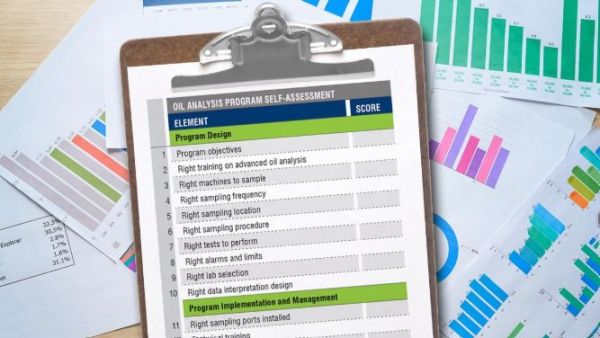
¿Qué tan efectivo es su programa de análisis de aceite? Para determinar la respuesta, es necesario realizar una autoevaluación del diseño y la gestión de su programa. Muchos programas de análisis de aceite tienen un potencial limitado debido a la falta de visión. Esto puede deberse a una capacitación insuficiente o a una comprensión inadecuada de las capacidades del análisis de aceite.
Con demasiada frecuencia, el responsable del programa de análisis de aceite simplemente acepta el programa propuesto por el proveedor de lubricantes o un laboratorio externo, asumiendo que se adaptará a las necesidades de la organización. Si bien esta suposición no siempre es errónea, la pregunta es si el programa se ha ajustado adecuadamente a las condiciones de la planta, la criticidad de la maquinaria y los objetivos de confiabilidad.
Al realizar un autodiagnóstico rápido, pero exhaustivo, una instalación puede evaluar la eficacia de su programa actual de análisis de aceite.
Evaluación del programa
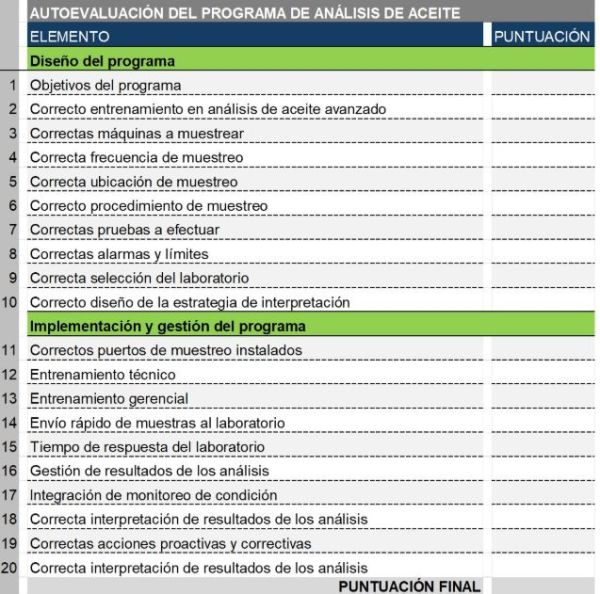
Se puede completar una autoevaluación calificando cada uno de los 20 elementos esenciales (mostrados arriba) en una escala del 1 al 4.
Puntuación 1: indica que el elemento no ha sido considerado o no hay información sobre si ha sido incluido en el diseño/implementación del programa.
Puntuación 2: hay poca evidencia de que se haya considerado el elemento.
Puntuación 3: hay documentación adecuada disponible que demuestra que el elemento ha sido considerado para el programa.
Puntuación 4: el elemento ha sido considerado, discutido y documentado para el diseño/implementación del programa.
Puntuación final: es la suma de las 20 puntuaciones individuales.
Interpretación de la autoevaluación
Los programas con puntuaciones de 70 o más funcionan bien, pero aún pueden tener algunas áreas que se puedan mejorar. Un plan de implementación que aborde problemas específicos puede ayudarle a lograr una mayor confiabilidad.
Los programas con una puntuación entre 50 y 69 tienen sus puntos fuertes, pero varios aspectos deben corregirse. Los programas con una puntuación de 49 o menos tienen bastantes oportunidades de mejora. Las puntuaciones en este rango indican que es posible que falte información crítica de su maquinaria.
Independientemente de su puntuación actual, siempre hay margen de mejora. Mediante evaluaciones periódicas, puede revitalizar su programa de análisis de aceite y maximizar su potencial.
Diseño del programa
Diseño del programa
El primer paso es evaluar el diseño de su programa de análisis de aceite, incluyendo:
- Objetivos
- Capacitación
- Criticidad de la maquinaria
- Frecuencia de muestreo
- Conjuntos de pruebas
- Ubicaciones de muestreo
- Alarmas y límites
- Procedimientos de muestreo
- Selección del laboratorio
- Interpretación de resultados
Determine si el programa tiene un enfoque holístico de mantenimiento basado en condición (predictivo y proactivo) o si está diseñado para maximizar los intervalos de cambio de aceite. ¿El análisis del aceite nuevo al ingresar a la planta forma parte del programa? También es fundamental brindar la capacitación adecuada al gerente del programa para que pueda colaborar con el laboratorio en el diseño y la comprensión de los objetivos y las características del programa.
La selección de las máquinas por incluir en el programa debe estar basada en su criticidad, la cual se prioriza según múltiples factores, entre ellos:
- Costos
- Mantenibilidad
- Seguridad
- Riesgos o preocupaciones ambientales
Los procedimientos de muestreo deben realizarse de forma correcta y consistente para obtener muestras de aceite representativas. Los intervalos de muestreo deben establecerse en función de diversos parámetros, como:
- Criticidad de la máquina
- Severidad del entorno
- La vida en servicio del aceite
- La edad de las máquinas
Dado que la concentración de contaminantes en el aceite varía en diferentes puntos de una máquina o sistema de lubricación, es fundamental elegir las mejores ubicaciones de muestreo. Una vez identificado el punto de muestreo correcto, suele ser necesario instalar un puerto de muestreo adecuado.
Las pruebas deben seleccionarse según los objetivos del programa y la criticidad de la maquinaria. Estas pueden centrarse en el análisis de la condición del lubricante, los contaminantes y las partículas de desgaste, y pueden clasificarse como pruebas de rutina y de excepción.
Las alarmas y los límites deben alertarle cuando un parámetro específico excede las condiciones normales. Pueden basarse en las recomendaciones del fabricante de equipo original y en información histórica, pero también deben validarse y ajustarse a las características específicas de la máquina.
La selección del laboratorio también debe tener en cuenta:
- Capacidades técnicas (pruebas y experiencia)
- Aseguramiento de calidad
- Gestión de la información
- Servicio al cliente
- Costo
La interpretación de los datos debe efectuarse con base en los modos de falla con mayor probabilidad y considerando la metalurgia de la máquina. Si bien existen modos de falla típicos para las máquinas, se debe realizar un análisis específico para las máquinas críticas según sus condiciones de operación.
Implementación y gestión del programa
También se debe evaluar la implementación y gestión de su programa. Estos elementos incluyen:
- Los puertos de muestreo instalados
- Gestión de entrenamiento y habilidades
- Envío de muestras al laboratorio
- El tiempo de respuesta del laboratorio
- Integración del monitoreo de condiciones
- Interpretación de los resultados
- Acciones proactivas y correctivas
- Mejora continua
Al implementar el programa en campo, una de las primeras acciones debe ser instalar puertos de muestreo en los lugares correctos con los dispositivos necesarios que permitan tomar una muestra limpia y confiable.
Se debe ofrecer capacitación en los diferentes niveles de la organización. Se debe exigir capacitación práctica a los técnicos u operadores que tomarán y etiquetarán las muestras. Se debe brindar capacitación técnica e interpretativa a los ingenieros o técnicos que interpretarán la información y confirmarán las acciones a tomar. Se debe brindar capacitación gerencial a los gerentes y supervisores responsables de la implementación, ejecución y mejora continua del programa.
Las muestras deben enviarse al laboratorio dentro de las 24 horas siguientes a su obtención. El plazo ideal de recepción de resultados del laboratorio es de 24 horas desde la recepción de la muestra hasta el envío del informe. El envío rápido de las muestras al laboratorio, junto con un plazo de respuesta corto, será valioso en caso de que se presente una condición anormal que requiera una acción inmediata.
El software de gestión de resultados del laboratorio debe ser capaz de analizar tendencias para una mejor detección de posibles fallas, así como acceder a información histórica para una retroalimentación continua. La capacidad de detección de fallas se puede mejorar al combinar dos o más tecnologías predictivas, como el análisis de vibraciones y el análisis de aceite.
Una interpretación adecuada debe provenir del diseño adecuado de la estrategia, junto con el conocimiento del contexto operativo actual de la máquina en particular. Cuando se reportan condiciones anormales, se deben tomar medidas específicas. Algunas medidas simples pueden incluir filtrar o cambiar el aceite si está contaminado, mientras que las más complejas pueden implicar investigar la causa raíz de la contaminación para eliminarla.
Asegúrese de que el programa se revise periódicamente o siempre que haya cambios en las máquinas de la planta, los lubricantes, los resultados del análisis de aceite o los objetivos de confiabilidad.
Este documento se proporcionó como material de apoyo para la ponencia de Alejandro Meza en la Conferencia Reliable Plant. Para obtener más información sobre cómo asistir a la Conferencia Reliable Plant, haga clic aquí.
Alejandro Meza. Traducción por Roberto Trujillo Corona, Noria Latín América