto con las partículas submicrónicas. Este método utiliza principalmente una escala de colores para identificar la condición del fluido y no incluye el peso de la membrana. Cuando hay hollín en el sistema, se puede suponer que habrá una mancha negra, por lo que, si bien el color es importante, el peso de la membrana será la información más valiosa. Por lo tanto, asegúrese de que su laboratorio pueda pesar las membranas.
Filtración electrostática
Dado que cambiar el filtro final de un elemento de 3 a 1 micrones no era práctico, se probó con filtración electrostática. Este tipo de filtración se había utilizado anteriormente con excelentes resultados, pero no se consideró rentable para el fluido viejo y degradado.
Una cosa a considerar cuando se utiliza la filtración electrostática es el contenido de agua del fluido, ya que no funciona correctamente cuando el nivel del agua es superior a 500 partes por millón (ppm). Dado que los fluidos de éster fosfatados son hidrofílicos, pueden solubilizar entre 4000 a 4500 ppm de agua a la temperatura de funcionamiento, lo que puede crear problemas.
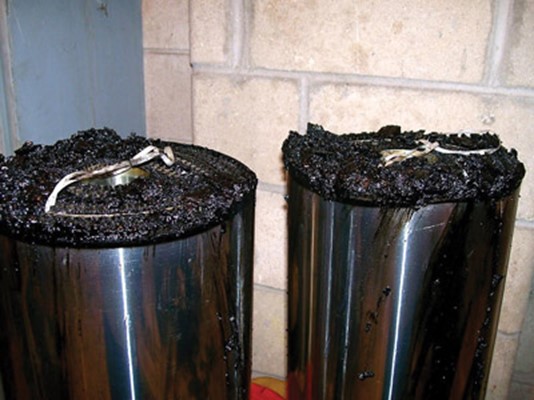
En este caso, el sistema tenía instalado un sistema de purga de espacio superior con aire seco desde hace muchos años. Esto utiliza un dispositivo que seca el aire hasta un punto de rocío de menos 40 grados C. Luego, el aire se inyecta en el espacio superior del depósito y sale a través de la ventilación existente.
El equilibrio de fase permite que el agua se extraiga del fluido hacia el aire seco y luego se expulse por el respiradero. Esto ha funcionado muy bien. Incluso en los veranos cálidos y húmedos de Florida, se han mantenido niveles de agua por debajo de 500 ppm.
Hay dos tipos de filtración electrostática disponibles para lubricantes: aglomeración de carga balanceada (BCA, por sus siglas en inglés) y el de tipo colector. BCA inicialmente se probó en la segunda unidad. Consta de un prefiltro y una cámara de mezcla que carga las partículas e inicia el proceso de aglomeración. Las partículas aglomeradas más grandes se filtran en un filtro final o posterior. Aunque este método redujo el peso de la membrana, no se observó cambio de color en el fluido.
A continuación, se empleó el de tipo de colector. Con la filtración en servicio, tomó algunos meses para que el aceite comenzara a cambiar de color y para que el peso de la membrana disminuyera. Luego ocurrió un problema con la unidad de filtración, que no se solucionó durante un par de meses debido a que la unidad se apagó.
Afortunadamente, durante la misma parada, se instalaron acumuladores en la segunda unidad. Esto permitió el funcionamiento con una sola bomba. Ahora, no solo aumentó el tiempo de residencia del depósito para la liberación de aire, sino que también disminuyó la generación de carbón debido a la compresión adiabática de las burbujas dentro de la bomba.
Cuando se volvió a poner en servicio la filtración electrostática en la segunda unidad, el tiempo de limpieza para limpiar el aceite se redujo considerablemente. El tiempo de liberación de aire también disminuyó en dos minutos. La esperanza es que esto se deba a la reducción de partículas generadas en lugar de que el sistema se limpie con aceite nuevo.
Control de problemas del sistema
Al igual que con la mayoría de las cosas mecánicas, cuando algo sale mal, por lo general no es solo un problema, sino varios problemas compuestos. La solución rápida a menudo es simplemente cambiar el aceite, pero este caso es un ejemplo perfecto de que el aceite no es el problema. En cambio, era el sistema el que estaba causando el problema. Si bien se han realizado muchas de las soluciones fáciles, solo el tiempo dirá si son suficientes para resolver los problemas que parecen plagar los sistemas EHC.
La filtración electrostática parece ser la mejor tecnología para eliminar partículas submicrónicas del fluido en este sistema. Aunque siempre es bueno tener un fluido a través del cual se pueda observar, su principal preocupación debe ser reducir y controlar los problemas dentro del sistema que crean partículas submicrónicas, ya que esto puede ser muy perjudicial para el mantenimiento adecuado de su aceite.
Noria Corporation. Traducido por Roberto Trujillo Corona, Noria Latín América.